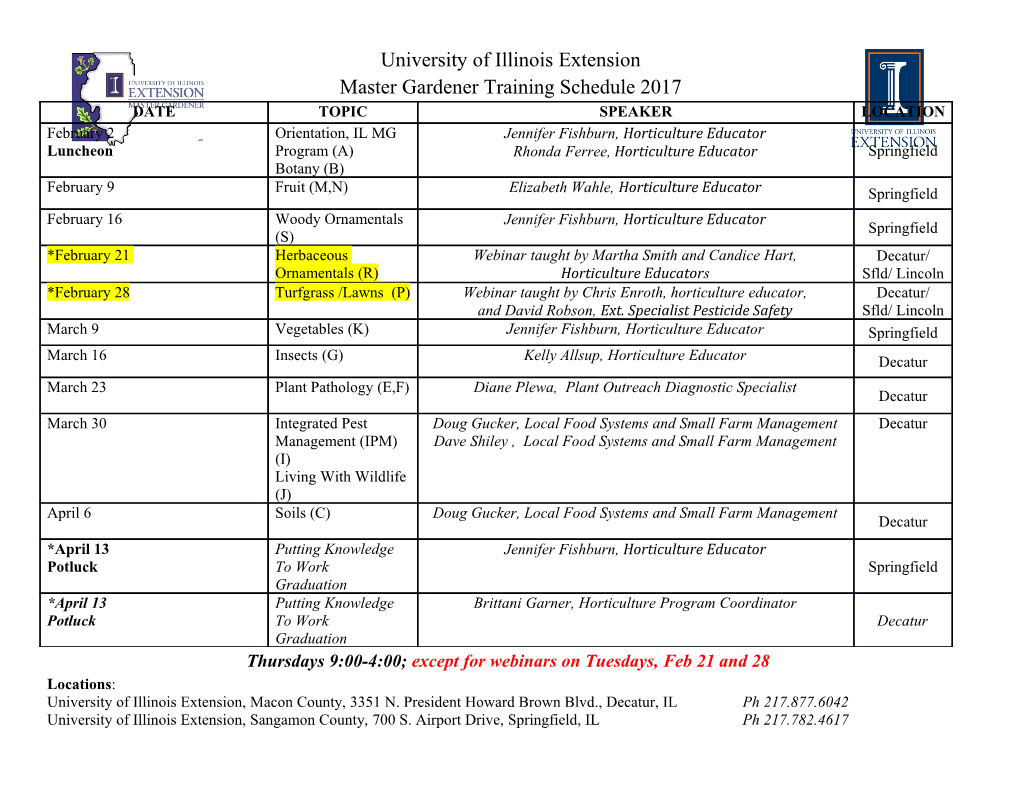
Ti-2007 Science and Technology, edited by M. Ninomi, S. Akiyama, M. Ikeda, M. Hagiwara, K. Maruyama The Japan Institute of Metals (2007) Grain Growth Behavior of Commercially Pure Titanium Katsushi Matsumoto, Yasuaki Sugizaki Materials Research Laboratory, Kobe Steel Ltd., Kobe 651-2271, Japan Effects of annealing conditions on grain growth process for commercially pure titanium were studied focusing on the character of initial crystallographic texture. Hot slab of commercial purity titanium was cold-rolled to 86% reduction in thickness and recrystallized by annealing with several heating rate, holding temperature and holding time. The primary recrystallized texture were dependent on the heating rate; the sample of rapid heating condition was composed of {1215 }<1010> component as a major one, which was close to the major rolling texture component, and {0113}<2110> component as a minor one, whereas the sample of slow heating condition was composed of both {l215}<1010> and {0113}<2110> components. Moreover, the texture evolution during grain growth was dependent on the initial texture component; the samples of rapid heating condition developed the {0113}<2110> component alternatively, whereas the samples of slow heating condition developed those of both components, resulting in more evolved texture. These different texture changes were related to the spatial distribution of these oriented grains, which formed cluster, and the frequency of cluster increased with texture development. Moreover, the frequency of low angle boundary increased with texture development. These cluster formation was considered to play a role in texture development during grain growth. Keyword: commercially pure titanium, crystallographic texture, grain growth, scanning electron microscope/electron backscatter pattern technique (SEM/EBSP), grain boundary character 1. Introduction The final annealing for primary recrystallization and grain The demand for commercially pure titanium sheet has growth was performed under the following conditions. been increasing rapidly on a global scale in late years, Specimen A : heated rapidly (about 10K/s) up to 923, which is due to the extensive use for press-forming 1023 and 1123K held for 1.80 x 102 - 8.64 x 104s products such as instrument, mobile telephone, and Specimen B : heated slowly (about 10-2K/s) up to 923, housing of personal computer in addition to the existing 1023 and 1123K held for 1.80x 102 - 8.64x 105s main use for plate heat exchanger. Thus to respond to For specimen A, primary recrystallization was performed these new needs, development of the press formability of by air furnace at each temperature for 1.80 x 102s. commercially pure titanium sheet has been of much more Further annealing of specimen A for grain growth and all importance. annealing of specimen B were carried out by vacuum Press formability such as deep drawing and stretch furnace. Microstructure was investigated in the central forming is strongly influenced by microstructure such as portion of annealed specimens using a scanning electron grain size distribution and crystallographic texture. As for microscope /electron backscatter pattern technique (SEM/ commercially pure titanium sheet, these microstructures EBSP). are determined by annealing of cold rolled sheets. In 3. Results and discussion annealing process where recrystallization and grain growth 3.1 Changes of grain orientation distribution during occurs, it is true of hcp metals that primary grain growth recrystallization texture forms and changes drastically Figure 1. shows the initial texture represented by during following grain growth in fcc and bcc metals 1-3). In orientation distribution function (ODF) of specimen A and commercially pure titanium, the primary recrystallization B with short time annealing conditions. In this figure only texture characterized mainly by orientation of {1215} the f1=0° section of ODF is represented for the texture <1010>, which is close to the rolling texture, changes to change, since it contains major orientation components. For {0113}<2110> during grain growth4-7). However, further both specimens annealed at 923K, primary recrystallization information about mechanisms of evolution of these was completed and {1215}<1010> component which is orientation distribution and grain size distribution during characterized by {f1=0°, Φ=35°,f2=0°} was a major grain growth is needed to obtain the controlling concept of orientation component. With an increase in annealing these microstructural factors for manufacturing. temperature, these two specimens showed a different In the present paper, effects of annealing conditions on texture development; {0113} <2110> component which is grain growth process for commercially pure titanium were characterized by {f1=0°, Φ=35°,f2=30°} evolved studied focusing on the character of initial texture. predominantly in specimen A, whereas both these two orientation components developed equally in specimen B. 2. Experimental Procedure By using these specimens with short time annealing A hot rolled plate with a thickness of 3.5mm for ASTM conditions at each temperature as initial textures, additional grade 1 (Fe: 0.03%, O: 0.05%) was used for this long time annealing at each temperature for further grain investigation. This plate was annealed at 973K for 3.0 x 10 growth was performed and the results are shown in the 2s in order to be recrystallized. Subsequent cold rolling following paragraph. was carried out and a sheet with a thickness of 0.5mm was prepared. 901 Figure 2. Variation of volume fraction of recrystallized grain orientation Figure 1. Initial texture represented by ODF of specimen A and B components with the average grain size. (a) specimen A, (b) specimen B. evaluated from SEM-EBSP data with several annealing temperatures. Figure 2. shows the changes in volume fractions of {1215} <1010> and {0113}<2110> components during grain growth. In the present paper, the volume fraction of each orientation component was calculated for grains with a deviation of less than 15° from an exact each orientation, respectively. As for specimen A, the volume fraction of {0113}<2110> component increased with an increase in grain size, while that of {1215}<1010> component slightly increased regardless of almost the same volume fraction of these two orientation components at the first stage (923K-1. 8 x 102s). Especially for {0113}<2110> component, its volume fraction increased rapidly at early stage of grain growth but saturated as grain growth proceeded. Thus, it can be indicated that mechanisms of texture development changes on the way of grain growth. In contrast, as for specimen B, the rate of increase in the volume fraction of {0113}<2110> component decreased in comparison with specimen A, whereas the volume fraction of {1215}<1010> component increased in the same level as {0113}<2110> component as grain growth proceeded. Furthermore, in both specimens, it is found that there was no clear temperature dependence of changes in volume fractions of these two orientation components accompanied by changes in average grain sizes. To reveal the difference in the texture change behavior Figure 3. Variation of frequency of recrystallized grain orientation during grain growth, the changes in frequency of these two components with the average grain size. (a) specimen A, (b) specimen B. orientation grains were investigated, and results are shown in Figure 3. This figure indicates that these increase in {1215}<1010> grains in specimen A remained unchanged volume fraction of these two orientation components shown or slightly decreased regardless of slight increase in volume in Figure 2. corresponded to the increase in frequency of fraction of that. each orientation grain, respectively, except for {1215} To clarify the reason why texture evolved differently <1010> grain in specimen A. The frequency of during grain growth in these specimens, grain size 902 distribution was analyzed and results are shown in the following section. 3.2 Changes of grain size distribution during grain growth Figure 4. shows the grain size distribution of {1215} <1010> and {0113}<2110> components annealed at the initial stage (923K–1.8 x 102s) for specimen A and B. As for specimen A, there was a little difference in the distribution of grain size at the initial state among {1215} <1010>, {0113}<2110> and other orientation component excluding these two components; average grain size for { 0113 }<2110> grains was slightly larger than others and in particular, frequency of larger grain size than about 5µm for {0113}<2110> grains was higher than that for {1215} <1010> grains. On the other hand, as for the specimen B, there was no significant difference in grain size distributions between {1215}<1010> and {0113}<2110> grains. It is reported that these grains, which developed during grain growth, belonged to the larger size fraction at the end of primary recrystallization7). Thus, it can be considered that one of the reason for texture development of specimen A at the initial state is grain size effect. To clarify the difference in grain size distribution at the end of primary recrystallization, more detailed study of the primary recrystallization behavior of these two specimens is Figure 4. Grain size distribution of recrystallized grain orientation required. components. R orientation grain means the other grains excluding { Figure 5. shows the relationship between average grain 1215}<1010> and {0113}<2110> grains. (a) specimen A, 923K-1.8 x size and individual grain size of {1215}<1010> and 102s, d=3.7μm, (b) specimen B, 923K-1.8 x 102s, d=12.6μm. {0113}<2110> components during grain growth. As for specimen A, grain size of {0113}<2110> component, which evolved during grain growth, became smaller than average grain size as grain size increased, while that of {1215}<1010> component became larger than that of average and even {0113}<2110> components. On the other hand, as for specimen B, there was no remarkable difference among average grain size and these two orientation components. From the standpoint of only grain size effect, texture evolution as described in section 3.1 can not be correlated with these difference in grain size.
Details
-
File Typepdf
-
Upload Time-
-
Content LanguagesEnglish
-
Upload UserAnonymous/Not logged-in
-
File Pages4 Page
-
File Size-