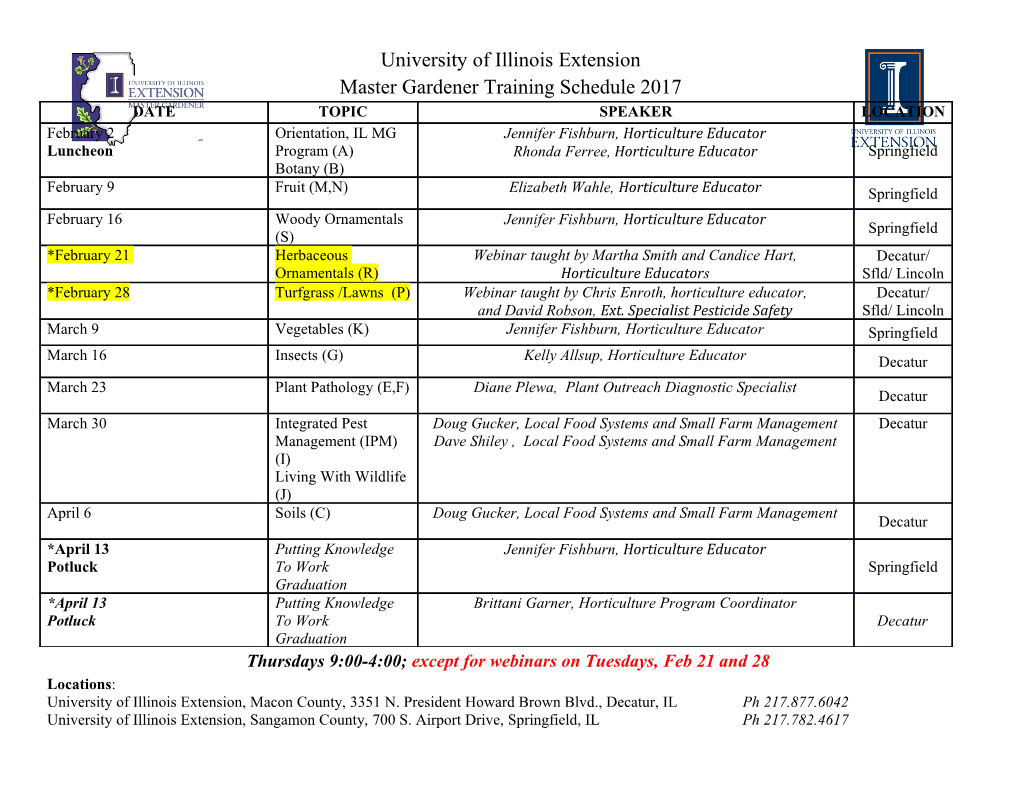
Appendix A Performance of the Ericsson Cycle Chapter 3 shows that intercoolers and reheat combustors can improve the per­ formance of gas turbines. Cooling the air during the compression process with intercoolers reduces the power requirement of the compressor stages. Heat­ ing the gas during the expansion process with reheat combustors increases the power output of the turbine stages. Thus, intercoolers and reheat combustors can improve thermal efficiency and cycle specific power. A gas-turbine cycle with an infinite number of intercoolers and an infinite number of reheat com­ bustors is known as an Ericsson cycle, after the Swedish inventor John Ericsson. This appendix shows that the thermal efficiency of an Ericsson cycle with ideal components approaches the Carnot efficiency, which is the maximum thermal efficiency achievable by any heat engine. To find the thermal efficiency of an Ericsson cycle, we will derive expressions for the heat inputs of the combustors, the power inputs to the compressors, and the power outputs of the turbines. Then, we will let the number of compressor stages, turbine stages, and combustors approach infinity and show that the thermal efficiency approaches the Carnot efficiency. Thermal efficiency can be calculated as the ratio of the cycle specific power to the cycle specific heat-input rate: W' (A.I) 'fJTH = Q1 ' where 'fJT H Thermal efficiency (~); Q' Cycle specific heat-input rate (~); and W' Cycle specific power (~). Cycle specific power can be calculated using Equations 3.5 and 3.6. Cycle specific heat-input rate is the sum of the specific heat-input rates of the n 235 236 A Performance of the Ericsson Cycle combustors in the cycle: (A.2) j The specific heat-input rate of each combustor is the heat-input rate to the combustor divided by (roughly 1 ) the enthalpy flow rate into the gas turbine: Q' QHj (A.3) Hj = (mcpT)o ' where Specific heat-input rate of Combustor j (-); Heat-input rate to Combustor j (W); Roughly the enthalpy flow rate into the gas tur­ bine (W); Mass flow rate (kgj s); Cp = Specific heat capacity evaluated at a constant pressure (J jkg-K); and T Total temperature (K). With an ideal regenerator (100% effective), the heat-input rate to each of the combustors (including the first combustor) is equal to the power output of each successive turbine stage. Thus, thermal efficiency is ~7=1 Wej (AA) TJTH = 1 + ",n W' 6j=1 Ej where ~7=1 Wej Sum of the specific powers of the n compressor stages (-); and ~7=1 W.b Sum of the specific powers of the n turbine stages (-). In this approximate analysis, we assume a constant specific heat capacity of the working fluid (air and combustion products for open-cycle gas turbines). The specific heat capacity of air actually increases by about 10% for every 600 K of temperature increase. For a constant specific heat capacity and ideal compressor stages (100% efficient), the sum of the specific powers of the n compression stages is ~ [(R/CP)] ~ Wej = n 1 - r-n- , (A.5) j=l where r Cycle pressure ratio, the ratio of the outlet pres­ sure of the last compressor stage to the inlet pres­ sure to the gas turbine (-); and R G as constant for air (J jkg- K) . 1 As explained in Chapter 3, the denominator in Equation A.2 is only roughly the enthalpy flow rate into the gas turbine because specific heat capacity varies with temperature. A Performance of the Ericsson Cycle 237 Similarly, the sum of the specific powers of the n ideal (100% efficient) turbine stages is """,n , [ -(R/CP)] L..tWEj=nT 1-r n , (A.6) j=l where T' = Cycle temperature ratio, the ratio of the outlet temperature of each of the n combustors to the inlet temperature to the gas turbine (-). We insert the expressions for the specific powers of the compressor and tur­ bine stages (Equations A.5 and A.6) into our expression for the thermal effi­ ciency (Equation A.4) and take the limit as the number of compressor stages, turbine stages, and combustors approaches infinity: [l_r(R/,;P)] 1 'TJTH = lim 1 + --''"""[-----,('"''R,-;-/C....:..,..)"] = 1 - T' . (A.7) n-+oo T' 1 - r~ This is the Carnot efficiency (see Equation 3.3). References [1] Babcock & Wilcox Co., "Steam, Its Generation and Use," New York, 1963. [2] Bahnke, G. D. and C. P. Howard, "The Effect of Longitudinal Heat Con­ duction on Periodic-Flow Heat Exchanger Performance," Transactions of the ASME, Journal of Engineering for Power, Vol. 86, 1964. [3] Bannister, R. L., N. S. Cheruvu, D. A. Little, and G. McQuiggan, "De­ velopment Requirements for an Advanced Gas Turbine System," AS ME Paper 94-GT-388, AS ME New York, New York, 1994. [4] Beck, D. S. "Optimization of Regenerated Gas Turbines," ASME Paper 94- GT-231, accepted for publication in the Transactions of the ASME, Journal of Engineering for Gas Turbines and Power. [5] Beck, D. S. "Regenerator Effectiveness during Transient Operation," AS ME Paper 94-GT-230, accepted for publication in the Transactions of the ASME, Journal of Engineering for Gas Turbines and Power. [6] Beck, D. S. "Regenerators for Gas-Turbine Applications," PhD thesis in the department of mechanical engineering at MIT, 1993. [7] Beck, D. S. "The Effect of Seal Width on Regenerator Effectiveness," Transactions of the ASME, Journal of Engineering for Gas Turbines and Power, Vol. 116, No.3, July 1994. [8] Beck, D. S. "The Compactness of Rectangular-Passage Regenerators," in­ ternal memorandum, department of mechanical engineering, MIT, Cam­ bridge, Massachusetts, 1992. [9] Bowden, A. T. and W. Hryniszak, "The Rotary Regenerative Air Preheater for Gas Turbines," Transactions of the ASME, July 1953. [10] Cadwell, R. G., et aI., "The Ford Turbine-An Engine Designed to Com­ pete with the Diesel," SAE Paper No. 720168, Detroit, Michigan, 1972. [11] Carnot, Sadi, On the Motive Power of Heat. 239 240 References [12] Chappell, M. S. and E. P. Cockshutt, "Gas Turbine Cycle Calculations: Thermodynamic Data Tables for Air and Combustion Products for Three Systems of Units," NRC, Aeronautical Report LR-579, National Research Council of Canada, August, 1974. [13] Chiprich, J. M., "ICR Program Overview," The Institute of Marine Engi­ neers, Eastern USA Branch, 15 February 1994. [14] Coppage, J. E. and A. L. London, "The Periodic-Flow Regenerator-A Summary of Design Theory," The Transactions of the ASME, Vol. 75, 1953. [15] "Cowper," an entry in The New Encyclopaedia Britannica, 15th Edition, University of Chicago, Encyclopaedia Britannica, Inc., 1980. [16] Cox, M. and R. K. P. Stevens, "The Regenerative Heat Exchanger for Gas-Turbine Power Plants," Proceedings of The Institute of Mechanical Engineers, Vol. 163, W. E. P. No. 60, London, UK, 1950. [17] Davis, James E. and William N. Gill, "The Effects of Axial Conduction in the Wall on Heat Transfer with Laminar Flow," International Journal of Heat and Mass Transfer, Vol. 13, Pergamon Press, 1970. [18] Day, Paul J. "ATTAP Extruded Ceramic Regenerator Disk Development," Proceedings of the Annual Automotive Technology Development Contrac­ tors' Coordination Meeting, 1991 P-256. [19] Day, Paul J., "A Rotary Heat Exchanger for Automotive and Other Ground-Based Gas Turbines," ASME Paper 94-GT-124, ASME New York, New York, 1994. [20] Edelman, H. C. M., "In Search of Stirling," The Announcer, pp. 6-12, N. V. Philips, Eindhoven, 1969. [21] Gale, W. K. V., "Ferrous Metals," in An Encyclopaedia of the History of Technology, McNeil, Ian (ed.), Routledge, London and NY, 1990. [22] Grossman, D. G., and J. G. Lanning, "Aluminous Keatite-An Im­ proved Rotary-Ceramic-Regenerator Core Material," ASME Paper 77-GT- 60, AS ME New York, New York, 1977. [23] Hagler, Carla D., "The Design of a Ceramic Rotary Regenerator for a Regenerated Low-Pressure-Ratio Gas-Turbine Engine," M. S. thesis, Me­ chanical Engineering, MIT, 1987. [24] Hahnemann, H. W., "Approximate Calculation of Thermal Ratios in Heat Exchangers Including Heat Conduction in Direction of Flow," National Gas Turbine Establishment Memorandum No. M36, 1948. [25] Hansson, Sven A., "Birger and Fredrik Ljungstrom-Inventors," AB Inter­ national STAL Company, Stockholm, Sweden, 1955. References 241 [26] Harper, D. B., "Seal Leakage in the Rotary Regenerator and Its Effect on Rotary-Regenerator Design for Gas Turbines," The Transactions of the ASME, February, 1957. [27] Harper, D. B. and W. M. Rohsenow, "Effect of Rotary Regenerator Per­ formance on Gas-Turbine-Plant Performance," The Transactions of the ASME, July, 1953. [28] Hawkins, W. J., D. Mathieson, C. J. Bruce, and P. Socoloski, "System Development Test Program for the WR-21 Intercooled Recuperative (lCR) Gas Turbine Engine System," ASME Paper 94-GT-186, ASME New York, New York, 1994. [29] Helms, H. E., et al., "Ceramic Applications in Turbine Engines," DoEjNASAj0017-6, NASA CR-174715, EOR-11442, Cleveland, OH, 1984. [30] Helms, H. E., et al., "AGT 100 Advanced-Gas-Turbine Technology­ Development Project," Proceedings of the 23rd Automotive Technology Development Contractor's Coordination Meeting, SAE Publication, War­ rendale, Pennsylvania, 1986. [31] Huebner, G. J., Jr., personal communication with one of the authors: letter dated 11 January 1994 to D. G. Wilson from Ann Arbor. [32] Huebner, G. J., Jr., "Chrysler's Automotive Gas Turbine," (approximate title), seminar and automobile demonstration given at MIT, Cambridge, Massachusetts, 1968. [33] Hirschkron, R. and C. J. Russo, "Small TurboshaftjTurboprop-Engine Technology Study," AIAAj ASMEjSAEj ASEE 22nd Joint Propulsion Con­ ference, Huntsville, Alabama, 1986. [34] Johnson, Dag, and R. J. Mowill, "Aegidius Elling-A Norwegian Gas­ Turbine Pioneer," Norwegian Technical Museum, Oslo ,1968. [35] Kawasaki, K. T. Matsuhisa, 1. Sakai, and K. Hijikata, "Heat Transfer Char­ acteristics of Rotating Ceramic Regenerators-Numerical Solution Using a Hybrid Finite DifferencejLaplace Transform Scheme," AS ME report 91- GT-371.
Details
-
File Typepdf
-
Upload Time-
-
Content LanguagesEnglish
-
Upload UserAnonymous/Not logged-in
-
File Pages15 Page
-
File Size-