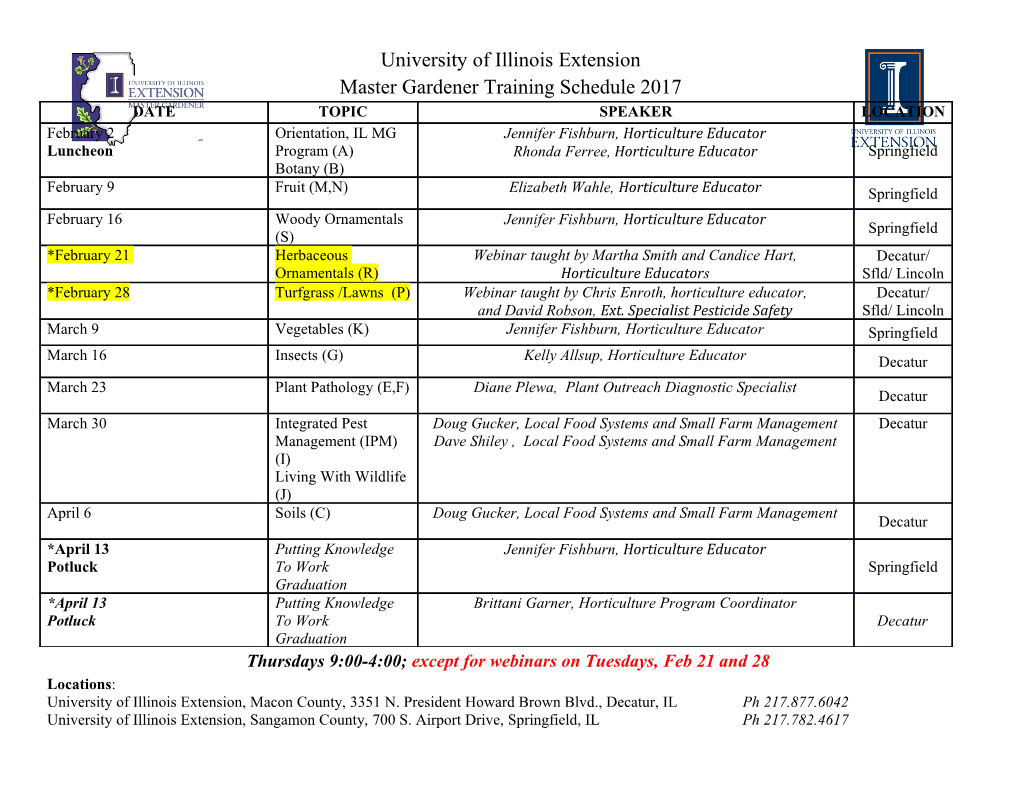
Effect of trace Lanthanum Hexaboride and Boron additions on microstructure, tensile properties and anisotropy of Ti-6Al-4V produced by Additive Manufacturing M.J Bermingham1, S D McDonald, M.S Dargusch Centre for Advanced Materials Processing and Manufacturing, School of Mechanical and Mining Engineering, The University of Queensland, St Lucia, Queensland, 4072, Australia Abstract In this work trace lanthanum hexaboride (LaB6) and elemental boron are alloyed with Ti-6Al-4V and their effects on the microstructure, tensile properties (including anisotropy) and melt pool shape during Additive Manufacturing (AM) are investigated. During the melting process, the LaB6 scavenges oxygen and decomposes into La2O3 and TiB. The presence of the rare earth element drastically changes the apparent surface tension and shape of the deposited layers. This is attributed to the Heiple-Roper effect and could have benefits during AM in producing components with unsupported overhangs. The formation of eutectic TiB during the final stages of solidification results in highly directional TiB needles in between columnar grains that are aligned with the build direction. The slow cooling rate during deposition of approximately 90-100°Cs-1 produces very large TiB particles which can exceed 50µm in length. Although improving strength by up to 10%, under tensile stress the high aspect ratio TiB particles are sites for crack opening which leads to a decline in ductility in the longitudinal test direction and a corresponding increase in anisotropy over unmodified Ti-6Al-4V. Keywords: titanium alloys; characterization; stress/strain measurements; grains and interfaces 1 Corresponding author: [email protected] 1 1.0 Introduction Additive Manufacturing offers many advantages over conventional manufacturing processes and research efforts to advance this technology have grown considerably in recent years. Titanium alloys are strong candidates for AM because of their high material cost and the high cost of traditional manufacturing processes. Ti-6Al-4V is by far the most studied of all titanium alloys in AM and now researchers have a comprehensive understanding of the Ti-6Al-4V microstructure and properties inherent to AM. For instance, across multiple AM technologies with different cooling rates it is now understood that the solidification conditions during AM of Ti-6Al-4V generally favour epitaxial growth of textured columnar-β grains which can create material property anisotropy [1-7]. While incomplete fusion (and therefore porosity) between layers can also contribute to anisotropy during AM of Ti-6Al- 4V [8, 9], Kobryn and Semiatin [8] and Qiu et al. [10] have shown that, even after the removal of porosity through Hot Isostatic Pressing, or in the absence of porosity in the case of Carroll et al. [11], anisotropy still remains, on account of the microstructural texture. It has been proposed that grain boundary-α (which delineates the columnar prior β-grains) is susceptible to failure under tensile loads normal to the build direction and this can account for anisotropy [11, 12]. It is therefore important for future research efforts to find ways to prevent anisotropy. The most obvious way of achieving this is to produce homogeneous equiaxed microstructures during AM. There are two approaches that may improve the homogeneity in the microstructure of α+β titanium alloys produced during solidification. The first is to eliminate the highly textured columnar β-grains that result from the prevailing solidification conditions and alloy constitution, i.e. promote the Columnar to Equiaxed Transition (CET). The second approach is to refine the α-phase and eliminate unfavourable variants such as grain boundary-α or large α-colonies that can be several millimetres in size and adopt texture from the parent β-grain. Both of these approaches may be achievable through selective chemical alloying, however, to date there has been limited progress made in developing new titanium alloys for this purpose. Silicon is an effective growth restricting solute based grain refiner in titanium [13] and recently Mereddy et al. [14] investigated Ti-Si alloys during Wire Arc Additive Manufacturing (WAAM) in an attempt to achieve homogenous equiaxed grains throughout the build. Although substantial refinement of the grain size occurred (including the presence of some fine grained equiaxed crystals), ultimately the addition was unable to completely suppress epitaxial growth and some columnar grains still formed. Boron has also been studied as a grain refiner in trace additions to Ti-6Al-4V during AM processes. Although the columnar grain structure remained, Bermingham et al. [15] demonstrated substantial refinement of the α-grain morphology, elimination of continuous 2 segments of grain boundary-α and an improvement in compressive strength with trace boron additions during Ti-6Al-4V AM. In light of the work by Carroll et al. [11], the elimination of grain boundary-α is another promising approach that may eliminate anisotropy and warrants further investigation. Additions of as little as 1000ppm boron to cast Ti-6Al-4V are known to prevent the formation of grain boundary-α [16]. Recently the ASTM released a standard specification for additive manufacturing Ti-6Al-4V by powder bed fusion (ASTM F2924). The standard provides guidance on the acceptable chemistry tolerance of the base alloy, and interestingly, it indicates a provision for up to 0.1wt% of any ‘other’ elements2, up to a maximum of 0.4wt% in total. Potentially, new alloys could be carefully developed based on Ti- 6Al-4V that contain trace additions capable of eliminating the microstructural directionality and the associated anisotropy of AM while still complying with this new standard. However, there are only a handful of known elements that are powerful enough to impart substantial refinement in such small concentrations. Boron [17, 18], Beryllium [19], Carbon [20] and several Rare Earth elements including La and Y [21-24] have all been reported to refine the microstructure of titanium alloys in small concentrations during solidification. Rare Earth elements are also known to reduce the dissolved oxygen concentration in titanium through a ‘scavenging’ phenomena [25] and this trait could be very beneficial for AM. Not only could this permit the use of lower quality, cheaper feedstock material (i.e. with higher oxygen contents), but it also provides a margin of safety for AM processes that are vulnerable to atmospheric contamination. For example, there is growing interest in developing large scale ‘out of chamber’ AM technologies capable of producing components several metres in size [26] outside of an inert gas or vacuum chamber, and therefore, any trace alloy addition that can reduce the dissolved oxygen content has clear potential in AM processes susceptible to atmospheric contamination. The purpose of this study is to investigate the effect of trace Lanthanum hexaboride (LaB6) additions on the microstructure and tensile properties, including the effects of anisotropy, of Ti-6Al-4V components produced by Wire Arc Additive Manufacturing (WAAM). The level of addition is to be within the chemical tolerance specified by ASTM F2924, and thus considered to be present in ‘trace levels’. Although ASTM F2924 specifically relates to powder bed fusion AM, it is reasonable to expect that other AM processes including Directed Energy Deposition (such as WAAM, LENS etc.) would 2 ASTM F2924 specifies maximum levels for Al, V, Fe, O, C, N, H and Y but all other elements individually have a maximum allowance of 0.1wt%, up to a combined limit of 0.4wt%. 3 follow similar guidelines for acceptable alloy chemistry. Only a few researchers have considered using LaB6 as a trace alloy element in titanium and these have been exclusively in casting and powder metallurgy processes [27-29]. When mixed with titanium the LaB6 is reported to decompose into TiB and La2O3 (via the reaction 2LaB6 + 12Ti + 3O → 12TiB + La2O3), and the subsequent TiB is reported to refine the microstructure while the lanthanum lowers the dissolved oxygen content. Therefore, this is a promising compound to explore as a trace alloy addition to Ti-6Al-4V for AM. For comparison, Ti- 6Al-4V modified with trace boron is also investigated. Although the effect of trace boron additions on the microstructure and compressive strength of Ti-6Al-4V has been reported [15], to date no research has investigated the potential improvement in tensile anisotropy associated with the elimination of grain boundary-α with the introduction of TiB during AM of Ti-6Al-4V. 2.0 Experimental Methods The wire arc additive manufacturing technique was used for this study (details about the equipment available in [15]). Ti-6Al-4V wire was used as the feedstock and a wrought Ti-6Al-4V base plate was used as a substrate for the deposits. Three alloys were investigated in this study, namely Ti-6Al-4V, Ti- 6Al-4V + boron and Ti-6Al-4V + LaB6. As previously mentioned, the level of addition of B and La was targeted to be within the limits specified by ASTM F2924, i.e. <0.10wt% of each element. The boron and LaB6 containing alloys were prepared by coating the build surface with specially prepared alcohol based paints (each approximately 15wt% of LaB6 or B) prior to each deposition using a similar method as reported elsewhere [14, 15]. The average LaB6 powder size used in the paint was 10µm (Sigma Aldrich, 99%) and the average boron powder size was 1µm (Strem Chemicals, 92-95%). The average alloy chemistry sampled from multiple locations within the built components is shown in Table 1. Each deposit was created by moving the welding torch in a linear direction and feeding wire into the molten pool, which solidified to make a layer. A subsequent layer was then deposited over the first by increasing the height of the torch, however, between layers the direction of torch travel was reversed so that the component was built up in a zig-zag fashion.
Details
-
File Typepdf
-
Upload Time-
-
Content LanguagesEnglish
-
Upload UserAnonymous/Not logged-in
-
File Pages26 Page
-
File Size-