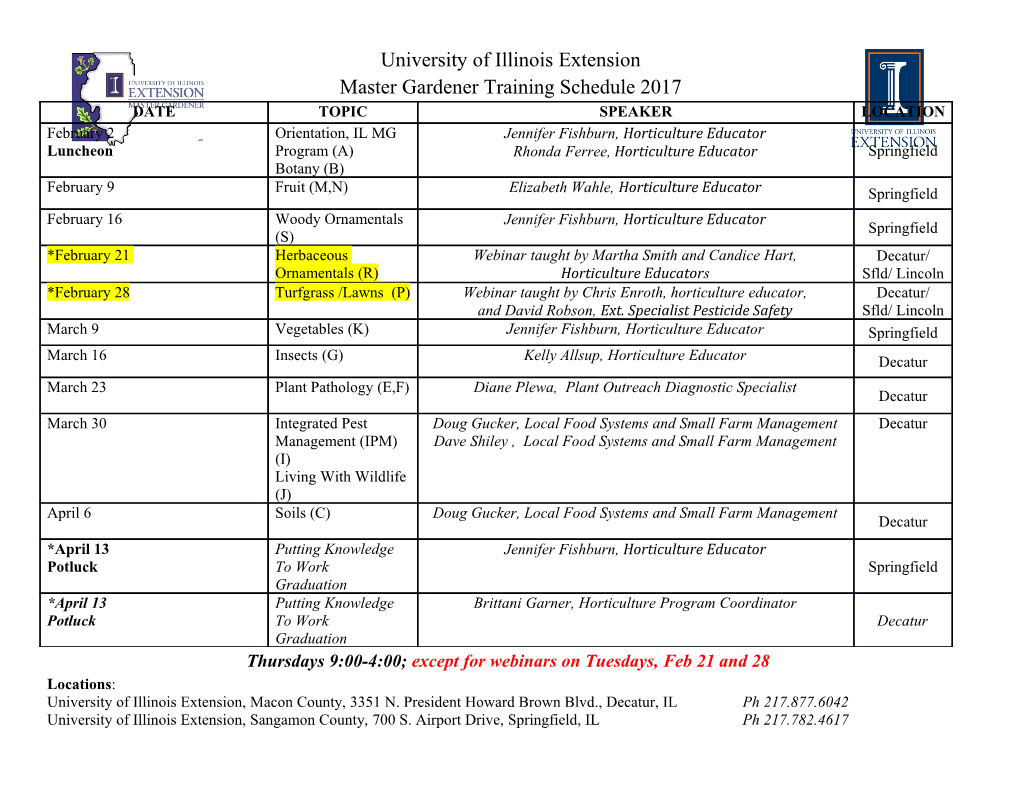
Essentials of Lean Manufacturing Reviewing the essentials of lean thinking and terminology Provided by: Newcastle Systems, Inc. 15B Sylvan Street Middleton, MA 01949 USA P: 781-935-3450 F: 978-777-1803 www.newcastlesys.com Contents 1 ESSENTIALS OF LEAN MANUFACTURING 1 1.1 Lean thinking ............................................. 1 1.1.1 Overview ........................................... 1 1.1.2 Lean thinking practices .................................... 2 1.1.3 Controversies ......................................... 4 1.1.4 Itʼs about people first .................................... 4 1.1.5 Lean and green ........................................ 4 1.2 Lean manufacturing .......................................... 5 1.2.1 Overview ........................................... 5 1.2.2 A brief history of waste reduction thinking .......................... 6 1.2.3 Types of waste ........................................ 9 1.2.4 Lean implementation develops from TPS ........................... 10 1.2.5 Lean services ......................................... 12 1.2.6 Goals and strategy ....................................... 13 1.2.7 The Lean Management Model ................................ 14 1.2.8 Steps to achieve lean systems ................................. 14 1.2.9 Implementation dilemma ................................... 14 1.2.10 See also ............................................ 15 1.2.11 References .......................................... 16 1.2.12 Further reading ........................................ 17 1.2.13 External links ......................................... 17 2 TERMINOLOGY 18 2.1 Muda (Japanese term) ......................................... 18 2.1.1 Seven wastes ......................................... 18 2.1.2 Other candidate wastes .................................... 19 2.1.3 Implementation ........................................ 19 2.1.4 See also ............................................ 20 2.1.5 References .......................................... 20 2.1.6 External links ......................................... 20 2.2 Mura (Japanese term) ......................................... 20 2.2.1 Implementation ........................................ 20 2.2.2 Limitations, critiques and improvements ........................... 21 i www.newcastlesys.com ii CONTENTS 2.2.3 References .......................................... 21 2.3 Muri (Japanese term) ......................................... 21 2.3.1 Avoidance of muri in Toyota manufacturing ......................... 21 2.3.2 Implementation ........................................ 21 2.3.3 References .......................................... 21 2.4 Kaizen ................................................. 22 2.4.1 Overview ........................................... 22 2.4.2 History ............................................ 22 2.4.3 Implementation ........................................ 23 2.4.4 See also ............................................ 23 2.4.5 References .......................................... 24 2.4.6 External links ......................................... 24 2.5 Kanban ................................................ 25 2.5.1 Origins ............................................ 25 2.5.2 Operation ........................................... 25 2.5.3 Electronic kanban ....................................... 26 2.5.4 Types of kanban systems ................................... 26 2.5.5 See also ............................................ 26 2.5.6 References .......................................... 27 2.5.7 Further reading ........................................ 27 2.5.8 External links ......................................... 27 3 HISTORICAL THOUGHT LEADERS 28 3.1 Taiichi Ohno .............................................. 28 3.1.1 See also ............................................ 28 3.1.2 Published works ........................................ 28 3.1.3 References .......................................... 28 3.2 Shigeo Shingo ............................................. 28 3.2.1 Life and work ......................................... 29 3.2.2 Education ........................................... 29 3.2.3 Bibliography ......................................... 29 3.2.4 Footnotes ........................................... 30 3.2.5 Further reading ........................................ 30 3.2.6 See also ............................................ 30 3.2.7 External links ......................................... 30 4 Text and image sources, contributors, and licenses 31 4.1 Text .................................................. 31 4.2 Images ................................................. 33 4.3 Content license ............................................ 33 www.newcastlesys.com Chapter 1 ESSENTIALS OF LEAN MANUFACTURING 1.1 Lean thinking Toyota and have grasped the fact that the aim of con- tinuous improvement is continuous improvement. Lean thinking is a business methodology which aims to Lean thinking as such is a movement of practition- provide a new way to think about how to organize human ers and writers who experiment and learn in differ- activities to deliver more benefits to society and value ent industries and conditions, to lean think any new to individuals while eliminating waste. The term lean activity. thinking was coined by James P. Womack and Daniel T. * 2. Lean manufacturing adepts who have interpreted the Jones [1] to capture the essence of their in-depth study term“lean”as a form of operational excellence and ʼ * of Toyota s fabled Toyota Production System. [2] Lean have turned to company programs aimed at taking thinking is a new way of thinking any activity and seeing costs out of processes. Lean activities are used to the waste inadvertently generated by the way the process improve processes without ever challenging the un- is organized by focusing on the concepts of: derlying thinking, with powerful low-hanging fruit results but little hope of transforming the enterprise 1. Value, as a whole. This“corporate lean”approach is funda- mentally opposed to the ideals of lean thinking, but 2. Value streams, has been taken up by a great number of large busi- 3. Flow, nesses seeking to cut their costs without challenging their fundamental management assumptions. 4. Pull, 5. Perfection. 1.1.1 Overview The aim of lean thinking is to create a lean enterprise, Lean thinking was born out of studying the rise of Toyota one that sustains growth by aligning customer satisfac- Motor Company from a bankrupt Japanese automaker in tion with employee satisfaction, and that offers innovative the early 1950s to todayʼs dominant global player. At products or services profitably whilst minimizing unnec- every stage of its expansion, Toyota remained a puzzle essary over-costs to customers, suppliers and the environ- by being capturing new markets with products deemed ment. The basic insight of lean thinking is that if you relatively unattractive and with systematically lower costs train every person to identify wasted time and effort in whilst not following any of the usual management dictates their own job and to better work together to improve pro- . In studying the company firsthand it appeared that it had cesses by eliminating such waste, the resulting enterprise a unique group of elders (sensei) and coordinators (train- will deliver more value at less expense whilst developing ers from Japan) dedicated to help managers think differ- every employeeʼs confidence, competence and ability to ently. Contrarily to every other large company, Toyotaʼs work with others. training in its formative years was focused on developing peopleʼs reasoning abilities rather than pushing them to The idea of lean thinking gained popularity in the busi- execute specialist-derived systems. ness world and has evolved in two different directions: These“sensei”, or masters in lean thinking would chal- 1. Lean thinking converts who keep seeking to under- lenge line managers to look differently at their own jobs stand how to seek dynamic gains rather than static by focusing on: efficiencies. For this group of thinkers, lean think- ing continuously evolves as they seek to better un- 1. The workplace: Going and seeing firsthand work derstand the possibilities of the way opened up by conditions in practice, right now, and finding out the 1 www.newcastlesys.com 2 CHAPTER 1. ESSENTIALS OF LEAN MANUFACTURING facts for oneself rather than relying on reports and piecemeal. Pull is the basic technique to“lean”the boardroom meeting. The workplace is also where company and, by and large, without pull there is no real people make real value and going to see is a lean thinking. mark of respect and the opportunity to support em- ployees to add value through their ideas and ini- 6. Seeking perfection through kaizen: The old time tiative more than merely make value through pre- sensei used to teach that the aim of lean thinking scribed work. The management revolution brought was not to apply lean tools to every process, but to by lean thinking can be summed up by describing develop the kaizen spirit in every employee. Per- jobs in terms of Job = Work + Kaizen fection is not sought through better, more clever systems or go-it-alone heroes but through a com- 2. Value through built-in quality: Understanding mitment to improve things together step-by-small- that customer satisfaction is paramount and is built- step. Kaizen literally means change for the better in at every step of the enterpriseʼs process, from and Kaizen spirit is about seeking a hundred 1% im- building
Details
-
File Typepdf
-
Upload Time-
-
Content LanguagesEnglish
-
Upload UserAnonymous/Not logged-in
-
File Pages36 Page
-
File Size-