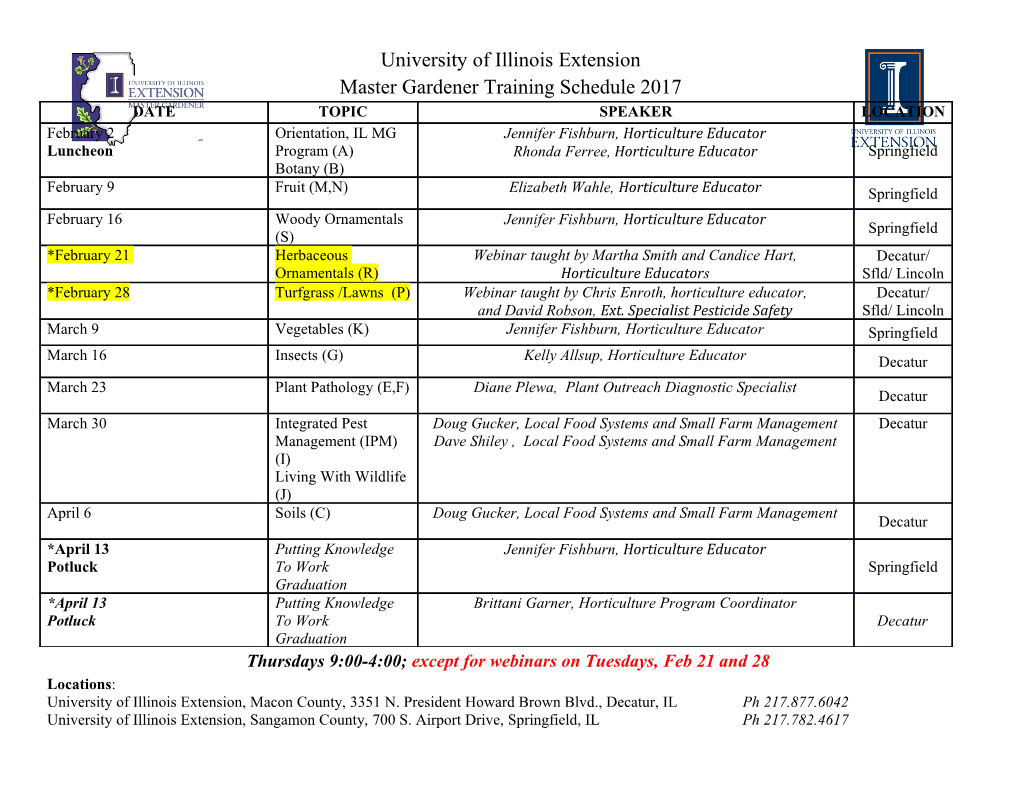
Erie County Technical School CALIBRATION MANUAL 1. Purpose: 1.1. To establish and maintain a calibration system to control the accuracy of equipment that is used for measuring student performance evaluation, particularly state or national credentials. Including measuring equipment used for public health and safety purposes. 1.2. To prevent inaccuracy, detect deficiencies and provide for timely positive corrective action. 1.3. The instructor is responsible for overall control of the calibration system and designating “master” tools and equipment that are subject to calibration. Instructional tools and equipment may be checked against the “master” tools for accuracy, as the instructor deems necessary. 2. Procedure: 2.1. “Master” tools will be calibrated by means of certified standards or equipment that has been calibrated using certified standards. 2.2. Master gauge blocks will be used to calibrate the optical comparator in the Tool and Die lab. 2.3. A list of controlled, calibrated “master tools and equipment” is maintained by the instructor. Master tools are used to check instructional tools as the instructor deems is necessary. 2.4. Any gauge or tool is considered out of tolerance if it exceeds one reference mark or graduation, or as evaluated by the instructor. The instructor shall be informed of any out-of-tolerance condition found during use so that proper actions may be taken. 3. Calibration Frequency: 3.1. The Optical Comparator will be calibrated with the Master gauge blocks each year prior to the start of testing. 3.2. Tool and Die Lab measuring tools will be calibrated in accordance with National Institute of Metalworking Skills (NIMS) standards. Tools shall be calibrated at the beginning of any job requiring NIMS standards, or when the instructor determines it should be calibrated due to accuracy requirements for the specific job. 3.3. Culinary Arts food preparation equipment shall be calibrated for temperature accuracy every other year. Records of calibration shall be maintained in the Facility Manager’s office. 3.4. National Occupational Competetency Testing Institute (NOCTI) tools are to be calibrated prior to the test. Created 4/18/2002 Revised 5/6/05 Erie County Technical School CALIBRATION MANUAL 4. Calibration Standards: 4.1. Master gauge blocks used for calibration shall be kept in the Facility Manager’s office. Certification attesting to the accuracy of the Master Gauge Blocks shall be kept on file in the Facility Manager’s office. 5. Responsibility: 5.1. The instructors shall be responsible to identify and appropriately mark “master” measuring equipment used to check the accuracy of instructional measuring equipment. 6. Records: 6.1. Facility Manager shall log the calibration of Optical Comparator on the Equipment Calibration Log. The frequency of calibration and dates indicate the calibration was performed. The Facility Manager will maintain logs for 3 years. This record is maintained in the Facility Manager’s office and is available for review. 6.2. Instructors shall list the ID and description of equipment on the Equipment Calibration Logs. The frequency of calibration and dates indicate the calibration was performed. The Facility Manager will maintain logs for 3 years. This record is maintained in the Facility Manager’s office and is available for review. Created 4/18/2002 Revised 5/6/05 Erie County Technical School PROCEDURE FOR CALIBRATING BI-METALLIC STEMMED THERMOMETERS Before Calibrating Bi-metallic stemmed thermometers they must be checked for any signs of outward damage: 1. Bent stem 2. Broken lens 3. Loose nut If damaged remove from service. Calibration 1. First prepare a beaker with a 50/50 ice/water slush. 2. Insert thermometer into mixture, making sure that the dimple is submerged. 3. Let the thermometer stabilize for three to five minutes. 4 . Check temperature it should read 32°F. 5. If your reading is more than +/- 2°F you will need to recalibrate the thermometer. 6. To recalibrate you turn the calibration nut until indicator reads 32°F. 7. After calibration let the thermometer come to room temperature. 8. Then repeat steps 2 thru 7. 9. The thermometer will be considered out of tolerance if after 3 tries the thermometer will not hold the temperature of 32°F +/- 2°F. Created 4/18/2002 Revised 5/6/05 Erie County Technical School PROCEDURE FOR CALIBRATING INCH-METRIC MICROMETERS Before Calibrating micrometers they must be checked for any signs of outward damage: 1. Chipped measuring faces 2. Bent anvil 3. Loose or missing parts If damaged remove from service. Calibration 1. It is extremely important that all parts of the micrometer be kept clean during calibration. 2. Wipe micrometer clean with a clean cloth and apply a drop of fine oil to spindle. 3. First you will need to remove play/looseness from the threads due to wear in the spindle. 4. To do this back off the thimble. 5. Insert the C-spanner into the slot or hole of the adjusting nut. 6. Turn the adjusting nut clockwise until play between the threads has been eliminated. 7. Do not over tighten, the spindle should move freely when the ratchet stop or friction thimble is being turned. 8. Next you will need to test the accuracy of the micrometer. 9. You will need a gage block from the Master Gage Blocks for the size micrometer that you will be checking. 10. Open the micrometer so that the gage block will fit between the measuring faces. 11. Check to make sure that the measuring faces are clean and there are no chips in them. 12. Place the master gage block between the measuring faces. 13. Turn the thimble using the ratchet stop or friction thimble until the measuring faces contact the master gage block. 14. The reading of the micrometer must be the same +/- .0005 as the master gage block. 15. If the reading is more than +/- .0005 you will need to adjust the micrometer. 16. To adjust the micrometer close the measuring faces carefully until they contact the master gage block. 17. Insert the C-spanner into the hole or slot provided in the sleeve. 18. Carefully turn the sleeve until the index line on the sleeve coincides with the zero line on the thimble. 19. Recheck the accuracy of the micrometer by opening the micrometer and then closing the measuring faces carefully until they contact the master gage block again. 20. The micrometer will be considered out of tolerance if after 3 tries the micrometer will not hold the reading of the master gage block +/- .0005. 21. The micrometer will be considered out of tolerance if after repeating steps 10 thru 14 and the micrometer will not hold +/- .0005” it will then be removed from service. Created 4/18/2002 Revised 5/6/05 Erie County Technical School PROCEDURE FOR CALIBRATING VERNIER, DIAL OR DIGITAL CALIPERS Before calibrating calipers they must 1st be checked for any signs of damage: 1. Chipped or damaged measuring faces and points 2. Dirty or damaged track or gear 3. Numbers worn off and unreadable 4. Loose face 5. Not repeating back to “0” 6. Sticking, skipping or binding during operation of full travel If damaged remove from service and send for repair Calibration 1. Place a rag on a demagnetizer and run calipers over to remove magnetism 2. Clean calipers with a clean cloth and check for dirt and metal chips in track 3. A light air blast may be needed to remove chips 4. Close calipers and adjust “0” on face if needed 5. Get 3 gauge block stacks from the master set: Example: If checking a 6” caliper, use a 1-inch, a 3-inch and a 6-inch stack 6. Verify accuracy over the 3 stacks of gauge block 7. The caliper will be considered out or tolerance if after 3 tries over 3 stacks the caliper will not repeat within +/- .002 Created 4/18/2002 Revised 5/6/05 Erie County Technical School CALIBRATION PROCEDURE FOR A FRAMING SQUARE Before calibrating a framing square it must be checked for any signs of outward damage such as: 1. Cracks 2. Bends 3. Twists If damaged remove from service. Calibration 1. To check calibration of a framing square you will need to obtain the Master Framing Square from the instructor, so that you can compare the gradations and square ness of the framing square to the Master Framing Square. 2. If it is more than 1/16” out of square or the gradations are off by more than 1/16” you will need to recalibrate the framing square. 3. To recalibrate the framing square, if out of square you would either bend back to square or replace. 4. If the gradations are off remove from service there is no way to recalibrate this item. 5. The framing Square will be considered out of tolerance if after 3 tries it doesn’t hold to 1/16” of square. 6. Remove it from service. Created 4/18/2002 Revised 5/6/05 Erie County Technical School CALIBRATION PROCEDURE FOR A LASER LEVEL Before calibrating Laser Level it must be checked for any signs of outward damage such as: 1. Broken parts If damaged remove from service. Calibration 1. This tool is self-leveling. 2. If damaged remove from service there is no way to recalibrate this item. Created 4/18/2002 Revised 5/6/05 Erie County Technical School CALIBRATION PROCEDURE FOR A LEVEL Before Calibrating a Level it must be checked for any signs of outward damage such as: 1. Cracked vials. 2. Excess air in the vials 3. Bends or twists in the frame If damaged remove from service. Calibration 1. The level is self-checking by holding to a surface and then turning the level around to see if it read the same.
Details
-
File Typepdf
-
Upload Time-
-
Content LanguagesEnglish
-
Upload UserAnonymous/Not logged-in
-
File Pages23 Page
-
File Size-