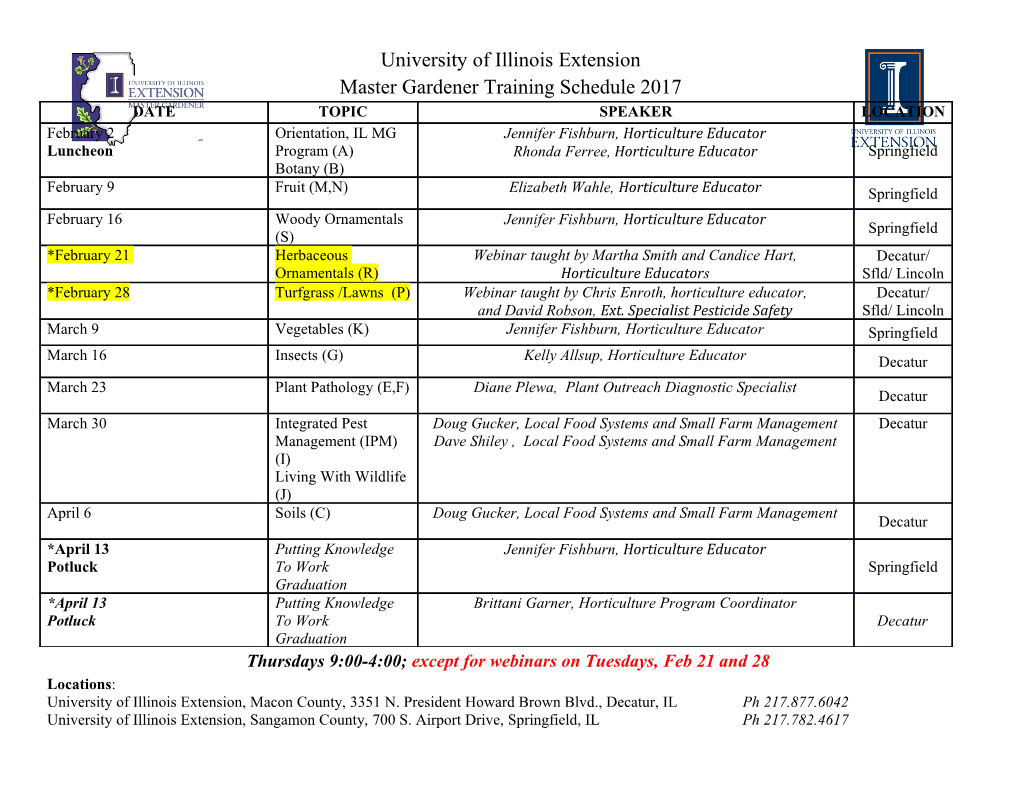
processes Review A Review of Crystallization Fouling in Heat Exchangers Jure Berce , Matevž Zupanˇciˇc , Matic Može and Iztok Golobiˇc* Faculty of Mechanical Engineering, University of Ljubljana, Aškerˇceva6, SI-1000 Ljubljana, Slovenia; [email protected] (J.B.); [email protected] (M.Z.); [email protected] (M.M.) * Correspondence: [email protected] Abstract: A vast majority of heat exchangers suffer from unwanted deposition of material on the surface, which severely inhibits their performance and thus marks one of the biggest challenges in heat transfer. Despite numerous scientific investigations, prediction and prevention of fouling remain unresolved issues in process engineering and are responsible for large economic losses and environmental damage. This review article focuses specifically on crystallization fouling, providing a comprehensive overview of the state-of-the-art of fouling in heat exchangers. The fundamentals of the topic are discussed, as the term fouling resistance is introduced along with distinct fouling behaviour, observed in laboratory and industrial environments. Insight into subsequent phases of the fouling process is provided, along with the accompanying microscale events. Furthermore, the effects of fluid composition, temperature, flow velocity, surface condition, nucleate boiling and composite fouling are comprehensively discussed. Fouling modelling is systematically reviewed, from the early work of Kern and Seaton to recently used artificial neural networks and computational fluid dynamics. Finally, the most common fouling mitigation approaches are presented, including design considerations and various on-line strategies, as well as off-line cleaning. According to our review, several topics require further study, such as the initial stage of crystal formation, the effects of ageing, the interplay of two or more fouling mechanisms and the underlying phenomena of several mitigation strategies. Citation: Berce, J.; Zupanˇciˇc,M.; Može, M.; Golobiˇc,I. A Review of Keywords: heat exchanger; fouling; energy efficiency; crystallization; fouling modelling; fouling mit- Crystallization Fouling in Heat igation Exchangers. Processes 2021, 9, 1356. https://doi.org/10.3390/pr9081356 Academic Editor: Weizhong Dai 1. Introduction Heat exchangers (HEs) are among the most widely used thermal devices and appear Received: 7 July 2021 Accepted: 29 July 2021 in various designs, such as shell and tube HEs, plate HEs, double pipe HEs. They can be Published: 1 August 2021 found in heating and refrigeration, power production and conversion, transport, chemical industry, waste heat recovery, petroleum and pharmaceutical industry, space applications Publisher’s Note: MDPI stays neutral or fluid treatment to name a few. As such, the entire HE market is valued in billions of euros, with regard to jurisdictional claims in and with increasing world population and energy demands it is expected to grow even published maps and institutional affil- larger. In several industrial and household heat transfer applications where HEs are found, iations. heat exchange fluids may contain certain amounts of dissolved or suspended material and can also provide a favourable environment for existence and growth of biological organisms. As a result, an unwanted accumulation of deposits on heat transfer surfaces, i.e., fouling, can occur. This induces a significant reduction of heat transfer coefficients Copyright: © 2021 by the authors. and causes changes in surface topography and flow geometry. In addition, substantial Licensee MDPI, Basel, Switzerland. pressure drops occur as a result of flow constriction and increased friction due to scale This article is an open access article formation, which can render a heat exchanger inoperable even sooner than the reduced distributed under the terms and thermal efficiency [1]. Substantial safety margins in the design, pre-treatment of fluids conditions of the Creative Commons and regular cleaning are thus needed to combat this problem, bringing about additional Attribution (CC BY) license (https:// costs and down-time. According to surveys [2,3], more than 90% of heat exchangers across creativecommons.org/licenses/by/ various industries are experiencing fouling problems. 4.0/). Processes 2021, 9, 1356. https://doi.org/10.3390/pr9081356 https://www.mdpi.com/journal/processes Processes 2021, 9, 1356 2 of 24 Processes 2021, 9, x FOR PEER REVIEW The effect of fouling on heat transfer equipment is generally described with2 addedof 25 thermal resistance as a result of the fouling layer. The calculation of the overall heat transfer coefficient U thus becomes: The effect of fouling on heat transfer equipment is generally described with added 1 1 A2 1 thermal resistance as a result= of the+ foulingRf,1 layer.+ RThewall calculation+ + Rf,2 of the overall heat trans(1)‐ U h1 A1 h2 fer coefficient U thus becomes: In Equation (1), h and A are the heat transfer coefficient and the heat transfer area 1 1 1 of the heat-exchanging fluids (subscripted, with 1 and 2), respectively,, while Rwall is(1) the thermal resistance of the wall, separating the two flows. Fouling resistance Rf comes from theIn deposit,Equation1, which h and accumulates A are the heat on one transfer or both coefficient sides of theand separating the heat transfer wall, depending area of the on theheat conditions‐exchanging present fluids in (subscripted the heat exchanger with 1 and (Figure 2), respectively,1). The term while can R bewall classified is the thermal as the differenceresistance betweenof the wall, reciprocal separating values the two of overall flows. heatFouling transfer resistance coefficients Rf comes prior from to the fouling de‐ posit, which accumulates on one or both sides of the separating wall, depending on the (Uc) and after fouling occurs (Uf) such that: conditions present in the heat exchanger (Figure. 1). The term can be classified as the dif‐ ference between reciprocal values of overall1 heat1 transfer1 coefficients prior to fouling (Uc) = − (2) and after fouling occurs (Uf) such that:R f Uf Uc 1 1 1 If one assumes constant values of U over the heat exchange area, the extra heat transfer(2) surface area needed to achieve the same performance is obtained as: If one assumes constant values of U over the heat exchange area, the extra heat transfer surface area needed to achieve theA samef = A performancec 1 + R f ·UC is obtained as: (3) 1 ∙ (3) Similarly, if one assumes a constant heat exchange area A, an increase in temperature differenceSimilarly, betweenif one assumes cold and a constant hot stream heat is exchange required area for theA, an same increase performance: in temperature dif‐ ference between cold and hot stream is required for the same performance: UC DTf = DTc 1 + R f ·UC = DTc (4) ∆ ∆1 ∙∆ Uf (4) ShouldShould neither neither of of the the discusseddiscussed parameters be adjusted adjusted to to accommodate accommodate fouling, fouling, the the heat heat exchangerexchanger will will experience experience aa deteriorationdeterioration of performance: QC (5) Q f = 1 ∙ (5) 1 + R f ·UC FigureFigure 1. 1.Schematic Schematic representationrepresentation of scaling in a heat exchanger. exchanger. TheThe processprocess of of fouling fouling can can be be classified classified into into six different six different types: types: (i) crystallization (i) crystallization foul‐ foulinging or scaling, or scaling, (ii) particulate (ii) particulate fouling, fouling, (iii) chemical (iii) chemical reaction reaction fouling, fouling,(iv) corrosion (iv) corrosion fouling, fouling,(v) biofouling (v) biofouling and (vi) and solidification (vi) solidification fouling; fouling; a combination a combination of various of variousmechanisms mechanisms is also ispossible also possible [4]. Out [4 of]. Outall fouling of all foulingtypes, crystallization types, crystallization fouling has fouling the most has harmful the most effect harmful on effectheat exchangers, on heat exchangers, which gives which merit gives to the merit emphasis to the placed emphasis on it placed in this onreview it in article. this review article.Depending on the heat transfer process and the accompanying fouling mechanisms, the observed fouling resistance can behave differently over time, as shown in Figure 2. This behaviour depends greatly on the strength of the formed deposit, i.e. weaker deposits generally exhibit an asymptotic fouling resistance, while hard and resilient ones have a Processes 2021, 9, 1356 3 of 24 Depending on the heat transfer process and the accompanying fouling mechanisms, Processes 2021, 9, x FOR PEER REVIEW 3 of 25 the observed fouling resistance can behave differently over time, as shown in Figure2 . This behaviour depends greatly on the strength of the formed deposit, i.e. weaker deposits gen- erally exhibit an asymptotic fouling resistance, while hard and resilient ones have a linear orlinear falling or rate falling tendency. rate tendency. The first threeThe first curves three in Figurecurves2 inshow Figure. idealized 2 show conditions, idealized while condi‐ thetions, saw-tooth while the represents saw‐tooth the represents oscillations, the due oscillations, to aging due induced to aging deposit induced break-off deposit [5], break that ‐ canoff be[5], found that can in some be found experimental in some experimental and industrial and data. industrial The three data. phases, The three visually phases, shown vis‐ inually Figure shown2, are in further Figure discussed 2, are further in the discussed
Details
-
File Typepdf
-
Upload Time-
-
Content LanguagesEnglish
-
Upload UserAnonymous/Not logged-in
-
File Pages24 Page
-
File Size-