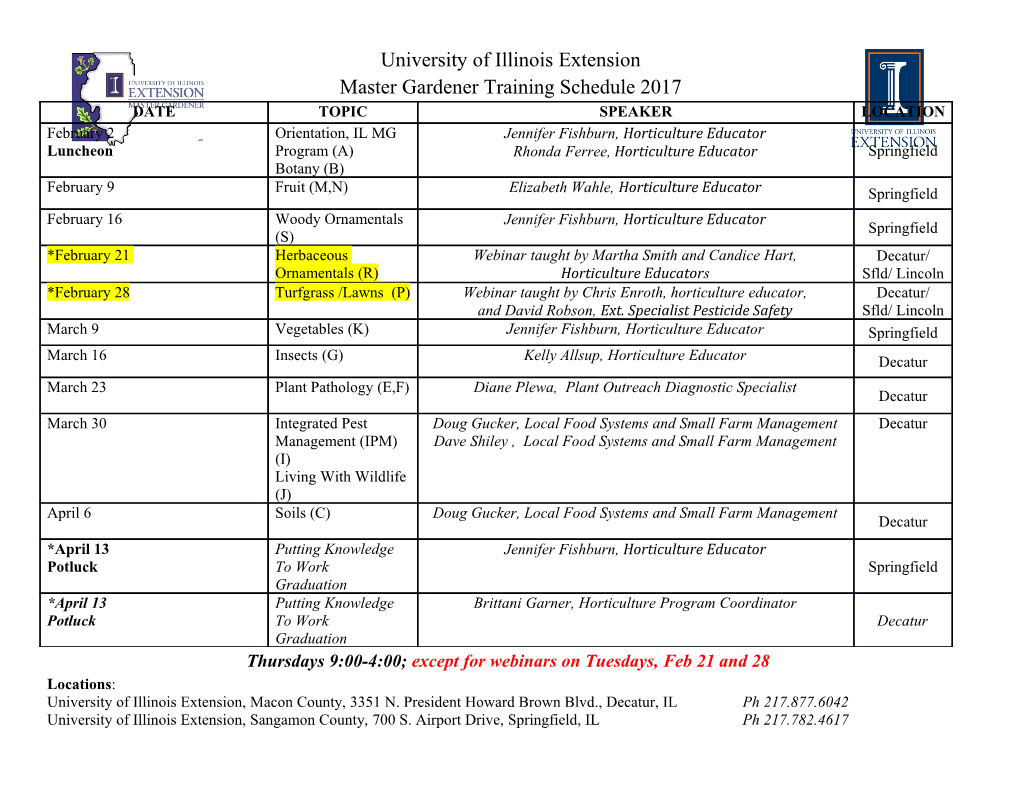
Quenched and Tempered Bar trengthening in steel is gener- the bar reheats to approximately Abstract Sally achieved by adding alloys 600-700°C. After the bar reach- to the liquid steel, causing dis- es its peak reheat temperature, In-line quenching and tempering tortions of the molecular lattice. it cools naturally until reaching has allowed CMC Steel Arizona Some of the steel standards that ambient temperatures. to have a higher-ductility bar at are available are either very open Figure 1 shows the typical higher strength levels compared on the chemistry requirements cooling and reheating curves of with classic rebar production, or else have no chemical restric- the surface of the bar, the cen- with a substantial reduction in tions at all. Two examples of such ter of the bar and the midway a standard are A615 and A706 point of the bar. The figure also alloy consumption. The results of for rebar production. The pur- shows the microstructure before implementing this process have pose of this paper is to describe quenching, after quenching and ranged from improved bundle quenched and tempered bar after tempering. The final bar quality to combined nigh-strength (QTB) as an alternate, cost- has a pearlite core, a thin layer of and high-ductility steel. effective means of achieving the mixed bainite and an outer shell mechanical requirements of the of tempered martensite. standards by quenching a hot After the bar has reached rolled bar to a surface tempera- ambient temperature, it behaves ture below martensitic transfor- more like a composite material mation to increase the strength than a single, solid material. For of the bar, and then tempering example, steel-reinforced con- the martensitic surface of the crete has the tension-bearing bar to promote ductility. This properties of the steel and the paper considers the QTB over- compression strength of the con- Author view, microstructural evaluation, crete. Similarly, a QTB bar has implementation, quality assur- the ductility of the core of the ance of the process, and the bar and the strength of the case Jacob Selzer advantages and disadvantages of of the bar. By reducing the allo\ plant metallurgist and quality assurance using QTB in place of a tradi- additions, the core of the bar is CMC Steel Arizona, Mesa, Ariz. [email protected] tional, alloy-based process. softer and more ductile than the fully alloyed counterpart. The tensile strength is determined QTB Overview by the combination of bar chem- QTB is designed to be installed istry and the depth of quench in-line with the rolling process. achieved during the quenching The hot rolled bar is fully sub- phase of the process. The end merged in water in order to rap- result is that the elongation pen- idly cool the surface of the bar alty is reduced when increasing below the martensitic transfor- yield and tensile strength, com- mation temperature. This phase pared to traditional strengthen- of the process creates a hard- ing methods for hot rolled bar. ened "case" on the outside of the Steel that is manufactured bar. The core of the bar remains from recycled scrap can face austenitic. The residual heat in another challenge related to the core of the bar radiates out the raw materials. There are to the shell of the bar, temper- elements that can have signifi- ing the newly formed martensite. cant impact to the mechanical During this time, the surface of properties of the steel that are 106 • l'on S. Steel Technology A Publication of the Association for Iron & Steel Technology Figure 13 Figure 14 Figure 2 PEARLFTE FERRITE MIXED BAINITE Ш Atom TEMPERED QUENCHING STASE TEMPERING STAGE FINAL COOLING TIME Thermal path of the QTB process. Ferrite "molecule" (body centered cubic). present in ever-changing quantities in the scrap and in the final product. Examples of these elements are Figure 3 Cr, Ni, Mo, Co and W. The aim carbon for a typical QTB rebar application is between 0.25 and 0.30%. As a result, carbide-forming residuals have a lessened effect compared to when they are found in fully alloyed steel. Also, when using QTB, the mechanical properties are not determined by chemistry alone, so the operator is able to adjust the quenching phase of the process to adapt to the changes in chemistry. The process is able to absorb a wider range of residu- als in the steel scrap compared to a more traditional process, while still achieving the strength aims of the standard being manufactured. QTB Microstructural Evaluation Steel is an allotropie material, meaning it can exist in different crystalline structures. Most "plain" carbon steel exists in the ferrite microstructure. It is magnetic, stable and, for the strength it imparts, it remains reasonably ductile. Because steel is allotropie, it can be heat treated to change the mechanical properties of the metal. An alternate steel microstructure that Martensite "molecule ' (hexagonal bipyramid). is also stable at ambient temperature is martensite. Martensite is stronger and harder than ferrite and has a correspondingly lower ductility. Figures 2 and Figure 4 3 represent comparison renderings of the molecular structures. The ferrite rendering (Figure 2) is typical of most carbon steels. The martensite rendering (Figure 3) is typical of the surface (case) of a QTB-treated bar. Tempering the martensite is necessary to reduce internal stresses to the newly formed martensite and to eliminate brittleness in the final bar. Comparison micro etches are shown in Figures 4 and 5. The core of the QTB-treated bar (Figure 6) is pearlitic. Grain refinement of the pearlitic core of the bar is observed compared with as-rolled bar of identical chemistry (Figure 7). This grain refinement contributes to the generally improved elongations of Etchant: Nital 3% Mag: 500x QTB-treated bar compared to the fully alloyed bar. This characteristic of the QTB-treated bar allows the Crude (untempered) martensite. AIST.org August 2012 4-111 Figure 5 Figure 6 Figure 7 WiÊÈÈÊWÊÊSSm: ШЯшшШшЁЁт "i- Etchant: Nital 3% Mag: 500x Etchant: Nital 3% Mag: 100x ' Etchant: Nital 3% Mag:100x s Tempered martensite. QTB 19-mm rebar case and eore As-rolled 19-mm rebar core (1026 (1026 chemistry). chemistry). manufacturer to increase the strength of the bar with- the closer the cooler inside diameter (ID) is to the size out sacrificing ductility of the bar. of the bar being quenched, the more powerful the Figure 8 is a micro etch of a QTB-treated bar show- quenching effect will be. When sizing the coolers, the ing the surface and the microstructural transition engineer must also consider the challenges of thread- from surface to core. This sample is 3/4 inch, grade ing the bar through the tubes. For example, a 2-inch 60 rebar with chemistry conforming to AISI 1026. ID cooler will be ineffective quenching a У 2-inch bar. Starting at the surface of the bar, the microstructure A 7/8-inch ID cooler will be difficult to repeatedly is tempered martensite. Moving toward the center of thread a 3/4-inch bar through. the bar, the tempering becomes more pronounced, The quenching process starts when the bar enters which is viewed as a "softening" of the microstructure. the first tube. The next critical event is to provide the At the transition from martensite to ferrite, approxi- system with a definite stopping point to the quench- mately 0.035 inch below the surface, there is some evi- ing process. To do this, a different tube, called a dence of mixed bainite. The pearlitic structure begins "stripper," is installed in the quench box. The stripper from this point through to the center of the bar. functions the same way as a cooler, but the water is applied against the direction of travel instead of with Implementation in Production it. The stripper uses a high-pressure water spray and Implementation in production requires good water air to blast any residual water off the bar, so that when quality, a pumping system capable of handling the required volumes and pressures of water to achieve Figure 8 martensitic transformation, and a delivery system « -s:-----1.-- .г-- r --- vr- -i? capable of evenly distributing water pressure and flow around the surface of the bar. Water must be deliv- ered to the bar with enough pressure to prevent boil- ing of the water, generating steam at the bar surface. The part responsible for water delivery is commonly called a "cooler." Figure 9 is a schematic showing the water delivery to the bar for one cooler. The cooler shown in Figure 9 is supplied with high- pressure water and is capable of sustaining high flow- rates of water. In practice, multiple coolers are placed in series in order to obtain the desired quenching power of the system, as shown in Figure 10. Water must be supplied with sufficient pressure to avoid steam generation — commonly called a "steam barrier." Steam acts as a thermal insulator and reduces the rate at which heat is extracted from the bar, which can prevent formation of martensite. Several consider- ations are needed to maintain effective quenching. A pumping system must, be installed that can maintain the pressure and flowrates to create martensite on the surface of the bar. Second, the coolers must be sized Etchant: Nital 3% Mag: 100x: appropriately for the bar being produced. In general, QTB surface, transition and core. 110 • Iron & steel Technology A Publication of the Association for Iron & Steel Technology Figure 9 Water Water Rolling Direction Representation of a functioning QTB cooler. Figure 10 Water Water. Hoi Sto-'l Cooler • Quenched Steel Water- Water Representation of QTB coolers in series.
Details
-
File Typepdf
-
Upload Time-
-
Content LanguagesEnglish
-
Upload UserAnonymous/Not logged-in
-
File Pages7 Page
-
File Size-