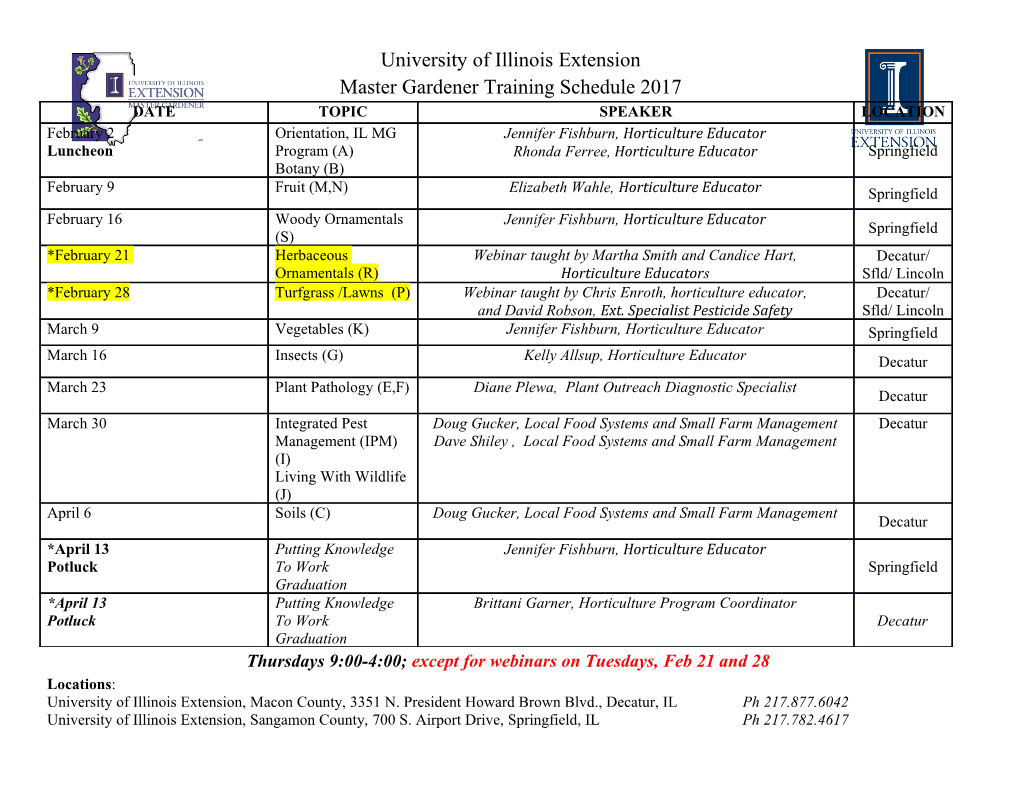
X-33 Flight Operations Center ~9 v ANNUAL PERFORMANCE REPORT April 1,1998 - March 31,1999 Lockheed Martin Skunk Works Cooperative Agreement NCCB- 1 15 LOCKYWWD mAlrlY- & CGoodrich ~S~CIEIAIO Aerospace -DY~ Forward In response to Clause 17 of the Cooperative Agreement NCC8-115, Lockheed Martin Skunk Works has compiled an Annual Performance Report of the X-33/RLV Program. This report consists of individual reports from all industry team members, as well as NASA team centers. Contract award was announced on July 2, 1996 and the first milestone was hand delivered to NASA MSFC on July 17,1996. With the dedication of the launch site, and continuing excellence in technological achievement, the third year of the Cooperative Agreement has been one of outstanding accomplishment and excitement. Lockheed Martin Skunk Works Vehicle Development Operations Development X-33 and RLV Systems Engineering Manufacturing Ground Operations Reliability, MaintainabilitylTestability, Supportability, & Special Analysis Team X-33 Flight Assurance Lockheed Martin Technical Operations Launch Support Systems Ground Support Equipment Flight Test Operations RLV Operations Development Support Lockheed Martin Space Operations TAEM and AIL Guidance and Flight Control Design Evaluation of Vehicle Configuration TAEM and AIL Dispersion Analysis Modeling and Simulations Frequency Domain Analysis Verification and Validation Activities Ancillary Support Lockheed Martin Astronautics - Denver Systems Engineering X-33 Development Sanders - A Lockheed Martin Company Vehicle Health Management Subsystem Progress GSS Progress Lockheed Martin Michoud Space Systems X-33 Liquid Oxygen (LOX) Tank Key Challenges Page Lessons Learned 70 X-33/RLV Composite Technology 7 2 Reusable Cyrogenic Insulation (RCI) and Vehicle Health Monitoring 74 Main Propulsion Systems (MPS) 78 Structural Testing 80 X-33System Integration and Analysis 82 Cyrogenic Systems Operations 83 X-33 Flight Operations Center Dedication Pictured from left: Jerry Rising, President of Venturestarm LLC (A Lockheed Martin Company), Jack Gordon, President of Lockheed Martin Skunk Works, Daniel Goldin, NASA Administrator, Major General Richard V. Reynolds, Commander of Air Force Flight Test Center. X-33 Flight Operations Center Dedication Pictured Dan Goldin, NASA ~dmini&ator, Jack Gordon, President of Lockheed ~ar&Skunk Works, Major General Richard V. Reynolds, Commander of Air Force Flight Test Center. Lockheed Martin Skunk Works Single Stage to Orbit / Reusable Launch Vehicle 9 I ,' -,:=j- Vehicle Development Design Configuration optimization completed this year as LMSW demonstrated the benefit of a partially protruding faired payload to produce a vehicle with higher propellant mass fraction. To validate the parametric database used in developing this configuration, a comprehensive structural and systems design and analysis was completed. The lessons learned from the X-33 Technology Demonstrator program have been incorporated into the latest RLV design, including a uniform TPS interface to the airframe, elimination of honeycomb core from cryogenic tanks, and dual purpose/redundant structural load paths throughout. Detail structural design and analyses completed on this configuration demonstrated a 10.7% improvement in vehicle propellant packing efficiency. A fully modular wind tunnel test program is now underway to validate the flying qualities of this vehicle. Graphite composite structure is essential to achieving the high propellant mass fraction required for a single-stage-to-orbit vehicle. All but the aerosurfaces (canted finfvertical fin/body flap) have been configured using graphite composites, and reflect structural optimization studies from NASA Langley Research Center, and LMSW's own optimization work. The aerosurfaces were optimized as titanium hot structures. Over 25 separate trade studies were completed to verify the optimum load path and lightweight structure used in the current baseline RLV design. Page 3 Studies were conducted on payload accommodations and airborne support equipment to aid in developing the RLV mission module baseline concept. Both commercial satellite missions and ISS missions were rigorously evaluated to maximize mission flexibility. LMSW and the NASA Langley Research Center worked closely together to assess payload interface requirements, and develop detail design layouts of the mission module, payload bay support structure, and payload bay doors for several iterations of the RLV baseline configuration. Producibility Manufacturing was an active participant in the design layouts prepared during the past year. The design of the RLV LH2 and LO2 tanks emphasizes keeping the construction details as similar as possible to limit the costs of tooling. This was achieved by selecting a constant tank cross section. Alternate joint concepts were defined to address scale-up issues with the baseline RALPH process. A mechanically fastened or e-beam processing are under consideration. Titanium ingot sizes for the larger structures of the vehicle i.e. wing spars, stub spars, landing gear bulkhead, etc. to support the fewest number of splices were reviewed with a local titanium company. The TPSS standoff interface was redesigned to address manufacturing lessons learned during X-33 rosette installation. LMSW worked closely with BFG to establish a better design for the proposed RLV standoff designs and their installation process. Future activity will focus on standoff producibility and the material to use as a thermal isolator between it and the ring frame. Laser sintering applications, alternate materials (AMC, CMC, et al), holograms for tooling applications and simulation tools for composite lay-ups are under study for incorporation into the RLV manufacturing process. Page 4 LOCIYWWD mnnr1m- IGoodrioh @..ni~~n ~l.o*?lcl Aerospace -~h '=""-a!r Propulsion Design and flight sciences work closely with Rocketdyne to develop the propulsion system design for the RLV. Rocketdyne delivered an engine deck to model the RLV propulsion system performance. The model was used to support trajectory analysis in optimizing the vehicle performance, as well as Trade studies on engine area ratio, nozzle length, mixture ratio, number of engines, and inlet pressure to the pumps were performed on the main propulsion system. Orbital maneuvering and reaction control systems were analyzed to select an optimum propellant combination. The baseline approach of performing orbital maneuvers using the main propulsion system was replaced with a separate orbital maneuvering system using liquid hydrogen and liquid oxygen. The baseline reaction control system was changed from a gas blowdown hydrogen and oxygen system to a liquid oxygen and ethanol system. Flight Sciences Several candidate trajectories were analyzed to define RLV external heating characteristics. Rapid temperature transients are experienced early in reentry and ascent. TPS stress indicators are driven by the time derivatives of dynamic pressure and heating rate. Trajectory and atmospheric dispersions appear to have a greater impact than boundary layer transition dispersions. Non-continuum heating effects are significant for TPS and trajectory design. Results of the external heating studies were used to assess internal heating characteristics. A hot structure approach can be used for the leeward side of the canted fins. The impact of plume radiation heating in the base region is mitigated with low absorptivity coatings. Heat flux into vehicle structure after landing is not significant. The initial temperature gradient experienced by the TPS is high due to on-orbit environment. TPS stress and creep indicators were incorporated into the trajectory design process. A strategy for minimizing the integrated product of dynamic pressure and heat rate was Page 5 developed to keep TPS stress indicators within an acceptable range. These trajectories keep the vehicle higher in the atmosphere during the early reentry phase. Vehicle configurations and were analyzed for control characteristics along candidate trajectories. Landing studies indicate vehicle drag to weight ratio should be no larger than 0.5 for landing. Control analysis indicates aerodynamic instability levels greater than 2% will be difficult to accommodate during any phase of flight. Several candidate vehicle configurations were analyzed for aerodynamic and stability characteristics. Semi-submerged payloads can be incorporated without introducing large drag penalties. Additional vertical tail volume is required for semi-submerged payload configurations. Additional canted fin incidence is required for semi-submerged payload configurations during transonic flight. Canted fin position and orientation is significant to hypersonic lateral-directional stability. Body shape provides a substantial contribution to hypersonic longitudinal and lateral-directional stability. Avionics During the past year, the avionics effort concentrated on refinement of the system requirements and the allocation of these requirements to the avionics, software and health management elements. Additional effort was directed toward the development of candidate avionics system architectures and the development of an accurate baseline for evaluating changes to the configuration (weight, power, cooling, performance and cost). Lessons learned from the X-33 as well as technical discussions with the supporting NASA Centers helped to define and refine this baseline. The RLV baseline architecture was established and submitted for review. Primary areas
Details
-
File Typepdf
-
Upload Time-
-
Content LanguagesEnglish
-
Upload UserAnonymous/Not logged-in
-
File Pages287 Page
-
File Size-