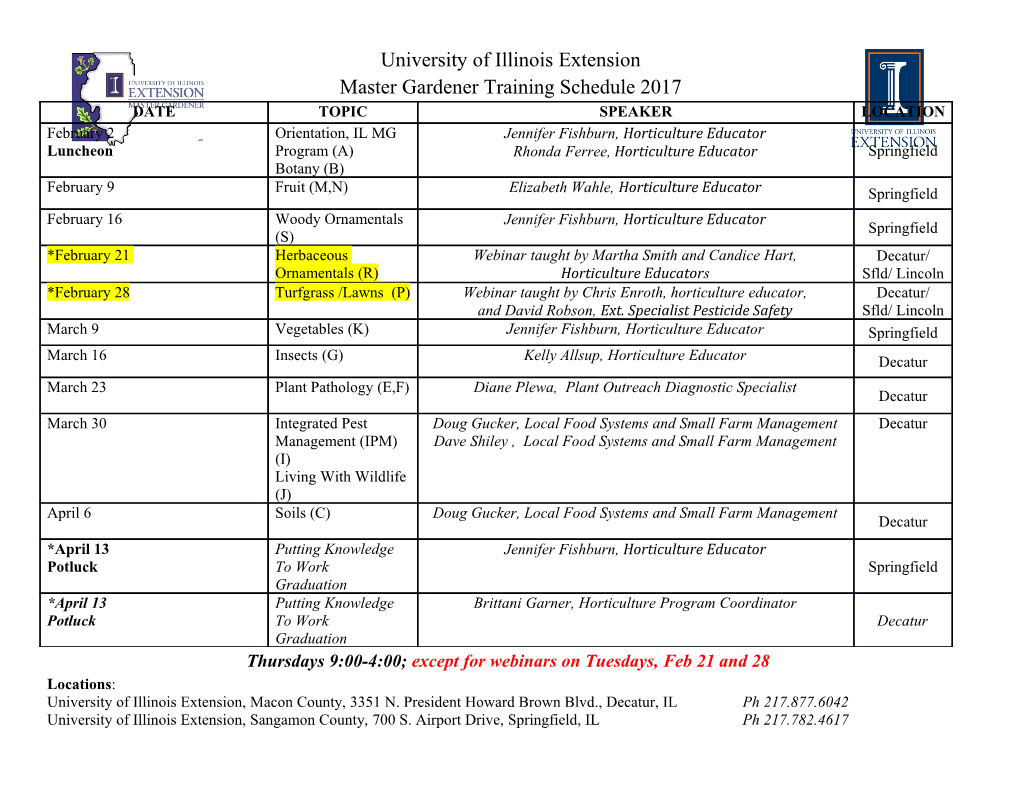
NASA Technical Memorandum 104247 Effects of Bleed Air Extraction on Thrust Levels of the F404-GE-400 Turbofan Engine Andrew J. Yuhas PRC Inc., Edwards, California Ronald J. Ray NASA Dryden Flight Research Facility, Edwards, California 1992 N/kS/_ National Aeronautics and Space Administration Dryden Flight Research Facility Edwards, California 93523-0273 EFFECTS OF BLEED AIR EXTRACTION ON THRUST LEVELS OF THE F404-GE-400 TURBOFAN ENGINE Andrew J. Yuhas* PRC Inc. P.O. Box 273 Edwards, California 93523-0273 Ronald J. Ray** NASA Dryden Flight Research Facility P.O. Box 273 Edwards, California93523-0273 Abstract EAFB Edwards Air Force Base, Edwards, CA EBAS A ground test was performed to determine the effects excess bleed air system of compressor bleed flow extraction on the perform- ECS environmental control system ance of F404-GE-400 afterburning turbofan engines. FFC forebody flow control The two engines were installed in the F/A-18 High GE General Electric Alpha Research Vehicle at the NASA Dryden Flight Research Facility. A specialized bleed ducting system HATP High Alpha Technology Program was installed onto the aircraft to control and measure HARV High Alpha Research Vehicle engine bleed airflow while the aircraft was tied down HPC to a thrust measuring stand. The test was conducted high-pressure compressor on each engine and at various power settings. The HPT high-pressure turbine bleed air extraction levels analyzed included flow rates LPT low-pressure turbine above the manufacturer's maximum specification limit. LPC The measured relationship between thrust and bleed low-pressure compressor flow extraction was shown to be essentially linear at M Mach number all power settings with an increase in bleed flow caus- N1 fan rotor speed, rpm or percent ing a corresponding decrease in thrust. A comparison N2 with the F404-GE-400 steady-state engine simulation high compressor rotor speed, rpm or showed the estimation to be within ±1 percent of mea- percent sured thrust losses for large increases in bleed flow rate. PAMB ambient pressure, psia PLA power lever angle, deg Nomenclature PS3 compressor discharge static pressure, psia PT56 turbine exhaust total pressure, psia ALT pressure altitude, ft TVCS thrust vectoring control system AOA angle-of-attack, deg T1 fan inlet temperature, °R A8 nozzle throat area, in 2 or percent T25 compressor inlet temperature, °R BV1 excess bleed air system control valve 1 T56 low rotor turbine exit temperature, °R BV2 excess bleed air system control valve 2 or °C) DTAMB ambient temperature increment from WFE combustor fuelflow,(Ib/hr) standard day temperature, °R *Senior Propulsion Research Engineer. Introduction ** Aerospace engineer. Copyright (_)1992 by the American Institute of Aeronau- The High Alpha Technology Program (HATP) was tics and Astronautics, Inc. No copyright is asserted in the initiated within NASA to develop and demonstrate United States under Title 17, U.S. Code. The U.S. Govern- ment has a royalty-free license to exercise all rights under concepts that provide favorable control and maneu- the copyright claimed herein for Governmental purposes. All verability for high-performance aircraft at high-angle other rights are reserved by the copyright owner. of attack. 1 Current fighters have degraded maneuver- Because the pneumatic FFC studies for the F/A-18 ability at high-angle of attack because of loss in aero- were encouraging, the HATP initiated a feasibility dynamic control surface effectiveness. One of the tech- study for a full-scale flight-test program to be con- nologies studied to enhance aerodynamic control is the ducted. To support this goal, the NASA Ames Re- use of pneumatic forebody flow control (FFC). The search Center at Moffett Field, CA, formed a research FFC injects air from a slot on the aircraft forebody team from Dryden and Moffett to evaluate engine to manipulate the forebody vortices that form at high- bleed air capability and aircraft environmental bleed angles of attack. For pneumatic FFC to be feasible, a air requirements on a full-scale aircraft. The F/A-18 significant supply of high-pressure airflow is required. High Alpha Research Vehicle (HARV) was equipped with a specially designed ducting system known as Experiments have demonstrated that the manipula- the excess bleed air system (EBAS) and tested on the tion of the asymmetric forebody vortices of a fighter at universal horizontal test stand at Edwards Air Force high-angle of attack through various blowing schemes Base (EAFB). This ducting system branches off from can have a strong effect on the yawing moment? -4 the aircraft environmental control system (ECS) and Forebody flow control feasibility studies into various is- allows engine bleed extraction to be controlled and sues have been conducted by various government agen- measured. Various ground test objectives were per- cies including NASA. The X-29 Advanced Technology formed using EBAS, including the determination of Demonstrator will test a simple pneumatic blowing sys- bleed air extraction effects on engine performance and tem to demonstrate FFC effectiveness. 5 The X-29 sys- operability. tem will use a compressed air bottle to supply the high- pressure air and is limited to a total of 20 sec of op- This paper addresses the measurement of thrust loss eration. The HATP supported research on pneumatic during increases in bleed air extraction for an F404-GE- FFC applications to an F/A-18, including various wind 400 engine installed on the F/A-18 HARV. A compar- tunnel tests. One feasibility study looked at various ison of the predicted thrust loss provided by an engine ways to obtain the estimated flow rates required. These computer simulation and the measured values will be included compressed or liquefied gas bottles, an aux- presented. The analysis offers a comparison of each en- iliary compressor, or engine bleed air. The results of gine at various power settings. A detailed description this study predicted that only engine bleed air would of EBAS and its function will also be presented. meet the mass flow requirements over an extended time period, e Bleed extraction however, has a negative ef- Description of Equipment and Model fect on engine performance. A past study on an F100- F-18 High Alpha Research Vehicle PW-220 engine predicts up to 2 percent of net thrust loss for each percent of airflow extracted for bleed. 7 The HARV (Fig. 1) is a one-of-a-kind research air- craft located at the NASA Dryden Flight Research EC 91-201-9 Fig. 1. F/A-18 High Alpha Research Vehicle (HARV). ORIGIr,,IAL P_E BLACK AND WHITE PHOiOGRAI..'r_ Facility.This pre-production,single-seatF/A-18 air- modifiedto provide a selectableturbine dischargetem- crafthas been uniquely modified to perform extensive perature biasforadditionalengine stallmargin at high flighttestingin the high-angle-of-attack(AOA) region. AOA. These modificationsinclude a thrust vectoringcontrol system (TVCS). The incorporationof the TVCS re- The controlsystem has two basicmodes of operation which aredependent on the throttlesetting(PLA). Be- quired modificationsto the aircraftavionics,flightcon- trols,hydraulics,cockpit,and engines.I low Militarypower, high compressor rotorspeed (N2) and exhaust nozzle area (A8) are scheduled. Throt- F404-GE-400 Turbofan Engines tle positionand compressor inlettemperature (T25) Two pre-production F404-GE-400 engines (General schedule N2. The throttlepositionschedules A8. At Electric,Lynn, Massachusetts) are installedin the Militaryand above, the controlsystem schedulesmax- HARV. The F404-GE-400 (Fig.2) is a two-spool,low imum fan speed (N1) and maximum low-pressuretur- bypass axial-flowturbofan with afterburner.The en- bine exittemperature (T56). Fan speed is controlled gine consistsof a 3-stage fan, 7-stage high-pressure as a function of engine inlettemperature (TI). The variableexhaust nozzle is modulated to maintain the compressor, annular combustor, l-stagehigh-pressure scheduled T56 which is a function of T1 and ambient turbine,and 1-stagelow-pressureturbine.Variablege- pressure (PAMB). ometry isincorporated into the fan and high-pressure compressor along with a convergent-divergentnozzle. Aircraft-Engine Bleed Air System The F404 engines on the HARV have the divergent Bleed aircomes from an annular manifold at the exit portion of the nozzle and externalflapsremoved to in- of the high-pressurecompressor of each engine (Fig.3). corporate the TVCS. The engine controlsystem was A bleedairpressureregulatorand shutoffvalvein each EC91-201-9 Fig.2. F404-GE-400 turbofan engine. LPT discharge measuring plane Exhaust LPC HPC LPT Afterburner nozzle throat Inlet discharge discharge Inlet Exhaust Exhaust Free- Engine I HPC ICombustor nozzle nozzle stream Inlet discharge I 'ni°'I InletI I discharge I I 0 1 2 2.5 3 4 5 5586 7 8 9 manifold 920148 Fig. 3. F404 engine showing compressor bleed and measured engine parameters. engine compartment is controlled by the bleed air knob Excess Bleed Air System located in the cockpit. The cockpit control allows bleed The EBAS was a specially designed ducting system air to be selected from either or both engine sources, for measuring bleed air flow rates from the F/A-18 or to be turned off. The bleed air passes through a HAKV (Fig. 6). The EBAS hardware was designcd check valve which prevents reverse flow from one en- by NASA Ames Research Center at Moffett Field, CA gine to the other. The bleed air lines are then teed and is illustrated schematically in Fig. 7. The system together. The bleed air line is routed up the backbone consists of two principal sections, the ECS flow mea- of the aircraft over the fuel tanks and then down into surement section and the bleed airflow dump section. the ECS and heat exchanger ejectors (Fig. 4). Bleed The ECS flow measurement section required a section flow is regulated by the ECS. Maximum engine bleed is of ECS duct along the backbone of the aircraft to be re_ limited by the size of the bleed port on the engine but moved and replaced with modified ducting and a Ven- can exceed the manufacturer's maximum specification turi flowmeter (Fig.
Details
-
File Typepdf
-
Upload Time-
-
Content LanguagesEnglish
-
Upload UserAnonymous/Not logged-in
-
File Pages16 Page
-
File Size-