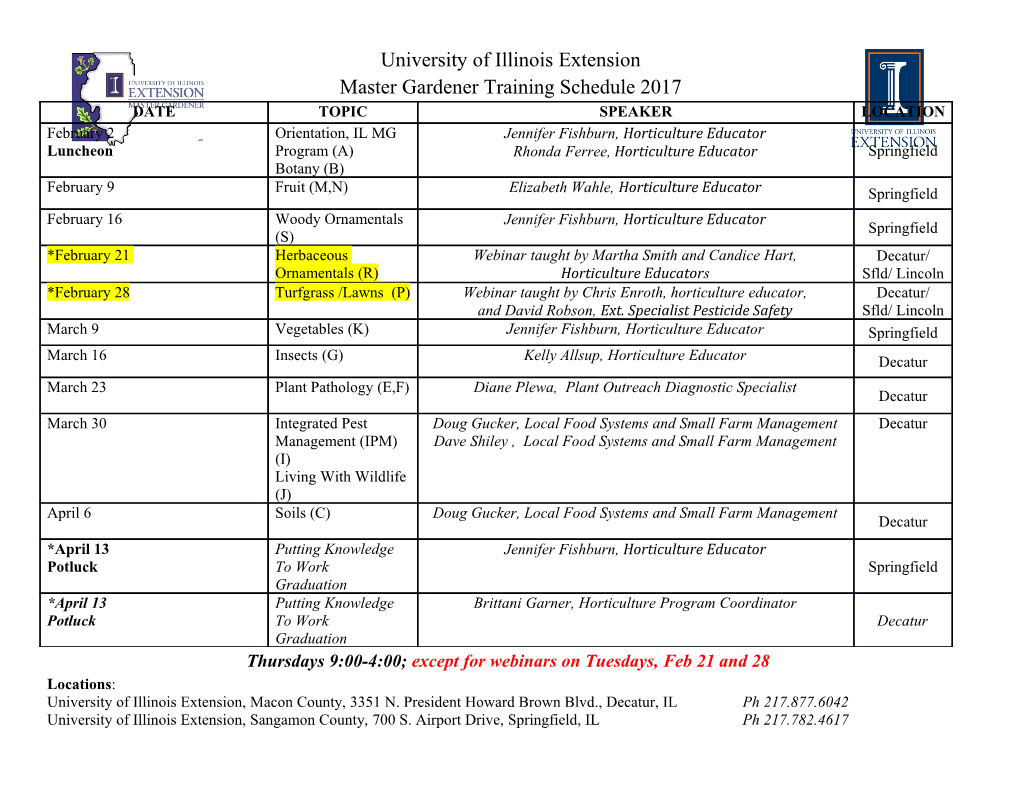
fract.qxd 7/15/03 7:27 PM Page 1 FRACTO-Fractographic features are critical to failure analysis of metals and plastics. GRAPHIC Ronald J. Parrington* IMR Test Labs Lansing, New York FEATURES in Metals and Plastics ractography is the science of examining fracture surfaces. When material failure in- volves actual breakage, fractography can identify the fracture origin, direction of Fcrack propagation, failure mechanism, material de- fects, environmental interaction, and the nature of stresses. Fractography of plastics is a relatively new field, with many similarities to metals. Common failure modes include ductile overload, brittle fracture, im- pact, and fatigue. Analogies can also be drawn between stress corrosion cracking (SCC) in metals/ stress cracking in plastics, corrosion/chemical aging, de-alloying/scission, residual stress/frozen- in stress, and welds/knit lines. Stress raisers, microstructure, material defects, and thermo- mechanical history play important roles in both materials. This article describes some of the macroscopic and microscopic features considered by the failure analyst to evaluate fracture surfaces of metals and plastics. It discusses several case histories in order to explain key fractographic features for metals and Fig. 1— This image shows the hollowing out of a polyacetal hinge due to acid plastics, and to compare and contrast various as- catalyzed hydrolysis, a form of scission. pects of failure analysis and fractography. • High residual stresses can result from metal Causes of failure forming, heat treatment, welding, and machining. The primary objective of a failure analysis is to Similarly, high frozen-in stresses contained by in- determine the root cause. Whether dealing with jection molded plastic parts often contribute to metallic or nonmetallic materials, the root cause can failure. normally be assigned to one of four categories: de- • Porosity and voids are common to metal cast- sign, manufacturing, service, or material. In prac- ings and plastic molded parts. These serve as stress tice, several adverse conditions frequently con- raisers and reduce load carrying capability. tribute to the part failure. • Adverse thermo-mechanical history, poor mi- Improper material selection and stress concen- crostructure, and contamination are among other trations are examples of design-related problems manufacturing- and material-related problems that that can lead to premature failure. Material selec- may lead to failure. tion must take into account environmental sensi- Many service-related causes are also found to be tivities as well as requisite mechanical properties. the reason for failures. Environmental degradation Fractures frequently originate at stress raisers, par- is one of the most important service-related causes ticularly in fatigue. These include thread roots, of failure for both metals and plastics. Others in- sharp radii of curvature, through-holes, and sur- clude excessive wear, impact, overloading, and elec- face discontinuities such as gate marks in molded trical discharge. plastic parts. Likewise, many manufacturing and material Failure mechanisms problems found in metals are also observed or have Another key objective of failure analysis is to a corollary in plastics. identify the failure mechanisms. Once again, some • Weldments are a troublesome area for metals, failure mechanisms are identical for metals and as are weld lines or knit lines in molded plastics. plastics. These include ductile overload, brittle frac- *Member of ASM International ture, impact, fatigue, wear, and erosion. ADVANCED MATERIALS & PROCESSES/AUGUST 2003 37 fract.qxd 7/15/03 7:27 PM Page 2 Fig. 2— Hydrogen damage of an in- Fig. 3— Explosive decompression fractures Fig. 4 — Beach and radial marks are visible duction hardened steel piston rod displays of rubber O-rings are characterized by fisheye- on this torsional fatigue fracture of a six-inch di- “fisheyes.” like patterns. ameter shaft made of 4340 steel. Analogies can also be drawn between metals and Many macroscopically visible fractographic fea- plastics with regard to environmental degradation. tures serve to identify the fracture origin and di- Whereas metals corrode by an electrochemical rection of crack propagation. Fractographic features process, plastics are vulnerable to chemical changes common to metals and plastics are radial marks from aging or weathering. Stress corrosion cracking, and chevron patterns. Radial marks (Fig. 4) are lines a specific form of metallic corrosion, is similar in on a fracture surface that radiate outward from the many ways to stress cracking of plastics. Both re- origin and are formed by the intersection of brittle sult in brittle fracture due to the combined effects fractures propagating at different levels. Chevron of tensile stress and a material-specific aggressive patterns or herringbone patterns are radial marks environment. resembling nested letters “V,” and pointing towards Likewise, corrosion pitting and de-alloying or the origin. selective leaching in metals, defined as the prefer- Fatigue failures in metals display beach marks ential removal of one element from an alloy by cor- and ratchet marks that serve to identify the origin rosion, are somewhat similar to scission. This is a and the failure mode. Beach marks (Fig. 4) are form of aging that can cause chemical changes by macroscopically visible semi-elliptical lines run- selectively cutting molecular bonds in polymers ning perpendicular to the overall direction of fa- (Fig. 1). tigue crack propagation and marking successive Analogies can also be drawn between metals and positions of the advancing crack front. rubber, which is another type of polymer. The pre- Ratchet marks are macroscopically visible lines cipitation of internal hydrogen in steels can lead to running parallel to the overall direction of crack hydrogen damage, which is characterized by lo- propagation. They are formed by the intersection calized brittle areas of high reflectivity known as of fatigue cracks propagating from multiple ori- flakes or fisheyes on otherwise ductile fracture sur- gins. faces (Fig. 2). Brittle fractures in plastics exhibit characteristic Similarly, explosive decompression in rubber features, several of which are macroscopically vis- O-rings produces fisheye-like ovular patterns on ible (Fig. 5). These may include a mirror zone at the the fracture surfaces (Fig. 3). Explosive decom- origin, mist region, and rib marks. The mirror zone pression is the formation of small ruptures or em- is a flat, featureless region surrounding the origin bolisms that develop when an elastomeric seal, and associated with the slow crack growth phase saturated with high pressure gas, is subjected to of fracture. The mist region is located immediately an abrupt pressure reduction. adjacent to the mirror zone and displays a misty appearance. This is a transition zone from slow to Macroscopic fractures fast crack growth. Rib marks are semi-elliptical lines On a macroscopic scale, all fractures (metals and resembling the beach marks in metallic fatigue plastics) fall into one of two categories: ductile and fractures. brittle. Ductile fractures are characterized by material Microscopic features tearing, and they exhibit gross plastic deformation. On a microscopic scale, ductile fracture in metals Brittle fractures display little or no macroscopically (Fig. 6) displays a dimpled surface appearance cre- visible plastic deformation, and require less energy ated by microvoid coalescence. Ductile fracture in to form. plastics (Fig. 7) is characterized by material Ductile fractures result when stresses exceed the stretching related to the fibrillar nature of the material yield or flow stress. Brittle fractures gen- polymer’s response to stress. Although a part may erally develop well below the material yield stress. fail in a brittle manner, ductile fracture morphology In practice, ductile fractures result from over- is frequently observed away from the origin, if the loading or under-designing. They are rarely the final fast fracture was caused by ductile overload subject of a failure analysis, which usually involves (e.g., the “shear lip” in metal failures). The extent the unexpected brittle failure of normally ductile of this overload region is an indication of the stress materials. level. 38 ADVANCED MATERIALS & PROCESSES/AUGUST 2003 fract.qxd 7/22/03 8:32 AM Page 3 100 microns 100 microns Fig. 5 — Brittle fracture of an epoxy layer Fig. 6 — Dimpled appearance typical of duc- Fig. 7 — Fracture of a polyethylene tensile displays a mirror zone, rib marks, and hackles. tile fracture of metallic materials. test specimen exhibits material stretching. 100 microns 100 microns 20 microns Fig. 8 — Brittle fracture of a powder-forged Fig. 9 — Intergranular fracture of an em- Fig. 10 — Fatigue striations are visible on steel connecting rod displays cleavage facets. brittled cast steel pneumatic wrench. this Type 302 stainless steel spring fracture. Brittle fracture of metallic ma- erials may result from a variety of failure mechanisms, but only a few basic micro-fractographic features clearly indicate the failure mecha- nism: cleavage facets (Fig. 8); inter- granular facets (Fig. 9); and striations (Fig. 10). • Cleavage facets form in body-cen- tered cubic (BCC) and hexagonal close-packed (HCP) metals when the crack path follows a well-defined transgranular crystallographic plane Fig. 11 — Fatigue striations emanate from the Fig. 12 — SEM photomicrograph of the fa- (e.g., the {100} planes in BCC
Details
-
File Typepdf
-
Upload Time-
-
Content LanguagesEnglish
-
Upload UserAnonymous/Not logged-in
-
File Pages4 Page
-
File Size-