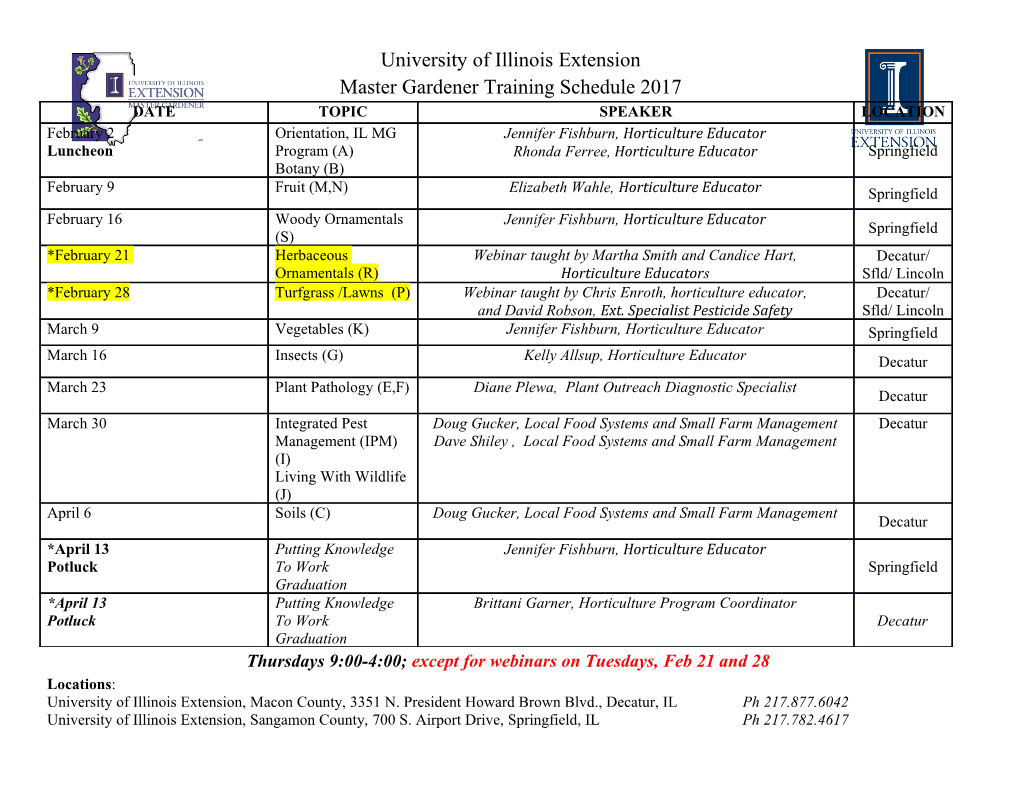
DFX GUIDELINES Copyright Notice This document contains proprietary information of .No part of this document may be reproduced, stored, copied, or transmitted in any form or by means of electronic, mechanical, photocopying or otherwise, without the express consent of. This document is intended for internal circulation only and not meant for external distribution. O_GD0322_10 DFX GUIDELINES Glossary Abbreviation Description ADHESIVE (SMT) A substance such as glue or cement used to fasten objects together. In surface mounting, an epoxy adhesive is used to adhere SMD’s to the substrate. AQUEOUS WASH De-ionized water wash process used to remove contaminates and (SMT and PTH) flux residue from the PCB. Teradyne uses an aqueous cleaning system. AUTO PLACE (SMT) The act or operation of assembling discrete components to printed boards by means of electronically controlled equipment. CABLE ASSEMBLY Manual process to route, solder and tie down coax or other cable assemblies. COMPONENT Component insertion equipment installs the leads of a PTH INSERTION (PTH) component Into the PCB, cuts each lead to the proper length and then clinches some or all of the leads against the Surface of the PCB. Current capability includes axial insertion, DIP insertion, SIP insertion and socket Insertion. CURE A chemical reaction that changes the physical properties of a substance, e.g., an adhesive. DPMO Defects per million opportunities is the number of defects divided by the number of opportunities multiplied by one million. DISPENSING (SMT) Process to dispense adhesive material used to secure large parts on the bottom side of PCB. Solder paste is also dispensed on land pads for BGA rework. ECO ASSEMBLY Manual process to incorporate jumper wires and other add-on components required by engineering change documentation. LEAD FORM (PTH) Preconditioning leaded components by forming and/or trimming leads prior to insertion. MANUAL SOLDER Manual process. Soldering using a solder iron or other hand-held, (PTH) operator controlled apparatus. MECHANICAL Manual installation of mechanical components such as Ejectors, ASSEMBLY Heat sink Plates, air baffles etc. Page 2 of 95 O_GD0322_10 DFX GUIDELINES Abbreviation Description PRESS-FIT Manual process to press-fit an electrical contact into a hole in a printed board with or without Plated thru holes. PRINTING (SMT) Process to apply a material (solder paste or thermally conductive epoxy) by forcing it thru a stainless steel stencil. Two methods are employed in printing: automated (solder paste printing for PCBs) and manual (thermally conductive epoxy for heat sink applications). REFLOW SOLDERING The joining of surfaces that have been tinned and have solder (SMT) between them, placing them together, heating them until solder flows, and allowing the surfaces and the solder to cool in the joined surfaces. REWORK (PTH and The act of reprocessing non-complying articles, thru the use of SMT) original or alternate equivalent processing, in a manner that assures compliance of the article with applicable drawings or specifications. SOCKET ASSEMBLY Manual process to hand load socketed components such as relays into pre-installed sockets. SOLDER PASTE Solder paste is a homogeneous mixture of metal spheres and flux APPLICATION (SMT) that promotes wetting. Two automated methods are used to apply solder paste to the PCB surface: printing or dispensing. Printing, which has the fastest cycle time and best process capability, is the preferred process. SURFACE PREP Manual process where the bonding surfaces are abraded prior to applying epoxy. WAVE SOLDERING A process wherein an assembled printed board is brought in contact (PTH) with the surface of a continuously flowing and circulating mass of solder ALIGNMENT HOLES Unplated holes used to position component alignment fixtures during assembly and soldering. BREAKOFF BORDERS PCB material used to adapt PCB arrays to conform to PTH, In-Line or Carrier formats. BREAKOFF PCB material used to extend the dimensions of a PCB image or EXTENSIONS array to conform to PTH or In-Line formats. BREAK-OFF TABS Snap-off tabs between images in an array to permit depanelization after assembly. MULTI-IMAGE ARRAYS PCB images arranged in rows & columns to reduce costs or meet processing format requirements. Page 3 of 95 O_GD0322_10 DFX GUIDELINES Abbreviation Description PANELIZATION Method to reduce costs by using break off borders, extensions or by creating multi-image arrays. CARRIER FORMAT Processing format for Mixed Technology Boards that do not meet requirement of In-Line format. PCB IMAGE Refers to a single PCB which can be processed individually or as part of an array. PTH FORMAT Processing format for leaded technology boards that permits use of standard board holding plates. ROUTER TABS Webs of PCB material between images in an array which are cut or routed after assembly. SAW SCORING Grooves cut between images in an array to permit depanelization after assembly. SMT CARRIER Processing format for SMT or Mixed Technology Boards that do not FORMAT meet requirement of In-Line format. SMT IN-LINE FORMAT Processing format for Mixed Technology Boards that permits conveyorized board handling. TOOLING HOLES Un plated holes used for mechanical board alignment during assembly and test. Page 4 of 95 O_GD0322_10 DFX GUIDELINES Table of Contents 1 Introduction..................................................................................................................................8 2 Tooling Holes, Fiducials..............................................................................................................8 3 Layout considerations (SMT/THT)...............................................................................................9 4 PTH Calculations .......................................................................................................................11 5 Outline Drawing dimension and requirements.........................................................................12 6 Stackup construction ................................................................................................................12 7 Silkscreen guidelines ................................................................................................................13 8 SOLDERMASK REQUIREMENTS ..............................................................................................13 9 Solder Paste Requirements.......................................................................................................14 10 PCB Surface Finishes................................................................................................................14 11 Soldering Types and Layout Requirements .............................................................................16 11.1 Design Guideline for Reflow soldering...........................................................................16 11.2 Design Guideline for Intrusive Reflow............................................................................16 11.3 Design Guideline for Wave Soldering............................................................................17 11.4 Selective Wave Soldering Requirements.......................................................................18 12 Assembly Drawing Requirements:............................................................................................18 13 Panelization and De-Panelization..............................................................................................19 13.1 Panelization:.................................................................................................................19 13.2 Depanelization Methods:...............................................................................................20 14 Vias (Types, Preferred, Via Selection).......................................................................................22 15 Laminate Material Selection ......................................................................................................25 16 Pb-free Laminate Characteristics..............................................................................................26 16.1 Laminate Selection .......................................................................................................27 17 ROHS compliance......................................................................................................................28 17.1 Minimum RoHS Component Requirements...................................................................28 17.2 All PCB surface finishes must meet the following requirements .....................................29 18 Chip Components......................................................................................................................30 19 Design for Testability Guidelines..............................................................................................52 19.1 ICT (In circuit Test) Mechanical Guidelines ...................................................................52 19.1.1 Probe Spacing .....................................................................................................52 19.1.2 Probe Access.......................................................................................................52 19.1.3 Test Pad Density..................................................................................................53 19.1.4 Test Pad Requirement: ........................................................................................53 19.1.5
Details
-
File Typepdf
-
Upload Time-
-
Content LanguagesEnglish
-
Upload UserAnonymous/Not logged-in
-
File Pages95 Page
-
File Size-