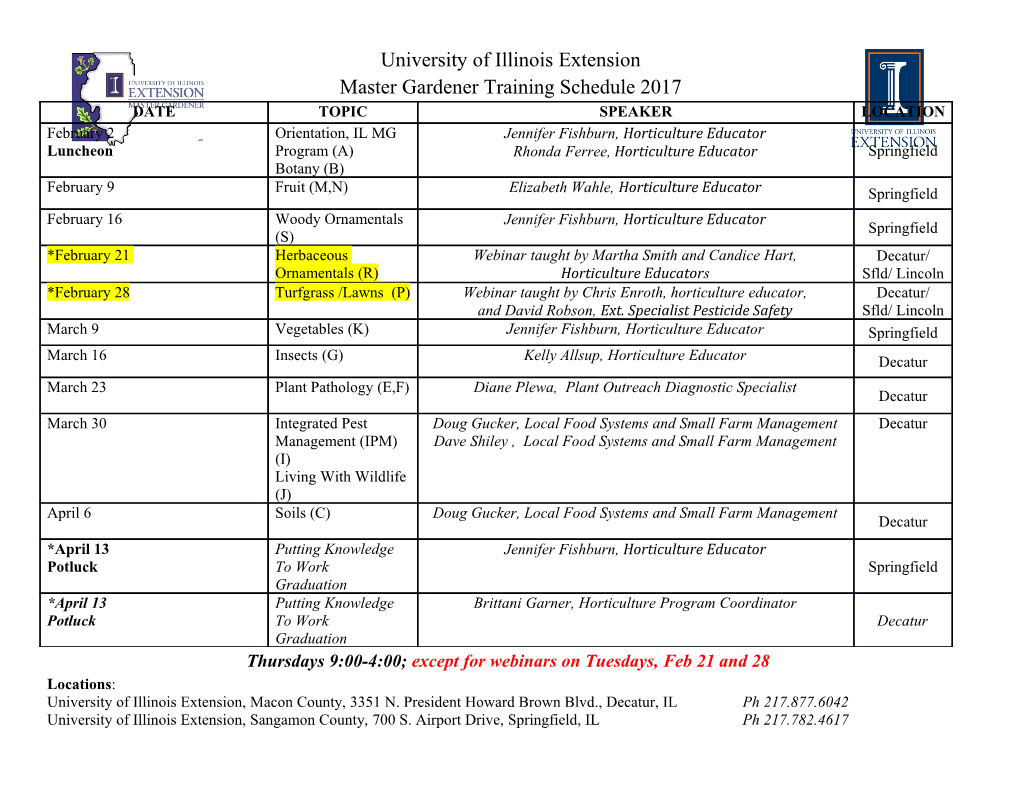
Tennis Boundary Ball Detection ECE 445 Fall 2016 Design Review Team 12 TA: Zipeng Wang David Chen (dchen44) David Joe (dkjoe2) Table of Contents 1.0 Introduction 2 2.0 Design 2.1 Block Diagram 3 2.2 Block Description 2.2.1 Text Description 4-5 2.2.2 Circuit Description 6-10 2.3 Flow Chart (Processing/Software) 11 2.4 Energy Calculation 12 3.0 Requirement and Verification 13-15 4.0 Tolerance Analysis 16-17 5.0 Safety and Ethics 18-19 6.0 Costs and Schedule 6.1 Parts Costs 19 6.2 Labor Costs 19 6.3 Total Costs 19 6.4 Schedule 20-21 7.0 Citations 22 1 1.0 Introduction In professional tennis there are two main systems used to electronically judge if a ball is in or out, these are mainly used when a player challenges the call of the referee. For the service line, the boundary for serves, uses a system called “Cyclops” which normally uses five or six infrared beams about 10mm off the ground and upon breaking the line determines if the serve was in or out. The “Hawkeye” uses six or seven high-performance cameras that are placed around the stadium all from various angles, and it keeps track of the ball and uses triangulation to make a three-dimensional representation of the ball. Neither system is flawlessly accurate but is accurate enough to be qualified as an electronic line judge [1]. The problem this project tackles is the lack of an electronic line judge for any level of tennis that isn’t professional. Most college, recreational, high school, and others rely solely on human judgement to determine if a ball is in or out. A ball is considered in if the ball lands on the line by any amount, and when the ball lands on the outer edge of the boundary line with variables like velocity of the ball can be sometimes difficult to determine if a ball was indeed out or in. Sports have advanced in technology over the years and limiting it to only certain sports or levels of play doesn’t need to be a hinderance to the technology of sports. Similar to the “Cyclops” this project will use infrared beams to detect if a “close-call” ball is in. One device will be placed on one end of the boundary line and another device on the opposite side. The infrared beam will be emitted from one device and collected at the other, and upon a break judged to be a ball (and not for example a foot) the device will indicate to the user through LEDs that the ball was in, otherwise the ball was out (no indication). 2 2.0 Design 2.1 Block Diagram 3 2.2 Block Description 2.2.1 Text Description Laser Alignment System For both the IR Emitter and IR Collector modules there will be a line laser, 5mW 650nm red, that will be in line with the IR beam and collector respectively and angled towards the ground. Will be simply controlled by a switch that turns on and off the line laser and powered by the power supply. The line laser operates on 2.8-5.2V and can be achieved with a step-down voltage regulator. User can use it to line the device up with the boundary line by matching the line laser to the line, and it also helps line the emitter device with the collector device. LED Indicator The LED Indicator is on the IR Collector device. It will be controlled by the microcontroller and powered by the power supply. The module consists of four red LEDs that will be bunched together, this is so that the user can easily see the color while on the court. The microcontroller will turn on the LEDs when it is determined that the most recent ball that landed is in, if it is out it will remain off. The LEDs will remain on for 10 seconds to give user time to check. Optical System : IR Emitter / IR Collector The Infrared Emitter and Receiver are manufactured modules from Tri-Tronics. These Mini-Eye MLSIC and MRC modules satisfy our range constraint of 20 meters, and use pulse modulation to prevent noise from interfering with the detection system. Both modules run at 24V and sink up to 30mA regardless of the load. The output of the receiver provides the data corresponding to a broken or unbroken beam, and therefore the data necessary to determine the presence of a tennis ball breaking the beam. Microcontroller The microcontroller module consists of the ATmega328p which is the center of both devices. It is used because of the clock speed is fast enough for our calculations (standard 16MHz but can go to 20Mhz), and meets the general needs of the devices. The microcontroller for the IR Emitter main function is to control the emitter. The microcontroller for the IR Collector is to process the data coming from the IR Emitter, the infrared beam and its presence, and from that determine whether the ball is in. If the ball is in the microcontroller then communicates with the LED Indicator to turn on (flow chart of software can be seen in the Flow Chart section). The IR Collector 4 microcontroller is where most of the testing will be done as it outputs the data for the optical system. Power Supply The power supply consists of a 12V 1.2Ah lead-acid battery. The lead-acid chemistry is used because of the ease of recharging without complication charging algorithms, which is crucial to our project. In addition, lead-acid is less dangerous and less prone to explosions than other chemistries, such as Lithium-Ion. We use a 12V source as an intermediary between the 24V and 5V required in our circuits, and step up and step down the voltages using voltage regulators. The amp-hourage of 1.2Ah is chosen according to the necessary power constraints of running our entire system for 3 continuous hours, as described later in this report. Solar Charging Circuit The Power Supply is charged using a solar charging circuit. Power is sourced from four 4V 50mA solar panels for each device linked in series to give the solar panels collectively 16V and 50mA of current. This voltage and current is then input to a regulating circuit that contains a LM317 voltage regulator. The 16V signal is regulated to a 14.4V signal, which allows the 12V lead acid battery to charge even when it is at capacity. This 2.4V margin facilitates charging and prevents sulfation of the battery. Additional circuitry reduces noise and prevents the battery from reaching a voltage higher than the solar panels and creating a short circuit that may potentially damage the solar panels or battery. 5 2.2.2 Circuit Description IR Emitter Device The IR Emitter Device consists of the necessary solar panels, battery, solar charging circuitry, and voltage regulators to power the Emitter and the Alignment Line Laser. Interconnections of this system are shown in the figure below. Figure 4: IR Emitter Device 6 IR Collector Device The IR Collector Device consists of the necessary solar panels, battery, solar charging circuitry, and voltage regulators to power the Receiver, ATmega 328P microcontroller, and the Indicator LEDs. Data from the receiver is analyzed by the microcontroller, and a valid beam break by a tennis ball is indicated by powering on the LEDs for a duration of time. Figure 5: IR Collector Device 7 Microcontroller The microcontroller is an ATmega328P. It receives various voltage inputs and ground, and also receives an input signal from the receiver that ranges from 0V to 24V, going into an analog I/O pin. The output comes from a digital I/O pin and goes to the LEDs that indicate whether a tennis ball is in or out. Internal computation will determine whether the input signal from the receiver represents a tennis ball or not. Figure 6: ATmega328P 8 12V to 24V Step-Up (Boost) Switching Regulator This voltage regulator circuit steps up the 12V battery voltage to a 24V signal usable by the emitter and receiver modules. [6] Figure 7: 12V to 24V Step-Up (Boost) Switching Regulator 9 Solar Charging Circuit This circuit takes the input from the solar panels, a 16V 50mA signal, and regulates it to 14.4V, which is the optimal charging voltage for the 12V lead-acid battery. The voltage regulating circuit is based on the LM317 voltage regulator. The actual output voltage may be adjusted using the potentiometer R3. [7] Figure 8: Solar Charging Circuit 10 2.3 Flow Chart (Processing/Software) Figure 9: Flow Chart of how system determines ball is in *ball threshold is the time range that beam should be broken for it to be a tennis ball. This is determined mainly from testing various types of ball bounces on system. More quantitative theoretical calculations in Tolerance Analysis section. 11 2.4 Energy Calculations Emitter Circuit Emitter Module: V = 24V I = 30mA P = 24V * 30mA = 0.72W Time = 3h Energy = P * Time = 2.16 Wh Alignment Laser: V = 5V I = 25mA P = 5V * 25mA = 0.125W Time = 3h Energy = P * Time = .006 Wh Emitter Circuit Energy = 2.166 Wh Receiver Circuit Receiver Module: V = 24V I = 30mA P = 24V * 30mA = 0.72W Time = 3h Energy = P * Time = 2.16 Wh Atmega 328P: V = 5V I = 20mA P = 5V * 20mA = 0.1W Time = 3h Energy = P * Time = 0.3 Wh Receiver Circuit Energy = 2.46 Wh Total Circuit Energy = Emitter Circuit Energy + Receiver Circuit Energy = 4.626 Wh Individual Power Systems: V = 12V Amp Hourage = 1.2Ah Total Energy = Emitter Circuit Energy + Receiver Circuit Energy = 14.4 Wh We find that the individual power systems each generate an ideal total energy of 14.4 Wh, which is more than sufficient for the respective energy needs of the emitter and receiver circuits.
Details
-
File Typepdf
-
Upload Time-
-
Content LanguagesEnglish
-
Upload UserAnonymous/Not logged-in
-
File Pages23 Page
-
File Size-