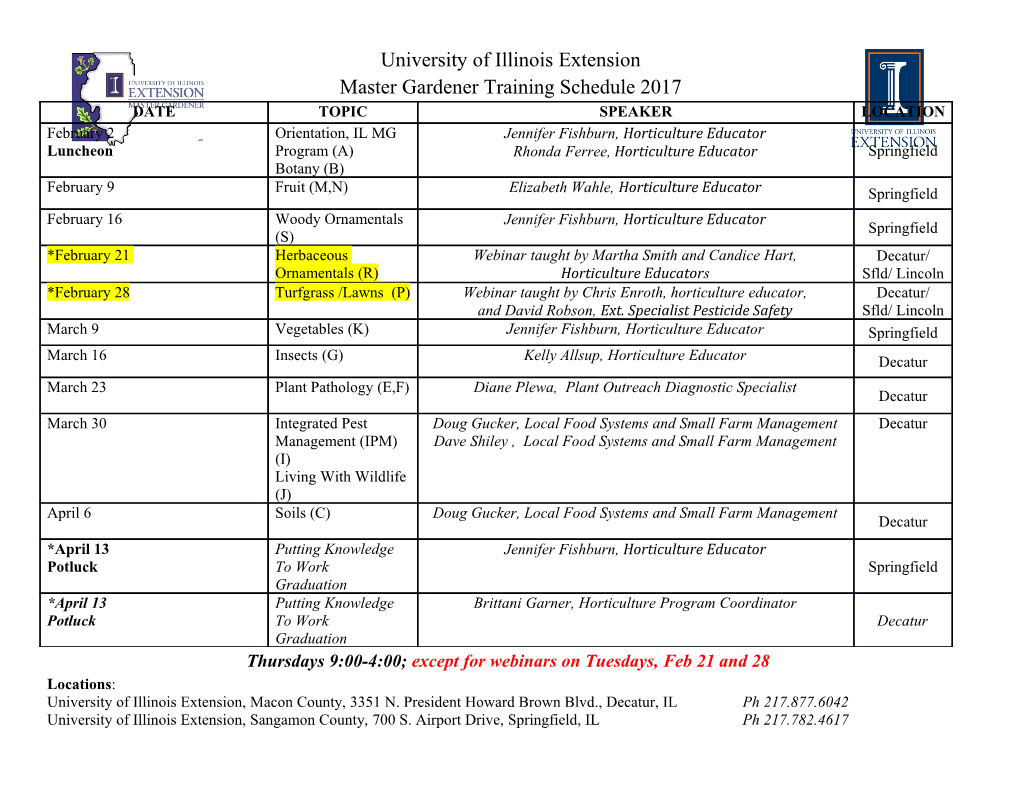
§ 230.62 49 CFR Ch. II (10–1–02 Edition) or repaired. (See appendix B of this § 230.67 Responsibility for inspection part.) and repairs. The steam locomotive owner and/or STEAM PIPES operator shall inspect and repair all steam locomotives and tenders under § 230.62 Dry pipe. their control. All defects disclosed by Dry pipes subject to pressure shall be any inspection shall be repaired in ac- examined at each annual inspection to cordance with accepted industry stand- measure wall thickness. Dry pipes with ards, which may include established wall thickness reduced below that re- railroad practices, before the steam lo- quired to render the pipe suitable for comotive or tender is returned to serv- the service intended at the MAWP ice. The steam locomotive owner and/ must be replaced or repaired. or operator shall not return the steam locomotive or tender to service unless § 230.63 Smoke box, steam pipes and they are in good condition and safe and pressure parts. suitable for service. The smoke box, steam pipes and pres- sure parts shall be inspected at each SPEED INDICATORS annual inspection, or any other time § 230.68 Speed indicators. that conditions warrant. The indi- vidual conducting the inspection must Steam locomotives that operate at enter the smoke box to conduct the in- speeds in excess of 20 miles per hour spection, looking for signs of leaks over the general system of railroad from any of the pressure parts therein transportation shall be equipped with speed indicators. Where equipped, and examining all draft appliances. speed indicators shall be maintained to STEAM LEAKS ensure accurate functioning. ASH PANS § 230.64 Leaks under lagging. The steam locomotive owner and/or § 230.69 Ash pans. operator shall take out of service at Ash pans shall be securely supported once any boiler that has developed a from mud-rings or frames with no part leak under the lagging due to a crack less than 21⁄2 inches above the rail. in the shell, or to any other condition Their operating mechanism shall be so which may reduce safety. Pursuant to arranged that they may be safely oper- § 230.29, the boiler must be repaired be- ated and securely closed. fore being returned to service. BRAKE AND SIGNAL EQUIPMENT § 230.65 Steam blocking view of engine crew. § 230.70 Safe condition. The steam locomotive owner and/or (a) Pre-departure inspection. At the be- operator shall keep the boiler, and its ginning of each day the locomotive is piping and appurtenances, in such re- used, the steam locomotive operator pair that they do not emit steam in a shall ensure that: manner that obscures the engine crew’s (1) The brakes on the steam loco- vision. motive and tender are in safe and suit- able condition for service; (2) The air compressor or compres- Subpart C—Steam Locomotives sors are in condition to provide an and Tenders ample supply of air for the locomotive service intended; § 230.66 Design, construction, and (3) The devices for regulating all maintenance. pressures are properly performing their The steam locomotive owner and op- functions; erator are responsible for the general (4) The brake valves work properly in design, construction and maintenance all positions; and of the steam locomotives and tenders (5) The water has been drained from under their control. the air-brake system. 334 VerDate 0ct<31>2002 08:18 Nov 29, 2002 Jkt 197203 PO 00000 Frm 00334 Fmt 8010 Sfmt 8010 Y:\SGML\197203T.XXX 197203T Federal Railroad Administration, DOT § 230.72 (b) Brake pipe valve required. Each § 230.71 Orifice testing of compressors. steam locomotive shall have a brake (a) Frequency of testing. The com- pipe valve attached to the front of the pressor or compressors shall be tested tender, the rear of the back cab wall, for capacity by orifice test as often as or adjacent to the exit of a vestibuled conditions may require, but not less cab. The words ‘‘Emergency Brake frequently than once every 92 service Valve’’ shall be clearly displayed near days. the valve. (b) Orifice testing criteria. (1) Compres- sors in common use, as listed in the following table, shall have orifice test criteria as follows: Diameter of Air pressure Make Compressor size Single strokes orifice maintained per minute (in inches) (in pounds) Westinghouse ........................................................ 91⁄2 ................................ 120 11⁄64 60 Westinghouse ........................................................ 11 .................................. 100 3⁄16 60 Westinghouse ........................................................ 150 CFM 81⁄2 CC .......... 100 9⁄32 60 Westinghouse ........................................................ 120 CFM 81⁄2 ................ 100 15⁄64 60 New York ............................................................... 2a .................................. 120 5⁄32 60 New York ............................................................... 6a .................................. 100 13⁄64 60 New York ............................................................... 5b .................................. 100 15⁄64 60 Note: This table shall be used for altitudes to and including 1,000 feet. For altitudes over 1,000 feet the speed of compressor may be increased 5 single strokes per minute for each 1,000 feet increase in altitude. (2) For compressors not listed in the D=(.6PR/(S¥.6P)) table in paragraph (b)(1) of this section, the air pressure to be maintained shall Where: be no less than 80 percent of the manu- D = Extreme depth of telltale holes in inches facturer’s rated capacity for the com- but in no case less than one-sixteenth inch; pressor. P = certified working pressure in psi; S = 1⁄5 of the minimum specified tensile § 230.72 Testing main reservoirs. strength of the material in psi; and R = inside radius of the reservoir in inches. (a) Hammer and hydrostatic testing. Except as described in paragraphs (b) (2) One row of holes shall be drilled through (d) of this section, every main lengthwise of the reservoir on a line reservoir, except those cast integrally intersecting the drain opening. When with the frame, shall be hammer and main reservoirs are drilled as described hydrostatically tested during each an- in paragraph (b)(1) of this section, the nual inspection. The reservoir shall be hydrostatic and hammer tests de- hammer tested while empty and with scribed in paragraph (a) of this section no pressure applied. If no defective are not required during the annual in- areas are detected, a hydrostatic test spection. Whenever any telltale hole of MAWP shall be applied. shall have penetrated the interior of any reservoir, the reservoir shall be (b) Drilling of main reservoirs. (1) Only permanently withdrawn from service. welded main reservoir originally con- structed to withstand at least five (c) Welded main reservoirs without lon- gitudinal lap seams. For welded main times the MAWP may be drilled over reservoirs that do not have longitu- its entire surface with telltale holes dinal lap seams, an appropriate NDE 3 that are ⁄16 of an inch in diameter. The method that can measure the wall holes shall be spaced not more than 12 thickness of the reservoir may be used inches apart, measured both longitu- instead of the hammer test and hydro- dinally and circumferentially, and static test required in paragraph (a) of drilled from the outer surface to an ex- this section. The spacing of the sam- treme depth determined by the fol- pling points for wall thickness shall lowing formula: not be greater than 12 inches longitu- dinally and circumferentially. The res- ervoir shall permanently be withdrawn 335 VerDate 0ct<31>2002 08:18 Nov 29, 2002 Jkt 197203 PO 00000 Frm 00335 Fmt 8010 Sfmt 8010 Y:\SGML\197203T.XXX 197203T § 230.73 49 CFR Ch. II (10–1–02 Edition) from service where the NDE testing re- or dead weight tester designed for this veals wall thickness less than the value purpose. determined by the following formula: § 230.74 Time of cleaning. T=(PR/(S¥.6P) All valves in the air brake system, including related dirt collectors and Where: filters, shall be cleaned and tested in t = Minimum value for wall thickness; accordance with accepted brake equip- P = Certified working pressure in psi; ment manufacturer’s specifications, or S = 1⁄5 of the minimum specified tensile as often as conditions require to main- strength of the material in psi, or 10,000 psi tain them in a safe and suitable condi- if the tensile strength is unknown; and tion for service, but not less frequently R = Inside radius of the reservoir in inches. than after 368 service days or during (d) Welded or riveted longitudinal lap the second annual inspection, which- seam main reservoirs. (1) For welded or ever occurs first. riveted longitudinal lap seam main res- ervoirs, an appropriate NDE method § 230.75 Stenciling dates of tests and that can measure wall thickness of the cleaning. reservoir shall be used instead of, or in The date of testing and cleaning and addition to, the hammer test and hy- the initials of the shop or station at drostatic test. The spacing of the sam- which the work is done, shall legibly be pling points for wall thickness shall stenciled in a conspicuous place on the not be greater than 12 inches longitu- tested parts or placed on a card dis- dinally and circumferentially. Par- played under a transparent cover in the ticular care shall be taken to measure cab of the steam locomotive. along the longitudinal seam on both plates at an interval of no more than 6 § 230.76 Piston travel. inches longitudinally. The reservoir (a) Minimum piston travel. The min- shall be withdrawn permanently from imum piston travel shall be sufficient service where NDE testing reveals wall to provide proper brake shoe clearance thickness less than the value deter- when the brakes are released. mined by the following formula: (b) Maximum piston travel. The max- imum piston travel when steam loco- T=(PR/(0.5S¥0.6P)) motive is standing shall be as follows: Maximum Where: Type of wheel brake piston travel t = Minimum value for wall thickness; (in inches) P = Certified working pressure in psi; Cam Type Driving Wheel Brake .......................
Details
-
File Typepdf
-
Upload Time-
-
Content LanguagesEnglish
-
Upload UserAnonymous/Not logged-in
-
File Pages13 Page
-
File Size-