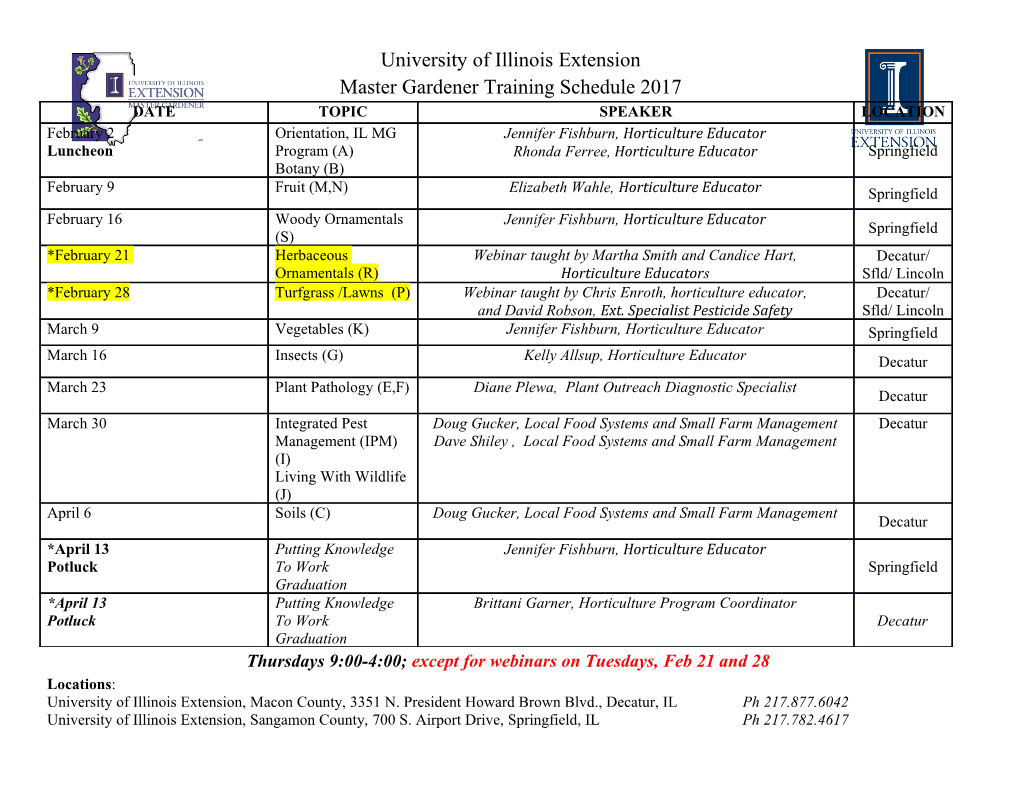
Eindhoven University of Technology MASTER A repairable spare parts management strategy for the Royal Netherlands Air Force Wisse, C. Award date: 2017 Link to publication Disclaimer This document contains a student thesis (bachelor's or master's), as authored by a student at Eindhoven University of Technology. Student theses are made available in the TU/e repository upon obtaining the required degree. The grade received is not published on the document as presented in the repository. The required complexity or quality of research of student theses may vary by program, and the required minimum study period may vary in duration. General rights Copyright and moral rights for the publications made accessible in the public portal are retained by the authors and/or other copyright owners and it is a condition of accessing publications that users recognise and abide by the legal requirements associated with these rights. • Users may download and print one copy of any publication from the public portal for the purpose of private study or research. • You may not further distribute the material or use it for any profit-making activity or commercial gain Hoogerheide, August 2017 A Repairable Spare Parts Management Strategy for the Royal Netherlands Air Force By C. Wisse BSc Industrial Engineering Student identity number 0808994 In partial fulfillment of the requirements for the degree of Master of Science In Operations Management and Logistics Supervisors : Dr. T. Tan, TU/e, OPAC Dr. Ir. J.J. Arts, TU/e, OPAC Prof. Dr. Ir. G.J.J.A.N. van Houtum, TU/e, OPAC Second Lieutenant Ing. L.W.F. Koops, Royal Netherlands Air Force TUE. Department of Industrial Engineering and Innovation Sciences Series Master Theses Operations Management and Logistics Subject headings: spare parts; static scheduling; dynamic scheduling; discrete event simulation; inventory control It should be noted that the numbers used in this report are fictitious and serve only for illustrative purposes due to confidentiality reasons. I ABSTRACT This research has been conducted in collaboration with the RNLAF. Stakeholders at the RNLAF indicate that orders at the component repair shop are currently scheduled inefficient, which causes longer lead times and thus higher inventory levels. The objective of this research is to identify scheduling rules and to study their effect in repairable inventory systems. Furthermore, we aim to optimize the base stock levels based on the optimal scheduling rule, i.e. we jointly optimize the base stock levels and the real-time scheduling decisions. Therefore, we modeled a M/M/1 queueing system that evaluates the aggregate mean number of backorders for a given base stock vector and scheduling rule. Then, for each constraint on the aggregate mean number of backorders, optimized base stock levels follow from Lagrangian relaxation and Newsvendor equations. We conclude that the optimal scheduling rule over all cases has the following main characteristics: - Takes into account the stochasticity of the arrival process. - Takes into account the average processing time of a SKU. - Takes into account the real-time stock levels of SKU’s. We show that the Myopic Allocation rule meets all these characteristics and outperforms the other scheduling rules in almost all cases. II EXECUTIVE SUMMARY This document contains the results of a master thesis project carried out at the Royal Netherlands Air Force. Most assets used by the RNLAF are expensive and consist of technologically advanced systems. A high availability of these assets is desired, since the assets are used to protect the country and during military missions. Since the development of these assets is very costly and time consuming, repairing an asset is preferred instead of purchasing an entire new one. To achieve a high availability of the assets, orders are placed at 981 SQN, which is the component repair shop of the RNLAF. The lead time of a component is highly dependent of the route through the repair shop, the capacity of operators, machines, test equipment and the availability of lower level SRU’s. Therefore, to optimize the lead time of a component, the capacity of the repair shop needs to be used optimally and the repair process needs to be controlled as good as possible. The repairable spare part inventory and scheduling methodology that is currently used at the RNLAF is mainly based on the experiences of employees instead of on specified control rules. According to stakeholders, orders are currently scheduled inefficient due to this method. Therefore, the objective of this research is to identify scheduling rules and to study their effect in repairable inventory systems. Furthermore, we aim to optimize the base stock levels based on the optimal scheduling rule, i.e. we jointly optimize the base stock levels and the real-time scheduling decisions. We design a conceptual integrated model which aims to minimize investment costs subject to a constraint on the aggregate mean number of backorders. This thesis contributes both to science and to industry. Despite the fact that Adan et al. (2009), Tiemessen and van Houtum (2010), and Tiemessen and van Houtum (2013) suggest that research needs to be done to jointly optimize dynamic priority rules and base stock levels, it has not been investigated yet. Besides, the already existing method of jointly optimizing static priority rules and base stock levels is extended the possibility of having different processing times for each SKU. Finally, we design scheduling rules especially for repair shops with high material and capacity uncertainty, which are evaluated in our model. This thesis also contributes to industry, since highly expensive spare parts and high material and capacity complexity are common in the aviation industry. Therefore, the contributions of this research also apply for other parties in this industry. MODEL FORMULATION We consider a M/M/1 queueing system with a stock point that keeps multiple repairable spare parts on stock to serve a set of technical systems in a certain region. The stock point keeps repairable SKU’s and we have repair by replacement. To formulate the model, we made the following assumptions: - All parts are critical - For each SKU, the number of part failures in the installed base occurs according to a Poisson process with a constant rate - We model the repair facility as a single exponential server - Processing times of all SKU’s are exponentially distributed and mutually independent - Priorities are preemptive III The objective of the model is to minimize the total investment in spare parts subject to a constraint on the aggregate mean number of backorders. To solve this non-linear integer programming problem, we evaluate the aggregate mean number of backorders for a given base stock vector and scheduling rule. For static scheduling rules, we build an analytic model to evaluate the aggregate mean number of backorders. We use the exact method of Sleptchenko et al. (2015) to find the steady state joint queue length distribution under a given assignment of SKU’s to unique priority classes. Then, optimized base stock levels for each backorder constraint follow from Lagrangian functions and Newsvendor equations. For dynamic rules we build a simulation model to evaluate the aggregate mean number of backorders, due to the high computational complexity of applying an analytical model. The simulation model is used to find the average distribution of the joint queue length under a specific dynamic scheduling rule and specific base stock levels. Then, through an iterative process, optimized base stock levels for each backorder constraint follow from this distribution, Lagrangian relaxation and Newsvendor equations. SCHEDULING RULES We evaluate three static scheduling rules. The first heuristic schedules the SKU with the highest costs first (Heuristic 1). Heuristic 2 schedules the order with shortest processing times first. Finally, Heuristic 3 schedules the SKU with the highest product of costs and processing rate first. Furthermore, we tested six dynamic scheduling rules, starting with two rules that performed best in literature (Tiemessen and van Houtum, 2013). One that aims to maximize the expected backorder reduction (the MA-Rule) and one that aims to equalize the time until the next backorder (the MERT- Rule). Since the repair shop of the RNLAF differs from the repair shops discussed in these studies, we choose to test a four scheduling rules that are designed especially for the repair shop of the RNLAF. The first rule is comes closest to the currently used methodology of the RNLAF and is added to serve as a base line. This rule consist of three priority classes, with in the first class SKU’s with an active backorder, in the second class SKU’s with a net stock level of zero and in the third class SKU’s with a positive inventory level (the CPS-Rule). Ties are broken FCFS. The second rule breaks ties in the priority classes as in the CPS-Rule based on prices of the SKU’s (the MPS1-Rule) and the third rule breaks ties based on the deviation from the base stock level (the MPS2-Rule). Finally, the MA-Rule is adapted to take into account the prices of a spare part (the MMA-Rule). CASE STUDY To model the repair shop at the RNLAF as a repair shop with a single location with one workstation and one stock point, the repair shop at the RNLAF is simulated. This simulation is used to decide on the processing times of an order through the repair shop, which are used as input of both M/M/1 models. This case study shows that the costs of inventory can be reduced with at least 54,8% by only taking into account the prices of SKU’s and real-time inventory levels (the CPS-Rule) and with at least 54,6% by taking into account the stochasticity of the arrival rates, the processing rates and the real-time inventory levels (the MA-Rule).
Details
-
File Typepdf
-
Upload Time-
-
Content LanguagesEnglish
-
Upload UserAnonymous/Not logged-in
-
File Pages78 Page
-
File Size-