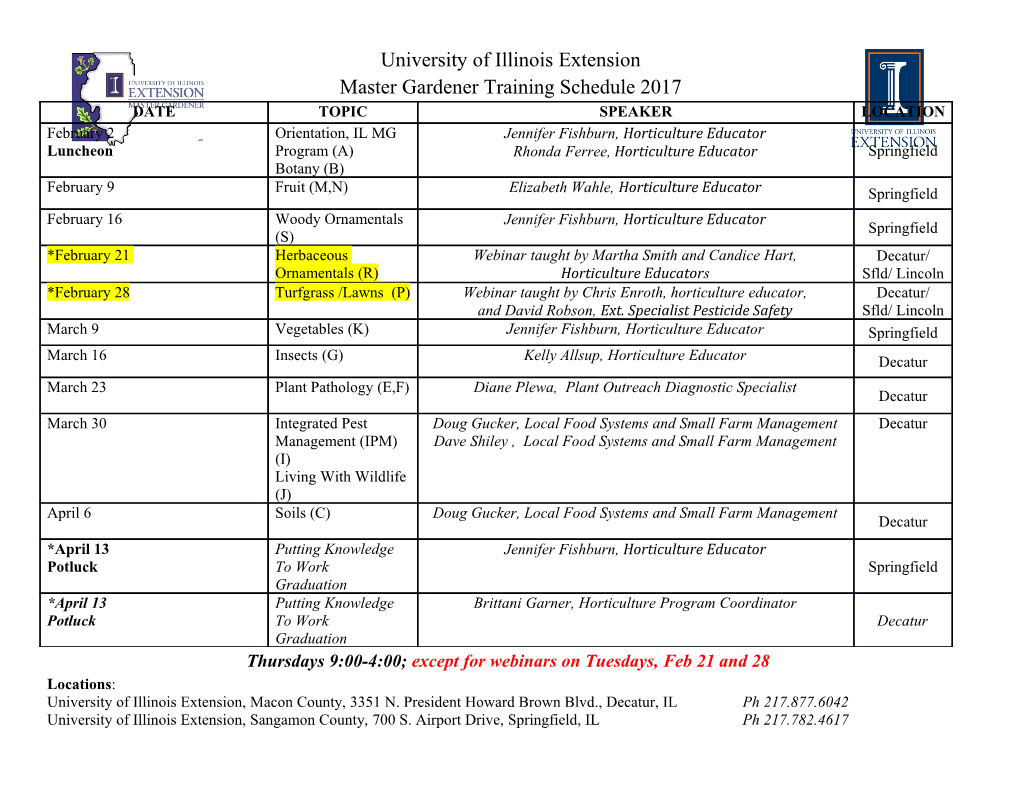
United States Patent (19) 11) Patent Number: 4,809,412 Nelson 45) Date of Patent: Mar. 7, 1989 54 APPARATUS FOR PRODUCING A 3,433,007 3/1969 Myers . NOVELTY NUB YARN 3,653,196 4/1972 Pike ................................... 57/350X 3,795,367 3/1974 Mocarski. (75) Inventor: Thomas L. Nelson, Georgetown, Del. 3,852,857 12/1974 Etbridge et al. ...................... 28/255 73 4,119,253 10/1978 Benson .............. ... 28/252 X Assignee: E. I. Du Pont de Nemours and 4,212,152 7/1980 Roman ...... ... 28/271 X Company, Wilmington, Del. 4,453,297 6/1984 London, Jr. et al. ............ 28/258 X 21) Appl. No.: 46,090 FOREIGN PATENT DOCUMENTS Filed: May 5, 1987 22) 45-14580 5/1970 Japan ..................................... 28/271 48-25387 7/1973 Japan ..................................... 28/258 Related U.S. Application Data 51-60749 5/1976 Japan .................................. 28/271 (62) Division of Ser. No. 804,408, Dec. 4, 1985, Pat. No. 51-75156 6/1976 Japan. ... 28/271 4,697,317. 60-17135 1/1985 Japan. ... 28/271 60-17134 1/1985 Japan ..................................... 28/271 51 Int. Cl." ........................... D02G 1/16; D02J 1/06 (52) U.S. C. ........................................ 28/271; 28/258; Primary Examiner-Robert R. Mackey 57/209; 57/350 57 ABSTRACT (58) Field of Search ......................... 28/252,258, 271; A substantially twist-free, crimped, continuous, multifil 57/209,350 ament yarn containing randomly-spaced, tightly entan (56) References Cited gled nubs and the process and apparatus used for mak ing such yarns is disclosed. The nub yarn is made by U.S. PATENT DOCUMENTS feeding a substantially entanglement-free, multifila 1,997,771 4/1935 McGowan . ment, crimped, continuous yarn through a forwarding 2,052,869 9/1936 Coanda . 2,278,879 4/1942 Hunter. jet, through an aspirating entanglement jet where nubs 2,878,548 3/1959 Lohr et al. are formed and passing the yarn through a loop guide. 3,042,482 7/1962 Woodell . The nubs of the yarn are less than one inch in length and 3,047,208 7/1962 Coanda . the yarn is useful in textile and carpet end uses. 3,093,878 6/1963 Fieldman . 3,402,446 9/1968 Benson .................................. 28/273 6 Claims, 4 Drawing Sheets S N 42 3 NN N 52 U.S. Patent Mar. 7, 1989 Sheet 1 of 4 4,809,412 7 / O WND Er O U.S. Patent Mar. 7, 1989 Sheet 2 of 4 4,809,412 U.S. Patent Mar. 7, 1989 Sheet 3 of 4 4,809,412 4,809,412 1. 2 rently with said flow of air out of the entrance of a APPARATUS FOR PRODUCING ANOVELTY NUB separate entanglement jet. The forwarding jet feeds the YARN yarn along with a stream of fluid, e.g., air, through a feed tube into an entanglement jet to form nubs. Passing This is a division of application Ser. No. 804,408 filed 5 the yarn through highly turbulent gas within the entan Dec. 4, 1985 now U.S. Pat. No. 4,697,317 granted Oct. glement jet, entangles the yarn, forming nubs. The legs 6. 1987. of the loop are maintained at a close spacing to each other by a loop guide, located near the forwarding jet DESCRIPTION exit, such guide together with controlled overfeed act 1. Technical Field 10 ing to prevent the formation of large slubs during the This invention relates generally to novelty yarns, preferred formation of nubs. more particularly, substantially twist free, crimped, The nub yarn so produced is characterized by a de continuous, multifilament yarn containing randomly nier per filament of 5-10, a total denier of 500-5000, and spaced, tightly entangled nubs and the process and ap is interlaced to increase yarn coherence and then used paratus used for making such yarns. 15 as a single yarn or combined in the interlace step with 2. Background additional yarns, with or without nubs for textile or The production of novelty yarns has long been a carpet end use. major objective in the textile and carpet industry. These yarns are commercially valuable as they provide unique BRIEF DESCRIPTION OF THE DRAWINGS and desirable aesthetics to their end use articles. One 20 FIG. 1 shows one preferred embodiment of the pro such novelty yarn, nub yarn, refers to a yarn containing cess of this invention wherein a nub yarn is produced. small lumps, knots or specks which have been intro FIG. 2 shows a side-by-side arrangement of two for duced into the main yarn. Nub yarns are sometimes warding and embodiment jet assemblies with a detailed referred to as slub yarns, however nubs are generally view of the loop guides useful in practicing the inven shorter and more compact and thus have a larger diam 25 tion. eter to length ratio than do slubs. FIG. 3 is a detailed view of the nub entanglement jet, The presence of larger slubs is undesirable for certain the feed jet tube and the loop guide. end uses where the aesthetics are more dependent on a FIG. 4 shows an additional embodiment of the cur low variability in slub size as well as an absence of large rent proposal, whereby a nub yarm is combined with a slubs. 30 yarn without nubs in a continuous process. Carpet containing small nubs is generally made from staple and the nubs are not tightly adhered to the core DETAILED DESCRIPTION OF THE fiber. This type of carpet can be used only in low traffic DRAWINGS areas, since the nubs are held in place only by the fric In FIG. 1 a crimped and interlaced supply yarn (10) tion restraint of the twist. In a high traffic area, these 35 is forwarded from a supply package over a yarn wetti carpets would quickly lose their nubs and the corre ing device (12) by the first forwarding means (shown sponding desirable aesthetic appearance. are rolls (14) where (14a) is the driven roll and (14b) is SUMMARY OF THE INVENTION an idler roll) and then through deinterlacing pins (16), such as those described in U.S. Pat. No. 4,059,873, to Apparatus and a process have been developed to add remove interlace from the crimped supply yarn. Ten randomly-spaced nubs numbering between 1 and 200 sion through the pins is maintained by controlling the per 10 meters of yarn which are consistently less than 1' differential speeds of the first forwarding means (14) in length, preferably less than 'in length, to a crimped, and the second forwarding means (shown are rolls (18) continuous, twist-free, multifilament yarn, thereby pro where (18a) is the driven roll and (18b) is an idler roll). ducing a novelty nub yarn for use by itself or in combi 45 The yarn is then forwarded by and through a third nation with additional yarns of the same or different forwarding means, the forwarding jet (20), passing dyeabilities. through the exit (23) of the forwarding jet and into the The apparatus of this invention comprises a forward nub-forming entanglement jet (24). The nub yarn (26) ing jet for forwarding feed yarn along a path, as aspirat then passes through a loop guide (28) as it is pulled from ing nub-forming entanglement jet, having a tube pas 50 the entanglement jet (24) by a fourth forwarding means sage diverging from the inlet to the outlet, a housing (shown are rolls (30) where (30a) is the driven roll and having a chamber in communication with the inlet end (30b) is an idler roll). The nub yarn is then routed of the jet tube, an opening in the housing in line with through an interlace jet (32), such as that described in and in communication with the inlet and of the jet tube U.S. Pat. No. 4,505,013, to add cohesion to the yarn, and a means to supply gas to the chamber, positioned in 55 and then collected by a suitable means, such as a winder line with said path to receive the yarn from the for (not shown). warding jet concurrently with said path into the inlet In the above process, the distance (34) (shown in end of the entanglement jet tube and separated from the FIG. 3) of the exit (23) of the forwarding jet from the forwarding jet by a small interval and a means for guid entrance of the entanglement jet tube inlet (51) (shown ing the yarn positioned adjacent to the exit of the for 60 in FIG. 3), air pressure and flow in both of these jets, warding jet to receive the yarn countercurrently with and the wall thickness between the forwarding jet and said path out of the inlet end of the entanglement jet the loop guide (40) are, in part, all important for effi tube. cient operation. It is also important that the overfeed of The new process comprises a controlled overfeeding the yarn into the entanglement jet (24) be maintained at of a substantially entanglement-free, multifilament 65 a level which allows for only the arch portion of the crimped continuous yarn through a forwarding jet hav yarn loop to actually enter the body of the jet. This ing a flow of air therethrough and then, as a loop, con overfeed can vary depending on the speed of the yarn currently with said flow of air into and countercur between about 5% and 40% and is controlled by main 4,809,412 3 4. taining a constant speed ratio between the forwarding manifold housing and follows the surface of both the means (18 and 30) located before and after the forward external lip (55) and internal curved surface (56) of the ing and entanglement jets.
Details
-
File Typepdf
-
Upload Time-
-
Content LanguagesEnglish
-
Upload UserAnonymous/Not logged-in
-
File Pages8 Page
-
File Size-