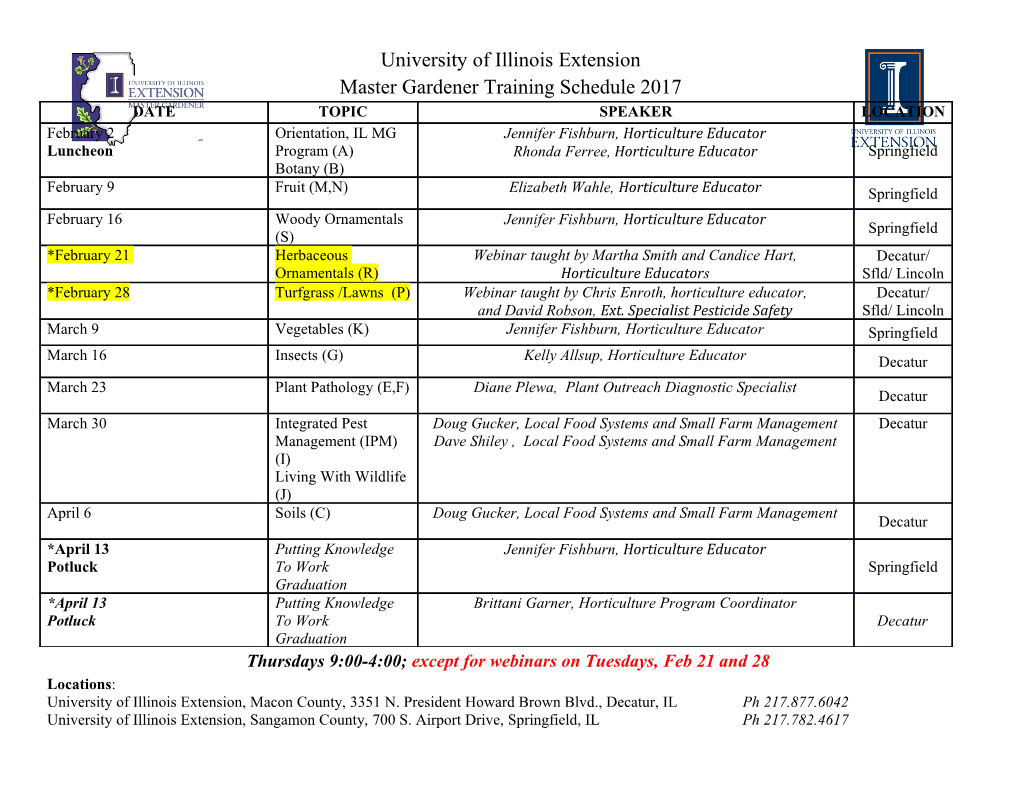
Theories of Failure • Failure: Every material has certain strength, expressed in terms of stress or strain, beyond which it fractures or fails to carry the load. • Failure Criterion: A criterion (standard/principle/measure/gauge/norm) is used to hypothesize (imagine/assume/theory/visualize) the failure. • Failure Theory: A Theory behind a failure criterion. Why we need failure theories? • To design structural components/elements and calculate margin of safety. • To guide in materials development. • To determine weak and strong directions. Failure Mode • Yielding: a process of global permanent plastic deformation. Change in the geometry of the object. • Low stiffness: excessive elastic deflection. • Fracture: a process in which cracks grow to the extent that the component breaks apart. • Buckling: the loss of stable equilibrium. Compressive loading can lead to bucking in columns. • Creep: a high-temperature effect. Load carrying capacity drops. Theories OF Failure 1 Four important failure theories, namely (1) maximum shear stress theory, (2) maximum normal stress theory, (3) maximum strain energy theory, and (4) maximum distortion energy theory. Out of these four theories of failure, the maximum normal stress theory or Rankins’s theory is only applicable for brittle materials, and the remaining three theories are applicable for ductile materials. Following are the important common features for all the theories. 1. In predicting failure, the limiting strength values obtained from the uniaxial testing are used. 2. The failure theories have been formulated in terms of three principal normal stresses (S1, S2, S3) at a point. 3. For any given complex state of stress (sx, sy, sz, txy, tyz, tzx), we can always find its equivalent principal normal stresses (S1, S2, S3). Thus the failure theories in terms of principal normal stresses can predict the failure due to any given state of stress. 4. The three principal normal stress components S1, S2, & S3, each which can be comprised of positive (tensile), negative (compressive) or zero value. 5. When the external loading is uniaxial, that is S1= a positive or negative real value, S2=S3=0, then all failure theories predict the same as that has been determined from regular tension/compression test. 6. The material properties are usually determined by simple tension or compression tests 7. Some structural members are subjected to biaxial or triaxial stresses. 8. To determine whether a component/element will fail or not, some failure theories are proposed which are related to the properties of materials obtained from uniaxial tension or compression tests. 9. Ductile materials usually fail by yielding and hence the limiting strength is the yield strength of material as determined from simple tension test which is assumed the same in compression also. For brittle materials limiting strength of material is ultimate tensile strength intension or compression. 2 Conservative ( traditional/old fashioned/ conventonal) 3 Problem solving strategy for Failure thoery: Syp- yield strength , Sut and Suc=ultimate tensile strength and ultimate compressive strengths Failure Theories 1. Failure under load can occur due to excessive elastic deflections or due to excessive stresses. 2. Failure prediction theories due to excessive stresses fall into two classes: Failure when the loading is static or the number of load cycles is one or quite small, and failure due to cyclic loading when the number of cycles is large often in thousands of cycles. Failure under static load Parts under static loading may fail due to: a) Ductile behavior: Failure is due to bulk yielding causing permanent deformations that are objectionable. These failures may cause noise, loss of accuracy, excessive vibrations, and eventual fracture. In machines, bulk yielding is the criteria for failure. Tiny areas of yielding are OK in ductile behavior in static loading. b) Brittle behavior: Failure is due to fracture. This occurs when the materials (or conditions) do not allow much yielding such as ceramics, grey cast iron, or heavily cold-worked parts or concrete. End of Lecture…….. 4 The yield point, alternatively called the elastic limit, marks the end of elastic behaviour and the beginning of plastic behaviour. When stresses less than the yield point are removed, the material returns to its original shape. For many materials that do not have a well-defined yield point, a quantity called yield strength is substituted. Yield strength is the stress at which a material has undergone some arbitrarily chosen amount of permanent deformation, often 0.2 percent. Any increase in the stress beyond the yield point causes greater permanent deformation and eventually fracture. A point at which Maximum load or stress required to initiate the plastic deformation of material such point is called as Upper yield point. And a point at which minimum load or stress required to maintain the plastic behavior of material such a point is called as Lower yield point. Upper yield point is the point after which the plastic deformation starts. This is due to the fact that the dislocations in the crystalline structure start moving. But after a while, the dislocations become too much in number and they restrict each other’s movement. This is called strain hardening and lower yield point is the point after which strain hardening begins. Dislocations are defects present in crystal areas where atoms are out of position (irregular alignment). Why the lower yield point stress value of mild steel is consider as a strength of material instead of upper yield point stress? Failure of mechanical component means it fail To perform it's operations efficiently for example consider shaft which transmits rotational motion ,now when shaft is unable to transmit motion efficiently then it will fail. Basically their are three types of failure in case of mechanical component i.e 5 1) failure due to elastic deformation 2) failure due to plastic deformation 3) failure due to fracture When component deforms elastically it's dimensions changes and it fails. And this failure is known as failure due to elastic deformation When component undergoes plastic deformation it's dimension changes permanently and failure takes place this is known as failure due to plastic deformation. For ductile metals elastic failure is criteria of failure because ductile metals undergo elastic deformation before failure. And elastic deformation starts at lower yield point. As Mild steel is ductile material we consider lower yield point Upper yield point is not constant it varies with shape of specimen and rate of loading Lower yielding point is constant for all shapes and rate of loading because of its consistency lower yielding point is taken as yield stress of mild steel Upper yield point corresponds to the load that is required to initiate yielding. Lower yield point corresponds to the min load that is required to maintain yield. Normally we use the lower yield point to determine the yield strength of the material being tested, cause the upper yield is momentary. Upper yield point is the max load at which deformation starts, starting of deformation means dislocations are started moving in the material. So this type of phenomenon is called permanent deformation by slip ( slip mechanism). 6 As the slip is taking place in the material, it offers less resistance to the material and hence curve falls slightly ( stress is the measurement of resistance offered by the material during the application of load). And it reaches to some stress ( lower yiled point stress) which is the minimum stress required to maintain the deformation in the mateial.. And at the lower yield point for the low carbon steels ( mild steels) the stress strain cure is in some wave nature , this is because to break bonds with impurites while dislocations are moving out of the material , hence resistance increases and decreases periodically after that strain hardening takes place which increases resistance slowly by increasing of dislocations in the material... What is strain softening and strain hardening? Work hardening, also known as strain hardening is the strengthening of a metal by plastic deformation. This strengthening occurs because of dislocation movements and dislocation generation within the crystal structure of the material. Reason for Work hardening: As the deformation of the material occur in the plastic region, the dislocation of the material increases. The dislocation interaction is repulsive in nature. As the dislocation density increases the further deformation of the material become difficult, this is called Work Hardening or Strain Hardening. some materials exhibit an elevation in yield stress along with plastic strain, sometimes strain rate or some internal variables which is known as hardening and if it shows a decrease in yield stress with plastic strain, it is called softening. Strain hardening is the process of increasing the hardness and strength of a metal by plastic deformation and is a cold working process. Strain hardening is due to the increased resistance to dislocation movement through a crystal lattice. No crystal lattice is perfect, it has some crystallographic defects called dislocations ( Dislocation). The dislocation movement is along the slip plane (plane of greatest atomic density and direction is along the closest packed direction within the slip plane).Slip will occur when the shear stress along the crystallographic plane reaches a critical value, which leads to movement of dislocations. What is Plasticity?
Details
-
File Typepdf
-
Upload Time-
-
Content LanguagesEnglish
-
Upload UserAnonymous/Not logged-in
-
File Pages28 Page
-
File Size-