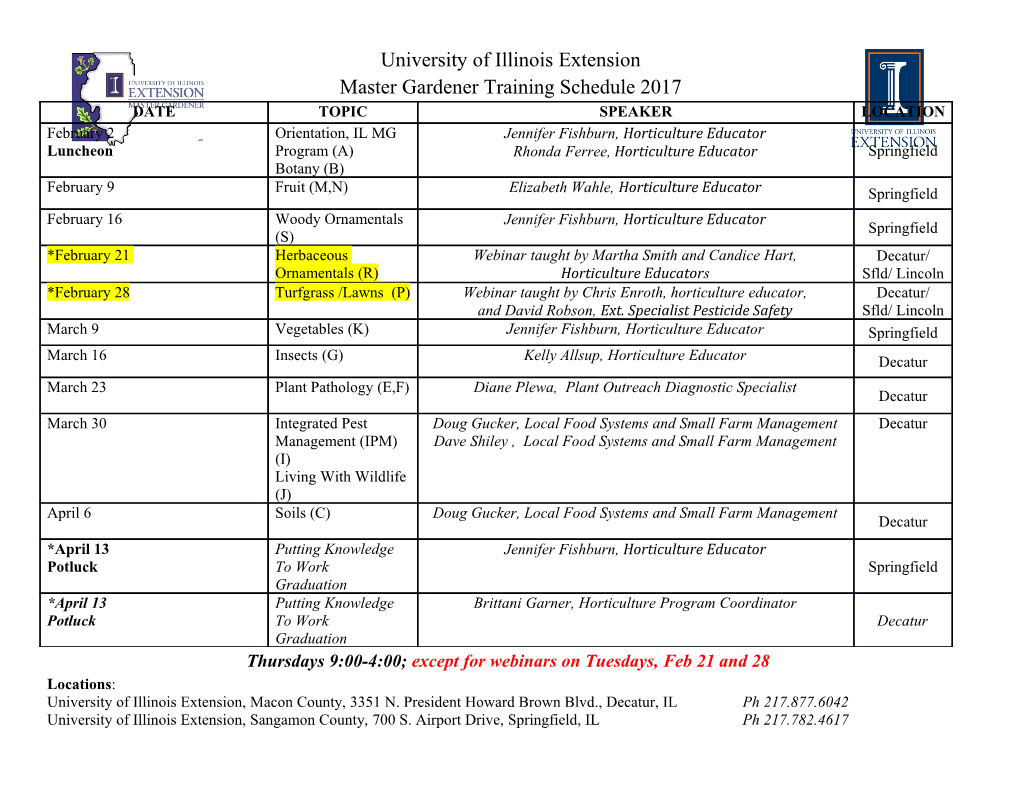
ASM Handbook, Volume 15: Casting Copyright © 2008 ASM International® ASM Handbook Committee, p 468-481 All rights reserved. DOI: 10.1361/asmhba0005240 www.asminternational.org Thermophysical Properties Juan J. Valencia, Concurrent Technologies Corporation Peter N. Quested, National Physical Laboratory ADVANCED COMPUTER SIMULATION of casting processes must not be used indiscrim- Limitations and Warning on TECHNOLOGY is a powerful tool used to inately without knowing their source and reli- the Use of Data understand the critical aspects of heat transfer ability. Prior to using a given set of data, it is and fluid transport phenomena and their rela- very important to critically evaluate and analyze tionships to metallurgical structures and defect the available thermophysical property data, to The thermophysical properties data presented formation in metal casting processes. Computa- give judgment on their reliability and accuracy. in this article are provided to assist in the mate- tional models are enabling the design and pro- There are several main sources of thermo- rials properties selection for the simulation of duction of more economical and higher-quality physical property data that provide the most casting processes. Great effort has been exer- castings. In order to produce accurate and reli- authoritative and comprehensive compilations cised in the compilation and analysis of the able simulation of the complex solidification of critically and systematically evaluated data data, and careful attention has been taken to processes, accurate, self-consistent, and realis- that are presently available. The challenge of faithfully duplicate the data and their sources tic thermophysical properties input data are finding data is discussed in Ref 2. The data found in the literature. The thermophysical necessary. Unfortunately, reliable data for have been published and can be found in the properties data provided here shall bear the many alloys of industrial interest are very following resources: warning “not for design purposes.” It is the full limited. responsibility of the reader to further investi- Sand, ceramic, and metal molds are exten- The Center for Information and Numerical gate the sources of information and follow all sively used to cast most metals. During the Data Analysis and Synthesis (CINDAS) gen- necessary engineering steps to make sure the solidification process, the predominant resis- erated and recommended reference values validity and quality of the data meet the tance to heat flow is within the mold/metal for diverse materials (Ref 3–12). requirements of the intended application. interface and the mold itself; thus, the primary Smithells’ Metals Reference Book provides interest is not the mold thermal history but an extensive compilation of thermochemical Methods to Determine rather the rate at which the heat is extracted data for metals, alloys, and compounds of Thermophysical Properties from the solidifying metal. Therefore, heat metallurgical importance (Ref 13). transfer is the governing phenomenon in any Summary of Thermal Properties for Casting Experimental determinations of reliable ther- casting process. Heat transfer is fundamentally Alloys and Mold Materials by R.D. Pehlke mophysical properties are difficult. In the solid described by the heat-transfer coefficient, the and co-workers (Ref 14). state, the properties recorded in the technical lit- temperature gradient, the geometry of the sys- The ASM International Materials Properties erature are often widely diverging, conflicting, tem, and the thermophysical properties of both Database Committee publishes a compre- and subject to large uncertainties. This problem metal and mold material. hensive thermal properties database of most is particularly acute for materials in the mushy Table 1 shows the required thermophysical commercially available metals (Ref 15). and liquid state. Also, accurate, consistent, and properties that must be available for input Recommended Values of Thermophysical reliable thermophysical property measurements before reliable numerical simulations of a cast- Properties for Selected Commercial Alloys are experimentally difficult. Convection effects ing process can be performed, as well as their by K.C. Mills. Experimental determination, in molten samples and their interactions and influence in the prediction of defects. Current estimation, and validation of the thermophy- reactivity with their containers and environment commercial software requires that the thermal sical properties in the solid and liquid states often exacerbate the difficulties. conductivity, specific heat capacity, latent heat, (Ref 16) The measurements are difficult because of high solidus and liquidus temperatures, and density temperatures and the reactivity of some alloys. must be known for heat-transfer operations. Computer models based on first principles of Strategies adopted to minimize these effects are: Viscosity, density, wetting angle, and surface thermodynamics and kinetics of phase transfor- tension of the molten alloy are required for fluid mations have been developed to calculate ther- Perform the experiments quickly using tran- flow operations. In addition to the metal proper- mophysical properties for various materials in sient methods ties, mold materials properties are also needed the solid and liquid states (Ref 17–22). How- Choose crucible materials that contact the to conduct an effective simulation. ever, their use is still limited due to the lack sample to minimize reactions of thermodynamic data and accurate measure- Eliminate container levitation Sources and Availability ments of thermophysical properties for materi- Measure properties in microgravity als of industrial interest. Also, sensitivity Control the composition of the atmosphere of Reliable Data studies (Ref 23) are necessary to truly evaluate the reliability of calculated thermophysical Mills et al. (Ref 24) describe the necessity to The thermophysical property data found in the property data from these models in actual exercise care when analyzing the experimental literature for engineering and design calculations casting processes. results. The following cases are discussed: Thermophysical Properties / 469 Thermal diffusivity measurements for the Table 1 Thermophysical property data required for metal casting mushy region are prone to error because Computer modeling some of the energy supplied may be used Casting process Transport phenomena for for process, part design, and defect component casting Thermophysical data required prediction for further melting of the alloy. Oxide films on the surface of the molten Furnace metal S Heat transfer Heat-transfer coefficient Effective design for: alloy can affect measurements of physical Conduction Metal/mold Metal/core Riser Chill Insulation properties; wettability of the metal on the Convection Metal/chill Mold/chill Solidification direction O Solidification shrinkage crucible and/or rotor can affect viscosity Radiation Mold/environment Porosity Emissivity—Metal/mold/furnace wall measurements and nonwetting, leading to Hot spots L Temperature-dependent parameters low values for the viscosity. Density Heat capacity Conductivity Table 2 lists some common techniques used for I Latent heat of fusion the measurement of relevant thermophysical Liquidus and solidus properties. Mold core chillD Mass transfer Temperature dependent Effective design for: Numerous methods exist for the measure- (fluid flow) Viscosity Ingate Runner Vents ment of thermophysical properties of metallic Surface tension Pouring parameters materials and are cited in the literature (Ref I Density Temperature Pouring rate 16, 27–47). However, only a few of them have Mold filling time Cold shut been standardized, and most of them are limited F Missruns to the solid-state properties. The current ASTM Insulation Microstructural Phase diagram Microsegregation International standards and selected CEN and I evolution Phase chemical composition Macrosegreation ISO standards include: Capillarity effect (Gibbs-Thompson Grain size coefficient) Grain orientation C Specific heat capacity: Differential scanning Nucleation and growth parameters Phase morphology Solid fraction vs, temperature Mechanical properties calorimetry, ASTM E 1269, E 967, E 968, Diffusivity E 2253, E 793, and D 2766 (Ref 48–53). A Solubility Ceramics, EN 821–3 drop and DSC (Ref 54) Stress analysis Temperature-dependent parameters Casting design for: Thermal expansion: Dilatometry, ASTM E T Coefficient of thermal expansion Dimension and distortion 228; interferometry, ASTM E 289; and ther- Stress/strain Internal stresses momechanical analysis, ASTM E 831 (Ref I Hot tears and hot cracks 55–57). Ceramics, EN 821–1 and ISO O 17562, both dilatometry (Ref 58, 59) Thermal conductivity: Modulated-temperature N scanning calorimetry, ASTM E 1952; thermal Source: Ref 1 diffusivity of solids by the laser flash method, ASTM E 1461; and the steady-state heat flow, ASTM C 518 (Ref 60–62). Ceramics, EN 821–2 and ISO 18755, both laser flash (Ref Table 2 Thermophysical and mechanical properties needed for casting process simulation 63, 64) and common measurement techniques Thermal emittance: Radiometric techniques, Thermophysical property Measurement technique ASTM E 307 and E 408 (Ref 65, 66) Thermal conductivity Comparative stationary (solid), indirect (liquid) Heat capacity Differential scanning calorimetry, pulse heating; drop calorimetry Best practices for the measurement of alloy Density Archimedian
Details
-
File Typepdf
-
Upload Time-
-
Content LanguagesEnglish
-
Upload UserAnonymous/Not logged-in
-
File Pages14 Page
-
File Size-