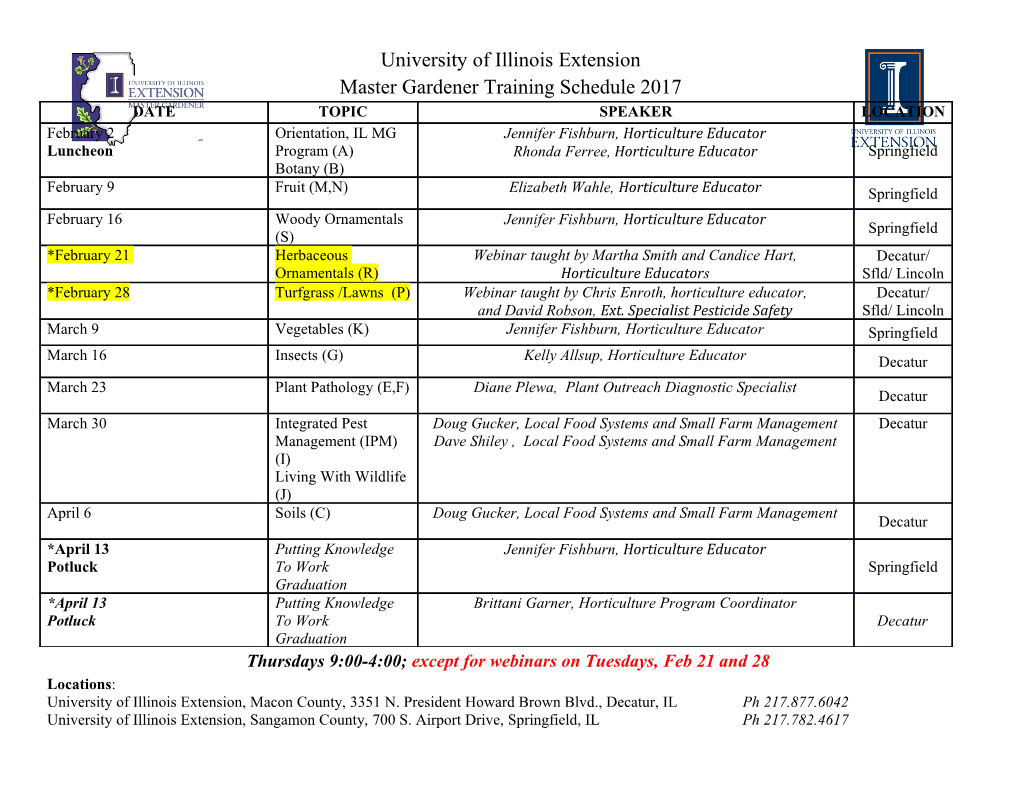
Catal Lett (2011) 141:168–177 DOI 10.1007/s10562-010-0468-z Study on Alumina-Supported Cobalt–Nickel Oxide Catalyst for Synthesis of Acetonitrile from Ethanol Cheng Feng • Yuecheng Zhang • Yining Zhang • Yanlong Wen • Jiquan Zhao Received: 2 July 2010 / Accepted: 8 October 2010 / Published online: 26 October 2010 Ó Springer Science+Business Media, LLC 2010 Abstract A new alumina-supported cobalt–nickel oxide 1 Introduction catalyst for the synthesis of acetonitrile from ethanol and ammonia was prepared by coprecipitation-kneading Acetonitrile is an important fine chemical product which has method. The parameters influencing the reaction were been widely used as the synthetic intermediate for pharma- studied thoroughly and an optimized process, which is ceutical, agricultural, and functional material chemicals [1]. running the reaction at 380 °C under atmospheric pressure It also used as a general purpose solvent for many com- while keeping the ammonia/alcohol molar ratio of 5 and pounds and movable phase in high-performance liquid GHSV of 1,163 h-1, was obtained. Under the optimized chromatographic analysis. Currently, it is mainly produced conditions the catalyst reached its best performance when as a by-product during the propylene ammoxidation process being on stream for 40 h, at which the yield of acetonitrile to acrylonitrile [2, 3]. With the increasing demand, it is dif- was 92.6%. Then the selectivity to acetonitrile decreased ficult to meet the need in the future to obtain acetonitrile only gradually but the yield of acetonitrile always remained from the production of acrylonitrile. Furthermore, the pro- higher than 81% within 720 h. The samples of the fresh and duction of acetonitrile as a by-product of acrylonitrile has the used catalyst were characterized by XRD, XPS, TEM, disadvantages of concomitance of toxic hydrogen cyanide EDX and N2 adsorption–desorption analysis. The results and difficulty in separation of the crude product [4]. There- revealed that carbon deposition and formation of metal fore, it is important to develop a green and advanced process carbides from the active species in the catalytic runs led to to produce acetonitrile. Many methods have been reported to the deterioration of the catalyst. synthesize acetonitrile from other chemical substances up till now. The raw materials include carbon monoxide [5–8], Keywords Cobalt–nickel oxide Á Catalyst Á Acetonitrile Á methane or other hydrocarbon compounds [9–14], ethanol Ethanol Á Deterioration Á Metal carbides [15–21] and acetic acid [22, 23]. Among all the raw materials ethanol becomes the first choice because it can provide a process which avoids the concomitance of high toxic hydrogen cyanide and gives high quality acetonitrile. Two approaches so-called amination-dehygrogenation [20, 21] and ammoxidation of ethanol [15–20] can be employed to the transfer of ethanol to acetonitrile. However, only the former can meet the need of avoiding formation of high toxic & C. Feng Á Y. Zhang Á Y. Zhang Á Y. Wen Á J. Zhao ( ) hydrogen cyanide. In 1960s, Kryukov et al. [24] first reported School of Chemical Engineering and Technology, Hebei University of Technology, Tianjin 300130, the conversion of alcohols to acetonitriles by amination- People’s Republic of China dehygrogenation process over a fused iron catalyst. Since e-mail: [email protected] then, several catalysts have been reported to transfer ethanol to acetonitrile [4, 20, 25]. But all the catalysts suffer from a C. Feng College of Science, Agriculture University of Hebei, disadvantage of either a high ammonia/ethanol ratio Baoding 071001, People’s Republic of China dependence [20] or low acetonitrile selectivity [4]. Besides, 123 Study on Alumina-Supported Cobalt–Nickel Oxide Catalyst 169 no clear information about the lifetime and structures of the of the samples were recorded with a Rigaku D/max 2500 catalysts was mentioned in any of the reports. X-ray diffractometer using Cu Ka radiation (40 kV, 150 Recently, we prepared an alumina-supported cobalt– mA) in the range 2h = 10°–90°. X-ray photoelectron nickel oxide catalyst for the amination-dehygrogenation of spectroscopy (XPS) was performed with a PHI 1600 ethanol to acetonitrile by kneading method. The catalyst spectroscope using Mg Ka X-ray source for excitation. showed high catalytic activity, good selectivity and long Transmission electron micrographs (TEM) were obtained lifetime [21]. However, the catalyst was fragile during the on a JEOL 100CX-II instrument equipped with an energy course of regeneration for further investigation. For dispersive X-ray (EDX) detector (Oxford Instruments) at improving the mechanical strength of the catalyst, we used an accelerating voltage of 200 kV. Specimens for TEM coprecipitation-kneading method instead of kneading analysis were prepared by ultrasonic dispersion in n-buta- method to prepare a new alumina-supported cobalt–nickel nol where a drop of the resultant suspension was evapo- oxide catalyst. The catalyst also showed high activity, good rated on a lacey-carbon/Cu grid. The surface area, total selectivity to acetonitrile and long lifetime as that prepared pore volume and pore size distribution of the samples were by kneading method, but had good mechanical strength in measured at 77 K by nitrogen adsorption using a catalytic runs. Therefore, we characterized the catalyst Micromeritics ASAP 2020 Surface Area and Porosity thoroughly to explore the deterioration reasons of the new Analyzer. The crushing strength of the catalyst was mea- catalyst in catalytic runs. Herein, we present the results of sured on a ZQJ-II particle strength tester produced by the study. Dalian Intelligent Tester Plant. The applied force and idle stroke velocity were automatically set on 5 N/s and 1 mm/s, respectively. 2 Experimental Section The IR spectra of adsorbed pyridine were recorded using a Thermo Nicliet Nicolet Nexus 470 spectrometer equip- 2.1 Catalyst Preparation ped with a heatable and evacuatable IR cell with CaF2 windows, connected to a gas dosing-evacuating system. All the chemicals were reagent grade. The alumina-sup- The powdered samples were pressed into self-supporting ported cobalt–nickel oxide catalyst was prepared by wafers with a diameter of 20 mm and a weight of 50 mg. coprecipitation-kneading method as the following proce- Prior to analysis, all samples were pretreated at 400 °C for 5 dures. 44.4 g of Co(NO3)2Á6H2O and 6.7 g of Ni(NO3)2Á 1 h, under high vacuum conditions (5 9 10 Pa), followed 6H2O were dissolved in 302.6 g of distilled water, then into by cooling to 200 °C. Then, pyridine was adsorbed at this this solution was dropped 20% (w/w) sodium carbonate temperature for 15 min. The physisorbed pyridine was solution under vigorous stirring at 60 °C until the pH removed by evacuating during 1 h at 200 °C, under high reached 8. The reaction mixture was submitted to an aging vacuum conditions (5 9 105 Pa). Then the infrared spectra treatment at 80 °C for 0.5 h while maintained the pH of 8. were recorded. The resulting mixture was filtered and the solid separated was washed with distilled water until the pH of the filtrate 2.3 Catalytic Experiments reached 7 to remove the excess of sodium completely. Afterwards, the resulting solid was dried and pulverized to Catalytic tests were carried out in a continuous fixed-bed obtain a black powder finally. The black powder was mixed reactor. 30.0 mL of the catalyst sample was loaded into a with 34.7 g of c-Al2O3 pretreated with about 10 mL of 1% reactor (i.d. = 12 mm; length = 1,100 mm), which created diluted nitric acid. The mixture was kneaded for 3 h in a a catalyst zone of 100 mm. The temperature in the catalyst kneader and the resulting kneaded material was then pro- zone was kept constant and measured using a thermocouple cessed in an extruder to obtain extrudates in a diameter of located in the center of the catalyst bed. The ethanol (95%) 2 mm and length of 2.5 mm. The extrudates were superfi- was dosed into the reactor at a speed of 7.0 mL/h by a cially dried at 120 °C for 12 h, and then calcined at 550 °C syringe pump and the flux of ammonia was regulated by a for 4 h. The contents of Co and Ni were determined by PID cascade controller (STP 220 mL/min). The liquid inductively coupled plasma (ICP) spectroscopy. products were separated from a gas–liquid separator and analyzed by a gas chromatograph equipped with a 30 m of 2.2 Catalyst Characterization PEG-20M capillary column and a thermal conductivity detector (TCD) with H2 as carrier gas. The exhaust (H2, For determining the metal content, the sample was first NH3,C2H4 et al.) was analyzed by the same gas chro- dissolved in concentrated HNO3 and HF, and then the matograph with N2 as carrier gas. The components of the metal content of the solution was analyzed by a T.J.A. ICP- mixture were identified by a HP5971 MS equipped with a 9000(N?M) type ICP-AES instrument. The XRD patterns 30 m of PEG-20M capillary column. 123 170 C. Feng et al. 2.4 Regeneration Procedure 100 Regeneration of the used catalyst sample for further cata- lytic evaluation was carried out by continuously blowing 80 conversion of ethanol air (STP 250 mL/min) into the fixed-bed at 470 °C for 5 h selectivity of acetonitrile on-line. selectivity of butyronitrile 60 selectivity of ethylene selectivity of pyridine base selectivity of higher boiling 20 3 Results and Discussion components 10 3.1 Catalytic Activity Test Conversion/selectivity (%) 0 The mechanical strength of the catalyst was evaluated by 340 360 380 400 420 440 measuring the crushing strength of the catalyst.
Details
-
File Typepdf
-
Upload Time-
-
Content LanguagesEnglish
-
Upload UserAnonymous/Not logged-in
-
File Pages10 Page
-
File Size-