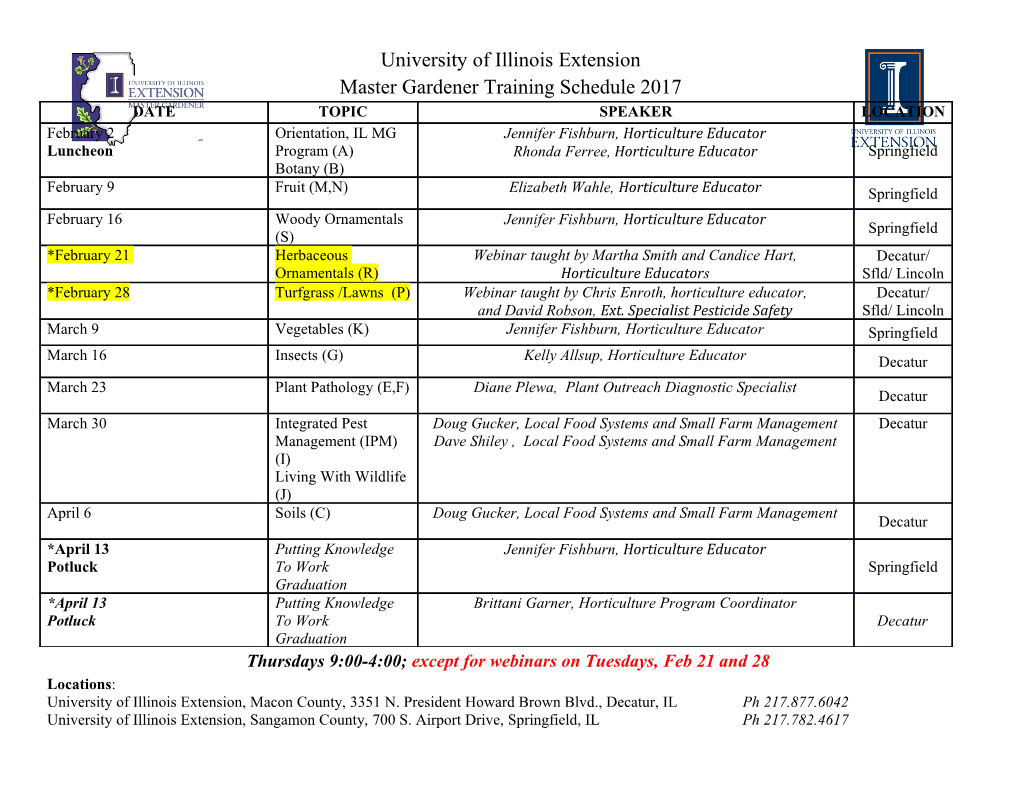
Improving a virtual race car performance using MSC.ADAMS/Car-MotorSports and modeFrontier modeFrontier User’s Meeting Trieste, Italy Sep 2004 Diego Minen Eddi Valvason Special Project Development Group MSCSoftware Courtesy of AUDI Sport Courtesy of SAUBER F1 Courtesy of Williams F1 Agenda Basic elements for Race Car Simulation System Level Approach for Race Simulation Multibody vehicle model Chassis Engine, GearBox, Differential, Driveline Tires Aerodynamics Track profile Driver Model Simulation Types Exploration of the limits=> Process Integration Functional Virtual Race Vehicle Track Data 3D CAD Test Data Flexibility Aerodynamics Controls/Hydraulics Success – at Audi Sport Business: Automotive Race Manufacturer Challenge: Re-enter Sport Racing at Le Mans Solution: Virtual race car + track; rapid design iteration Value: 1999 : 3rd 2000 : 1st, 2nd, & 3rd 2001 : 1st & 2nd 2002 : 1st, 2nd, & 3rd 2003 : 1st, 2nd (Bentley) 2004 : private team victory “…procedures to optimize vertical dynamics, aerodynamic, mechanical setup and differential setup at the same time simulating a high dynamic kerb crossing have been investigated… simulation helps to understand how to improve performance of a complex race vehicle...“ --Dr. Martin Mühlmeier Vehicle Dynamics AUDI Sport AG Ingolstadt Success – at N.Technology Business: Motorsport competitions (ETCC, Rally) Challenge: To shorten development cycle while improving the over all performance Solution: Use ADAMS/Motorsport (Analyses: Suspension, 4post testrig, ADAMS/Insight, AeroLap, Close Loop Track Simulations) Value: Won TCC Championship in 2001, 2002 and 2003. “Using ADAMS/Motorsport allows us to build and tune suspension subsystems in a more productive way before going on the test track. Running sensitivity studies with hundreds of different configurations is now a matter of minutes. ADAMS/Motorsport gives us also the possibility to have all important parameters under control.” -- Guido Pasquino Head of Calculation Dept. ADAMS/MotorSports Outline Aston Martin NewmanHaas CART Audi Sport AG NTech BAR F1 Panther Racing Dallara Automobili Patrick Racing Dunlop MotorSports UK Penske (IRL & NASCAR) DODGE Motorsports Porsche Ferrari F1 PPI Motorsports Ford MotorSports Prodrive Gforce SAUBER F1 Goodyear Tire Co. Solution F. GM MotorSports Team Rosberg F3 HWA-AMG Racing Toyota F1 Jaguar F1 Team Menard IRL Jasper Motorsports Team Mo Nonn IRL Lotus Engineering Williams F1 MultiMatic CAR/MS CAR PRE/MS CAR&PRE The Vehicle Model Assembly Template Component Data Files Files (Teim Orbit) E ADAMS L Suspensions Dampers C Engine Map I Chassis Bushings Vehicle H E Steering Bumpstops Model V Brakes Tires ... ... Vehicle+Road+Driver System Toe Course Data File N O Camber I A (Teim Orbit) System & Analysis T Caster T Configuration A A P Ride height R D U 2D or 3D - Springs Static Sim U T profile D Steering Pad Fuel G Driver E I A Step Steer F S Driver Mass Open Loop O Racing Line Double Lane Driver path N Machine Ballast R Data Driven ... Max Xls O Human ... C The Simulation Requirements Basic elements for Race Car Simulation Simulation Types Quasi-Static Testrigs Suspension 2D or 3D Tracks Open or Closed Even road profile Dynamic Testrigs Tires MultiPostRigs 2D or 3D Tracks Open Loop Closed Loop (limit performance Driver Model) Even or uneven road profile Real Time SmartDriver Architecture SmartDriver is a feedback controller: it receives as inputs the sensor measurements and provides the vehicle controls: steering, throttle, User Inputs: Task Planner -driving style brake, clutch and gear commands -driving task on line learning -… The control actions depend only on past and Trajectory Planner present measurements r e Motion Controller v i s l e It mimics human driving on one hand and drive r n n D a h t c r the vehicle to its dynamic limits of performance on n Perception channels o a i t a u t m c the other A S The two different control tasks are taken into ACAR Model Tire Model Road Builder account and can be both fullfilled thanks a 2D Aero Model 3D Model Based Predictive Controller technique Robustness and, consequently, limited need of Road Model tuning is the crucial requirement SmartDriver Machine Controller desired velocity desired yaw rate on connecting contour actual yaw rate Yaw rate control path geometry Control of Lateral Dynamics ADAMS Vehicle Model Road Model Throttle velocity r e Clutch Acceleration l l Brake gear o r t Gear RPM n o C Control of Long Dynamics n o i t o Trajectory Planner M The program drives the vehicle along a desired path, given as a curve in 3D at velocity v(s) SmartDriver provides default inputs to the vehicle at a frequency of 100Hz: MACHINE driving The outer control loop uses a one track nonholonomic vehicle model and computes an optimal feasible vehicle trajectory up to the time horizon, or “preview time”, Tp From the current position to Tp, SD controls the vehicle yaw rate The inner control loop acts on steering, throttle and brake to best track the yaw rate profile determined above SmartDriver at Max Speed - MSC.Track Requirements for Improvements Identify component data from experimental analysis Tires Exploration of the limits with the full car model MultiObjective Optimization Handling Tire Magic Formula Identification EExxaammpplele: :P Paacceejijkikaa 9 944 [L[LAATTEERRAALL__CCOOEEFFFFICICIEIENNTTSS] ] aa00 = = n nuummbbeerr aa11 = = nnuummbbeerr Identification Process aa22 = = n nuummbbeerr aa33 = = n nuummbbeerr aa44 = = n nuummbbeerr Experimental Data have been considered as data to identify aa55 = = n nuummbbeerr aa66 = = n nuummbbeerr aa77 = = n nuummbbeerr Virtual Tyre Model the Magic Formula is commonly used to calculate the aa88 = = n nuummbbeerr aa99 = = n nuummbbeerr aa1100 = = n nuummbbeerr steady-state and transient behavior of handling tire. It’s a set of aa111111 = = n nuummbbeerr aa111122 = = n nuummbbeerr aa1122 = = n nuummbbeerr mathematical formulas based on the physical behavior of the tire, road, aa1133 = = n nuummbbeerr aamm00 = = n nuummbbeerr and the tire-to-road contact; it calculates the forces (Fx, Fy) and moments aamm11 = = n nuummbbeerr aamm22 = = n nuummbbeerr aamm33 = = n nuummbbeerr (Mx, My, Mz) acting on the tyre under pure and combined slip conditions, aamm44 = = n nuummbbeerr aamm55 = = n nuummbbeerr aamm66 = = n nuummbbeerr using longitudinal and lateral slip( , ), wheel camber ( ) and the vertical aamm77 = = n nuummbbeerr aamm88 = = n nuummbbeerr force (Fz) as inputs aamm99 = = n nuummbbeerr EExxaammpplele: :P Paacceejkjkaa9944 - -LLaateteraral lFFoorcrceeEEqquuaatitoionnss Softwares Used: CC==aa00 DD==(a(a11**FFZZ++aa22)*)*FFZZ**RROOAADDMMUU TireBuilder Æ generation of the lateral force BBCCDD==aa33**SSININ(A(ATTAANN(F(FZZ/a/a44)*)*22.D.D00)*)*(1(1.0.0-a-a55**AABBSS(G(GAAMMMMAA))) BB==BBCCDD/(/C(C**DD)) curves SShh==aa88**GGAAMMMMAA++aa99**FFZZ++aa1100 SSvv==(a(a111122**FFZZ++aa111111)*)*FFZZ**GGAAMMMMAA++aa1122**FFZZ++aa1133 PHI=(1-E)*(DELTA+Sh)+E/B*ATAN(B*(DELTA+Sh)) Excel Æ formulating of relaxation length eqs PHI=(1-E)*(DELTA+Sh)+E/B*ATAN(B*(DELTA+Sh)) EE==(a(a66**FFZZ++aa77) ) CCGG==aamm00 Æ modeFRONTIER used as identifiction tool AAGG==aamm11 BBGG==aamm22**CCOOSS(A(ATTAANN(a(amm33**(D(DEELLTTAA-a-amm44)))) TARGET: Create automatically a TIR file to reproduce GGaa00==aamm66**FFZZ++aamm77 FFyy00==DD**SSININ(C(C**AATTAANN(B(B**PPHHI)I)+)+SSvv the experimental tire curves FFyyxxgglil=i=SSININ(1(1.9.9**AATTAANN(a(amm88**KKAAPPPPAA))) FFyyxxddeel=l=CCOOSS(A(ATTAANN(a(amm99**DDEELLTTAA))) FFyyxx==aamm55**FFZZ**(G(GAAMMMMAA-G-Gaa00)*)*FFyygglil*i*FFyyddeel l FFyy==FFyy00**CCOOSS(C(CGG**AATTAANN(B(BGG**(K(KAAPPPPAA-A-AGG)))/)C/COOSS(C(CGG**AATTAANN(-(B-BGG**AAGG))+)+FFyyxx Handling Tire Magic Formula Identification Identification Targets Tire Lateral Response [ Fy = Fy(D,Fz) ] V Relaxation Length [ D] ­ ª º½ ­ª CP § 180 ·º FL ½ ° Fz ° ¡ V V o ® ¨ ¸ ¾ o Pty1 SIN ®Pty2 ATAN « »¾ R0 « S » LS 2 ° « Fz0 Pty3 »° ¯¬ © ¹¼ ¿ ¯ ¬ ¼¿ Tire Lateral Response Identification Process The methodology has been structured in the following way: Experimental Data: 8 lateral force curves: 4 Fz values 2 camber values 128 check points (16 for each experimental curve) Æ the objective is made by the sum of the difference between the target point and the point evaluated from Tire_Builder: OBJ ¦ >ABS Pti Pi @ i where “i” Æ [1,...,112] All the Pacejka Pure-Lateral Coefficients (18 coeff) have been considered as input variable for the IP The TIR file considered is based on the MF Tyre model. All Pacejka Pure-Lateral Coefficients have been considered, and during the IP each coeff has been changed of ± 50% with respect its original value. From the optimization point of view the problems is equivalent to find the minimum of an objective function which is mathematically defined as: n m f : where: n: it represents the number of the input variables Æ 18 m: it represents the number of the objective Æ 1 Tire Lateral Response Identification Process Structure 1. The experimental tire curves are considered as the target for the IP (i.e. Curves representing Æ Lateral Forces, Aligning Moments Æ as function of different Normal Forces, Camber and Lateral Slip Angles,...) 2. For each curve a certain number of check points has been chosen, in order to compare them with those calculated with Tire_Builder during the IP Æ or during the variation of the Pacejka coefficients in the TIR file • 16 check points for each curve • 4 Fz values • 2 camber values For a total of: • 8
Details
-
File Typepdf
-
Upload Time-
-
Content LanguagesEnglish
-
Upload UserAnonymous/Not logged-in
-
File Pages39 Page
-
File Size-