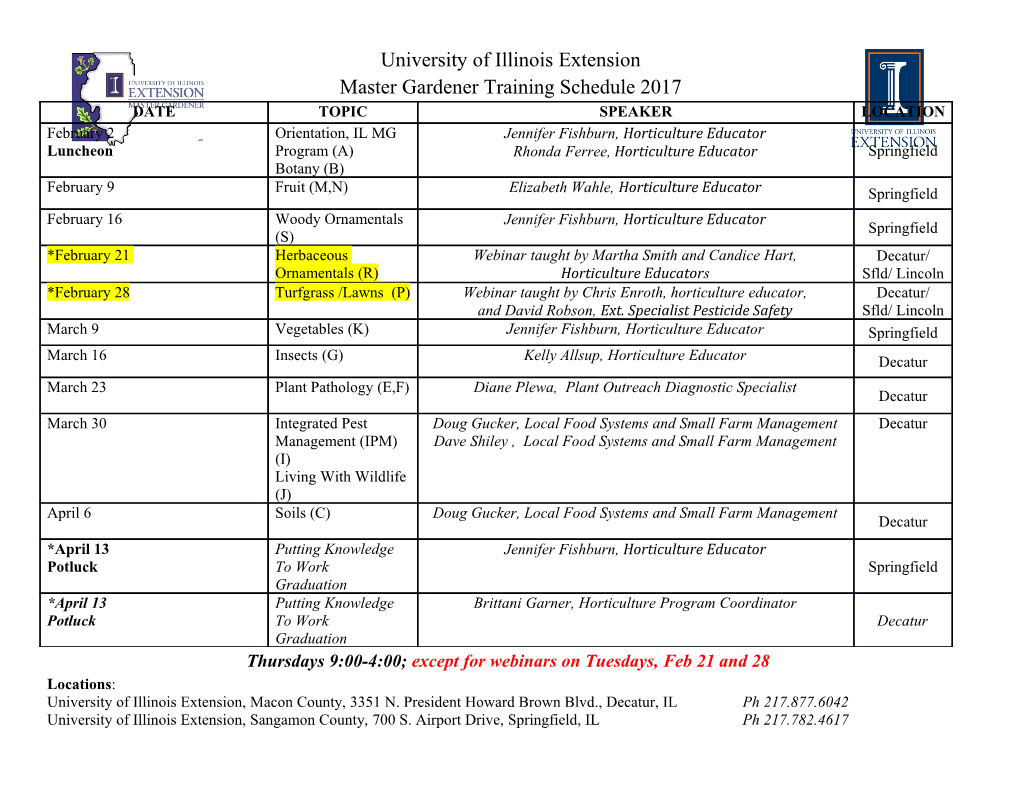
THE CATHOLIC UNIVERSITY OF AMERICA Wideband Structural and Ballistic Radome Design Using Subwavelength Textured Surfaces A DISSERTATION Submitted to the Faculty of the Department of Electrical Engineering and Computer Science School of Engineering Of The Catholic University of America In Partial Fulfillment of the Requirements For the Degree Doctor of Philosophy © Copyright All Rights Reserved By Paul Eugene Ransom, Jr. WASHINGTON, DC 2016 Wideband Structural and Ballistic Radome Design Using Subwavelength Textured Surfaces Paul Eugene Ransom, PhD Director: Ozlem Kilic, D.Sc. This dissertation presents a methodology for designing and fabricating wideband structural and ballistic radomes using conventional composite and ballistic materials. The methodology employed centers on transforming the radome design into an impedance matching problem utilizing electrically compatible materials. Included in this dissertation is a thorough overview of both structural composite and ballistic materials, with the aim of identifying the compatible conventional materials by highlighting both advantageous and detrimental electrical properties. Moreover, I describe the current state of the art in radome design and performance. As with all impedance matching problems there are standard techniques for developing impedance matching solutions, in this dissertation I describe the most common analytical methods for impedance matching. In addition to analytical methods for designing impedance matching structures, iterative methods are explored. The impedance matching solutions developed through the analytical and iterative methods are implemented using subwavelength textured surfaces. The efficacy of the textured surfaces is controlled by the accuracy of the numerical modelling, many of the common electromagnetic subwavelength modelling techniques like effective medium theory (EMT), are not sufficient to design textured surfaces because EMT breaks down. To address this short fall, the rigorous coupled wave analysis method was employed. Fabrication of properly modelled textured surfaces was accomplished using both subtractive and additive manufacturing techniques. The advantages and pitfalls of each manufacturing technique is explored and conclusions are provided. Finally, to validate this methodology I present experimental results of radomes designed and fabricated using this new methodology. This dissertation by Paul Eugene Ransom Jr. fulfills the dissertation requirement for the doctoral degree in Electrical Engineering approved by Ozlem Kilic, Dr. Sc. as Director, and by Nader Namazi, Ph.D., Mark Mirotznik, Ph.D., and Steven Russell, Ph.D., as Readers. Dr. Ozlem Kilic, Director Dr. Nader Namazi, Reader Dr. Mark Mirotznik, Reader Dr. Steven Russell, Reader ii Dedication As children, my sisters and I would spend our summers in Fort Pierce, Florida, with my mother’s family. These opportunities to connect with my aunts, uncles, cousins, and especially my grandmother were times I still cherish. My grandmother, Laura Idella Grier, was the unquestioned matriarch and head of our family. She always had the highest of expectations for me and would often refer to me as “Dr. Paul,” declaring that I would one day be a doctor. She was a steadfast servant of God, rock of her family, and friend to many. I dedicate this work, in loving memory, to my beloved grandmother, Laura Idella Grier. iii Dedication iii List of Figures viii List of Tables xiv Acknowledgements xv Chapter 1: Introduction 1 Contributions to Radome Design 4 Original Publications 5 Overview of Dissertation 6 Chapter 2: Structural Composites Background 8 Structural Composite Materials 8 Matrix Systems 15 Structural Core Materials 19 Electrical Properties of Structural Composite Materials for Radomes 22 Chapter 3: Composite Armor Background 26 Ballistic Armor Design Considerations 27 iv Chapter 4: Current State of Radome Design and Performance 30 Non-structural Radomes 30 Conventional Structural Radome 36 Sandwich Wall Materials 37 Ballistic Radomes 41 Chapter 5: Wideband Impedance Matching Methodologies 44 Wideband Impedance Matching by Dielectric Layers 44 Analytical Methods 45 Tapered Structures or networks 52 Iterative Optimization 55 Textured Surfaces 57 Chapter 6: Numerical Methods 63 Multilayered Dielectrics 64 Rigorous Coupled Wave Method 67 Iterative Design 82 Chapter 7: Wideband Structural Radome Design 90 v Conventional Radome Design Methods 90 Antireflective Surface Radome Approach 92 Chapter 8: Ballistic Radome Wall Configuration Simulations 110 Ballistic Protection Radome Numerical Examples 113 Chapter 9: Antireflective Surface Fabrication Methods 118 Subtractive manufacturing - Computer Numerically Controlled (CNC) Machining 118 Additive Manufacturing Implementation 122 Chapter 10: Experimental Validation 128 Measurement System Background 129 Alternating Slope AR Ballistic 5-30GHz Radome FDM Iterative Design 132 Klopfenstein AR Surface Experimental Validation 134 Alternating Slope AR Structural Composite K-Band Radome 138 Chapter 11: Conclusion 141 References 144 Appendix A 150 vi Rigorous Couple Wave Analysis Enhanced Transmittance Matrix Approach 150 Analytical solution for rectangular and hexagonal permittivity distributions 153 vii List of Figures Figure 1.1 Radome wall configuration and associated frequency performance 1 Figure 1.2 Multilayer Dielectric Slab EM Configuration 2 Figure 1.3 Broadband Radome “Gold Standard” configuration and insertion loss. 3 Figure 2.1 (a). Illustration of structural composite layup. (b) Balsa Wood structural composite. 9 Figure 2.2 (a) Bundle of fibers. (b) 2D plain weave woven cloth. 9 Figure 2.3 Example of a single stack or multi-stack laminate 10 Figure 2.4 Plain Weave 14 Figure 2.5 Satin Weave 14 Figure 2.6 Honeycomb core. 20 Figure 2.7 Foam core. 21 Figure 3.1 Non-Armor Piercing Ballistic Protection Layers 26 Figure 3.2 Ballistic Protection Enhanced Design 28 Figure 4.1 Geodesic fabric radome 30 Figure 4.2 Complex Permittivity of E-glass 2D plain weave woven cloth and an E-glass plain weave vinyl ester laminate. 32 Figure 4.3 Complex permittivity of S-glass 2D plain weave woven cloth and an S-glass plain weave epoxy laminate. 33 Figure 4.4 Complex permittivity of Astroquartz 2D plain weave woven cloth and an Astroquartz plain weave epoxy laminate. 34 Figure 4.5 Insertion loss for Astroquartz, S-glass and E-glass laminates as a function of normalized thickness 35 Figure 4.6 Sandwich Radome Configuration 37 Figure 4.7 Radome Wall Categories 37 Figure 4.8 Structural core material loss calculated at 40GHz 39 Figure 4.9 Sandwich composite insertion loss for Astroquartz, S-glass and E-glass face sheets. 40 Figure 4.10 Non-AP Ballistic radome insertion loss for Figure 3.2 configuration 42 viii Figure 4.11 Amor piercing ballistic radome insertion loss for Figure 3.2 configuration. 43 Figure 5.1 Antireflective Conceptual Approach 44 Figure 5.2 Microwave engineering impedance matching model 45 Figure 5.3 Quarter-wavelength multilayered configurations 48 Figure 5.4 (a) Semi-infinite or half space medium configuration. (b) Dielectric slab configuration 48 Figure 5.5 Example of Klopfenstein, exponential and optimized multilayered tapered surfaces 54 Figure 5.6 General iterative optimization algorithm 56 Figure 5.7 – 1-D and 2-D Periodicity 58 Figure 5.8 – Common Grating Lattice Types and Fill Factors for CNC Implementation 59 Figure 6.1 Multilayered Dielectric 64 Figure 6.2 Two-dimensional periodic dielectric grating and problem geometry 67 Figure 6.3 Structural composite radome wall physical configuration and lay-up. 82 Figure 6.4 Direct Design Method Algorithm 83 Figure 6.5 Indirect Design Method Algorithm 84 Figure 6.6 Permittivity profile for Example 5. 86 Figure 6.7 Permittivity comparison between iterative design and Klopfenstein taper. 88 Figure 6.8 Transmission comparison between iterative design example 5 and Klopfenstein taper example 1 from normal incidence to 60° incidence. 88 Figure 7.1 Mode Matching Generalized Scattering Matrix 91 Figure 7.2 Slab transmission 94 Figure 7.3 Structural Composite Face sheet Permittivity and Loss Tangent Comparison 95 Figure 7.4 Permittivity and Loss Tangent of Structural Sandwich Composite Core Foams 95 Figure 7.5 Structural composite wall configuration without an AR surface and the associated transmission loss exhibited by the wall configuration. 97 Figure 7.6 Structural composite radome wall physical configuration and lay up – Klopfenstein FDM Polycarbonate Taper. Permittivity profile of two Klopfenstein AR surfaces implemented using FDM additive manufacturing. 100 ix Figure 7.7 Structural Composite insertion loss without AR surfaces Structural radome insertion loss simulation assuming Klopfenstein AR surfaces are layed up in accordance with Figure 7.6. 100 Figure 7.8 Structural composite radome wall physical configuration and lay up. Permittivity profile of two AR surfaces designed using simulated annealing and pattern search optimization routines; and implemented using FDM additive manufacturing. 101 Figure 7.9 Structural Composite insertion loss without AR surfaces (b) Structural radome insertion loss simulation assuming iteratively optimized AR surfaces that are layed up in accordance with Figure 7.8. 102 Figure 7.10 Structural composite radome wall physical configuration and lay up. Permittivity profile of two AR surfaces designed using simulated annealing and pattern search optimization routines; and implemented using FDM additive manufacturing. 103 Figure 7.11 Structural Composite insertion loss
Details
-
File Typepdf
-
Upload Time-
-
Content LanguagesEnglish
-
Upload UserAnonymous/Not logged-in
-
File Pages172 Page
-
File Size-