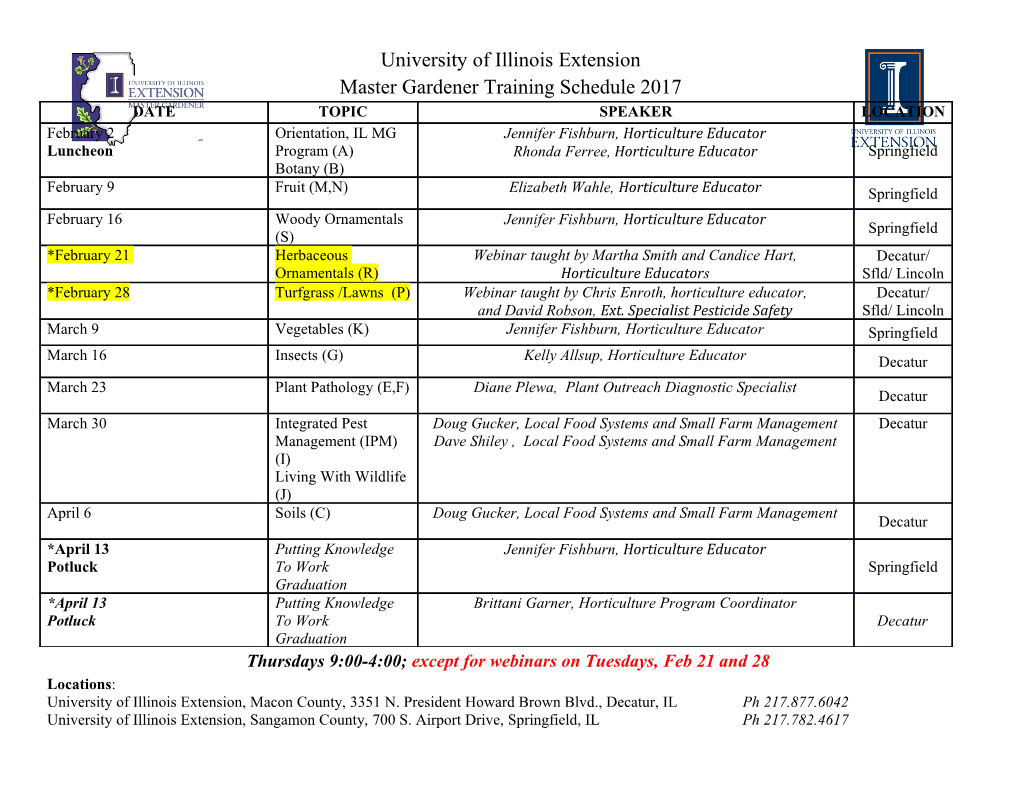
ENGINEERING TRIPOS PART IIA, 2012-13 MODULE 3C1: Materials Processing and Design MANUFACTURING ENGINEERING TRIPOS PART IIA, 2012-13 PAPER 3P1: Materials into products HANDOUT 2: CASTING 1. Processes, selection and design 1.1 Casting processes 1.2 Process selection 1.3 Design of castings 2. Solidification theory 2.1 Revision of nucleation theory 2.2 Solidification mechanisms 2.3 Solidification of alloys 3. Microstructure of castings 3.1 Grain structure 3.2 Chemical inhomogeneity 3.3 Porosity 3.4 Casting alloys Essential Revision: Phase diagrams, phase transformations, shaping processes IB Materials notes + Teach Yourself Phase Diagrams (www-materials.eng.cam.ac.uk/typd) Ashby, Shercliff & Cebon: Materials: engineering, science, processing and design (Ch. 18, 19) Ashby & Jones: Engineering Materials II Other References for Casting: Edwards L and Endean M. Manufacturing with Materials (CUED JA146) Waters, TF. Manufacturing for Engineers (CUED BN204) Campbell, J. Castings (Lots of technical detail) (CUED JO41) H.R Shercliff (C.Y. Barlow) October 2012 1 1. PROCESSES, SELECTION AND DESIGN 1.1 Casting processes Typical casting process and terminology: Sand Casting 1. A solid re-usable pattern (often wooden) is made of the component. 2. Sand with a small amount of resin binder is packed around the pattern in a box called a drag. 3. The drag is inverted and the pattern is lifted out, leaving a cavity. In-gates and runners may be carved or moulded into the sand. 4. Interior detail may be produced by inserting a core (also moulded out of sand) into the cavity. The upper part of the mould (the cope) is formed from sand, incorporating a pouring basin, a sprue, vents, risers/feeder heads (either moulded from patterns – e.g. runner pin and riser pin shown – or which may be carved in. 5. Mould bolted together, metal poured in. Once the casting has solidified, the mould is removed and the sand mould and any cores broken up and brushed out. The casting is fettled: cutting off the runner, ingate, sprue, risers and feeder head. The parting line of the mould may also leave a ridge which must be ground off. 2 Overview of Casting Processes Melt Transfer into mould Remove from mould Refractory (ceramic) crucible Pour under gravity Permanent mould (e.g. ingot casting, “Clean” heat sources: or continuous casting, Electric furnace, or RF Force under high pressure die casting): induction into mould open mould, remove (can be under vacuum or in an or inert gas atmosphere) part, clean mould and Use inert gas pressure re-use or (controlled atmosphere) to Oil/gas-fuelled furnace force metal into mould Permanent pattern (e.g. sand casting): one-off moulds, destroy on removal Check composition Solidify: a few before casting; additives seconds for small to refine grain size or parts; days for large modify structures Classification of casting processes Ingot or Continuous Shaped Casting Casting (i.e. solidify to near net-shape) Permanent mould casting Permanent pattern casting Simple shapes: no re-entrant More intricate shapes: mould surfaces (need to be able to for each individual casting is Continuous casting remove parts from mould). created around a pattern and for most high-volume Moulds expensive (tool steel; mould is destroyed as the steel; “direct chill” may make 103 – 106 castings), casting is removed. (DC) casting for production rates high. Low setup costs and wrought aluminium production rates. alloys. Typically used for large numbers of small parts. Used for larger parts, or Ingot casting when small production runs. (permanent mould) Examples: Examples: used for lower Gravity die casting Sand casting volume alloys. Pressure die casting Investment casting Centrifugal casting Evaporative mould casting Post-processing: Post-processing: Homogenisation “Fettling” (trim solidified feeder channels) + Thermomechanical Machine/grind critical areas (improve tolerances and surface processing, e.g. finish around joints, seals, contact surfaces) hot/cold rolling, Machine/drill features, holes etc. forging, extrusion Some castings heat-treated to improve properties. + heat treatment 3 Examples of permanent pattern (expendable mould) casting Sand Casting (details above) Advantages: Versatile, low material and equipment costs, OK for large simple parts; internal detail possible. Disadvantages: Poor dimensional accuracy and surface finish; not good for thin sections; relatively high labour costs; “dirty” process; can’t be used for refractory metals because sand undergoes phase change. Investment casting Something of a hybrid process: by “permanent pattern” we mean that a permanent mould is made to make an expendable pattern. This pattern is covered in a disposable ceramic/ refractory shell in which the casting itself is produced. Advantages: Excellent accuracy and surface finish Disadvantages: Limited to small parts; much more expensive. 4 Full / evaporative mould casting Closely related variant, using a polystyrene foam pattern. Advantages: High accuracy and surface finish (especially with small-bead polystyrene); lighter patterns than wax, so suitable for large parts. Disadvantages: Labour still quite high Examples of permanent mould casting Pressure die casting Externally applied pressure permits use of higher viscosity fluid, thinner sections, and minimises waste from runners, risers etc). Susceptible to entrapped bubbles due to turbulence, which can be detrimental to properties – see later. A common, important process – often just called ‘die casting’. Limited to low-melting point alloys (because the dies must not distort or wear whilst making many thousands of castings). Common example: zinc die-casting alloy (a low-melting point alloy, Zn + 4Al, 1Cu, 0.05Mg), chosen for ease of processing and cheapness, rather than for good mechanical properties, e.g. toy models. (Note equivalent polymer process: injection moulding, the commonest polymer process. It uses a rotating screw to plasticise the polymer, but the whole screw is translated along the feeder tube to force the polymer rapidly into the mould.) Gravity die casting Variant process using gravity feed (as in sand casting) but with permanent mould in separable parts, as in pressure die casting. 5 Centrifugal casting Used for axisymmetric hollow parts (e.g. pipes) (A related process for polymers is Rotational Moulding) 1.2 Process selection The choice of process depends on a range of factors including: material size, shape complexity, section thickness These are covered by CES (below) dimensional accuracy, surface finish number of parts required mechanical (and other) properties Properties sensitive to the combination of material, process and design parameters Technical attributes 6 Quality attributes Economic attribute Process attribute charts from CES, for metal shaping processes. The same factors influence the choice of process class (cast vs. deformation vs. powder) and the choice of process variant within a class (e.g. sand cast Observations (both comparing process classes, and on variants within casting): - considerable overlap between process classes on mass and section thickness; - wide variation in precision and surface finish; - competition between process classes largely driven by economics – but remember that it may be cheaper to use an inexpensive process (e.g. sand casting) followed by a local machining), rather than a more expensive process. Casting Alloys versus Wrought Alloys Casting and thermomechanical (wrought) processes use different, dedicated alloys, as casting alloys must satisfy separate requirements relating to fluidity, lower melting point, and solidification microstructure. For example: - carbon steels (Fe + 0.1-0.8wt% C): hot/cold formed; cast iron (Fe + 4wt% C): only cast. - wrought Al alloys: Al + Mg + (Cu, Zn or Si) ( 1-5wt%): hot/cold rolled, extruded; cast Al alloys: Al +Si (typically 12%) (+ Cu, Mg): only cast. Castings have historically had poorer mechanical properties than their forged counterparts, largely because of a tendency to contain porosity, and a high second phase content. Casting (plus heat treatment) can be the route to high-quality property-critical components (e.g. internal Al alloy frame of Airbus doors, jet engine nickel alloy turbine blades). Remember that the properties achieved in a casting are dependent on the coupling between material, process and design parameters. 7 1.3 Design of castings Solidification rate Solidification time is important in casting because it affects: - production rate, and hence process economics - the resulting microstructure, and hence properties Chvorinov’s rule states that: solidification time of a section is proportional to [Volume/Surface area]2 Physical basis: One application of this is in the design of the feeder heads for (e.g.) sand castings. Most metals shrink on cooling and solidifying, so moulds are designed to hold a reserve of molten metal to allow metal to be fed in during solidification. Hence the metal in the feeder head must solidify last, otherwise parts of the casting may be starved, leading to porosity: Solidification rate also affects the scale of the microstructure, which may have implications for mechanical properties. What matters physically is not the total time for solidification, but the local velocity of the solidification interface. The length-scale of the microstructure (e.g. the spacing of the plates in eutectics) is inversely proportional to this velocity. Casting Defects Defects include cavities, and internal or surface cracks. Non-destructive testing (NDT) of component integrity is routine
Details
-
File Typepdf
-
Upload Time-
-
Content LanguagesEnglish
-
Upload UserAnonymous/Not logged-in
-
File Pages25 Page
-
File Size-