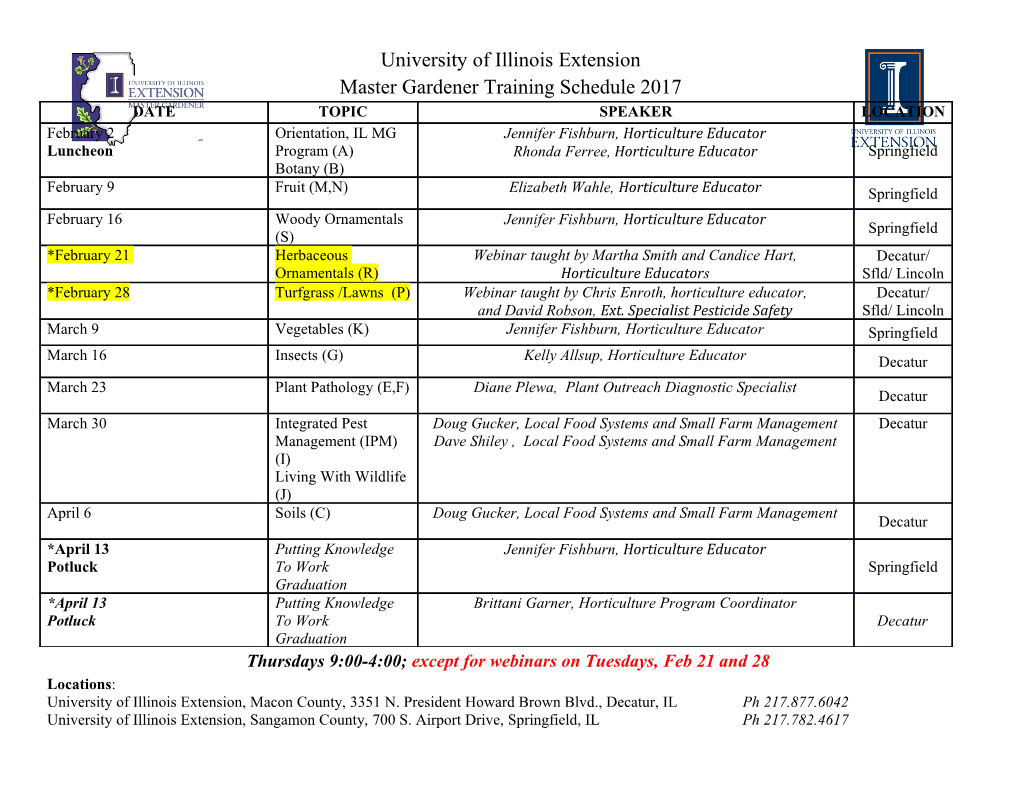
Challenge A: A more and more energy efficient railway The Merseyrail Energy Monitoring Project Edward Stewart, Paul Weston, Stuart Hillmansen and Clive Roberts The University of Birmingham, Birmingham, U. K. Abstract DC powered railway systems have significant losses in the power network. This paper presents results from a project that aims to measure simultaneously the power output from substations and power input to vehicles. Data have been recorded during initial instrumentation test runs on a vehicle and separately in two substations. It is possible to observe details in the current waveforms, such as notching currents, from the instrumentation located on board the train and at the substations. Further analysis of the data taken in one of the substations reveals the effects of different driving styles on the overall energy consumption. 1. Background Electric railway networks are either fed using high voltage AC or low voltage (750 to 1500 V) DC. Lower voltage DC systems often use line-side power conductors energised between 660 and 780 Volts nominal. Rolling stock deployed on these systems may take several thousand Amperes, and therefore minimising loop impedance of the power network is an effective way to limit the I2R losses. Generally, as the distance between a motoring train and a substation increases, so do the network losses. In addition, the line voltage and the touch potential of the return conductors may approach the acceptable upper limit at these locations. Whilst modelling of these systems is reasonably well established [1-3], there are few studies that report experimental results [4, 5]. This paper presents the results from an ongoing experimental study on a DC powered network. One train and two substations have been instrumented with custom made monitoring equipment. The intention is to analyse data recorded from train mounted equipment in conjunction with that recorded at substations. Using this combined information, it is possible to compute the instantaneous power flow, and therefore gain an insight into the losses in the system. To date, the systems have recorded data from both train and substations during the short-term initial instrumentation phases. 2. Experimental The energy metering systems used in this project have all been custom designed and built. Companies such as LEM who specialise in measuring electrical parameters also produce commercial energy metering systems. One example of these systems is the EM4T which is an energy meter designed specifically for railway traction systems. Systems such as these have been fitted to railway vehicles in the past. A report in the Railway Gazette International [6] describes a five month trial with energy metering equipment fitted to a vehicle in the Virgin Pendolino fleet (390049). The results from the trials were used to justify inclusion of the fleet in the reduced energy tariff associated with vehicles with regenerative braking capabilities [7]. These energy metering systems are designed in line with GM/RT2132, the UK railway group standard implementation of the European railway energy metering standard BS EN 50463, and the energy management systems standard, BS EN 16001. A second edition of GM/RT2453 (currently in draft) will update the mandatory data requirements for rolling stock to include energy metering data. These standards mandate energy results to be recorded every five minutes. This is adequate for billing and broad averaging purposes but does not provide the level of detail that is being sought in this study. Challenge A: A more and more energy efficient railway 2.1. Train mounted equipment The rolling stock instrumented was the British Rail Class 508, which is a camshaft controlled train. Each train comprises 3 cars. At each end there is a driving motor car which contains the traction control system and four series wound DC traction motors driving each axle. The driver’s commands are common to each end of the train, but the camshaft controller also uses input signals from the passenger weight transducer, a current sensor and the tacho signal, thus each of end of the train requires separate monitoring. The experimental equipment consisted of a suitable arrangement of current, voltage, and additional sensors, all interfaced to a number of instrumentation nodes connected to a CAN bus data network. Figure 1 is a plan view of a Class 508 vehicle showing the locations of the instrumentation. Class 508 plan view Digital I/O (Control & Cam Signals) Power Management (110 – 24 V) Data Logging Can / Fibre Optic Conversion GPS & Gyro IMU Tacho Laptop Data logging Power Measurement Figure 1: Plan view of instrumentation locations 2.1.1 Train-mounted instrumentation details The instrumentation was sited in 4 boxes duplicated at each end of the train. The instrumentation is spread over 7 sites and 16 PCBs. There are a total of 11 microcontrollers running 6 firmwares. A CAN bus is used to link the instrumentation nodes, and an optional fibre optic interface is provided for out-of-service data monitoring purposes. Data are stored in a custom format on solid state devices. Traction rated current and voltage sensors have been used for the main train circuit with an additional current sensor used for the auxiliary loads. Box A: This contains electronics for the energy monitoring components together with the main power conversion (from 110 V to 24 V) Box B: This contains the interface with the tacho test point signal and a data logger. Box C: This contains the driver’s demand and camshaft interface electronics. Box D: This contains the inertial measurement unit and a GPS receiver. Table 1 shows the sampling and data rates used by the monitoring equipment. Signal Sample Rate [Hz] Data Rate [Hz] Traction current 8192 256 Aux current 8192 256 Line voltage 8192 256 Driver’s demands 16 16 Camshaft position 16 16 Tacho 8 8 Challenge A: A more and more energy efficient railway Passenger weight 1024 1 Temperature 1024 1 Body inertial measurement 1024 16 Bogie inertial measurement 8192 256 GPS position and time 1 1 Traction energy 8192 1 Auxiliary energy 8192 1 Table 1: Data sampling rates 2.2 Substation equipment The substation equipment was contained in one box. Interfaces were provided to current sensors and the bus bar voltage sensors. Figure 2 shows the location of the instrumentation fitted in the substations at Hoylake and Meols. Each substation contained four feeder cables feeding the up and down lines, and a cross bonded return conductor. The instrumentation box was fitted with a GPS sensor that was used to provide a satellite time reference which can then be used for data synchronisation purposes. All current and voltage transducers were sampled at a rate of 256 Hz. Voltage Current GPS Also: Total return current at each substation Figure 2: Substation instrumentation 3. Initial results 3.1. Train measurements Data from one end of a three-car unit were collected on the 11th November 2009. The train was driven in between scheduled services, and a number of trials were carried out following a major overhaul. The route covered the line between Hoylake and Chester. Figure 3 shows the data for one driving vehicle recorded during a number of brake tests. The line voltage (around 780 V and below) drops as the train takes current. The magnitude of the voltage drop is dependent on both the loop impedance and the substation transformer regulation, hence from this data alone it is difficult to estimate the network losses with any degree of certainty. The current data (shown in blue) displays the classic series-parallel-weak field operation of these types of traction drives. The driver’s demands are also shown (in black). In driving position 2 the traction controller keeps the motors connected in series. Only in driving positions 3 and 4 are the motors allowed to switch from series to parallel operation. The speed of the train is shown in addition. Challenge A: A more and more energy efficient railway Traction Current / Voltage / Speed / Handle Position 1200 1000 800 600 400 200 Traction current [A] / Voltage [V]/ Voltage / [A] current Traction 100 x position / Handle [mph] x10 Speed 0 1500 1600 1700 1800 1900 2000 2100 Time [s] Figure 3: Initial data recorded during brake tests. Red line: line voltage. Blue line: traction current. Black line: driver's demand. Green line: vehicle speed. The operation of the camshaft was also recorded. These data are shown in Figure 4. The camshaft shift signal can be seen to correlate with the step changes in current which occur when a lower resistance is switched into the motor circuit. Traction Current / Handle Position / Camshaft Shift Signal 400 350 300 250 200 150 100 50 Traction current [A] / Handle position x 100 / x 100 position Handle / [A] current Traction shiftsignal Camshaft 0 1686 1688 1690 1692 1694 1696 1698 1700 1702 Time [s] Figure 4: Camshaft shift signal plotted together with the traction current for the driving vehicle Challenge A: A more and more energy efficient railway 3.2 Energy consumption from train measurements It is possible to compute the energy consumed (at the train) by the driving vehicle by integrating the product of the voltage and current. These data are plotted in Figure 5 for the journey from Chester to James Street (note that these data, as before, are for only one of the two driving vehicles). The data has also been processed to give summary outputs every five minutes. This represents the outputs from commercial energy metering systems. The figure also includes a speed profile for the vehicle. The figure shows the energy used by three different styles of acceleration. During the trials, the initial acceleration out of Chester consisted of a series of accelerations and braking stages at the maximum possible rate.
Details
-
File Typepdf
-
Upload Time-
-
Content LanguagesEnglish
-
Upload UserAnonymous/Not logged-in
-
File Pages14 Page
-
File Size-