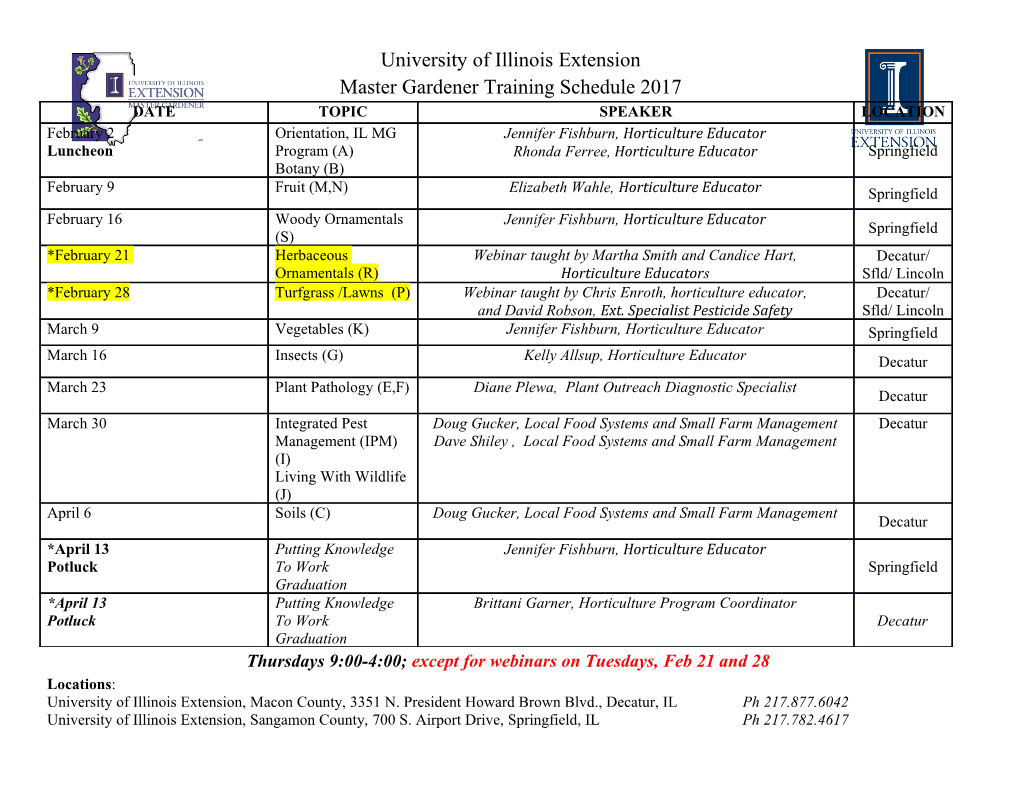
energies Article Full-Bridge Active-Clamp Forward-Flyback Converter with an Integrated Transformer for High-Performance and Low Cost Low-Voltage DC Converter of Vehicle Applications Jaeil Baek 1 and Han-Shin Youn 2,* 1 Department of Electrical Engineering, Princeton University, Princeton, NJ 08540, USA; [email protected] 2 Department of Electrical Engineering, Incheon National University, 119, Academy-ro, Yeonsu-gu, Incheon 406840, Korea * Correspondence: [email protected] Received: 14 January 2020; Accepted: 12 February 2020; Published: 16 February 2020 Abstract: This paper presents a full-bridge active-clamp forward-flyback (FBACFF) converter with an integrated transformer sharing a single primary winding. Compared to the conventional active-clamp-forward (ACF) converter, the proposed converter has low voltage stress on the primary switches due to its full-bridge active-clamp structure, which can leverage high performance Silicon- metal–oxide–semiconductor field-effect transistor (Si-MOSFET) of low voltage rating and low channel resistance. Integrating forward and flyback operations allows the proposed converter to have much lower primary root mean square (RMS) current than the conventional phase-shifted-full-bridge (PSFB) converter, while covering wide input/output voltage range with duty ratio over 0.5. The proposed integrated transformer reduces the transformer conduction loss and simplify the secondary structure of the proposed converter. As a result, the proposed converter has several advantages: (1) high heavy load efficiency, (2) wide input voltage range operation, (3) high power density with the integrated transformer, and (4) low cost. The proposed converter is a very promising candidate for applications with wide input voltage range and high power, such as the low-voltage DC (LDC) converter for eco-friendly vehicles. Keywords: active-clamp converter; DC-DC converter; eco-friendly vehicle; forward-flyback converter; high efficiency; high power density; integrated transformer; low-voltage DC converter; soft-switching 1. Introduction Nowadays, eco-friendly vehicles such as hybrid electric vehicle and electric vehicle have been researched and developed to satisfy the strengthened CO2 emission regulations as well as to increase fuel economy [1–3]. A lot of power conversion systems have been studied for eco-friendly vehicles. These power conversion systems require not only a high efficiency to improve the fuel economy but also a high power density because those are installed in the engine and trunk rooms of eco-friendly vehicles. Moreover, the price of eco-friendly vehicles is much higher than that of the traditional vehicles due to additional power conversion systems, i.e., drive motor, inverter, converters, and battery. Therefore, reducing the production cost is also one of the most important design considerations for eco-friendly vehicles. Furthermore, the power consumption caused by electronic devices of vehicles has been rapidly increased due to the remarkable improvement of information technology and development of electronic system such as advanced driver assistance system (ADAS), motor drive steering system (MDPS), traction control system (TCS), information devices, etc. [4]. Energies 2020, 13, 863; doi:10.3390/en13040863 www.mdpi.com/journal/energies Energies 2019, 12, x FOR PEER REVIEW 2 of 17 Energies 2020, 13, 863 2 of 17 Energies 2019, 12, x FOR PEER REVIEW 2 of 17 To supply power to electronic devices of vehicles, a LDC converter that charges low voltage (LV) battery (e.g., 13.6 V) with the energy stored in high voltage (HV) battery (e.g. 300 V) is commonly ToTo supply supply power power to to electronic electronic devices devices of of vehicles vehicles,, a a LDC LDC converter converter that that charges charges low low voltage voltage (LV) (LV) used in eco-friendly vehicles. The LV battery is usually controlled to maintain its nominal voltage. batterybattery (e.g., 13.613.6 V)V) withwith the the energy energy stored stored in in high high voltage voltage (HV) (HV) battery battery (e.g., (e.g. 300 300 V) is V) commonly is commonly used Namely, the LDC converter should be designed to cover wide input voltage range of the HV battery. usedin eco-friendly in eco-friendly vehicles. vehicles. The LV The battery LV battery is usually is usually controlled controlled to maintain to maintain its nominal its nominal voltage. voltage. Namely, Due to the increased power consumption of high-performance electronic devices (ADAS, MDPS, and Namely,the LDC the converter LDC converter should be should designed be designed to cover wide to cover input wide voltage input range voltage of the range HV of battery. the HV Due battery. to the so on) in vehicles, the discharging current of the LV battery has been increased. Accordingly, to Dueincreased to the powerincreased consumption power consumption of high-performance of high-performance electronic electronic devices (ADAS, devices MDPS, (ADAS, and MDPS, so on) and in maintain the LV battery in normal range, the nominal output current of the LDC converter, i.e., sovehicles, on) in thevehicles, discharging the discharging current of the current LV battery of the has LV been battery increased. has been Accordingly, increased. to Accordingly, maintain the LVto charging current of the LV battery, has been also continuously increased. As a result, it is getting maintainbattery in the normal LV battery range, in the normal nominal range, output the current nominal of theoutput LDC current converter, of the i.e., LDC charging converter, current i.e., of important for the LDC converter to achieve higher heavy load efficiency. Currently, plug-in hybrid chargingthe LV battery, current has of beenthe LV also battery, continuously has been increased. also continuously As a result, increased. it is getting As important a result, it for is the getting LDC importantconverterelectric vehicles tofor achieve the (PHEVs)LDC higher converter usually heavy to loadadopt achieve effi aciency. HV higher batte Currently, heavyry with load plug-in240–413 efficiency. hybrid V (nominal Currently, electric 360 vehicles plug-inV), and (PHEVs) hybridHEVs do electricusuallya HV batteryvehicles adopt awith HV(PHEVs) battery200–310 usually with V operating 240–413 adopt a V HVrange (nominal batte (nominry 360 with V),al 240–413270 and V). HEVs BothV (nominal do uses a HV approximatedbattery 360 V), with and 200–310HEVs 13.6 doV VLV aoperatingbattery. HV battery In range addition, with (nominal 200–310 the LDC 270V operating V).converter Both usesrange is designed approximated (nomin upal 270to 2kW 13.6V). Both Vmeaning LV uses battery. veryapproximated Inhigh addition, output 13.6 the current V LDC LV of battery.converter140–160 In A. isaddition, designed the up LDC to 2 converter kW meaning is designed very high up output to 2kW current meaning of 140–160 very high A. output current of 140–160InIn orderA.order to to achieve achieve high high e ffiefficiencyciency and and high high power power density density under under wide wide input input voltage voltage range range and and highhighIn outputoutput ordercurrent currentto achieve specifications, specifications, high efficiency the the conventional andconvention high poweral LDC LDC density converter converter under adopts adopts wide a phase-shiftedinputa phase-shifted voltage full-bridgerange full-bridge and high(PSFB)(PSFB) output converter converter current as as shownspecifications, shown in Figurein Figure the1 due convention 1 todue the to zero-voltage althe LDC zero-voltage converter switching adoptsswitching (ZVS) a phase-shifted characteristic (ZVS) characteristic full-bridge and twice and (PSFB)poweringtwice poweringconverter operation operationas inshown one switching in Figureone switching period 1 due ofto period the the PSFB zero-voltage of converterthe PSFB switching [converter5–9]. However, (ZVS) [5–9]. sincecharacteristic However, the operating since and the twicedutyoperating ratiopowering atduty the operationratio nominal at the inputin nominal one voltage switching input is farvoltage period small, is of thefar the PSFBsmall, PSFB converter the converter PSFB hasconverter [5–9]. large However, circulating has large since circulating current the operatingduringcurrent freewheeling during duty ratio freewheeling at periods the nominal periods as shown input as inshownvoltage Figure in is1 b,Figurefar which small, 1b, causesthe which PSFB significant causes converter significant high has large conduction high circulating conduction loss currentatloss heavy at duringheavy load condition.loadfreewheeling condition. Furthermore, periods Furthermore, as shown the PSFB the in Figure converterPSFB converter1b, which has large causeshas systemlarge significant system volume volumehigh because conduction because of two of lossmagnetictwo at magnetic heavy components load components condition. (transformer (transformerFurthermore, and output and the PSFBoutput inductor converter inductor shown has inshown Figurelarge in system2 b),Figure which volume 2b), must which because be firmlymust of be twofixedfirmly magnetic by fixed using by components additional using additional bulky (transformer devices, bulky anddevices, and large output and size largeinductor of snubber size shownofcircuits snubber in toFigure circuits constraint 2b), to constraintwhich voltage must stresses voltage be firmlyonstresses the fixed secondary on bythe using secondary diodes. additional As diodes. a result, bulky As the devices, a conventional result, and the large conventional
Details
-
File Typepdf
-
Upload Time-
-
Content LanguagesEnglish
-
Upload UserAnonymous/Not logged-in
-
File Pages17 Page
-
File Size-