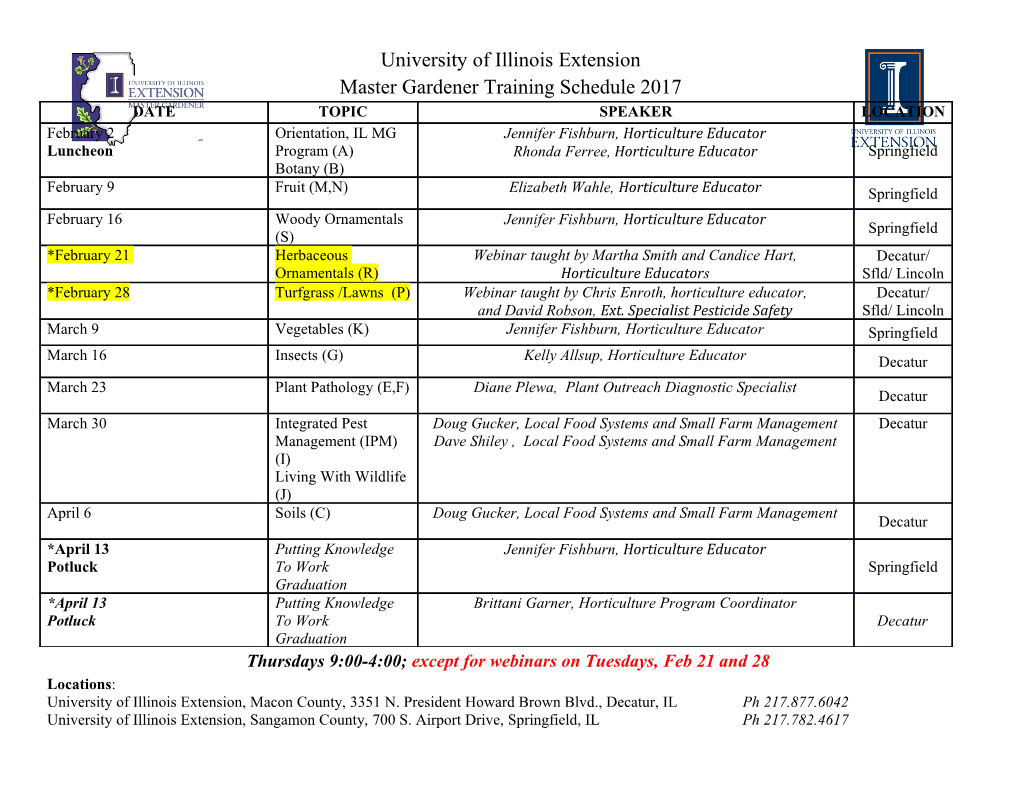
г, trials Science Forum S n?S5-5476, Vol 877, pp 485-491 •1:n4028/wmv.scientißc.net/MSF.877.485 doi7n 17 Trans Tech Publications, Switzerland Corrosion of Aluminum Aerospace Alloys J.T. Staley Element Materials Technology, 3200 South 166th Street, New Berlin, Wl 53151 [email protected] Keywords: aluminum, corrosion, aerospace, aloha, testing, mitigation. Abstract. The Junkers F13 airplane, which began production in 1919, was the first plane to be built using aluminum aerospace alloys. Nearly 100 years later, approximately 1,800 new planes are being ou:U each ycar with aluminum aerospace alloys. For the five trillion or so dollars worth of existing aging airplanes, cost of aerospace corrosion in United States alone is an estimated 23 billion dollars per war. hi addition, hidden corrosion costs have contributed to a bigger impact in the commercial aircraft industry. In 1988, in the corrosion sensitive environment of the Hawaiian islands, an Aloha Airlines 737 aircraft suffered an in-flight failure due to crevice corrosion in the lap joint of the fuselage. After this event, the aviation technical community launched a new era of advanced technology, improved procedures and higher standards for maintaining the world's aging and cuimding aircraft. This paper discusses types of corrosion that affect aluminum aerospace alloys including crevice corrosion, pitting, exfoliation, intergranular, stress corrosion cracking (SCC) and ..•orrosion fatigue. Standardized testing to determine if the alloy is susceptible to these types of corrosion is explained and examples of how to mitigate certain types of corrosion is discussed. Introduction Alfred Wilm studied metallurgy near Berlin and to support the German war effort, was commissioned to develop an aluminum alloy that could be used for the manufacture of ammunition. For two years he investigated the possible strengthening of Al-Cu alloys by heat treatment. Then, one day in 1906, he was experimenting with an Al-Cu-Mn-Mg alloy, which he quenched as usual and was surprised that the hardness increased for four days then remained constant giving way to a new alloy patent and by 1908 commercial production began at Durener Mct.ilwerke. Contractions of the words "Durener" and "aluminum" led to the name "Duralumin" 'Iii' t!u' new alloy, which is still recognized today. In fact, airships like the Hindenburg and the woild's first all-metal transport aircraft (the Junkers F13) was made from Duralumin. The plane was a technological success; it was able to travel long distances and carry heavy loads. However, duralumin had severe corrosion problems especially in salt spray. [1,2] In 1916, Alcoa produced a modification of duralumin, designated "17S", which is still in production l'xld\ as alloy 2017. Further Alcoa work resulted in alloys 14S (2014) and 24S (2024). Alloy 24S exhibited significantly higher strength (vs 2017) and better elongation (vs 2014-T6). It was used in tue T3 (naturally aged + cold-worked) temper and became the primary alloy for the Douglas DC3 airplane, which was introduced in the 1930's. Although these newly developed aluminum alloys had significantly better corrosion resistance than duralumin, they were still very susceptible to one or mure types of corrosion. In fact, a corrosion resistant aluminum aerospace alloy for all wrought forms •tnd directions has yet to be developed. Factors Influencing Corrosion Substances that cause corrosion of aluminum aerospace alloys are called corrosive agents. The most common corrosive agents are acids, alkalies, and salts. The atmosphere and water, the two most «>mmon media for these agents, may also act as corrosive agents. In general, moderately strong acids ^ill severely corrode most of the aluminum alloys used in airframes. Although alkalies, as a group, @#$%D1806040022YJ00*&^% 670 Aluminium Alloys 2016 - ICAA15 are generally not as corrosive as acids, aluminum is exceedingly prone to corrosive attack by many alkaline solutions unless the solutions contain a corrosion inhibitor. Particularly corrosive to aluminum are washing soda, potash (wood ashes), and lime (cement dust). Ammonia is an exception because aluminum alloys are highly resistant to it. Most salt solutions are good electrolytes and can promote corrosive attack of aluminum alloys. Exposure of airframe materials to salts or their solutions is extremely undesirable. Some factors that influence metal corrosion and the rate of corrosion are; type of metal, temper, grain direction, anode and cathode surface areas, temperature, humidity, presence of electrolytes, availability of oxygen, stress on the corroding metal and time of exposure to a corrosive environment. Aluminum Aerospace Alloys. In the aircraft industry, high-strength 2XXX and 7XXX series aluminum alloys (see Table 1 below) are commonly used for primary airframe structures (fuselage skins, stringers and frames, wing and empennage skins, spars and ribs), mechanical systems (landing gear legs, cylinders, forks and struts) and fluid systems (pressure vessels and connectors). Corrosion damage of the material is very essential to the structural integrity of the aircraft. Since the material of a component is subjected to corrosion, it is expected that its critical mechanical properties will vary with increasing service time, which must be taken into account for the structural integrity calculation of the component. The most widely used aluminum alloy in aerospace is the damage-tolerant Al 2024-T3 alloy. The location of the anodic path varies with the different alloy systems. In 2XXX series alloys, it is a narrow band on either side of the boundary that is depleted in copper; in copper-free 7XXX series alloys, it is generally considered to be the anodic zinc and magnesium bearing constituents on the grain boundary. 2XXX series aluminum alloys are especially sensitive to aqueous medium containing chloride ions (seawater) because such medium favor oxidation and pitting corrosion of these alloys. Because of the electrochemical nature of most corrosion processes, the solution potential relationships among the microstructural constituents of a particular alloy significantly affect its corrosion behavior. Solution potential is not affected significantly by second phase particles of microscopic size, but because these particles frequently have solution potentials differing from that of the solid solution matrix, localized galvanic cells may be formed between them and the matrix. Table 1. Composition of alloys 2024 3.8 - 4.9 1.2-1.8 0.25 0.30 - 6,90 0.50 , 0.50 2124 3,8-4.9 1,2-1.8 0.25 0.30-0,90 0,30 0,20 2026 3.6 - 4.3 1.0-1,6 0.10 0.30 - 0.80 0.0S-0.2S 0,07 0.05 2524 4.0 - 4,5 1,2-1.6 0.15 0,45 - 0,70 0.12 0.06 7075 1.2 - 2.0 2.1-2.9 5.1-6.1 0,30 0.18 - 0.28 0.50 0.40 7050 2.0 - 2.6 1.8 - 2.6 5,7 - 6.7 0.10 0.08 - 0.15 0.04 0.15 0.12 7150 1.9 - 2,5 2.0 - 2.7 5.9 - 6.9 0.10 0.08 - 0.15 0.04 0.15 0,12 7475 1.2-1.9 1,9 - 2.6 5.2 - 6,2 0.06 0,18*-0.25 0.12 0.10 2099 2,4 - 3.0 1.6 - 2.0 0.1-0.S 0.4-1.0 0.1-0.5 0,05 - 0.12 0.07 0.05 2199 2,3 - 2,8 1.4-1,8 0.05 - 0.40 0.2- 0.9 ОЛ-О.5 0.05-0.12 0.07 0.05 2050 3.2 - 3.9 0.70-1.3 0.20 - 0.60 0.20 - 0.50 0.06 - 0.14 0.20 - 0.70 0.10 0.08 2195 3.7 - 4.3 0.80-1.2 0.25 - 0.80 0,25 ' 0,08 - 0.16 0,25 - 0,60 0.15 0.12 Corrosion Types General. General corrosion consumes aluminum uniformly and affects a large area versus other more local types of aluminum aerospace alloy corrosion. It occurs at a relatively slow rate but left unattended over a long period, can remove enough metal to cause structural concerns. Aluminum exposed to marine, tropical and industrial atmospheres has the greatest rate of general corrosion. Pitting. Pitting corrosion is a localized form of attack where pits develop in aluminum causing localized perforation of the alloy. Pitting corrosion is confined to a point or small area that takes the @#$%D1806040022YJ00*&^% 669 Materials Science Forum Vol. 877 form of cavities. One area of the surface becomes anodic with respect to the rest of the surface. The its formed by this type of attack are generally very small and difficult to detect during routine inspection. ('ré*ice- Crevice corrosion occurs when localized changes in the corrosive environment exist and lead to accelerated localized attack. These changes are generated by the existence" of narrow crevices that contain a stagnant environment, which results in a difference in concentration of the cathode reactant between the crevice region and the external surface of the material. Crevices can be formed at joints between two materials, e.g. riveted or glued sections of an aircraft fuselage. G;il\:inic. Galvanic corrosion occurs when dissimilar metals are in direct electrical contact in a corrosive environment. This results in enhanced and aggressive corrosion of the less noble metal and protection of the more noble metal of the bimetallic couple. This type of corrosion can be recognized b\ severe corrosion near the junction of the two dissimilar metals, while the remaining surfaces are relatively corrosion-product free. The driving force for galvanic corrosion is a potential difference between the different materials. Stress Corrosion Cracking (SCC). Stress Corrosion Cracking is attributed primarily to the copper content.
Details
-
File Typepdf
-
Upload Time-
-
Content LanguagesEnglish
-
Upload UserAnonymous/Not logged-in
-
File Pages7 Page
-
File Size-