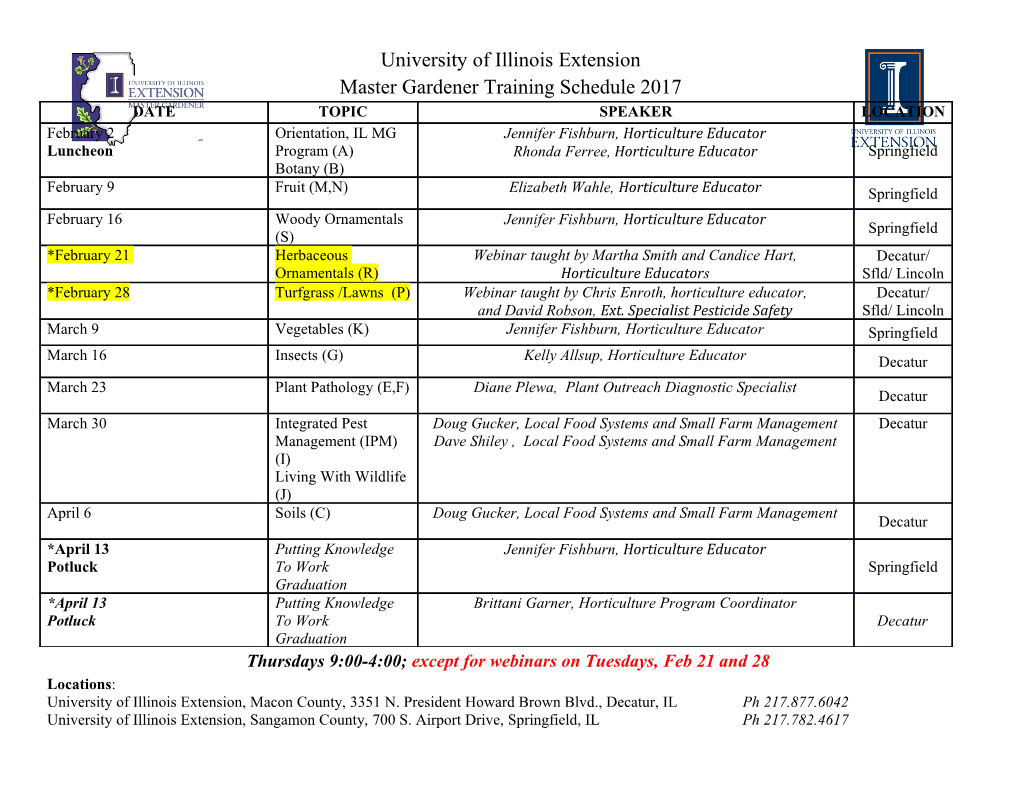
American Journal of Applied Sciences 2 (10): 1438-1444, 2005 ISSN 1546-9239 © 2005 Science Publications Modeling of Transient Heat Flux in Spark Ignition EngineDuring Combustion and Comparisons with Experiment Yusaf T.F., Sye Hoe, Fong, Yusoff M.Z. and Hussein I. Universiti Tenaga Nasional, Department of Mechanical Engineering, Km 7, Jalan Kajang-Puchong Kajang, Selangor 43009, Malaysia Abstract: A quasi-one dimensional engine cycle simulation program was developed to predict the transient heat flux during combustion in a spark ignition engine. A two-zone heat release model was utilized to model the combustion process inside the combustion chamber. The fuel, air and burned gas properties throughout the engine cycle were calculated using variable specific heats. The transient heat flux inside the combustion chamber due to the change in the in-cylinder gas temperature and pressure during combustion was determined using the Woschni heat transfer model. The program was written in MATLAB together with the Graphical User Interface (GUI). Numerical results were compared with the experimental measurements and good agreement was obtained. Four thermocouples were used and positioned equi-spaced at 5mm intervals along a ray from the spark plug location on the engine head. These thermocouples were able to capture the heat flux release by the burned gas to the wall during the combustion process including the cycle-to-cycle variations. Pressure sensor was installed at the engine head to capture the pressure change throughout the cycle. Key words: Internal combustion engine, Woschni, spark ignition engine, heat flux, mathematical model INTRODUCTION for both burned and unburned gases were expressed as functions of temperatures as follows: Heat transfer between the working fluid and the & (2) Qb = hAb (Tb − Tw ) combustion chamber in the internal combustion engine Q& = hA (T − T ) (3) is one of the most important parameter for cycle u u u w Where, and are the areas of the burned and simulation and analysis. Heat transfer influences the in- Ab Au cylinder pressure and temperature levels, engine unburned gas in contact with the cylinder walls at efficiency and exhaust emissions. During the temperature . The wall temperature is assumed to be Tw combustion process, the peak gas temperature was 450K which is maximum allowable limit for the limited to 2500K as metal components of the lubricant oil to work under a proper condition before it combustion chamber can only withstand 600K for cast oxidize due to overheat. The cylinder area inside the iron and 500K for aluminium alloys. Therefore, the combustion chamber is: cooling of the cylinder head, block and piston is very πb2 4V important to keep the engine running in optimum 1/ 2 (4) Ab = + x condition. The engine lubricant will oxidize if the 2 b temperature reaches more than 450K. Thus, Likewise for unburned gas investigating the transient heat flux in the cylinder is πb2 4V A = + 1− x1 / 2 (5) very significant. The quasi one dimensional model was u 2 b acceptable since the temperature gradient normal to the wall is large compared with the temperature gradients Equation (4) and (5) are empirical functions that along the wall[1]. have the correct limits in the case of a cylinder where and when . The x value represents the mass x → 0 x →1 fraction of cylinder content and burned gas is always Numerical analysis: In order to determine the transient assumed to occupy this larger fraction of the cylinder as heat flux inside the combustion chamber during the compared to unburned gas, due to the density difference combustion process, the heat transfer need to be defined [2] between burned and unburned gas. The burned gas as a function of θ as shown in the following equation : always occupies larger volume fraction of the cylinder. dQ − Q& − Q& − Q& = l = b u (1) Equation (2) and (3) represent the remaining parameter, dθ ω ω that required to determine the heat transfer coefficients. The combustion gases are defined into two zones In the present work, the heat transfer coefficients are which are unburned gas zone and burned gas zone evaluated using Woschni heat transfer model[3]. where & and & are the heat transfer rates for the Qb Qu −0.2 0.8 0.8 −0.55 (6) burned and unburned gas respectively. The heat fluxes hc = 3.26B p w T Corresponding Author: Yusaf T. F., Universiti Tenaga Nasional, Department of Mechanical Engineering, Km 7, Jalan Kajang-Puchong, Kajang, Selangor 43009, Malaysia 1438 Am. J. Applied Sci., 2 (10):1438-1444, 2005 Where: temperature combustion modelling. The internal b = bore energy, enthalpy and specific heats are function of p = pressure pressure and temperature. On the other hand, in the T = temperature burned routine, ten combustion species were tracked w =average cylinder gas velocity during the combustion process using chemical equilibrium combustion model. Both of these routines The average gas velocity is always assumed to be return partial derivatives in logarithmic form, which are required in the subsequent calculations. The specific proportional to the mean piston speed during the intake, [2] compression and exhaust stroke. However, during the internal energy of the system is given U (10) combustion process, the gas velocity is a function of u = = xub + ()1− x uu density due to temperature and pressure rise. Thus, the m average gas velocity is Since there are two combustion zones inside the cylinder, x represents the mass fraction of the burned V T w = C S + C d r ()P − P (7) gas, is the internal energy of the burned gas at 1 p 2 m ub PrVr temperature T and u is the internal energy of the Where: b u = piston displacement unburned gas at temperatureT . The internal energy of Vd u S = mean piston speed the burned gas is function of both temperature and p pressure. = reference temperature Tr (11) ub = ub (Tb , P) p ,V = pressure and volume at initial condition r r and the derivatives will be = motored pressure pm du ∂u dT ∂u dP b = b b + b (12) C1 = 2.28, C2 = 0.0 during the compression stroke dθ ∂Tb dθ ∂P dθ C = 2.28, C = 0.00324 during the combustion and by substituting the logarithmic form of partial 1 2 [2] expansion stroke derivatives return by the burned routine du Pv ∂lnv dT ∂lnv ∂lnv dP b b b b b b (13) = cPb − − vb + In order to determine the average gas velocity, the dθ Tb ∂lnTb dθ ∂lnTb ∂ln P dθ pressure and temperature histories throughout the cycle and for the unburned gases are required. Both of these parameters are functions of duu Pvu ∂lnvu dTu ∂lnvu ∂lnvu dP (14) thermodynamic properties. Based on the first law of = cPu − − vu + [2] dθ T ∂lnT dθ ∂lnT ∂ln P dθ thermodynamics , u u u ∆U = Q −W (8) Equation (10) can be expressed in derivatives form as Where, the change of internal energy of any system follows, is equal to the difference between the heat transfer and du dub duu dx (15) m = x + ()1− x + ()ub − uu m work generated by the system. The above equation can dθ dθ dθ dθ be expressed in differential form and when applied to a Substituting equations (13) and (14) into equation (15), control volume encasing the cylinder content, the du PvvdTbbb∂ln mmxc= Pb −+ equation becomes: dTTdθ bb∂ln θ (16) du dm dQ dV m&1h1 Pv∂ ln v dT m + u = − P − (9) uuu mxc()1−−Pu dθ dθ dθ dθ ω TTduu∂ ln θ Where: ∂ln vb ∂ lnvb ∂ln vu ∂ ln vu dP − mxvb + + m()1− x vu + m&1 = mass flow rate ∂lnTb ∂ln P ∂lnTu ∂ln P dθ = enthalpy of the blowby masses h1 dx + m()u − u u = internal energy b u dθ Q = heat transfer This equation defined the first term on the left hand side p = pressure of equation (9). V = volume Specific volume: The specific volume of the system = crank angle θ can be expressed in a similar manner as the specific = engine speed [2] ω internal energy U (17) Thermodynamic properties v = = xvb + ()1− x vu m Specific internal energy: Since the thermodynamic and the function form will be properties change with respect to temperature and v = v T , P (18) pressure, two MATLAB subroutines were programmed b b ( b ) to return the thermodynamic properties throughout the The derivatives is dv ∂v dT ∂v dP engine cycle. The unburned routine was used to b = b b + b (19) calculate the fuel-air-residual gas mixture using low dθ ∂Tb dθ ∂P dθ 1439 Am. J. Applied Sci., 2 (10):1438-1444, 2005 by substituting the logarithmic form partial derivatives specific heat calculation and the specific heat is return by the burned routine assumed to follow a polynomial equation as follows[3]: dv v ∂ ln v dT v ∂ ln v dP C b b b b b b (20) p 2 3 4 (30) = + =a1+a2T + a3T + a4T + a5T dθ Tb ∂ lnTb dθ P ∂ ln P dθ R and for the unburned gas Where, R is the gas constant and a is the curve dvu vu ∂lnvu dTu vu ∂lnvu dP (21) fitted polynomials coefficients. Thus, since ∂h , = + = C p dθ Tu ∂ lnTu dθ P ∂ ln P dθ ∂T p Likewise, equation (17) becomes by varying the constant specific heat throughout the 1 dV V dm dv dv dx cycle, the enthalpy will change accordingly. − = x b + ()1− x u + ()v − v (22) m dθ m 2 dθ dθ dθ b u dθ Substituting equations (20) and (21) into equation (22) Mass blowby pass rings: The rate of change of mass yields with respect to crank angle is represented in equation 1 dV VC v ∂ lnv dT v ∂ lnv dT (9).
Details
-
File Typepdf
-
Upload Time-
-
Content LanguagesEnglish
-
Upload UserAnonymous/Not logged-in
-
File Pages7 Page
-
File Size-