Mi-38 with Russian TV7-117V Engines Makes First Flight
Total Page:16
File Type:pdf, Size:1020Kb
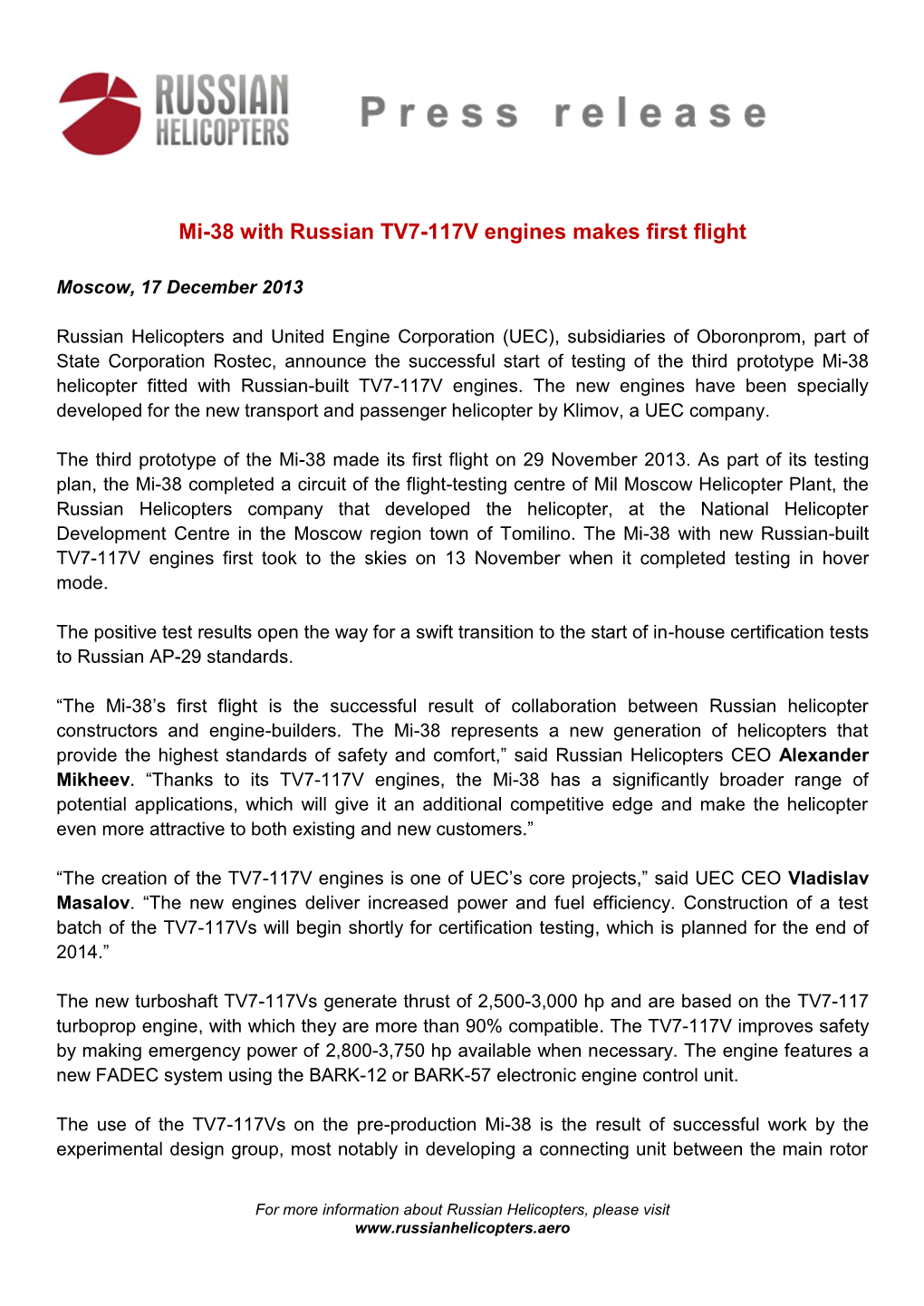
Load more
Recommended publications
-
Conceptual Design and Structural Analysis of Ground Support Equipment for Handling and Maintenance of Turboshaft Engines•
Conceptual design and structural analysis of ground support equipment for handling and maintenance of Turboshaft engines• Iván Felipe Rodríguez-Barón a, Jaime Enrique Orduy-Rodríguez a, Brayan Alejandro Rosas-Bonilla b, Jhon b b Sebastián Merchán-Camelo & Edison Jair Bejarano-Sepúlveda a Programa de Ingeniería Aeronáutica, Fundación Universitaria los Libertadores, Bogotá, Colombia: Instituto Nacional de Pesquisas Espaciais, São José dos Campos, Brasil. [email protected], [email protected] b Programa de Ingeniería Aeronáutica, Fundación Universitaria los Libertadores, Bogotá, Colombia [email protected], [email protected], [email protected] Received: November 17th, 2020. Received in revised form: March 3rd, 2021. Accepted: April 6th, 2021. Abstract This paper describes the application of computational modeling and computer-aided design (CAD) for the conceptual design and structural analysis of the maintenance process of Klimov TV3-117 engines at an approved Maintenance, Repair and Overhaul (MRO) facility in Colombia. The main issue is that these engines are difficult to roll and manipulate due to their weight, which ranges between 250 and 350 kg, which causes time and cost overruns for the operator, and delays in the scheduled maintenance times. The solution proposed by this study is the conceptualization and structural feasibility of a prototype of ground support equipment for handling and maintenance of Turboshaft engines, implementation of which could save up to 100 person-hours, which translates into about USD 10,000, since the current process requires four specialists and two inspectors, whereas the modified process would only require one of each. Keywords: Computer-Aided Design (CAD); structural analysis; turboshaft engines; ground support equipment; aeronautical maintenance. -
Comparison of Helicopter Turboshaft Engines
Comparison of Helicopter Turboshaft Engines John Schenderlein1, and Tyler Clayton2 University of Colorado, Boulder, CO, 80304 Although they garnish less attention than their flashy jet cousins, turboshaft engines hold a specialized niche in the aviation industry. Built to be compact, efficient, and powerful, turboshafts have made modern helicopters and the feats they accomplish possible. First implemented in the 1950s, turboshaft geometry has gone largely unchanged, but advances in materials and axial flow technology have continued to drive higher power and efficiency from today's turboshafts. Similarly to the turbojet and fan industry, there are only a handful of big players in the market. The usual suspects - Pratt & Whitney, General Electric, and Rolls-Royce - have taken over most of the industry, but lesser known companies like Lycoming and Turbomeca still hold a footing in the Turboshaft world. Nomenclature shp = Shaft Horsepower SFC = Specific Fuel Consumption FPT = Free Power Turbine HPT = High Power Turbine Introduction & Background Turboshaft engines are very similar to a turboprop engine; in fact many turboshaft engines were created by modifying existing turboprop engines to fit the needs of the rotorcraft they propel. The most common use of turboshaft engines is in scenarios where high power and reliability are required within a small envelope of requirements for size and weight. Most helicopter, marine, and auxiliary power units applications take advantage of turboshaft configurations. In fact, the turboshaft plays a workhorse role in the aviation industry as much as it is does for industrial power generation. While conventional turbine jet propulsion is achieved through thrust generated by a hot and fast exhaust stream, turboshaft engines creates shaft power that drives one or more rotors on the vehicle. -
The Power for Flight: NASA's Contributions To
The Power Power The forFlight NASA’s Contributions to Aircraft Propulsion for for Flight Jeremy R. Kinney ThePower for NASA’s Contributions to Aircraft Propulsion Flight Jeremy R. Kinney Library of Congress Cataloging-in-Publication Data Names: Kinney, Jeremy R., author. Title: The power for flight : NASA’s contributions to aircraft propulsion / Jeremy R. Kinney. Description: Washington, DC : National Aeronautics and Space Administration, [2017] | Includes bibliographical references and index. Identifiers: LCCN 2017027182 (print) | LCCN 2017028761 (ebook) | ISBN 9781626830387 (Epub) | ISBN 9781626830370 (hardcover) ) | ISBN 9781626830394 (softcover) Subjects: LCSH: United States. National Aeronautics and Space Administration– Research–History. | Airplanes–Jet propulsion–Research–United States– History. | Airplanes–Motors–Research–United States–History. Classification: LCC TL521.312 (ebook) | LCC TL521.312 .K47 2017 (print) | DDC 629.134/35072073–dc23 LC record available at https://lccn.loc.gov/2017027182 Copyright © 2017 by the National Aeronautics and Space Administration. The opinions expressed in this volume are those of the authors and do not necessarily reflect the official positions of the United States Government or of the National Aeronautics and Space Administration. This publication is available as a free download at http://www.nasa.gov/ebooks National Aeronautics and Space Administration Washington, DC Table of Contents Dedication v Acknowledgments vi Foreword vii Chapter 1: The NACA and Aircraft Propulsion, 1915–1958.................................1 Chapter 2: NASA Gets to Work, 1958–1975 ..................................................... 49 Chapter 3: The Shift Toward Commercial Aviation, 1966–1975 ...................... 73 Chapter 4: The Quest for Propulsive Efficiency, 1976–1989 ......................... 103 Chapter 5: Propulsion Control Enters the Computer Era, 1976–1998 ........... 139 Chapter 6: Transiting to a New Century, 1990–2008 .................................... -
POLITECNICO DI MILANO Thermodynamic Analysis of A
POLITECNICO DI MILANO School of Industrial and Information Engineering Department of Aerospace Science and Technology Master of Science in Aeronautical Engineering Thermodynamic analysis of a turboprop engine with regeneration and intercooling Advisor: Prof. Roberto ANDRIANI M.Sc. Dissertation of: Rasheed Michael ISHOLA Matr. 895396 April 2020 Academic Year 2019-2020 Contents Introduction 1 1 Turbopropeller engines overview 2 1.1 Turbopropeller characteristics . .4 1.2 Comparison with turbojets and piston-powered engines . .4 1.3 Turbopropeller-powered aircrafts . .5 1.4 Turbopropeller manufacturers . .9 1.4.1 Pratt & Whitney Canada (PWC) [1] . .9 1.4.2 Rolls-Royce [2] . 17 1.4.3 General Electric Aviation [3] . 22 1.4.4 JSC Kuznetsov [4] . 26 1.4.5 JSC \UEC-Klimov" [5] . 27 1.4.6 Ivchenko-Progress ZMKB [6] . 28 1.4.7 Honeywell Aerospace [7] . 33 1.4.8 PBS Aerospace [8] . 34 2 Thermodynamics of a turbopropeller engine with heat exchange 36 2.1 Intercooling and regeneration . 36 2.2 Thermodynamic cycle . 39 2.2.1 Assumptions . 39 2.2.2 The cycle . 42 2.3 Performances . 48 3 The code 53 3.1 Assumptions and data used . 54 3.1.1 Efficiencies and pressure losses . 54 3.1.2 Fuel properties . 54 3.1.3 Specific heat values . 55 3.2 Code Structure . 57 3.2.1 Input file . 57 3.2.2 Output files . 58 3.2.3 Code details . 62 4 Numerical simulation 78 4.1 Results . 78 4.1.1 Determination of the best βn condition . 79 4.1.2 Performances vs βc .......................... -
Pzl-10 Turboshaft Engine – System Design Review
Journal of KONES Powertrain and Transport, Vol. 26, No. 1 2019 ISSN: 1231-4005 e-ISSN: 2354-0133 DOI: 10.2478/kones-2019-0003 PZL-10 TURBOSHAFT ENGINE – SYSTEM DESIGN REVIEW Michal Czarnecki Rzeszow University of Technology, Department of Aircraft and Aircraft Engines Powstancow Warszawy Av. 8, 35-959 Rzeszow, Poland tel.: +48 17 8651609, fax: +48 17 8543116 e-mail: [email protected] John Olsen School of Mechanical and Manufacturing Engineering The University of New South Wales, Sydney, Ainsworth Building, N.S.W. 2052, Sydney, Australia tel.: +61 2 9385 5217, fax: +61 2 9663 1222 e-mail: [email protected] Ruixian Ma School of Energy Science and Engineering Harbin Institute of Technology Harbin, 150001, Heilongjiang, China e-mail: [email protected] Abstract The PZL – 10-turboshaft gas turbine engine is straight derivative of GTD-10 turboshaft design by OKMB (Omsk Engine Design Bureau). Prototype engine first run take place in 1968. Selected engine is interested platform to modify due gas generator layout 6A+R-2, which is modern. For example axial compressor design from successful Klimov designs TB2-117 (10A-2-2) or TB3-117 (12A-2-2) become obsolete in favour to TB7-117B (5A+R-2-2). In comparison to competitive engines: Klimov TB3-117 (1974 – Mi-14/17/24), General Electric T-700 (1970 – UH60/AH64), Turbomeca Makila (1976 – H225M) the PZL-10 engine design is limited by asymmetric power turbine design layout. This layout is common to early turboshaft design such as Soloview D-25V (Mil-6 power plant). Presented article review base engine configuration (6A+R+2+1). -
Russian Military Capability in a Ten-Year Perspective 2016
The Russian Armed Forces are developing from a force primarily designed for handling internal – 2016 Perspective Ten-Year in a Capability Military Russian disorder and conflicts in the area of the former Soviet Union towards a structure configured for large-scale operations also beyond that area. The Armed Forces can defend Russia from foreign aggression in 2016 better than they could in 2013. They are also a stronger instrument of coercion than before. This report analyses Russian military capability in a ten-year perspective. It is the eighth edition. A change in this report compared with the previous edition is that a basic assumption has been altered. In 2013, we assessed fighting power under the assumption that Russia was responding to an emerging threat with little or no time to prepare operations. In view of recent events, we now estimate available assets for military operations in situations when Russia initiates the use of armed force. The fighting power of the Russian Armed Forces is studied. Fighting power means the available military assets for three overall missions: operational-strategic joint inter-service combat operations (JISCOs), stand-off warfare and strategic deterrence. The potential order of battle is estimated for these three missions, i.e. what military forces Russia is able to generate and deploy in 2016. The fighting power of Russia’s Armed Forces has continued to increase – primarily west of the Urals. Russian military strategic theorists are devoting much thought not only to military force, but also to all kinds of other – non-military – means. The trend in security policy continues to be based on anti- Americanism, patriotism and authoritarianism at home. -
Etu – V Tulpar
2017-2018 Undergraduate Team Engine Candidate Engines for a Next Generation Supersonic Transport ETU – V TULPAR TEAM MEMBERS Veli Can ÜSTÜNDAĞ - 921399 Çağdaş Cem ERGİN - 920976 Baran İPER - 921398 Onur TAN - 921395 Faculty Advisor Asst. Prof. Sıtkı USLU SIGNATURES Faculty Advisor Asst. Prof. Sıtkı USLU TOBB University of Economics and Technology Team Leader Cagdas Cem ERGIN TOBB University of Economics and Technology Deparment of Mechanical Engineering AIAA Member Number: 920976 Team Member Veli Can USTUNDAG TOBB University of Economics and Technology Deparment of Mechanical Engineering AIAA Member Number: 921399 Team Member Baran IPER TOBB University of Economics and Technology Deparment of Mechanical Engineering AIAA Member Number: 921398 Team Member Onur TAN TOBB University of Economics and Technology Deparment of Mechanical Engineering AIAA Member Number: 921395 ii TABLE OF CONTENT LIST OF TABLES .................................................................................................................................................. v LIST OF FIGURES ............................................................................................................................................... vi NOMENCLATURE ............................................................................................................................................... ix 1. INTRODUCTION .......................................................................................................................................... 1 2. STATE OF THE -
By the Supervisory Board of Rostec Corporation (Minutes from ______2015, No
APPROVED 2014 Annual Report by the Supervisory Board of Rostec Corporation (Minutes from _________2015, No. __ ) of Rostec Corporation Rostec: A company of highly qualified, world-class professionals. In supporting the advancement of Russian industry, Rostec brings together the best Rostec Corporation traditions of Russian engineering, the latest technological innovations, and its significant expertise in the strategic development of mechanical engineering. Rostec Corporation is successfully restoring the relationship between science and industry by developing advanced technologies, introducing advanced know-how, and promoting effective cooperation between Russian industrial enterprises. Rostec’s experienced and highly qualified specialists enable the creation of unique products, opening new export opportunities for Russia. ANNUAL REPORT Rostec Corporation’s global objective is securing for Russia a leading position in high technology and mechanical engineering. for 2014 2014 Annual Report CEO CHIEF ACCOUNTANT OF ROSTEC CORPORATION OF ROSTEC CORPORATION of Rostec Corporation S.V. CHEMEZOV N.V. BORISOVA 2015 2015 4 ROSTEC CORPORATION Annual Report // 2014 5 Table of Contents Introductory notes from D. V. Manturov, Chairman of the Supervisory 5. Rostec production 6 Board, and S. V. Chemezov, CEO 108 5.1. Rostec contributions to Russian industry 5.2. New products and technologies 5.3. Import substitution 5.4. Military-technical cooperation, state orders, and federal target programs 5.5. Product optimization and restructuring 1. General information about Rostec corporation 5.6. Conversion of federal state unitary enterprises into joint-stock companies 10 1.1. History of Rostec 5.7. Management and production informatization 1.2. Supervisory board 5.8. Creating a single corporate treasury for Rostec organizations 1.3. -
A Design Study of Single-Rotor Turbomachinery Cycles
A Design Study of Single-Rotor Turbomachinery Cycles by Manoharan Thiagarajan A thesis submitted to the faculty of the Virginia Polytechnic Institute and State University in partial fulfillment of the requirements for the degree of Master of Science in Mechanical Engineering Committee Dr. Peter King, Chairman Dr. Walter O’Brien, Committee Member Dr. Clint Dancey, Committee Member August 12, 2004 Blacksburg, Virginia Keywords: Auxiliary power unit, single radial rotor, specific power takeoff, compressor, burner, turbine A Design Study of Single-Rotor Turbomachinery Cycles by Manoharan Thiagarajan Dr. Peter King, Chairman Dr. Walter O’Brien, Committee Member Dr. Clint Dancey, Committee Member (ABSTRACT) Gas turbine engines provide thrust for aircraft engines and supply shaft power for various applications. They consist of three main components. That is, a compressor followed by a combustion chamber (burner) and a turbine. Both turbine and compressor components are either axial or centrifugal (radial) in design. The combustion chamber is stationary on the engine casing. The type of engine that is of interest here is the gas turbine auxiliary power unit (APU). A typical APU has a centrifugal compressor, burner and an axial turbine. APUs generate mechanical shaft power to drive equipments such as small generators and hydraulic pumps. In airplanes, they provide cabin pressurization and ventilation. They can also supply electrical power to certain airplane systems such as navigation. In comparison to thrust engines, APUs are usually much smaller in design. The purpose of this research was to investigate the possibility of combining the three components of an APU into a single centrifugal rotor. To do this, a set of equations were chosen that would describe the new turbomachinery cycle. -
A New Direction for China's Defense Industry
THE ARTS This PDF document was made available CHILD POLICY from www.rand.org as a public service of CIVIL JUSTICE the RAND Corporation. EDUCATION ENERGY AND ENVIRONMENT Jump down to document6 HEALTH AND HEALTH CARE INTERNATIONAL AFFAIRS The RAND Corporation is a nonprofit NATIONAL SECURITY research organization providing POPULATION AND AGING PUBLIC SAFETY objective analysis and effective SCIENCE AND TECHNOLOGY solutions that address the challenges SUBSTANCE ABUSE facing the public and private sectors TERRORISM AND HOMELAND SECURITY around the world. TRANSPORTATION AND INFRASTRUCTURE WORKFORCE AND WORKPLACE Support RAND Purchase this document Browse Books & Publications Make a charitable contribution For More Information Visit RAND at www.rand.org Explore RAND Project AIR FORCE View document details Limited Electronic Distribution Rights This document and trademark(s) contained herein are protected by law as indicated in a notice appearing later in this work. This electronic representation of RAND intellectual property is provided for non- commercial use only. Permission is required from RAND to reproduce, or reuse in another form, any of our research documents. This product is part of the RAND Corporation monograph series. RAND monographs present major research findings that address the challenges facing the public and private sectors. All RAND mono- graphs undergo rigorous peer review to ensure high standards for research quality and objectivity. A New Direction for China's Defense Industry Evan S. Medeiros Roger Cliff Keith Crane James C. Mulvenon Prepared for the United States Air Force Approved for public release; distribution unlimited The research described in this report was sponsored by the United States Air Force under Contract F49642-01-C-0003. -
Power Sources of Military Helicopters Béla VARGA1
Vol. 17, No. 2 (2018) 139–168. Power Sources of Military Helicopters Béla VARGA1 In the early 1940s the first practically usable helicopters rose into the sky. Their importance was quickly recognised both by the military and civilian decision makers. A good summary of their most important advantage is the next quotation: “If you are in trouble anywhere in the world, an airplane can fly over and drop flowers, but a helicopter can land and save your life.” (Igor Sikorsky, 1947) Just after their appearance it immediately became an urgent problem to replace the relatively low-power and heavy piston engines, for which the much lighter and more powerful turboshaft engines offered a good alternative. Significant improvement of helicopter engines, which has embodied mainly in power to weight ratio, thermal cycle efficiency, specific fuel consumption, together with reliability and maintainability, of course, has influenced the technical- tactical parameters of helicopters. In this paper I introduce the evolution of helicopter turboshaft engines, the most important manufacturers and engine types. Through statistical analysis I display what kind of performance parameters the helicopter turboshaft engines had in the past and have in the present days. Keywords: helicopter gas turbine engines, turboshaft, shaft power, specific fuel consumption, thermal efficiency, specific net work output, specific power The Beginning of the Gas Turbine Era By the end of World War II, piston engine and propeller driven aircraft reached their performance limits. This meant their flying speed slightly exceeded 700 km/h. The flight altitude of an average fighter reached 12 km, the special reconnaissance planes could even reach 14 to 15 km. -
Turbofan Aero-Engine Efficiency Evaluation: an Integrated Approach Using VSBM Two-Stage Network DEA
Turbofan Aero-Engine Efficiency Evaluation: An Integrated Approach Using VSBM Two-Stage Network DEA Angelos T. Kottas1, Michail N. Bozoudis2 Michael A. Madas3* 1 Aristotle University of Thessaloniki, School of Economic Sciences, MSc Programme in Logistics and Supply Chain Management University Campus, 54124, Thessaloniki, Greece [email protected] 2 NATO Communications and Information Agency (NCIA) Boulevard Leopold III, 1110 Brussels, Belgium [email protected] 3 University of Macedonia, Department of Applied Informatics Information Systems and e-Business Laboratory (ISeB) 156, Egnatia Str., 54636, Thessaloniki, Greece [email protected] *Corresponding author Abstract The application of Data Envelopment Analysis (DEA) has been wide, especially for the purpose of evaluating efficiency among similar production processes within enterprises belonging to particular industries. Although research pertinent to DEA has primarily focused on efficiency of production systems or corporate entities/organizations (e.g., terminals, hospitals, universities/schools, banks), fairly little attention has been given to efficiency evaluation among engineering systems featuring common configurations (e.g., automobiles, power plants). Furthermore, the limited previous literature involving efficiency evaluation of engineering systems has implemented DEA methodologies with limited discriminatory power, i.e. there is a quite increased portion of efficient Decision Making Units (DMUs). In the current paper, a methodological framework deploying Variable