Geotechnical Aspects of Container Port Development
Total Page:16
File Type:pdf, Size:1020Kb
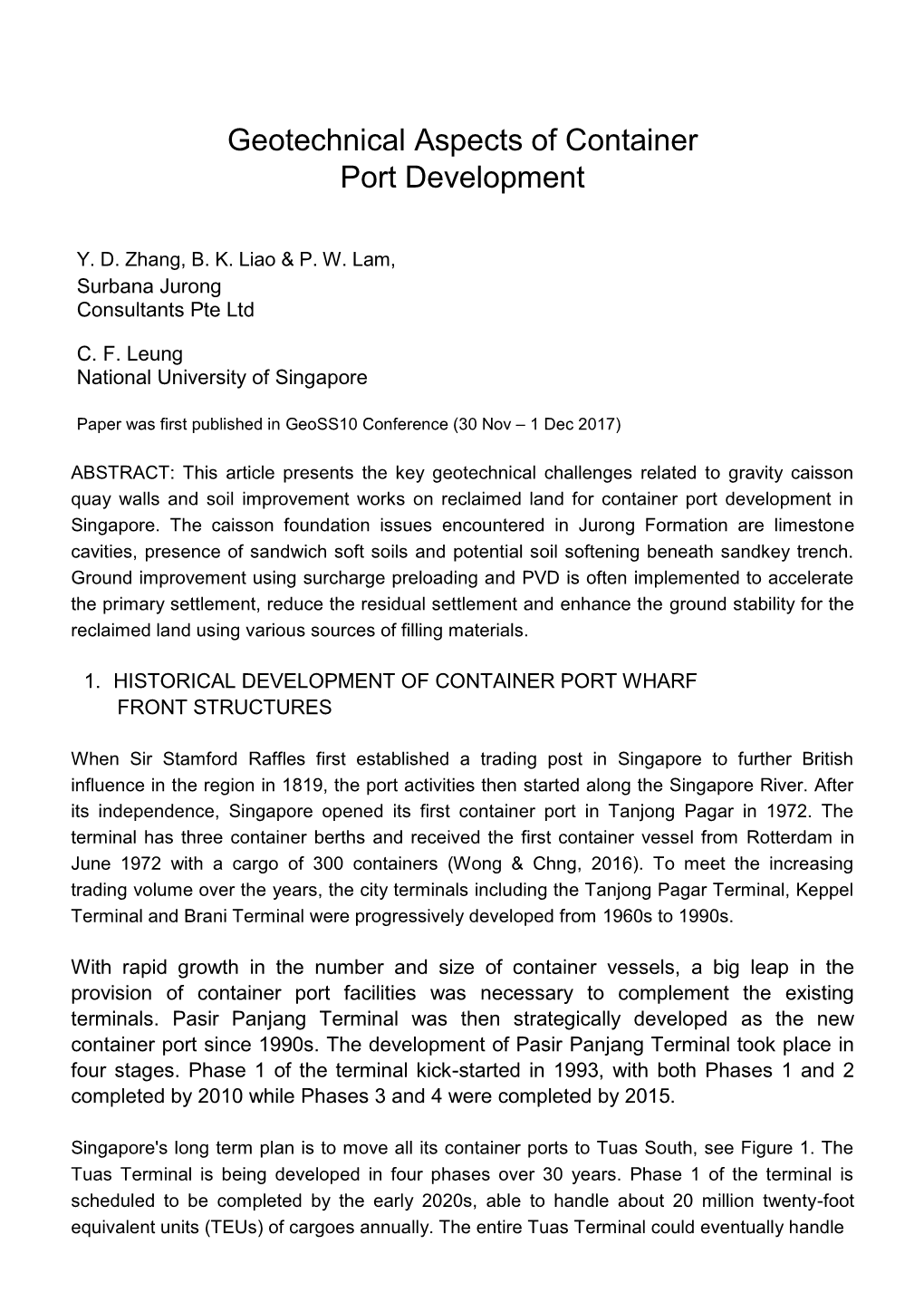
Load more
Recommended publications
-
Urban Tropical Ecology in Singapore Biology / Environ 571A
URBAN TROPICAL ECOLOGY IN SINGAPORE BIOLOGY / ENVIRON 571A Course Description (from Duke University Bulletin) Experiential field oriented course in Singapore and Malaysia focusing on human ecology, tropical diversity, disturbed habitats, Asian extinctions, and resource management. Students spend approximately three weeks in Singapore/Malaysia during the spring semester. Additional course fees apply. Faculty: Dr. Dan Rittschof, Dr. Tom Schultz General Description Singapore is a fascinating combination of biophysical, human and institutional ecology, tropical diversity, disturbed habitats, invasive species and built environments. Within the boundaries of the city state/island of Singapore one can go from patches of primary rain forest to housing estates for 4.8 million plus residents, industrial complexes, and a port that processes between 800 and 1000 ships a day. Singapore's land area grew from 581.5 km2 (224.5 sq mi) in the 1960s to 704 km2 (271.8 sq mi) today, and may grow by another 100 km² (38.6 sq mi) by 2030. Singapore includes thousands of introduced species, including a multicultural assemblage of human inhabitants. Singapore should be in the Guinness Book of World Records for its increase in relative country size due to reclamation, and for the degree of governmental planning and control for the lives of its citizens. It is within this biological and social context that this experiential field oriented seminar will be conducted. Students will experience how this city state functions, and how it has worked to maintain and enhance the quality of life of its citizens while intentionally and unintentionally radically modifying its environment, in the midst of the extremely complicated geopolitical situation of Southeast Asia. -
Hotel Address Postal Code 3D Harmony Hostel 23/25A Mayo
Changi Airport Transfer Hotel Address Postal Code 3D Harmony Hostel 23/25A Mayo Street S(208308) 30 Bencoolen Hotel 30 Bencoolen St S(189621) 5 Footway Inn Project Chinatown 2 227 South Bridge Road S(058776) 5 Footway Inn Project Ann Siang 267 South Bridge Road S(058816) 5 Footway Inn Project Chinatown 1 63 Pagoda St S(059222) 5 Footway Inn Project Bugis 8,10,12 Aliwal Street S(199903) 5 Footway Inn Project Boat Quay 76 Boat Quay S(049864) 7 Wonder Capsule Hostel 257 Jalan Besar S(208930) 38 Hongkong Street Hostel 38A Hong Kong Street S(059677) 60's Hostel 569 Serangoon Road S(218184) 60's Hostel 96A Lorong 27 Geylang S(388198) 165 Hotel 165 Kitchener Road S(208532) A Beary Best Hostel 16 & 18 Upper Cross Street S(059225) A Travellers Rest -Stop 5 Teck Lim Road S(088383) ABC Backpacker Hostel 3 Jalan Kubor (North Bridge Road) S(199201) ABC Premier Hostel 91A Owen Road S(218919) Adler Hostel 259 South Bridge Road S(058808) Adamson Inn Hotel 3 Jalan Pinang,Bugis S(199135) Adamson Lodge 6 Perak Road S(208127) Alis Nest Singapore 23 Robert Lane, Serangoon Road S(218302) Aliwal Park Hotel 77 / 79 Aliwal St. S(199948) Amara Hotel 165 Tanjong Pagar Road S(088539) Amaris Hotel 21 Middle Road S(188931) Ambassador Hotel 65-75 Desker Road S(209598) Amigo Hostel 55 Lavender Road S(338713) Amrise Hotel 112 Sims Avenue #01-01 S(387436) Amoy Hotel 76 Telok Ayer St S(048464) Andaz Singapore 5 Fraser Street S(189354) Aqueen Hotel Balestier 387 Balestier Road S(029795) Aqueen Hotel Lavender 139 Lavender St. -
NO. 9 NEIL ROAD the House Before Restoration
URA PILOT RESTORATION PROJECT The Urban Redevelopment Authority (URA) is the national planning authority for Singapore. Its active involvement in conservation started as early as the 1970s with the rehabilitation of some state-owned properties for adaptive reuse. To-date, conservation status has been given to 94 The house before conservation areas involving over 6800 buildings throughout the island. NO. 9 NEIL ROAD Conservation of our built heritage is an integral part of urban planning and development in Singapore. The restoration of our historic areas add variety to our streetscapes and modulate the scale of our urban fabric, creating restoration the visual contrast and excitement within the city while protecting the important reminders and representations of our past. In addition, it adds to the distinctive character and identity of our city, giving it a sense of history and memory of place. Revitalisation of Tanjong Pagar CREDITS Architect & Engineer: Urban Redevelopment Authority Contractors: Khian Heng Construction (Pte) Ltd Telephone No: (65) 6221 6666 Website: www.ura.gov.sg © Urban Redevelopment Authority. All Rights Reserved The information is accurate as at time of print and changes could have been made since then. URA is not responsible for any loss or damage that may be incurred or suffered by anyone using or relying on the information set out in the brochure. Designed and produced by Urban Redevelopment Authority, March 2009 KRETA AYER ROAD MAXWELL ROAD NO. 9 FOOD CENTRE JINRIKSHA NEIL ROAD STATION FAIRFIELD CONSERVATION OF METHODIST K CHURCH MAXWELL ROAD E TANJONG PAGAR 32 shophouses in Tanjong Pagar were restored to their O N PHASE 1 JIAK CHUAN ROAD NEIL ROAD G former glory between 1987 and 1988, in the first ever project S A I undertaken by the government to demonstrate that was it K S T technically possible and commercially viable to restore our R E E heritage shophouses. -
GES1004 Biophysical Environment of Singapore @ NUS Yunpeng's Final
GES1004 Biophysical Environment of Singapore @ NUS Yunpeng’s Final Summary GES1004 Biophysical Environment of Singapore Part 0 Introduction 1. There are 5 main components of the biophysical environment. Namely, they are the lithosphere, the hydrosphere, the atmosphere, the biosphere, and the anthrosphere. 2. To study the biophysical environment, we need to learn geology, geography, topography, biological sciences, environmental sciences, and social sciences. Part 1 Rocks and Plate Tectonics 1. There are mainly 3 types of rocks on the earth, igneous (intrusive and extrusive), sedimentary and metamorphic. 2. Internal structure of earth: atmosphere (exosphere, thermosphere, mesosphere, stratosphere and troposphere), crust (oceanic crust and continental crust), mantle (upper mantle and mantle), and core (outer core - liquid and inner core - solid). 3. The boundary surface between crust and upper mantle is called Mohorovicic discontinuity. Crust forms the lithosphere (100km) of the earth, while the upper mantle is considered to be the asthenosphere (250km) of the earth (low-velocity zone). The boundary surface between mantle and core is called Gutenberg discontinuity. 4. Structural components of the lithosphere: African Plate, Austral-Indian Plate, Eurasian Plate, Pacific Plate, Nazca Plate, South American Plate. 5. Evidence for Continental Drift (Alfred Wegener): continental fit, rock sequences, mountain ranges, glacial deposits and striations, fossil existence, palaeomagnetism & Curie point. Due to so many geologic evidences, a unifying theory called Plate Tectonics have been developed based on Continental Drift. 6. There are 3 types of plate boundaries. Namely, they are divergent, convergent and transform. Thus, dipping earthquake zone, Benioff zone and subduction zone always come together. For instance, the average rate of motion is 0-20cm/year. -
Participating Merchants
PARTICIPATING MERCHANTS PARTICIPATING POSTAL ADDRESS MERCHANTS CODE 460 ALEXANDRA ROAD, #01-17 AND #01-20 119963 53 ANG MO KIO AVENUE 3, #01-40 AMK HUB 569933 241/243 VICTORIA STREET, BUGIS VILLAGE 188030 BUKIT PANJANG PLAZA, #01-28 1 JELEBU ROAD 677743 175 BENCOOLEN STREET, #01-01 BURLINGTON SQUARE 189649 THE CENTRAL 6 EU TONG SEN STREET, #01-23 TO 26 059817 2 CHANGI BUSINESS PARK AVENUE 1, #01-05 486015 1 SENG KANG SQUARE, #B1-14/14A COMPASS ONE 545078 FAIRPRICE HUB 1 JOO KOON CIRCLE, #01-51 629117 FUCHUN COMMUNITY CLUB, #01-01 NO 1 WOODLANDS STREET 31 738581 11 BEDOK NORTH STREET 1, #01-33 469662 4 HILLVIEW RISE, #01-06 #01-07 HILLV2 667979 INCOME AT RAFFLES 16 COLLYER QUAY, #01-01/02 049318 2 JURONG EAST STREET 21, #01-51 609601 50 JURONG GATEWAY ROAD JEM, #B1-02 608549 78 AIRPORT BOULEVARD, #B2-235-236 JEWEL CHANGI AIRPORT 819666 63 JURONG WEST CENTRAL 3, #B1-54/55 JURONG POINT SHOPPING CENTRE 648331 KALLANG LEISURE PARK 5 STADIUM WALK, #01-43 397693 216 ANG MO KIO AVE 4, #01-01 569897 1 LOWER KENT RIDGE ROAD, #03-11 ONE KENT RIDGE 119082 BLK 809 FRENCH ROAD, #01-31 KITCHENER COMPLEX 200809 Burger King BLK 258 PASIR RIS STREET 21, #01-23 510258 8A MARINA BOULEVARD, #B2-03 MARINA BAY LINK MALL 018984 BLK 4 WOODLANDS STREET 12, #02-01 738623 23 SERANGOON CENTRAL NEX, #B1-30/31 556083 80 MARINE PARADE ROAD, #01-11 PARKWAY PARADE 449269 120 PASIR RIS CENTRAL, #01-11 PASIR RIS SPORTS CENTRE 519640 60 PAYA LEBAR ROAD, #01-40/41/42/43 409051 PLAZA SINGAPURA 68 ORCHARD ROAD, #B1-11 238839 33 SENGKANG WEST AVENUE, #01-09/10/11/12/13/14 THE -
Relocation Letter to Parents
20 April 2021 Dear Parents / Guardians, RELOCATION OF GRACE ORCHARD SCHOOL IN TERM 3, 2021 1. Ministry of Education (MOE) will be expanding Grace Orchard School (GOS) to provide new educational and vocational training facilities, larger classrooms, and modulation spaces to cater to our students. The new campus would also be equipped with PE and sports facilities such as sheltered playgrounds and outdoor fitness areas. 2. To facilitate its expansion plan, the school will be moving out of its current premises at Jurong West to a holding school at West Coast Road. Please see the Holding School Map in Annex A. 3. The school will start its operations at the holding school in Term 3, Week 1: Start Date Address of Holding School 28 June 2021 170, West Coast Road, Singapore 127443 4. The school has prepared a Travel Guide and Road Safety Advisory for your child/ward in Annex B. 5. To better understand and support your child/ward for the relocation, please complete the Survey Form in Annex C on the following: a) Child/Ward’s Travel Plan to the Holding Site b) School Bus Registration Service and Transportation Subsidy Please return the Survey Form to the Class Teacher by 28 April 2021. 6. For students who require school bus service to the holding school, please fill in the attached Bus Registration Form and submit to the General Office by 28 April 2021. Students currently on school bus service will also need to submit their applications. 7. The Parents’ Network Group is recruiting parent volunteers to support the relocation efforts. -
WARTIME Trails
history ntosa : Se : dit e R C JourneyWARTIME into Singapore’s military historyTRAI at these lS historic sites and trails. Fort Siloso ingapore’s rich military history and significance in World War II really comes alive when you make the effort to see the sights for yourself. There are four major sites for military buffs to visit. If you Sprefer to stay around the city centre, go for the Civic District or Pasir Panjang trails, but if you have time to venture out further, you can pay tribute to the victims of war at Changi and Kranji. The Japanese invasion of February 1942 February 8 February 9 February 10 February 13-14 February 15 Japanese troops land and Kranji Beach Battle for Bukit Battle of Pasir British surrender Singapore M O attack Sarimbun Beach Battle Timah PanjangID Ridge to the JapaneseP D H L R I E O R R R O C O A H A D O D T R E R E O R O T A RC S D CIVIC DISTRICT HAR D R IA O OA R D O X T D L C A E CC1 NE6 NS24 4 I O Singapore’s civic district, which Y V R Civic District R 3 DHOBY GHAUT E I G S E ID was once the site of the former FORT CA R N B NI N CC2 H 5 G T D Y E LI R A A U N BRAS BASAH K O O W British colony’s commercial and N N R H E G H I V C H A A L E L U B O administrative activities in the C A I E B N C RA N S E B 19th and 20th century, is where A R I M SA V E H E L R RO C VA A you’ll find plenty of important L T D L E EY E R R O T CC3 A S EW13 NS25 2 D L ESPLANADE buildings and places of interest. -
143 Bus Time Schedule & Line Route
143 bus time schedule & line map 143 Jurong East Int View In Website Mode The 143 bus line (Jurong East Int) has 2 routes. For regular weekdays, their operation hours are: (1) Jurong East Int: 5:30 AM - 11:27 PM (2) Toa Payoh Int: 5:25 AM - 11:26 PM Use the Moovit App to ƒnd the closest 143 bus station near you and ƒnd out when is the next 143 bus arriving. Direction: Jurong East Int 143 bus Time Schedule 74 stops Jurong East Int Route Timetable: VIEW LINE SCHEDULE Sunday 5:45 AM - 11:19 PM Monday 5:30 AM - 11:27 PM Lor 6 Toa Payoh - Toa Payoh Int (52009) 530 Lorong 6 Toa Payoh, Singapore Tuesday 5:30 AM - 11:27 PM Jln Toa Payoh - Opp Trellis Twrs (52079) Wednesday 5:30 AM - 11:27 PM Thomson Rd - Opp Thomson Med Ctr (50059) Thursday 5:30 AM - 11:27 PM Friday 5:30 AM - 11:27 PM Thomson Rd - Opp Novena Lodge (50049) 312 Thomson Road, Singapore Saturday 5:30 AM - 11:27 PM Thomson Rd - Novena Stn Exit B (50037) 1 Novena Terrace, Singapore Newton Rd - Hotel Royal (50069) 143 bus Info 36 Newton Road, Singapore Direction: Jurong East Int Stops: 74 Newton Rd - Newton Life CH (40129) Trip Duration: 110 min 18 Newton Road, Singapore Line Summary: Lor 6 Toa Payoh - Toa Payoh Int (52009), Jln Toa Payoh - Opp Trellis Twrs (52079), Scotts Rd - Newton Stn Exit B (40189) Thomson Rd - Opp Thomson Med Ctr (50059), 49 Scotts Road, Singapore Thomson Rd - Opp Novena Lodge (50049), Thomson Rd - Novena Stn Exit B (50037), Newton Rd - Hotel Scotts Rd - Env Bldg (40179) Royal (50069), Newton Rd - Newton Life CH (40129), Scotts Road, Singapore Scotts Rd - Newton Stn Exit B (40189), Scotts Rd - Env Bldg (40179), Scotts Rd - Far East Plaza Scotts Rd - Far East Plaza (09219) (09219), Orchard Rd - Orchard Stn/Tang Plaza (09047), Orchard Rd - Opp Mandarin Orchard Orchard Rd - Orchard Stn/Tang Plaza (09047) (09037), Orchard Rd - Orchard Plaza (08137), Scotts Road, Singapore Clemenceau Ave - Aft Haw Par Glass Twr (08019), Clemenceau Ave - Opp U.E. -
Download Map and Guide
Bukit Pasoh Telok Ayer Kreta Ayer CHINATOWN A Walking Guide Travel through 14 amazing stops to experience the best of Chinatown in 6 hours. A quick introduction to the neighbourhoods Kreta Ayer Kreta Ayer means “water cart” in Malay. It refers to ox-drawn carts that brought water to the district in the 19th and 20th centuries. The water was drawn from wells at Ann Siang Hill. Back in those days, this area was known for its clusters of teahouses and opera theatres, and the infamous brothels, gambling houses and opium dens that lined the streets. Much of its sordid history has been cleaned up. However, remnants of its vibrant past are still present – especially during festive periods like the Lunar New Year and the Mid-Autumn celebrations. Telok Ayer Meaning “bay water” in Malay, Telok Ayer was at the shoreline where early immigrants disembarked from their long voyages. Designated a Chinese district by Stamford Raffles in 1822, this is the oldest neighbourhood in Chinatown. Covering Ann Siang and Club Street, this richly diverse area is packed with trendy bars and hipster cafés housed in beautifully conserved shophouses. Bukit Pasoh Located on a hill, Bukit Pasoh is lined with award-winning restaurants, boutique hotels, and conserved art deco shophouses. Once upon a time, earthen pots were produced here. Hence, its name – pasoh, which means pot in Malay. The most vibrant street in this area is Keong Saik Road – a former red-light district where gangs and vice once thrived. Today, it’s a hip enclave for stylish hotels, cool bars and great food. -
List-Of-Bin-Locations-1-1.Pdf
List of publicly accessible locations where E-Bins are deployed* *This is a working list, more locations will be added every week* Name Location Type of Bin Placed Ace The Place CC • 120 Woodlands Ave 1 3-in-1 Bin (ICT, Bulb, Battery) Apple • 2 Bayfront Avenue, B2-06, MBS • 270 Orchard Rd Battery and Bulb Bin • 78 Airport Blvd, Jewel Airport Ang Mo Kio CC • Ang Mo Kio Avenue 1 3-in-1 Bin (ICT, Bulb, Battery) Best Denki • 1 Harbourfront Walk, Vivocity, #2-07 • 3155 Commonwealth Avenue West, The Clementi Mall, #04- 46/47/48/49 • 68 Orchard Road, Plaza Singapura, #3-39 • 2 Jurong East Street 21, IMM, #3-33 • 63 Jurong West Central 3, Jurong Point, #B1-92 • 109 North Bridge Road, Funan, #3-16 3-in-1 Bin • 1 Kim Seng Promenade, Great World City, #07-01 (ICT, Bulb, Battery) • 391A Orchard Road, Ngee Ann City Tower A • 9 Bishan Place, Junction 8 Shopping Centre, #03-02 • 17 Petir Road, Hillion Mall, #B1-65 • 83 Punggol Central, Waterway Point • 311 New Upper Changi Road, Bedok Mall • 80 Marine Parade Road #03 - 29 / 30 Parkway Parade Complex Bugis Junction • 230 Victoria Street 3-in-1 Bin Towers (ICT, Bulb, Battery) Bukit Merah CC • 4000 Jalan Bukit Merah 3-in-1 Bin (ICT, Bulb, Battery) Bukit Panjang CC • 8 Pending Rd 3-in-1 Bin (ICT, Bulb, Battery) Bukit Timah Plaza • 1 Jalan Anak Bukit 3-in-1 Bin (ICT, Bulb, Battery) Cash Converters • 135 Jurong Gateway Road • 510 Tampines Central 1 3-in-1 Bin • Lor 4 Toa Payoh, Blk 192, #01-674 (ICT, Bulb, Battery) • Ang Mo Kio Ave 8, Blk 710A, #01-2625 Causeway Point • 1 Woodlands Square 3-in-1 Bin (ICT, -
175 Bus Time Schedule & Line Route
175 bus time schedule & line map 175 Clementi Int View In Website Mode The 175 bus line (Clementi Int) has 2 routes. For regular weekdays, their operation hours are: (1) Clementi Int: 6:11 AM - 11:30 PM (2) Lor 1 Geylang Ter: 6:00 AM - 11:26 PM Use the Moovit App to ƒnd the closest 175 bus station near you and ƒnd out when is the next 175 bus arriving. Direction: Clementi Int 175 bus Time Schedule 62 stops Clementi Int Route Timetable: VIEW LINE SCHEDULE Sunday 6:00 AM - 11:30 PM Monday 6:11 AM - 11:30 PM Lor 1 Geylang - Lor 1 Geylang Ter (80009) Lorong 1 Geylang Terminal, Singapore Tuesday 6:11 AM - 11:30 PM Lor 1 Geylang - Opp Blk 2c (80101) Wednesday 6:11 AM - 11:30 PM Upp Boon Keng Rd - Geylang West Cc (80319) Thursday 6:11 AM - 11:30 PM Upper Boon Keng Road, Singapore Friday 6:11 AM - 11:30 PM Upp Boon Keng Rd - Aft Geylang West Cc (80309) Saturday 6:00 AM - 11:30 PM Upper Boon Keng Road, Singapore Geylang Bahru - Opp Blk 82 (80299) Kallang Bahru - Opp Blk 66 (60039) 175 bus Info Direction: Clementi Int Kallang Bahru - Blk 16 (60029) Stops: 62 16 Kallang Place, Singapore Trip Duration: 95 min Line Summary: Lor 1 Geylang - Lor 1 Geylang Ter Kallang Bahru - Bendemeer Stn Exit B (60019) (80009), Lor 1 Geylang - Opp Blk 2c (80101), Upp Boon Keng Rd - Geylang West Cc (80319), Upp Boon Lavender St - Aft Kallang Bahru (07369) Keng Rd - Aft Geylang West Cc (80309), Geylang 103 Lavender Street, Singapore Bahru - Opp Blk 82 (80299), Kallang Bahru - Opp Blk 66 (60039), Kallang Bahru - Blk 16 (60029), Kallang Lavender St - Aperia/Bef Kallang -
Participating Merchants Address Postal Code Club21 3.1 Phillip Lim 581 Orchard Road, Hilton Hotel 238883 A|X Armani Exchange
Participating Merchants Address Postal Code Club21 3.1 Phillip Lim 581 Orchard Road, Hilton Hotel 238883 A|X Armani Exchange 2 Orchard Turn, B1-03 ION Orchard 238801 391 Orchard Road, #B1-03/04 Ngee Ann City 238872 290 Orchard Rd, 02-13/14-16 Paragon #02-17/19 238859 2 Bayfront Avenue, B2-15/16/16A The Shoppes at Marina Bay Sands 018972 Armani Junior 2 Bayfront Avenue, B1-62 018972 Bao Bao Issey Miyake 2 Orchard Turn, ION Orchard #03-24 238801 Bonpoint 583 Orchard Road, #02-11/12/13 Forum The Shopping Mall 238884 2 Bayfront Avenue, B1-61 018972 CK Calvin Klein 2 Orchard Turn, 03-09 ION Orchard 238801 290 Orchard Road, 02-33/34 Paragon 238859 2 Bayfront Avenue, 01-17A 018972 Club21 581 Orchard Road, Hilton Hotel 238883 Club21 Men 581 Orchard Road, Hilton Hotel 238883 Club21 X Play Comme 2 Bayfront Avenue, #B1-68 The Shoppes At Marina Bay Sands 018972 Des Garscons 2 Orchard Turn, #03-10 ION Orchard 238801 Comme Des Garcons 6B Orange Grove Road, Level 1 Como House 258332 Pocket Commes des Garcons 581 Orchard Road, Hilton Hotel 238883 DKNY 290 Orchard Rd, 02-43 Paragon 238859 2 Orchard Turn, B1-03 ION Orchard 238801 Dries Van Noten 581 Orchard Road, Hilton Hotel 238883 Emporio Armani 290 Orchard Road, 01-23/24 Paragon 238859 2 Bayfront Avenue, 01-16 The Shoppes at Marina Bay Sands 018972 Giorgio Armani 2 Bayfront Avenue, B1-76/77 The Shoppes at Marina Bay Sands 018972 581 Orchard Road, Hilton Hotel 238883 Issey Miyake 581 Orchard Road, Hilton Hotel 238883 Marni 581 Orchard Road, Hilton Hotel 238883 Mulberry 2 Bayfront Avenue, 01-41/42 018972