Modeling and Simulation Software in MEMS Design
Total Page:16
File Type:pdf, Size:1020Kb
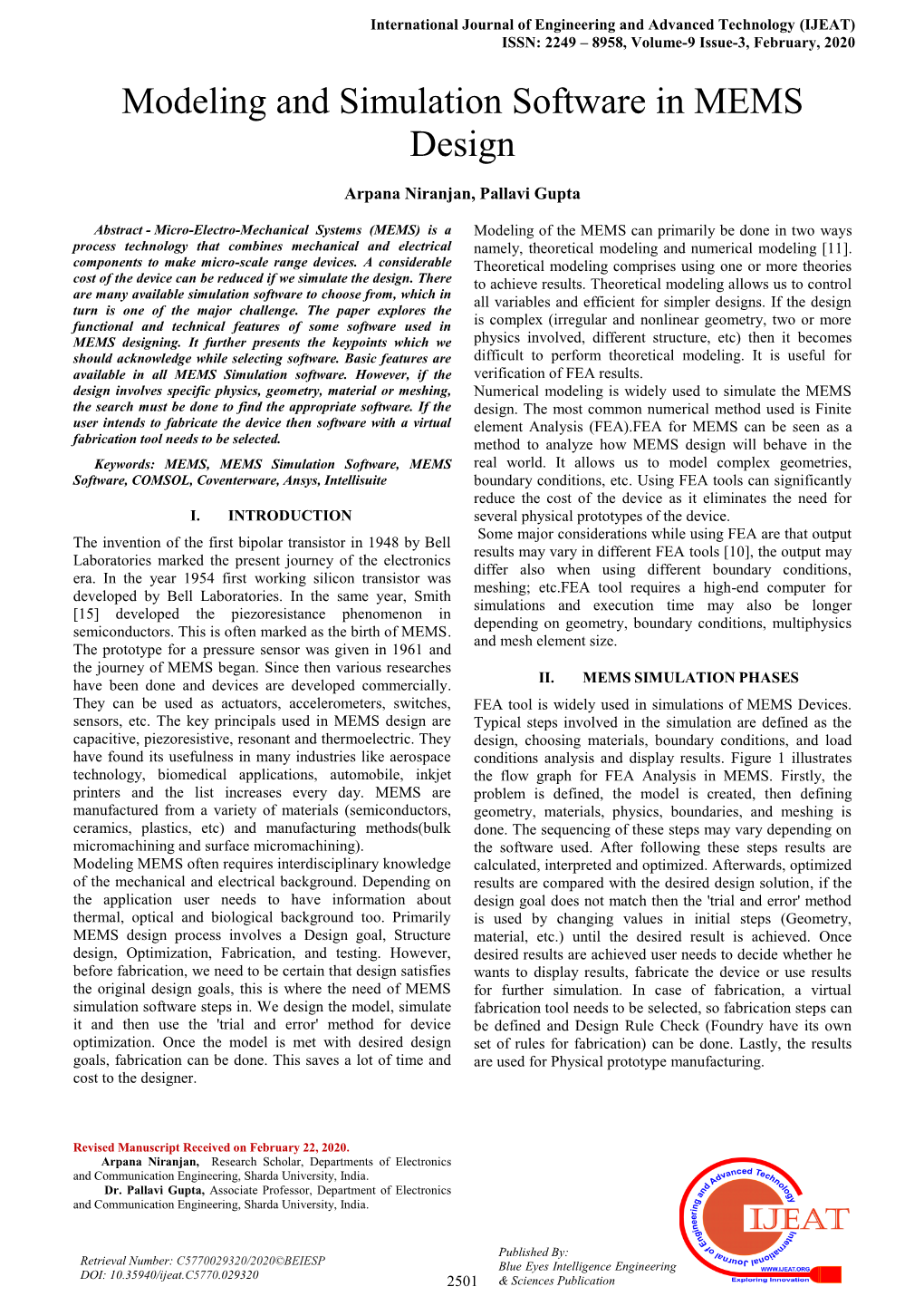
Load more
Recommended publications
-
Recent Developments in Microfluidic Large Scale Integration
UC Riverside UC Riverside Previously Published Works Title Recent developments in microfluidic large scale integration. Permalink https://escholarship.org/uc/item/3jh0x2hh Journal Current opinion in biotechnology, 25 ISSN 0958-1669 Authors Araci, Ismail Emre Brisk, Philip Publication Date 2014-02-01 DOI 10.1016/j.copbio.2013.08.014 Peer reviewed eScholarship.org Powered by the California Digital Library University of California Available online at www.sciencedirect.com ScienceDirect Recent developments in microfluidic large scale integration 1 2 Ismail Emre Araci and Philip Brisk In 2002, Thorsen et al. integrated thousands of The on-chip valve is the key component of mLSI, much micromechanical valves on a single microfluidic chip and like the transistor in semiconductor LSI. Typically, demonstrated that the control of the fluidic networks can be microfluidic valves are fabricated by multilayer soft litho- simplified through multiplexors [1]. This enabled realization of graphy (MSL) using PDMS and are actuated by external highly parallel and automated fluidic processes with substantial pneumatic controllers. A valve requires an elastomeric sample economy advantage. Moreover, the fabrication of these membrane that is deflected to control the fluidic resist- devices by multilayer soft lithography was easy and reliable ance; when the valve is open, the fluidic resistance has a hence contributed to the power of the technology; microfluidic minimum value, determined by channel dimensions and large scale integration (mLSI). Since then, mLSI has found use when the valve is closed, the fluidic resistance is increased in wide variety of applications in biology and chemistry. In the to infinity because flow rate is reduced to zero. -
Development of a Coupling Approach for Multi-Physics Analyses of Fusion Reactors
Development of a coupling approach for multi-physics analyses of fusion reactors Zur Erlangung des akademischen Grades eines Doktors der Ingenieurwissenschaften (Dr.-Ing.) bei der Fakultat¨ fur¨ Maschinenbau des Karlsruher Instituts fur¨ Technologie (KIT) genehmigte DISSERTATION von Yuefeng Qiu Datum der mundlichen¨ Prufung:¨ 12. 05. 2016 Referent: Prof. Dr. Stieglitz Korreferent: Prof. Dr. Moslang¨ This document is licensed under the Creative Commons Attribution – Share Alike 3.0 DE License (CC BY-SA 3.0 DE): http://creativecommons.org/licenses/by-sa/3.0/de/ Abstract Fusion reactors are complex systems which are built of many complex components and sub-systems with irregular geometries. Their design involves many interdependent multi- physics problems which require coupled neutronic, thermal hydraulic (TH) and structural mechanical (SM) analyses. In this work, an integrated system has been developed to achieve coupled multi-physics analyses of complex fusion reactor systems. An advanced Monte Carlo (MC) modeling approach has been first developed for converting complex models to MC models with hybrid constructive solid and unstructured mesh geometries. A Tessellation-Tetrahedralization approach has been proposed for generating accurate and efficient unstructured meshes for describing MC models. For coupled multi-physics analyses, a high-fidelity coupling approach has been developed for the physical conservative data mapping from MC meshes to TH and SM meshes. Interfaces have been implemented for the MC codes MCNP5/6, TRIPOLI-4 and Geant4, the CFD codes CFX and Fluent, and the FE analysis platform ANSYS Workbench. Furthermore, these approaches have been implemented and integrated into the SALOME simulation platform. Therefore, a coupling system has been developed, which covers the entire analysis cycle of CAD design, neutronic, TH and SM analyses. -
Livelink for MATLAB User's Guide
LiveLink™ for MATLAB® User’s Guide LiveLink™ for MATLAB® User’s Guide © 2009–2020 COMSOL Protected by patents listed on www.comsol.com/patents, and U.S. Patents 7,519,518; 7,596,474; 7,623,991; 8,457,932;; 9,098,106; 9,146,652; 9,323,503; 9,372,673; 9,454,625, 10,019,544, 10,650,177; and 10,776,541. Patents pending. This Documentation and the Programs described herein are furnished under the COMSOL Software License Agreement (www.comsol.com/comsol-license-agreement) and may be used or copied only under the terms of the license agreement. COMSOL, the COMSOL logo, COMSOL Multiphysics, COMSOL Desktop, COMSOL Compiler, COMSOL Server, and LiveLink are either registered trademarks or trademarks of COMSOL AB. MATLAB and Simulink are registered trademarks of The MathWorks, Inc.. All other trademarks are the property of their respective owners, and COMSOL AB and its subsidiaries and products are not affiliated with, endorsed by, sponsored by, or supported by those or the above non-COMSOL trademark owners. For a list of such trademark owners, see www.comsol.com/trademarks. Version: COMSOL 5.6 Contact Information Visit the Contact COMSOL page at www.comsol.com/contact to submit general inquiries, contact Technical Support, or search for an address and phone number. You can also visit the Worldwide Sales Offices page at www.comsol.com/contact/offices for address and contact information. If you need to contact Support, an online request form is located at the COMSOL Access page at www.comsol.com/support/case. Other useful links include: • Support Center: www.comsol.com/support • Product Download: www.comsol.com/product-download • Product Updates: www.comsol.com/support/updates • COMSOL Blog: www.comsol.com/blogs • Discussion Forum: www.comsol.com/community • Events: www.comsol.com/events • COMSOL Video Gallery: www.comsol.com/video • Support Knowledge Base: www.comsol.com/support/knowledgebase Part number: CM020008 Contents Chapter 1: Introduction About This Product 12 Help and Documentation 14 Getting Help . -
Navisworks 2013 Supported Formats and Applications
Autodesk Navisworks 2013 Solutions Autodesk ® Navisworks ® 2013 Supported File Formats London Blackfriars station, courtesy of Network Rail and Jacobs R Autodesk Navisworks 2013 Solutions Autodesk Navisworks 2013 Solutions This document details support provided by the current release of Autodesk Navisworks 2013 solutions (including Autodesk Navisworks Simulate and Autodesk Navisworks Manage) for: • CAD file formats. • Laser scan formats. • CAD applications. • Scheduling software. NOTE: When referring to Navisworks or Autodesk Navisworks 2013 solutions in this document this does NOT include Autodesk Navisworks Freedom 2013, which only reads NWD or DWF files. Product Release Version: 2013 Document version: 1.0 March 2012 © 2013 Autodesk, Inc. All rights reserved. Except as otherwise permitted by Autodesk, Inc., this publication, or parts thereof, may not be reproduced in any form, by any method, for any purpose. Autodesk, AutoCAD, Civil 3D, DWF, DWG, DXF, Inventor, Maya, Navisworks, Revit, and 3ds Max are registered trademarks or trademarks of Autodesk, Inc., in the USA and other countries. All other brand names, product names, or trademarks belong to their respective holders. Autodesk reserves the right to alter product offerings and specifications at any time without notice, and is not responsible for typographical or graphical errors that may appear in this document. Disclaimer Certain information included in this publication is based on technical information provided by third parties. THIS PUBLICATION AND THE INFORMATION CONTAINED HEREIN IS MADE AVAILABLE BY AUTODESK, INC. “AS IS.” AUTODESK, INC. DISCLAIMS ALL WARRANTIES, EITHER EXPRESS OR IMPLIED, INCLUDING BUT NOT LIMITED TO ANY IMPLIED WARRANTIES OF MERCHANTABILITY OR FITNESS FOR A PARTICULAR PURPOSE REGARDING THESE MATERIALS. -
The COMSOL Multiphysics Installation and Operations User's Guide
COMSOL Multiphysics ® Installation and Operations Guide VERSION 4.3 COMSOL Multiphysics Installation and Operations Guide 1998–2012 COMSOL Protected by U.S. Patents 7,519,518; 7,596,474; and 7,623,991. Patents pending. This Documentation and the Programs described herein are furnished under the COMSOL Software License Agreement (www.comsol.com/sla) and may be used or copied only under the terms of the license agree- ment. COMSOL, COMSOL Desktop, COMSOL Multiphysics, and LiveLink are registered trademarks or trade- marks of COMSOL AB. Other product or brand names are trademarks or registered trademarks of their respective holders. Version: May 2012 COMSOL 4.3 Contact Information Visit www.comsol.com/contact for a searchable list of all COMSOL offices and local representatives. From this web page, search the contacts and find a local sales representative, go to other COMSOL websites, request information and pricing, submit technical support queries, subscribe to the monthly eNews email newsletter, and much more. If you need to contact Technical Support, an online request form is located at www.comsol.com/support/contact. Other useful links include: • Technical Support www.comsol.com/support • Software updates: www.comsol.com/support/updates • Online community: www.comsol.com/community • Events, conferences, and training: www.comsol.com/events • Tutorials: www.comsol.com/products/tutorials • Knowledge Base: www.comsol.com/support/knowledgebase Part No. CM010002 Contents Chapter 1: Introduction General Tips 8 General System Requirements for Windows, Linux, or Mac Computers . 8 Hardware Parameters that Affect Performance . 9 COMSOL Release Notes . 9 Introduction to COMSOL Multiphysics and Online Help . 9 Technical Support . -
COMSOL Multiphysics®
COMSOL Multiphysics ® M ODEL L IBRARY V ERSION 3.5a How to contact COMSOL: Germany United Kingdom COMSOL Multiphysics GmbH COMSOL Ltd. Benelux Berliner Str. 4 UH Innovation Centre COMSOL BV D-37073 Göttingen College Lane Röntgenlaan 19 Phone: +49-551-99721-0 Hatfield 2719 DX Zoetermeer Fax: +49-551-99721-29 Hertfordshire AL10 9AB The Netherlands [email protected] Phone:+44-(0)-1707 636020 Phone: +31 (0) 79 363 4230 www.comsol.de Fax: +44-(0)-1707 284746 Fax: +31 (0) 79 361 4212 [email protected] [email protected] Italy www.uk.comsol.com www.comsol.nl COMSOL S.r.l. Via Vittorio Emanuele II, 22 United States Denmark 25122 Brescia COMSOL, Inc. COMSOL A/S Phone: +39-030-3793800 1 New England Executive Park Diplomvej 376 Fax: +39-030-3793899 Suite 350 2800 Kgs. Lyngby [email protected] Burlington, MA 01803 Phone: +45 88 70 82 00 www.it.comsol.com Phone: +1-781-273-3322 Fax: +45 88 70 80 90 Fax: +1-781-273-6603 [email protected] Norway www.comsol.dk COMSOL AS COMSOL, Inc. Søndre gate 7 10850 Wilshire Boulevard Finland NO-7485 Trondheim Suite 800 COMSOL OY Phone: +47 73 84 24 00 Los Angeles, CA 90024 Arabianranta 6 Fax: +47 73 84 24 01 Phone: +1-310-441-4800 FIN-00560 Helsinki [email protected] Fax: +1-310-441-0868 Phone: +358 9 2510 400 www.comsol.no Fax: +358 9 2510 4010 COMSOL, Inc. [email protected] Sweden 744 Cowper Street www.comsol.fi COMSOL AB Palo Alto, CA 94301 Tegnérgatan 23 Phone: +1-650-324-9935 France SE-111 40 Stockholm Fax: +1-650-324-9936 COMSOL France Phone: +46 8 412 95 00 WTC, 5 pl. -
Chapter 12 Computervision
Chapter 12 Computervision According to a 1994 Wall Street Journal article, Philippe Villers decided to start a technology company shortly after listening to the minister at Concord, Massachusetts’ First Parish Church extol Martin Luther King’s accomplishments a few days after he was murdered in April 1968. Villers felt he needed to do something meaningful with his life and that there were two options – either become a social activist or start a company, make a lot of money and then use that money to change the world. Luckily for what eventually became the CAD/CAM industry, he chose the second path.1 Villers was technically well qualified to start Computervision, Inc. or CV is it was generally known. Born in Paris, France, he came to this country via Canada in the early 1940s to escape the Nazis. Villers had an undergraduate liberal arts degree from Harvard and a masters degree in mechanical engineering from MIT. He worked for several years in General Electric’s management training program followed by stints at Perkin Elmer, Barnes Engineering and the Link Division of Singer-General Precision with increasing levels of project management responsibility. At the time he decided to establish Computervision, Villers was Manager of Advanced Products at Concord Control in Boston. Villers spent much of his spare time in 1968 meeting with a group of business and technical associates including Steve Coons and Nicholas Negroponte (founder of the MIT Media Lab). Realizing that it takes more than good technical ideas to build a successful company, Villers decided to find a partner with more business experience to help jump start the enterprise. -
Simulations of Contact Mechanics and Wear of Linearly Reciprocating Block-On-Flat Sliding Test
Simulations of contact mechanics and wear of linearly reciprocating block-on-flat sliding test André Rudnytskyj Mechanical Engineering, master's level (120 credits) 2018 Luleå University of Technology Department of Engineering Sciences and Mathematics Simulations of contact mechanics and wear of linearly reciprocating block-on-flat sliding test Andr´eRudnytskyj Master programme in Tribology of Surfaces and Interfaces - TRIBOS 4th ed. Enrollment Semester Autumn 2016. Department of Engineering Sciences and Mathematics Lule˚aUniversity of Technology ©Lule˚aUniversity of Technology, 2018. This document is freely available at www.ltu.se Preface This master’s thesis was carried out at the Division of Machine Elements, Depart- ment of Engineering Sciences and Mathematics of Lule˚aUniversity of Technology (LTU), in Sweden. It was made possible through the Joint Erasmus Mundus Mas- ter Course (EMMC) TRIBOS (Tribology of Surface and Interfaces), of which I took part in its 4th generation between the years of 2016 to 2018. I would like to thank the Education, Audiovisual and Culture Executive Agency (EACEA) of the European Union and the TRIBOS programme coordinators, pro- fessors, tutors, lecturers, and everyone involved in the programme from the Uni- versity of Leeds (UK), the University of Ljubljana (Slovenia), the University of Coimbra (Portugal), and Lule˚aUniversity of Technology (LTU) for their support inside and outside the classroom. I also thank the people directly involved in the development of the thesis for their helpful support and discussions throughout the time of this work. Andr´eRudnytskyj Lule˚a,June 2018 I Abstract The use of computational methods in tribology can be a valuable approach to deal with engineering problems, ultimately saving time and resources. -
Finite Element Method in Computer Simulation and Engineering
Finite Element Method in Computer Simulation and Engineering Dr. Anna A. Nasedkina [email protected] Institute of Mathematics, Mechanics and Computer Science Southern Federal University Outline of the lecture Computer Aided Engineering and Finite Element Analysis Main concepts of Finite Element Method Overview of Finite Element Software packages 2 Computer Aided Engineering and Finite Element Analysis 3 CAD/CAE/CAM CAD – CAE – CAM – Computer Aided Computer Aided Computer Aided Manufacturing Design Engineering 4 Role of simulation in Engineering: CAD example Boeing 777 First jetliner that is 100% digitally designed using 3D solid technology Throughout the design process, the airplane was "preassembled" on the computer, eliminating the need for a costly, full-scale mock-up (experimental model) $4 billion in CAD infrastructure CAD system: CATIA for design CAE system: ELFINI both by Dassault Systemes (France) 5 Role of simulation in Engineering: CAE example San Francisco Oakland Bay Bridge Seismic analysis of the bridge after the 1989 Loma Prieta earthquake Finite Element model of a section of the bridge subjected to an earthquake load CAE system: ADINA (USA, located in MA) 6 Flow diagram of computer simulation process 7 From physical system to mathematical modeling Idealization: mathematical model, which is an abstraction of physical reality. It is governed by partial differential equations. Modeling can be explicit and implicit. Discretization: numerical method, for example Finite Element Method. Solution: linear system -
INTRODUCTION to COMSOL Multiphysics Introduction to COMSOL Multiphysics
INTRODUCTION TO COMSOL Multiphysics Introduction to COMSOL Multiphysics © 1998–2017 COMSOL Protected by patents listed on www.comsol.com/patents, and U.S. Patents 7,519,518; 7,596,474; 7,623,991; 8,457,932; 8,954,302; 9,098,106; 9,146,652; 9,323,503; 9,372,673; and 9,454,625. Patents pending. This Documentation and the Programs described herein are furnished under the COMSOL Software License Agreement (www.comsol.com/comsol-license-agreement) and may be used or copied only under the terms of the license agreement. COMSOL, the COMSOL logo, COMSOL Multiphysics, COMSOL Desktop, COMSOL Server, and LiveLink are either registered trademarks or trademarks of COMSOL AB. All other trademarks are the property of their respective owners, and COMSOL AB and its subsidiaries and products are not affiliated with, endorsed by, sponsored by, or supported by those trademark owners. For a list of such trademark owners, see www.comsol.com/trademarks. Version: COMSOL 5.3a Contact Information Visit the Contact COMSOL page at www.comsol.com/contact to submit general inquiries, contact Technical Support, or search for an address and phone number. You can also visit the Worldwide Sales Offices page at www.comsol.com/contact/offices for address and contact information. If you need to contact Support, an online request form is located at the COMSOL Access page at www.comsol.com/support/case. Other useful links include: • Support Center: www.comsol.com/support • Product Download: www.comsol.com/product-download • Product Updates: www.comsol.com/support/updates •COMSOL Blog: www.comsol.com/blogs • Discussion Forum: www.comsol.com/community •Events: www.comsol.com/events • COMSOL Video Gallery: www.comsol.com/video • Support Knowledge Base: www.comsol.com/support/knowledgebase Part number: CM010004 Contents Introduction . -
A Rapid Production of Lab-On-A-Chip Biosensors Using 3D Printer and the Sandbox Game, Minecraft
sensors Article MineLoC: A Rapid Production of Lab-on-a-Chip Biosensors Using 3D Printer and the Sandbox Game, Minecraft Kyukwang Kim 1,†, Hyeongkeun Kim 2,† ID , Seunggyu Kim 2 ID and Jessie S. Jeon 2,3,* ID 1 Robotics Program, Korea Advanced Institute of Science and Technology, 291 Daehak-ro, Daejeon 34141, Korea; [email protected] 2 Department of Mechanical Engineering, Korea Advanced Institute of Science and Technology, 291 Daehak-ro, Daejeon 34141, Korea; [email protected] (H.K.); [email protected] (S.K.) 3 KAIST Institute for Health Science and Technology, 291 Daehak-ro, Daejeon 34141, Korea * Correspondence: [email protected]; Tel.: +82-42-350-3226 † These authors contributed equally to this work. Received: 17 April 2018; Accepted: 7 June 2018; Published: 10 June 2018 Abstract: Here, MineLoC is described as a pipeline developed to generate 3D printable models of master templates for Lab-on-a-Chip (LoC) by using a popular multi-player sandbox game “Minecraft”. The user can draw a simple diagram describing the channels and chambers of the Lab-on-a-Chip devices with pre-registered color codes which indicate the height of the generated structure. MineLoC converts the diagram into large chunks of blocks (equal sized cube units composing every object in the game) in the game world. The user and co-workers can simultaneously access the game and edit, modify, or review, which is a feature not generally supported by conventional design software. Once the review is complete, the resultant structure can be exported into a stereolithography (STL) file which can be used in additive manufacturing. -
COMSOL Multiphysics Version 4.3 Contains Many New Functions and Additions to the COMSOL Product Suite
COMSOL Multiphysics ® Release Notes VERSION 4.3 COMSOL Multiphysics Release Notes 1998–2012 COMSOL Protected by U.S. Patents 7,519,518; 7,596,474; and 7,623,991. Patents pending. This Documentation and the Programs described herein are furnished under the COMSOL Software License Agreement (www.comsol.com/sla) and may be used or copied only under the terms of the license agree- ment. COMSOL, COMSOL Desktop, COMSOL Multiphysics, and LiveLink are registered trademarks or trade- marks of COMSOL AB. Other product or brand names are trademarks or registered trademarks of their respective holders. Version: May 2012 COMSOL 4.3 Contact Information Visit www.comsol.com/contact for a searchable list of all COMSOL offices and local representatives. From this web page, search the contacts and find a local sales representative, go to other COMSOL websites, request information and pricing, submit technical support queries, subscribe to the monthly eNews email newsletter, and much more. If you need to contact Technical Support, an online request form is located at www.comsol.com/support/contact. Other useful links include: • Technical Support www.comsol.com/support • Software updates: www.comsol.com/support/updates • Online community: www.comsol.com/community • Events, conferences, and training: www.comsol.com/events • Tutorials: www.comsol.com/products/tutorials • Knowledge Base: www.comsol.com/support/knowledgebase Part No. CM010001 1 Release Notes COMSOL Multiphysics version 4.3 contains many new functions and additions to the COMSOL product suite. These Release Notes provide information regarding new functionality in existing products and an overview of new products. We have strived to achieve backward compatibility with the previous version and to include all functionality that is available there.