Advances in Printing and Media Technology
Total Page:16
File Type:pdf, Size:1020Kb
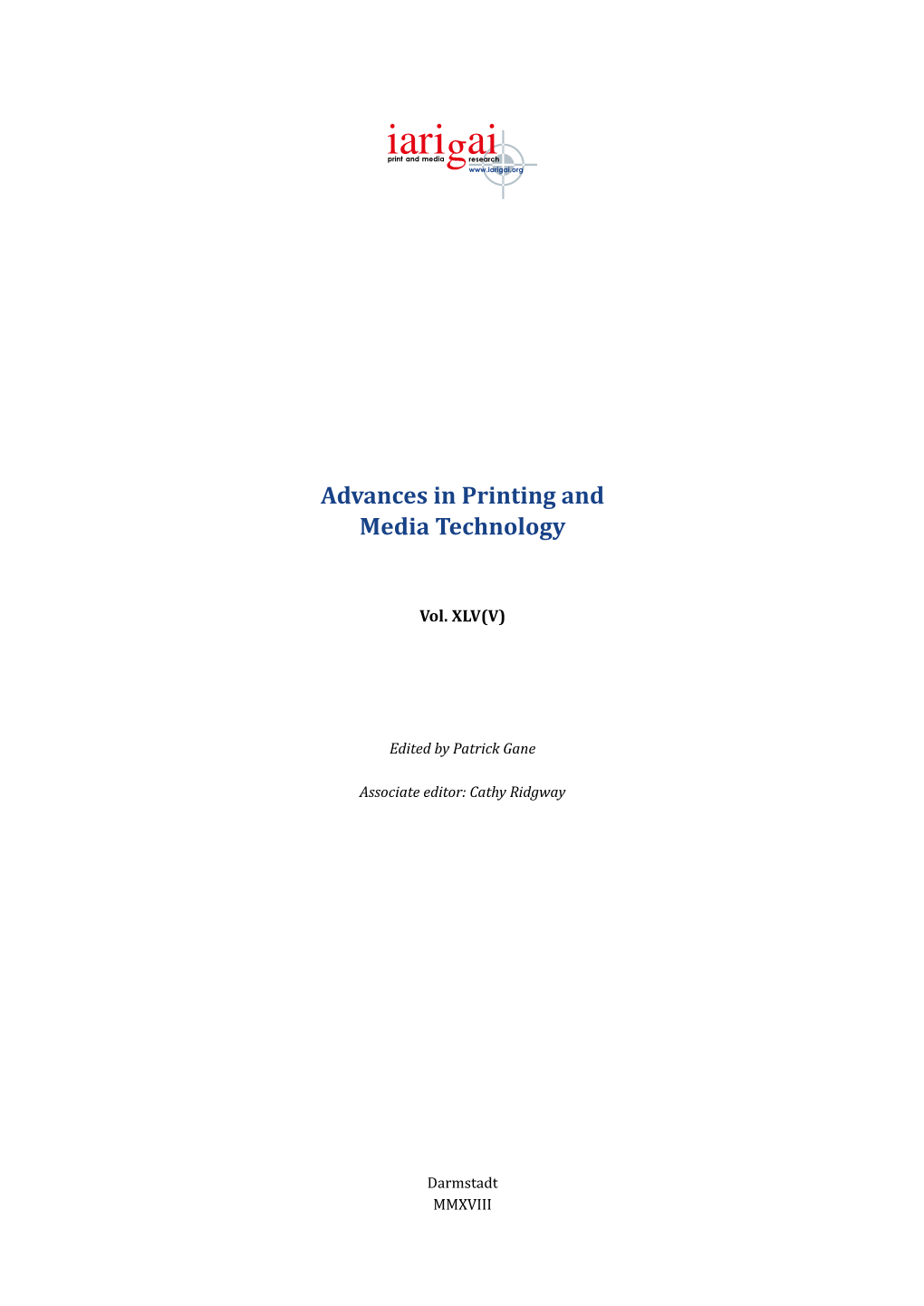
Load more
Recommended publications
-
GCLC-BT Conference 5 December 2005, London Competition Law and Media Content
GCLC-BT Conference 5 December 2005, London Competition Law and Media Content I. MORNING SESSION 9:00 – 9:10 General introduction to the conference Damien Geradin Director of the GCLC Paolo Palmigiano Head of Competition and Regulatory Law, BT Retail 9:10 – 9:30 Welcome words Dan Marks CEO TV Services, BT Paolo Palmigiano Head of Competition and Public Law, BT Retail SESSION 1: THE LAW AND ECONOMICS OF MEDIA CONTENT 9:30 – 10:00 The economics of media content Stefan Szymanski Professor of Economics, Tanaka Business School, Imperial College London 10:00 – 10:30 Overview of the legal framework applicable to the media content Romano Subiotto Partner, Cleary Gottlieb 10:30 – 10:50 Coffee break SESSION 2: REGULATORY AND COMPETITION LAW APPROACHES TO MEDIA CONTENT IN THE EU, THE UK, AND THE US 10:50 – 11:10 The situation in the EU Speaker from the European Commission to be advised 11:10 – 11:30 The situation in the UK Becket McGrath Partner, Berwin Leighton Paisner 11:30 – 11:50 The situation in the US John Thorne Deputy General Counsel, Verizon 11:50 – 12:20 Roundtable discussion 12:20 – 13:30 Lunch break II. AFTERNOON SESSION 13:30 – 13:50 Tomorrow’s world – How will the media content industry look like in the future SESSION 3: CURRENT ISSUES REGARDING MEDIA CONTENT Chairman: Bernard Amory, Partner, Jones Day 13:50 – 14:10 Competition law issues raised by exclusivity Didier Théophile Partner, Darrois, Villey, Maillot et Brochier 14:10 – 14:30 Cross platform bundling of rights Andrea Appella Vice President & Associate General Counsel - Time Warner Europe 14:30 – 14:50 Collective selling and buying of premium content rights Helmut Brockelman Partner, Martinez Lage & Associados 14: 50 – 15:20 Commentators Dr. -
Open Society Archives
OSA book OSA / Publications OPEN SOCIETY ARCHIVES Open Society Archives Edited by Leszek Pudlowski and Iván Székely Published by the Open Society Archives at Central European University Budapest 1999 Copyright ©1999 by the Open Society Archives at Central European University, Budapest English Text Editor: Andy Haupert ISBN 963 85230 5 0 Design by Tamás Harsányi Printed by Gábor Rózsa Printing House, Budapest on Niveus acid-free offset printing paper of 90g/m2 produced by Neusiedler Szolnok Paper Mill, Hungary. This paper meets the requirements of ISO9706 standard. TABLE OF CONTENTS CHAPTER I. The coordinates of the Archives The enemy-archives (István Rév) 14 Archival parasailing (Trudy Huskamp Peterson) 20 Access to archives: a political issue (Charles Kecskeméti) 24 The Open Society Archives: a brief history (András Mink) 30 CHAPTER II. The holdings Introduction 38 http://www.osaarchivum.org/files/1999/osabook/BookText.htm[31-Jul-2009 08:07:32] OSA book COMMUNISM AND COLD WAR 39 Records of the Research Institute of Radio Free Europe/Radio Liberty 39 • The Archives in Munich (András Mink) 39 • Archival arrangement and structure of the records of Radio Free Europe/Radio Liberty Research Institute (Leszek Pud½owski) 46 • The Information Resources Department 49 The East European Archives 49 Records of the Bulgarian Unit (Olga Zaslavskaya) 49 Records of the Czechoslovak Unit (Pavol Salamon) 51 Records of the Hungarian Unit (Csaba Szilágyi) 55 Records of the Polish Unit (Leszek Pud½owski) 58 Records of the Polish Underground Publications Unit -
Introduction to Printing Technologies
Edited with the trial version of Foxit Advanced PDF Editor To remove this notice, visit: www.foxitsoftware.com/shopping Introduction to Printing Technologies Study Material for Students : Introduction to Printing Technologies CAREER OPPORTUNITIES IN MEDIA WORLD Mass communication and Journalism is institutionalized and source specific. Itfunctions through well-organized professionals and has an ever increasing interlace. Mass media has a global availability and it has converted the whole world in to a global village. A qualified journalism professional can take up a job of educating, entertaining, informing, persuading, interpreting, and guiding. Working in print media offers the opportunities to be a news reporter, news presenter, an editor, a feature writer, a photojournalist, etc. Electronic media offers great opportunities of being a news reporter, news editor, newsreader, programme host, interviewer, cameraman,Edited with theproducer, trial version of Foxit Advanced PDF Editor director, etc. To remove this notice, visit: www.foxitsoftware.com/shopping Other titles of Mass Communication and Journalism professionals are script writer, production assistant, technical director, floor manager, lighting director, scenic director, coordinator, creative director, advertiser, media planner, media consultant, public relation officer, counselor, front office executive, event manager and others. 2 : Introduction to Printing Technologies INTRODUCTION The book introduces the students to fundamentals of printing. Today printing technology is a part of our everyday life. It is all around us. T h e history and origin of printing technology are also discussed in the book. Students of mass communication will also learn about t h e different types of printing and typography in this book. The book will also make a comparison between Traditional Printing Vs Modern Typography. -
Fine Art Papers Guide
FINE ART PAPERS GUIDE 100 Series • 200 Series • Vision • 300 Series • 400 Series • 500 Series make something real For over 125 years Strathmore® has been providing artists with the finest papers on which to create their artwork. Our papers are manufactured to exacting specifications for every level of expertise. 100 100 Series | Youth SERIES Ignite a lifelong love of art. Designed for ages 5 and up, the paper types YOUTH and features have been selected to enhance the creative process. Choice of paper is one of the most important 200 Series | Good decisions an artist makes 200SERIES Value without compromise. Good quality paper at a great price that’s economical enough for daily use. The broad range of papers is a great in determining the GOOD starting point for the beginning and developing artist. outcome of their work. Color, absorbency, texture, weight, and ® Vision | Good STRATHMORE size are some of the more important Let the world see your vision. An affordable line of pads featuring extra variables that contribute to different high sheet counts and durable construction. Tear away fly sheets reveal a artistic effects. Whether your choice of vision heavyweight, customizable, blank cover made from high quality, steel blue medium is watercolor, charcoal, pastel, GOOD mixed media paper. Charcoal Paper in our 300, 400 and 500 Series is pencil, or pen and ink, you can be confident that manufactured with a traditional laid finish making we have a paper that will enhance your artistic them the ideal foundation for this medium. The efforts. Our papers are manufactured to exacting laid texture provides a great toothy surface for specifications for every level of expertise. -
Sustainable Alternatives to Industrial Printing Practices: a Case Study Analysis of Esquire Magazine and Electronic Paper Display
Sustainable Alternatives to Industrial Printing Practices: A Case Study Analysis of Esquire Magazine and Electronic Paper Display Christopher Moore, Concordia University, Montreal, [email protected] Abstract In October 2008, Esquire magazine became the first commercial publisher to utilize electronic paper display technology (EPD) for mass production and distribution of printed ephemera. Initially developed at the MIT Media Lab in 1997, E Ink displays have been integrated into a variety of hardware devices, including the Amazon Kindle and Sony Reader. However, the Esquire cover represents a milestone achievement in the evolution of a more sustainable, paperless print solution due to the medium’s flexible nature, low power consumption, and limited circuitry requirements. 100,000 copies were sold on newsstands for the regular cover price of $5.99 USD, proving both the economic viability and flexible application of the technology, which is impervious to ambient lighting conditions and adaptable to multiple modalities. This paper outlines the key features and benefits of E Ink, as well as the critical challenges impeding widespread adoption of EPD. Keywords Sustainable design (primary keyword); design and society; eco-design; communication and information; case study/studies In response to political and consumer pressures, traditional print industries have increasingly adapted production methods to utilize more ecologically conscientious practices. Transitions to vegetable dyes, post-consumer fibres and dissolved air flotation de-inking processes have contributed to reduced environmental consequences from the paper and printing industries, but the overall output of ephemera has remained largely unchanged. The secondary carbon offset resulting from energy consumption and chemical disposal in the recycling and transportation of printed matter needs to be reconciled with advancements made in material technologies, and our cultural desire for tangible media. -
Northern Kentucky MARKET REVIEW 2019
Northern Kentucky MARKET REVIEW 2019 BRIDGES TO THE FUTURE Northern Kentucky’s transformation creates new paths for prosperity, growth and opportunity Underwritten by KY 40150 KY Lebanon Junction Lebanon Permit #327 #327 Permit Published by PAID ELECTRONIC SERVICE REQUESTED SERVICE ELECTRONIC U.S. POSTAGE U.S. PRST STD PRST 601 W. Short St., Lexington KY 40508 KY Lexington St., Short W. 601 $12 GREAT THINGS Accessibility, talent and financial COME resources, broad amenities and a low cost of living make Northern Kentucky an ideal place to start FROM and grow a business. NORTH ERERNKEN N TUCKY NorthernKentuckyUSA.com Northern Kentucky MARKET REVIEW 2019 Made in NKY ...............................................................53 Table of Contents Utilities ...............................................................................57 People & Places ..................................................6 Business Services .......................................................58 Northern Kentucky Tri-ED ................................12 Headquarters ..............................................................60 NKY Chamber of Commerce........................14 Meetings & Attractions .........................................62 Northern Kentucky Arts & Culture ............................................................65 On the Cover: From left: Katie Meyer, Mandy Lehman, Area Development District ......................16 Sports & Recreation ...............................................68 Bonnie Meyer, Gordon Henry, Shwetha T. Pai, -
& Who's Who in Printing 2018 Printing Impressions
2018 Printing Impressions 35th Annua l Ranking & Who’s Who in Printing PIworld.com | Printing Impressions 1 2018 PRINTING IMPRESSIONS Celebrating its 35th consecutive year, the PRINTING IMPRESSIONS 400 provides the industry’s most comprehensive listing 35th Annua of the leading printing companies in the l Ranking United States and Canada ranked by annual sales volume. The listings include company name and the their annual revenue figures, so they are not location of the headquarters; parent company, included on our PI 400 list. This year, based if applicable; current and previous year’s rank- on Forbes’ ranking of the largest privately-held ings; most recent and previous fiscal year sales companies, we included Taylor Corp. and figures; percentage change in sales; primary used Forbes’ estimated sales calculation. product specialties; principal officer(s); number In addition, some very large firms that are of employees and manufacturing plants; as well ranked, notably RR Donnelley, would not, as the firm’s total range of in-house sheetfed or could not, break down their annual sales and webfed digital and conventional printing by the various print market specialties that process capabilities. we track (so, they may not appear on some of The financial information shown for the our Top 5 market segment leaders charts). PI 400 rankings was provided voluntarily by Individual printing companies that are privately-held and employee-owned firms, part of larger graphic arts networks are not and we instructed companies to not provide listed separately. In essence, to do so would be projected/estimated sales figures if their fiscal to show sales figures twice. -
The Next Production Revolution
The Next Production Revolution IMPLICAtiONS FOr GOVErnMEntS AND BUSinESS The Next Production Revolution IM P L I CA ti O N S FO S r GOVE rn ME nt S A S N D BUS in ESS The Next Production Revolution IMPLICATIONS FOR GOVERNMENTS AND BUSINESS This report, except Chapters 2 and 5, was approved and declassified by the OECD Committee for Scientific and Technological Policy (CSTP) on 17 April 2017 by written procedure. Chapter 2 was approved and declassified by the Committee for Digital Economy Policy on 12 February 2017 by written procedure. Chapter 5 was approved and declassified by the Environment Policy Committee on 30 January 2017. The report was prepared for publication by the OECD Secretariat. This document, as well as any data and any map included herein, are without prejudice to the status of or sovereignty over any territory, to the delimitation of international frontiers and boundaries and to the name of any territory, city or area. Please cite this publication as: OECD (2017), The Next Production Revolution: Implications for Governments and Business, OECD Publishing, Paris. http://dx.doi.org/10.1787/9789264271036-en ISBN 978-92-64-27099-2 (print) ISBN 978-92-64-27103-6 (PDF) ISBN 978-92-64-27115-9 (ePub) The statistical data for Israel are supplied by and under the responsibility of the relevant Israeli authorities. The use of such data by the OECD is without prejudice to the status of the Golan Heights, East Jerusalem and Israeli settlements in the West Bank under the terms of international law. Photo credits: Cover © Willyam Bradberry/Shutterstock.com. -
E-Paper Technology
Special Issue - 2016 International Journal of Engineering Research & Technology (IJERT) ISSN: 2278-0181 NSDMCC - 2015 Conference Proceedings E-Paper Technology Anitta Joseph Vth Semester B.Sc. Computer Science Vimala College, Thrissur Abstract: Made of flexible material, requiring ultra-low These limitations include the backlighting of monitors power consumption, cheap to manufacture, and most which is hard on the human eye, while electronic paper importantly, easy and convenient to read, E-papers of the reflects light just like normal paper. In addition, e-paper is future are just around the corner, with the promise to hold easier to read at an angle than flat screen monitors. libraries on a chip and replace most printed newspapers Electronic paper also has the potential to be flexible before the end of the next decade.Electronic paper(E-paper) is a portable. Reusable storage and display medium that looks becauseit is made of plastic. It is also light and potentially like paper but can be repeatedly written on (refreshed) by inexpensive. electronic means, thousands or millions of times. E-paper will be used for applications such as e-books, electronics II. TECHNOLOGY BEHIND E_PAPER newspaper, portable signs, & foldable, rollable displays. Information to be displays is downloaded through a The E-Paper is also called Electronic Paper or Electronic connection to a computer or a cell phone, or created with ink Display. The first E-Paper was developed in 1974’s by mechanical tools such as an electronic “pencil”. This paper Nicholas K Sheridon at Xerox’s Palo Alto research centre. discusses the history, features, and technology of the electronic paper revolution. -
Research on Information Industry Innovation Model Under the Background of Integration of Industrialization and Informatization
·588· Proceedings of the 7th International Conference on Innovation & Management Research on Information Industry Innovation Model under the Background of Integration of Industrialization and Informatization Huang Jinsong School of Economics, Huazhong University of Science and Technology, Wu Han, P.R.China, 430074, (E-mail: [email protected]) Abstract The development of information industry innovation is an important driving force to promote adjustment of national industrial structure, the integration of industrialization and informatization has brought new opportunities and challenges to the development of information industry innovation. This paper defines the basic content of the information industry innovation, describes the relationship among integration of industrialization, informatization and information industry innovation, based on which analyses main content and models of the information industry innovation. Key words Integration of industrialization and informatization; Information industry; Innovation 1 Introduction It is a hot new research on industry innovation. Different scholars from different angles gave various interpretations on the connotation of industry innovation. It is generally believed that the concept of industry innovation was first proposed by the British economist, Freeman (1997)[1]. He believed that industry innovation including skills and technology innovation, product innovation, process innovation and management innovation and market innovation. Industry innovation includes sub-macro and micro -
Open Kuehn Dissertation Final Draft.Pdf
The Pennsylvania State University The Graduate School College of Communications PROSUMER-CITIZENSHIP AND THE LOCAL: A CRITICAL CASE STUDY OF CONSUMER REVIEWING ON YELP.COM A Dissertation in Mass Communications by Kathleen M. Kuehn © 2011 Kathleen M. Kuehn Submitted in Partial Fulfillment of the Requirements for the Degree of Doctor of Philosophy August 2011 The dissertation of Kathleen Kuehn was reviewed and approved* by the following: Patrick Parsons Professor of Telecommunications Dissertation Adviser Chair of Committee Michael Elavsky Assistant Professor of Film/Media Studies Matthew P. McAllister Professor of Film/Media Studies Michelle Miller-Day Associate Professor of Communication Arts and Sciences Marie Hardin Associate Professor of Journalism Associate Dean for Graduate Studies and Research *Signatures are on file in the Graduate School. ii ABSTRACT Over the past few years, content developers searching for new markets have found a potentially lucrative consumer base in local and location-based services as new media platforms have begun to “expand” their focus to hyper-local place-based communities. This shift to “local 2.0” has given birth to “local listing sites,” an emerging social medium that converges the content of traditional Yellow Pages, consumer-generated content and the interactive features of social network sites. Such sites harness the productive power of “prosumers,” the hybrid subjectivity of new media users who simultaneously produce and consume online content (Tapscott & Williams, 2006). These sites capitalize on the productivity of users who create discourses through and about local consumption by voluntarily rating and reviewing local businesses and services, challenging the power of institutions traditionally responsible for the production of consumer culture and reputation management (e.g., local business owners, marketers, advertisers, professional critics). -
Title Historical Value of Parabaik and Pei All Authors Moe Moe Oo Publication Type Local Publication Publisher (Journal Name, Is
Title Historical Value of Parabaik and Pei All Authors Moe Moe Oo Publication Type Local Publication Publisher (Journal name, Meiktila University, Research Journal, Vol.IV, No.1, 2013 issue no., page no etc.) Parabaiks and Palm Leaf Manuscripts are important in the rich and old tradition and cultural history of Southeast Asia. Many documents reflected the socio- economic situation and Buddhist text of ancient Myanmar. These sources are Abstract like a treasure-trove for historians. We hope that this Parabaik and Palm leaf will advance the study of the early modern history of Myanmar, as well as that of the whole Southeast Asian region, and will also contribute to the preservation of a valuable cultural heritage in Myanmar. cultural heritage, preservation Keywords Citation Issue Date 2013 61 Meiktila University, Research Journal, Vol.IV, No.1, 2013 Historical Value of Parabaik and Pei Moe Moe Oo1 Abstract Parabaiks and Palm Leaf Manuscripts are important in the rich and old tradition and cultural history of Southeast Asia. Many documents reflected the socio-economic situation and Buddhist text of ancient Myanmar. These sources are like a treasure-trove for historians. We hope that this Parabaik and Palm leaf will advance the study of the early modern history of Myanmar, as well as that of the whole Southeast Asian region, and will also contribute to the preservation of a valuable cultural heritage in Myanmar. Key Words: cultural heritage, preservation Introduction Myanmar Manuscripts are an attempt to deal with the socio- economic life of the people during the Kon-baung period. There are many books both published and unpublished in the forms of research journal and thesis.