Interaction of Liquid Droplets with Low-Temperature, Low-Pressure Plasma
Total Page:16
File Type:pdf, Size:1020Kb
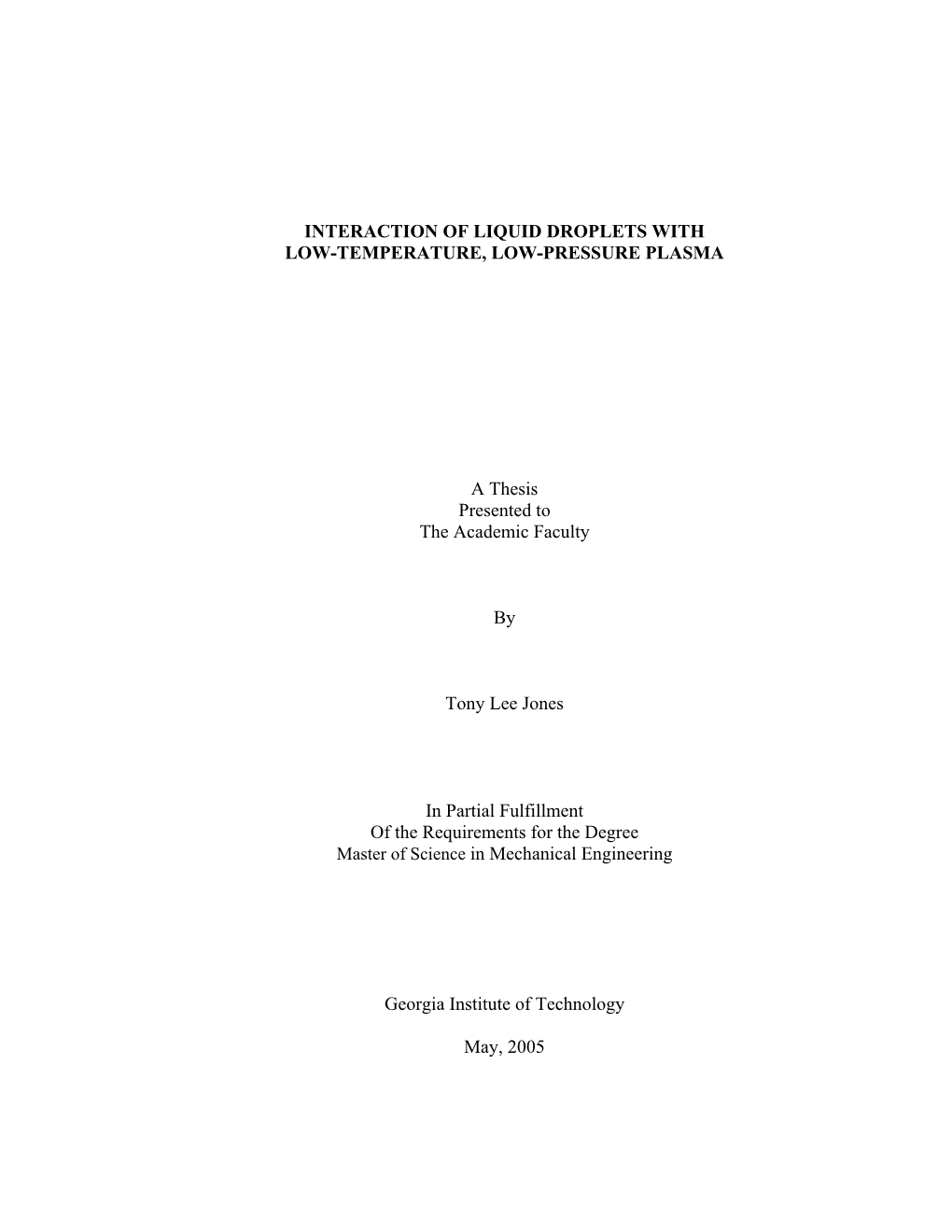
Load more
Recommended publications
-
Synthesis, Structure and Properties of Metal Oxychalcogenides
Durham E-Theses Synthesis, Structure and Properties of Metal Oxychalcogenides TUXWORTH, ANDREW,JAMES How to cite: TUXWORTH, ANDREW,JAMES (2014) Synthesis, Structure and Properties of Metal Oxychalcogenides, Durham theses, Durham University. Available at Durham E-Theses Online: http://etheses.dur.ac.uk/9497/ Use policy The full-text may be used and/or reproduced, and given to third parties in any format or medium, without prior permission or charge, for personal research or study, educational, or not-for-prot purposes provided that: • a full bibliographic reference is made to the original source • a link is made to the metadata record in Durham E-Theses • the full-text is not changed in any way The full-text must not be sold in any format or medium without the formal permission of the copyright holders. Please consult the full Durham E-Theses policy for further details. Academic Support Oce, Durham University, University Oce, Old Elvet, Durham DH1 3HP e-mail: [email protected] Tel: +44 0191 334 6107 http://etheses.dur.ac.uk Abstract “Synthesis, Structure and Properties of Metal Oxychalcogenides” PhD Thesis Andrew J. Tuxworth December 2013 Chapter 1 gives a brief review of oxychalcogenide materials and their properties, with particular focus on structures similar to the systems discussed in the later chapters. These oxychalcogenides, are of interest due to their potentially interesting magnetic and electronic properties. Chapter 2 discusses the synthetic methods and characterisation techniques used throughout this thesis. The theory behind both single crystal and powder diffraction techniques used in this work is described. Chapter 3 describes the synthesis of a new ZrCuSiAs-related transition metal containing oxychalcogenide La2O2ZnSe2. -
Curriculum Vitae Mercouri G
CURRICULUM VITAE MERCOURI G. KANATZIDIS Department of Chemistry, Northwestern University, Evanston, IL 60208 Phone 847-467-1541; Fax 847-491-5937; Website: http://chemgroups.northwestern.edu/kanatzidis/ Birth Date: 1957; Citizenship: US EXPERIENCE 8/06-Present: Professor of Chemistry, Northwestern University and Senior Scientist , Argonne National Laboratory, Materials Science Division, Argonne, IL 7/93-8/06: Professor of Chemistry, Michigan State University 7/91-6/93: Associate Professor, Michigan State University 7/87-6/91: Assistant Professor, Michigan State University EDUCATION Postdoctoral Fellow, 1987, Northwestern University Postdoctoral Associate, 1985, University of Michigan Ph.D. Inorganic Chemistry, 1984, University of Iowa B.S. Chemistry, November 1979, Aristotle University of Thessaloniki AWARDS • Presidential Young Investigator Award, National Science Foundation, 1989-1994 • ACS Inorganic Chemistry Division Award, EXXON Faculty Fellowship in Solid State Chemistry, 1990 • Beckman Young Investigator , 1992-1994 • Alfred P. Sloan Fellow, 1991-1993 • Camille and Henry Dreyfus Teacher Scholar, 1993-1998 • Michigan State University Distinguished Faculty Award, 1998 • Sigma Xi 2000 Senior Meritorious Faculty Award • University Distinguished Professor MSU, 2001 • John Simon Guggenheim Foundation Fellow, 2002 • Alexander von Humboldt Prize, 2003 • Morley Medal, American Chemical Society, Cleveland Section, 2003 • Charles E. and Emma H. Morrison Professor, Northwestern University, 2006 • MRS Fellow, Materials Research Society, 2010 • AAAS Fellow, American Association for the Advancment of Science, 2012 • Chetham Lecturer Award, University of California Santa Barbara, 2013 • Einstein Professor, Chinese Academy of Sciences, 2014 • International Thermoelectric Society Outstanding Achievement Award 2014 • MRS Medal 2014 • Royal Chemical Society DeGennes Prize 2015 • Elected Fellow of the Royal Chemical Society 2015 • ENI Award for the "Renewable Energy Prize" category • ACS Award in Inorganic Chemistry 2016 • American Physical Society 2016 James C. -
Layered Oxychalcogenides: Structural Chemistry and Thermoelectric Properties
CORE Metadata, citation and similar papers at core.ac.uk Provided by Elsevier - Publisher Connector Available online at www.sciencedirect.com ScienceDirect J Materiomics 2 (2016) 131e140 www.ceramsoc.com/en/ www.journals.elsevier.com/journal-of-materiomics/ Layered oxychalcogenides: Structural chemistry and thermoelectric properties Son D.N. Luu a,b, Paz Vaqueiro b,* a Institute of Chemical Sciences, Heriot-Watt University, Edinburgh, EH14 4AS, UK b Department of Chemistry, University of Reading, Whiteknights, Reading, RG6 6AD, UK Received 16 February 2016; revised 18 March 2016; accepted 3 April 2016 Available online 8 April 2016 Abstract Layered oxychalcogenides have recently emerged as promising thermoelectric materials. The alternation of ionic oxide and covalent chalcogenide layers found in these materials often results in interesting electronic properties, and also facilitates the tuning of their properties via chemical substitution at both types of layers. This review highlights some common structure types found for layered oxychalcogenides and their interrelationships. This review pays special attention to the potential of these materials for thermoelectric applications, and provides an overview of the thermoelectric properties of materials of current interest, including BiCuSeO. © 2016 The Chinese Ceramic Society. Production and hosting by Elsevier B.V. This is an open access article under the CC BY-NC-ND license (http://creativecommons.org/licenses/by-nc-nd/4.0/). Keywords: Oxychalcogenides; Layered structures; Thermoelectric; -
Layered Oxychalcogenides: Structural Chemistry and Thermoelectric Properties
Layered oxychalcogenides: structural chemistry and thermoelectric properties Article Accepted Version Creative Commons: Attribution-Noncommercial-No Derivative Works 4.0 Luu, S. D. N. and Vaqueiro, P. (2016) Layered oxychalcogenides: structural chemistry and thermoelectric properties. Journal of Materiomics, 2 (2). pp. 131-140. ISSN 2352-8478 doi: https://doi.org/10.1016/j.jmat.2016.04.002 Available at http://centaur.reading.ac.uk/62768/ It is advisable to refer to the publisher’s version if you intend to cite from the work. See Guidance on citing . To link to this article DOI: http://dx.doi.org/10.1016/j.jmat.2016.04.002 Publisher: Elsevier All outputs in CentAUR are protected by Intellectual Property Rights law, including copyright law. Copyright and IPR is retained by the creators or other copyright holders. Terms and conditions for use of this material are defined in the End User Agreement . www.reading.ac.uk/centaur CentAUR Central Archive at the University of Reading Reading’s research outputs online Layered oxychalcogenides: structural chemistry and thermoelectric properties Son D N Luu1,2, Paz Vaqueiro2* 1Institute of Chemical Sciences, Heriot-Watt University, Edinburgh, EH14, 4AS, UK 2Department of Chemistry, University of Reading, Whiteknights, Reading, RG6 6AD, UK Abstract Layered oxychalcogenides have recently emerged as promising thermoelectric materials. The alternation of ionic oxide and covalent chalcogenide layers found in these materials often results in interesting electronic properties, and also facilitates the tuning of their properties via chemical substitution at both types of layers. This review highlights some common structure types found for layered oxychalcogenides and their interrelationships. This review pays special attention to the potential of these materials for thermoelectric applications, and provides an overview of the thermoelectric properties of materials of current interest, including BiCuSeO. -
Download Article (PDF)
Z. Kristallogr. 226 (2011) 435–446 / DOI 10.1524/zkri.2011.1363 435 # by Oldenbourg Wissenschaftsverlag, Mu¨nchen Structural chemistry of superconducting pnictides and pnictide oxides with layered structures Dirk JohrendtI, Hideo HosonoII, Rolf-Dieter HoffmannIII and Rainer Po¨ttgen*, III I Department Chemie und Biochemie, Ludwig-Maximilians-Universita¨t Mu¨nchen, Butenandtstraße 5–13 (Haus D), 81377 Mu¨nchen, Germany II Frontier Research Center, Tokyo Institute of Technology, 4259 Nagatsuta, Midori-ku, Yokohama 226-8503, Japan III Institut fu¨r Anorganische und Analytische Chemie, Universita¨t Mu¨nster, Corrensstraße 30, 48149 Mu¨nster, Germany Received October 29, 2010; accepted February 6, 2011 Pnictide / Pnictide oxide / Superconductivity / for hydride formation of CeRuSi ! CeRuSiH [6] and Intermetallics / Group-subgroup relation CeRuGe ! CeRuGeH [7]. The crystal chemical data of the huge number of ZrCuSiAs materials have recently Abstract. The basic structural chemistry of supercon- been reviewed [8]. ducting pnictides and pnictide oxides is reviewed. Crystal Although the basic crystallographic data of the many chemical details of selected compounds and group sub- ThCr2Si2 and ZrCuSiAs type compounds are known for group schemes are discussed with respect to phase transi- several years, especially for the ZrCuSiAs family, systema- tions upon charge-density formation, the ordering of va- tic property studies have been performed only recently. cancies, or the ordered displacements of oxygen atoms. These investigations mainly focused on p-type transparent Furthermore, the influences of doping and solid solutions semiconductors like LaCuSO (for a review see [9]) or the on the valence electron concentration are discussed in or- colored phosphide and arsenide oxides REZnPO [10] and der to highlight the structural and electronic flexibility of REZnAsO [11]. -
IONIZATION ENERGIES of GAS-PHASE MOLECULES Sharon G
IONIZATION ENERGIES OF GAS-PHASE MOLECULES Sharon G. Lias This table presents values for the first ionization energies (IP) of approximately 1000 molecules and atoms. Substances are listed by molecular formula in the modified Hill order (see introduction). Values enclosed in parentheses are considered not to be well established. Data appearing in the 1988 reference, were updated in 1996 for inclusion in the database of ionization energies available at the Internet site of the Standard Reference Data program of the National Institute of Standards and Technology (http://webbook.nist.gov). The list appearing here includes these updates. ∆ The list also includes values for enthalpies of formation of the ions at 298 K, fHion, given according to the ion convention used by mass ∆ spectrometrists; to convert these values to the electron convention used by thermodynamicists, add 6 kJ/mol. Details on the calculation of fHion as well as data for a much larger number of molecules, may be found in the reference and on the Internet site. REFERENCE Lias, S.G., Bartmess, J.E., Liebman, J.F., Holmes, J.L., Levin, R.D., and Mallard, W.G., Gas-Phase Ion and Neutral Thermochemistry, J. Phys. Chem. Ref. Data, Vol. 17, Suppl. No. 1, 1988. ∆ Mol. f Hion Form. Name IP/eV kJ/mol Substances not containing carbon Ac Actinium 5.17 905 Ag Silver 7.57624 1016 AgCl Silver(I) chloride (≤ 10.08) ≤ 1065 AgF Silver(I) fluoride (11.0 ± 0.3) 1071 Al Aluminum 5.98577 905 AlBr Aluminum monobromide (9.3) 913 AlBr3 Aluminum tribromide (10.4) 593 AlCl Aluminum monochloride 9.4 -
Aleksi Matikainen MIXED-ANION COMPOUNDS
Aleksi Matikainen MIXED-ANION COMPOUNDS: AN UNEXPLORED ALD PLAYGROUND FOR APPLICATIONS Master´s Programme in Chemical, Biochemical and Materials Engineering Major in Chemistry Master’s thesis for the degree of Master of Science in Technology submitted for inspection, Espoo, 9 July, 2018. Supervisor Professor Maarit Karppinen Instructor Ph. D. Tripurari Sharan Tripathi Aalto University, P.O. BOX 11000, 00076 AALTO www.aalto.fi Abstract of master's thesis Author Aleksi Matikainen Title of thesis Mixed-anion compounds: An unexplored ALD playground for applications Degree Programme Master’s programme in Chemical, Biochemical and Materials Engineering Major Chemistry Thesis supervisor Professor Maarit Karppinen Thesis advisor(s) / Thesis examiner(s) PhD Tripurari Sharan Tripathi Date 09.07.2018 Number of pages 89 Language English Abstract Mixed-anion compounds, such as oxypnictides and oxychalcogenides, are an emerging research subject as functional solid-state materials. Their structures are more complex compared with traditional oxides, which provides novel building blocks for new functional materials. Potential applications include transparent electronics, photovoltaics and thermoelectrics. Atomic layer deposition (ALD) is a possible solution for fabricating mixed-anion thin films with superior properties to bulk mixed-anion compounds. Oxysulfides are an interesting group of mixed-anion compounds with desirable electrical properties and an inexpensive and non-toxic composition of earth-abundant elements. Their layered structure induces several intriguing properties such as superconductivity, transparent p-type semiconductivity and wide band gap. Only a few oxysulfides have been fabricated with ALD before. In this work, a novel atomic layer deposition process for fabricating oxysulfide LaOCuS (lanthanum oxide copper sulfide) thin films was implemented. -
Design and Synthesis of Perovskites and Corundum Derivatives with Unusual Magnetic, Electronic, and Structural Coupling
© 2021 Corey Frank ALL RIGHTS RESERVED DESIGN AND SYNTHESIS OF PEROVSKITES AND CORUNDUM DERIVATIVES WITH UNUSUAL MAGNETIC, ELECTRONIC, AND STRUCTURAL COUPLING By Corey Elizabeth Frank A dissertation submitted to the School of Graduate Studies Rutgers, The State University of New Jersey in partial fulfillment of the requirements for the degree of Doctor of Philosophy Graduate Program in Chemistry Written under the direction of Professor Martha Greenblatt and approved by ______________________________ ______________________________ ______________________________ ______________________________ New Brunswick, NJ January 2021 ABSTRACT OF THE DISSERTATION Design and Synthesis of Perovskites and Corundum Derivatives with Unusual Magnetic, Electronic, and Structural Coupling By Corey Elizabeth Frank Dissertation Director: Martha Greenblatt ABO3 perovskites and derivative structures are versatile materials, critical to the function of modern life, and the discovery of new perovskites is essential to developing the fields of photovoltaics, microelectronics, and telecommunication (푟 +푟 ) among others. The Goldschmidt tolerance factor (푡 = 퐴 푥 ) has been used for √2(푟퐵+푟푥) years to qualitatively predict stable perovskites; this formula predicts that with small A-cations (effective ionic radius < 0.9 Å) and B transition metal B-cations the perovskite structure will not form. With careful synthesis techniques, and the application of high pressure, this limitation can be overcome, unlocking distorted materials with interesting electronic-magnetic-structural coupling behaviors. These materials include highly distorted transition metal only double perovskites, such as Mn2CoReO6; quadruple perovskites with a square-planar coordinated A’ cation, such as La3Mn4RhO12; and even double corundum derivatives which feature face-sharing dimers of octahedrally coordinated A and B cations, such as Fe3-xInSnxO6 (x = 0, 0.25, 0.5) and In2Mn1.1Sn0.9O6. -
Arxiv:1704.01441V1 [Cond-Mat.Str-El] 5 Apr 2017 Tronic, Magnetic, and Structural Properties They Possess
The magnetic and electronic properties of Oxyselenides - influence of transition metal ions and lanthanides C. Stock1 and E. E. McCabe2 1School of Physics and Astronomy, University of Edinburgh, Edinburgh EH9 3FD, UK 2School of Physical Sciences, University of Kent, Canterbury, CT2 7NH, UK (Dated: October 15, 2018) Magnetic oxyselenides have been a topic of research for several decades, firstly in the context of photoconductivity and thermoelectricity owing to their intrinsic semiconduct- ing properties and ability to tune the energy gap through metal ion substitution. More recently, interest in the oxyselenides has experienced a resurgence owing to the possible relation to strongly correlated phenomena given the fact that many oxyselenides share a similar structure to unconventional superconducting pnictides and chalcogenides. The two dimensional nature of many oxyselenide systems also draws an analogy to cuprate physics where a strong interplay between unconventional electronic phases and localised magnetism has been studied for several decades. It is therefore timely to review the physics of the oxyselenides in the context of the broader field of strongly correlated magnetism and electronic phenomena. Here we review the current status and progress in this area of research with the focus on the influence of lanthanides and transition metal ions on the intertwined magnetic and electronic properties of oxyselenides. The emphasis of the review is on the magnetic properties and comparisons are made with iron based pnictide and chalcogenide systems. CONTENTS 8. Summary of the magnetic structure variation with transition metal ion 21 I. Introduction 1 E. Magnetic interactions 22 1. La2O2Fe2OSe2 and Ce2O2FeSe2 22 2+ 2+ II. Experimental techniques 2 2. -
Two-Dimensional Oxides: Recent Progress in Nanosheets
Z. Phys. Chem. 2019; 233(1): 117–165 Review Richard Hinterding* and Armin Feldhoff Two-Dimensional Oxides: Recent Progress in Nanosheets A Retrospection on Synthesis, Microstructure and Applications https://doi.org/10.1515/zpch-2018-1125 Received January 26, 2018; accepted February 27, 2018 Abstract: Two-dimensional (2D) materials have been widely investigated for the last few years, introducing nanosheets and ultrathin films. The often superior electrical, optical and mechanical properties in contrast to their three-dimen- sional (3D) bulk counterparts offer a promising field of opportunities. Especially new research fields for already existing and novel applications are opened by downsizing and improving the materials at the same time. Some of the most promising application fields are namely supercapacitors, electrochromic devices, (bio-) chemical sensors, photovoltaic devices, thermoelectrics, (photo-) catalysts and membranes. The role of oxides in this field of materials deserves a closer look due to their availability, durability and further advantages. Here, recent progress in oxidic nanosheets is highlighted and the benefit of 2D oxides for applications discussed in-depth. Therefore, different synthesis techniques and micro structures are compared more closely. Keywords: nanosheet; oxide; thermoelectric; two-dimensional; ultrathin film. 1 Introduction With the enablement of measuring functional properties of two-dimensional (2D) graphene sheets and the discovery of electrons being able to behave like Dirac-type fermions without restmass [1], new interest in 2D materials was awaken. Actual research considers all elements of the periodic table and their *Corresponding author: Richard Hinterding, Leibniz University Hannover, Institute of Physical Chemistry and Electrochemistry, Callinstraße 3A, D-30176 Hannover, Germany, e-mail: [email protected] Armin Feldhoff: Leibniz University Hannover, Institute of Physical Chemistry and Electrochemistry, Callinstraße 3A, D-30176 Hannover, Germany 118 R. -
GW100: Benchmarking G0W0 for Molecular Systems
GW 100: Benchmarking G0W0 for molecular systems Michiel J. van Setten,∗,y,z Fabio Caruso,{,x Sahar Sharifzadeh,k Xinguo Ren,#,@ Matthias Scheffler,@ Fang Liu,4 Johannes Lischner,r, Lin Lin, Jack R. Deslippe, Steven G. Louie,,r Chao Yang, Florian Weigend,, Jeffey B. Neaton, Ferdinand Evers, and Patrick Rinke,@ Nanoscopic Physics, Institute of Condensed Matter and Nanosciences, Université Catholique de Louvain, Louvain-la-Neuve, 1348, Belgium, Institute of Nanotechnology, Karlsruhe Institute of Technology Campus North, Karlsruhe, 76344 Germany, Fritz-Haber-Institut der Max-Planck-Gesellschaft, Berlin, 4195, Germany, Department of Materials, University of Oxford, Oxford, OX1 3PH, United Kingdom, Molecular Foundry, Lawrence Berkeley National Laboratory, Berkeley, CA 94720, USA, Department of Electrical and Computer Engineering, Boston University, Boston, MA 02215, USA, Key Laboratory of Quantum Information, University of Science and Technology of China, Hefei, 230026, China, Fritz-Haber-Institut der Max-Planck-Gesellschaft, Berlin, 14195, Germany, School of Applied Mathematics, Central University of Finance and Economics, Beijing, Materials Sciences Division, Lawrence Berkeley National Laboratory, Berkeley, CA 94720, USA, Department of Physics, University of California, Berkeley, CA 94720, USA, Computational Research Division, Lawrence Berkeley National Laboratory, Berkeley, CA 94720, USA, National Energy Research Scientific Computing Center, Berkeley, CA 94720, USA, Department of Physics, University of California, Berkeley, CA 94720, USA , Institute of Nanotechnology, Karlsruhe Institute of Technology Campus North, Karlsruhe, 76344, Germany, Institute of Theoretical Physics, University of Regensburg, Regensburg, 93040, Germany, and COMP/Department of Applied Physics, Aalto University School of Science, Aalto, 00076, Finland E-mail: [email protected] 2 May 16, 2015 Abstract ab initio GW calculations for 100 molecules, a benchmark set we term as GW 100, are presented using three independent codes and using different methods. -
Structure and Physical Properties of New Layered Iron Oxychalcogenide
Structure and physical properties of new layered iron oxychalcogenide BaFe2OSe2 Hechang Lei,1, Hyejin Ryu,1,2 John Warren,3 A. I. Frenkel,4 V. Ivanovski,5 B. Cekic5 and C. Petrovic1,2 1Condensed Matter Physics and Materials Science Department, Brookhaven National Laboratory, Upton, New York 11973, USA 2Department of Physics and Astronomy, Stony Brook University, Stony Brook, New York 11794-3800, USA 3Instrumentation Division, Brookhaven National Laboratory, Upton, New York 11973, USA 4Physics Department, Yeshiva University, 245 Lexington Avenue, New York, New York 10016, USA 5Institute of Nuclear Sciences Vinca, University of Belgrade, Belgrade 11001, Serbia (Dated: June 8, 2018) We have successfully synthesized a new layered iron oxychalcogenide BaFe2OSe2 single crystal. This compound is built up of Ba and Fe-Se(O) layers alternatively stacked along the c-axis. The Fe-Se(O) layers contain double chains of edge-shared Fe-Se(O) tetrahedra that propagate along the b-axis and are bridged by oxygen along the a-axis. Physical property measurements indicate that BaFe2OSe2 is a semiconductor without the Curie-Weiss behavior up to 350 K. There is a possible long range antiferromagnetic (AFM) transition at 240 K, corresponding to the peak in specific heat measurement and two glassy transitions at 115 K and 43 K. The magnetic entropy up to 300 K is much smaller than the expected value for Fe2+ in tetrahedral crystal fields and M¨osbauer spectrum indicates that long range magnetic order is unlikely at 294 K. Both results suggest that a short range magnetic correlations exist above the room temperature. PACS numbers: 75.50.Ee, 75.10.Pq, 75.30.Gw, 75.47.Np 2− I.