A Passive Thermal Energy Storage System for Laptop Cooling Using Phase Change Material
Total Page:16
File Type:pdf, Size:1020Kb
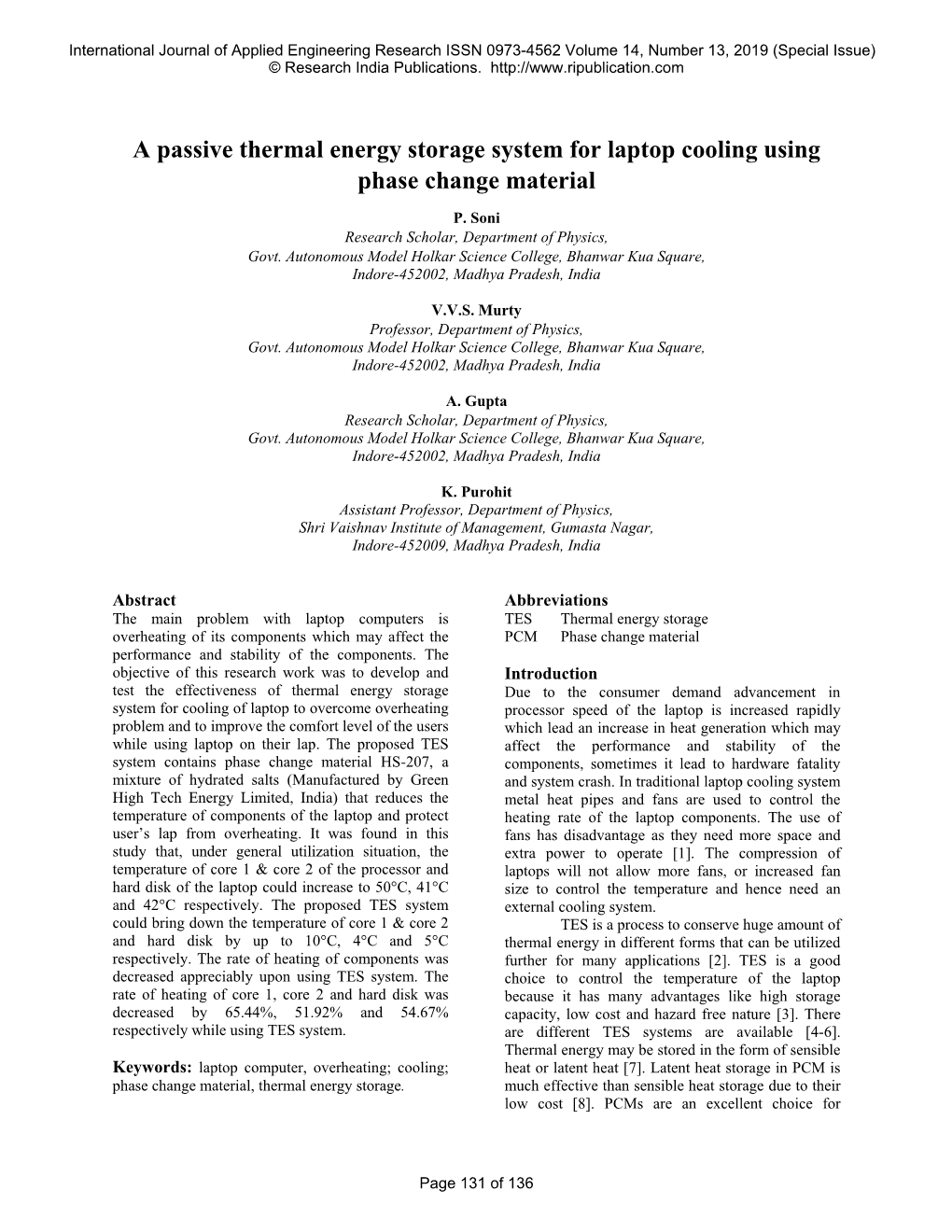
Load more
Recommended publications
-
Entire India Page 1
Entire India HOSPITAL CODE STATUS NAME OF THE HOSPITAL ADDRESS-1 GH-AP-01 ACTIVE Cure Emergency Hospital D.No.11-2-91/A GH-AP-02 ACTIVE Help Hospitals Behind Victoria Museum GH-AP-03 ACTIVE Nagarjuna Hospitals Ltd., Kanuru GH-AP-04 ACTIVE Surya Nursing Home Opp-Mission Hostel Vaatsalya Hospital (Old Name-Venkata Padma Three Lamps Junction, GH-AP-05 ACTIVE Hospitals Pvt Ltd.,) D.No.15-1-45 GH-AP-06 ACTIVE Venkateshwara Hospital Ashok Nagar GH-AP-08 ACTIVE Queen's NRI Hospital Gurudwara Lane GH-AP-09 ACTIVE Dr.Ramarao's Institute of Child Health Kasturibaipet GH-AP-10 ACTIVE Tirumala Nursing Home Near R.T.C. Complex GH-AP-100 ACTIVE Kinnera Superspeciality Hospital wyra road GH-AP-101 ACTIVE Karumuri Hospitals 13-4-23, GH-AP-102 ACTIVE Vishwabharathi Super specality Hospitals Gayathri Estate GH-AP-104 ACTIVE Nandana MultiCare Hospital 4th line 40-1/1-14abc,sivananda GH-AP-105 ACTIVE S.V.R.Neuro Hospital street GH-AP-106 ACTIVE Usha Cardiac Centre Ltd., Near Chennupati petrol bunk GH-AP-107 ACTIVE Dr.Anji Reddy Multispeciality Hospital 16-682, Piduguralla Main Rd GH-AP-108 ACTIVE Vijetha Hospital Suryarao pet GH-AP-109 ACTIVE Apollo Hospital Waltair Main Road GH-AP-11 ACTIVE Sai Bhargavi Eye Hospital Opp.Telephone Exchange #15-1-17, Opp: Gaddipatti Kalyana Mandapam, Near: GH-AP-110 ACTIVE Aswini Hospital Mangalagiri Rly Gate Opp.Anna srinivasarao GH-AP-111 ACTIVE R.K.Eye Centre Kalyana Mantapam GH-AP-112 ACTIVE Sri Amrutha Deepa Orthopaedic Hospital M.G.Road GH-AP-113 ACTIVE Sri Sai Maternity & General Hospital Bhoktapur GH-AP-114 ACTIVE -
List of PPN Hospitals in Indore
Sr. No. ROHINI_Code Hospital Name Location Address 1 8900080148239 Aditya Nursing Home Usha Nagar 315, Usha Nagar Ext 2 8900080146761 Anand Hospital & Research Center Sindhu Nagar 17, Sindhu Nagar, Bhanwar Kua Road, Indore, M.P. 3 8900080344525 Apollo Rajshree Hospitals Pvt. Ltd. Vijay Nagar Sch. No. 74-C, Sector-D, Vijay Nagar, Indore, M.P. 4 8900080333451 Apple Hospital Transport Nagar 15/1, Transport Nagar, Bhawarkua Square, Indore, M.P. 5 8900080148147 Banthia Hospital Airport Road #10, Tirupati Nagar, Airport Road, Indore 6 8900080148260 Bhandari Hospital & Research Centre Vijay Nagar GF-2122,2123, Sch. No. 54, Vijay Nagar, Indore, M.P. 7 8900080148376 Bombay Hospital Trust Ring Road Scheme No 94, Ring Road 8 8900080346789 City Nursing Home Jawahar marg 209, Jawahar Marg 9 8900080373594 Contacare Eye Hospital 19 Diamond Colony 19 Diamond Colony, Indore 10 8900080343177 Convenient Hospitals Ltd A B Road A B Road, Near LIG Square 11 8900080146921 Curewell Hospital Pvt Ltd New Palasia 19/1C, New Palasia 12 8900080394445 Dr Agrawals Healthcare Ltd A B Road Princes Business, Sky line, Block No 32 & 33, PU 3 Commercial Scheme No 54, A B Road, Indore 13 8900080147041 Eureka Hospital & Research Centre Pvt. Ltd. Old Palasia 347, Saket Nagar 14 8900080349803 Gaurav Hospital Khandwa Road 2-A, Rani Bagh, Sector A, Khandwa Naka, Next to Radhaswami Satsang, Khandwa Road 15 8900080148628 Greater Kailash Hospital Old Palasia 11/2, Old Palasia 16 8900080147225 Indore Eye Hospital Dhar Road M O G Lines, Dhar Road 17 8900080341494 Jyoti Hospital Vijay -
Research Policy with a View to Strengthen the Culture of Research on the Campus
Dr. R.K. Tugnawat Principal Govt. Holkar Science College, Indore Bhanwar Kua Chouraha AB Road, Indore - 452001 PREFACE I feel privileged to be a part of Govt. Holkar Science College which is one of the oldest colleges of central India and always recognized for its high quality academic and research output. It continues to be a leading college of Madhya Pradesh. The college constantly strives to live upto the high standards of research set by the eminent professors of this college in the past. A number of faculty members of the college are pursuing research in various fields. The college is also having some ongoing major and minor research projects. We have drafted the research policy with a view to strengthen the culture of research on the campus. The main objective of this policy is to make students research-oriented by fostering inquisitiveness, spirit of innovation and creativity in young minds. This policy envisages a research ambience in the college that offers ample opportunity to the prospective researchers to choose from a wide variety of the fields of investigations, ranging from the ones addressing the global concerns as well as those that have local relevance. Due emphasis is also given to the green research. A number of seminars, conferences and workshops are held on the campus round the year. They help members of the staff to update their knowledge and skills. The cross-fertilization of ideas that takes place during the discussions on these occasions opens up new avenues for scientific exploration. I hope the policy will serve the purpose of reinforcing the norms and conventions of research handed down to us by the great scholars who have graced the institution from time to time. -
Trade Marks Journal No: 1990 , 08/03/2021 Class 17 Certification
Trade Marks Journal No: 1990 , 08/03/2021 Class 17 Certification mark u/s 71(1) 2052835 12/11/2010 SMALL AND MEDIUM ENTERPRISES CORPORATION MALAYSIA (SME CORP. MALAYSIA) LEVEL 6, SME 1,BLOCK -B,LOT-E,JALAN STESEN SENTRAL 2,KAULA LUMPUR SENTRAL , 50470 KUALA LUMPUR, MALAYSIA AN AGENCY UNDER THE MINISTRY OF INTERNATIONAL TRADE AND INDUSTRY (MITI) GOVERMENT OF MALAYSIA Address for service in India/Attorney address: ASWAL ASSOCIATES 59 HARMONY APARTMENTS POCKET-1 SECTOR-4 DWARKA NEW DELHI-110078 Proposed to be Used DELHI RUBBER, GUTTA-PERCHA, GUM, ASBESTOS, MICA AND GOODS MADE FROM THESE MATERIALS AND NOT INCLUDED IN OTHER CLASSES; PLASTICS IN EXTRUDED FORM FOR USE IN MANUFACTURE; PACKING, STOPPING AND INSULATING MATERIALS; FLEXIBLE PIPES, NOT OF METAL. REGISTRATION OF THIS TRADE MARK SHALL GIVE NO RIGHT TO THE EXCLUSIVE USE OF THE.No right over the words MALAYSIAN BRAND.. 2132 Trade Marks Journal No: 1990 , 08/03/2021 Class 17 TIPTOP 3196261 25/02/2016 RIKESH MITTAL trading as ;RIKESH MITTAL JAI NARAYAN ASHOK KUMAR, JULANA MANDI, DISTT. JIND - 126101 (HARYANA) MANUFACTURER AND MERCHANTS Address for service in India/Attorney address: KAMAL GARG & ASSOCIATES B-26 ADARSH APARTMENTS SECTOR 9 ROHINI DELHI-85 Used Since :11/01/2012 DELHI INSULATING TAPE; SELF ADHESIVE TAPES FOR INDUSTRIAL PURPOSES; PACKAGING TAPES; DOUBLE SIDE TISSUE TAPE; DOUBLE SIDE FOAM TAPE; MASKING PAPER TAPE; BOPP PACKAGING TAPE;TEFLON TAPE; ALUMUNIUM FOIL TAPE; NYLON TAPE; COTTON TAPES 2133 Trade Marks Journal No: 1990 , 08/03/2021 Class 17 3354692 06/09/2016 UFLEX LTD. -
271120191113351031248261119
Data under the Central Sector Scheme of Scholarship for College and University Students S.No.. Application ID Board Name Applicant Name Father's Name Categroy Gender Annual Applicant's Applicant's Applicant's Institute Name Institute Address Applicant's Applicant's Renewal Application Status Family Address District Domicile State Mobile Email Status Income 1 MP201819008150636 BOARD OF SECONDARY SAPNA PANCHAL MAHESH OBC F 35000 WARD NO 5 AGARMALWA MADHYA MATA JEEJA BAI moti tabela indore (m.p.) 9424074178 sapnapanchal62 Renewed Application Under EDUCATION , BHOPAL PANCHAL MACHALPURA PRADESH GOVT. P.G. GIRLS [email protected] Process for ROAD DIST COLLEGE MOTI Verification at AGARMALWA TABELA, INDORE Institute Level MP 2 MP201819000786710 BOARD OF SECONDARY RAJU PRAJAPATI BAISAKHU SC M 40000 JANUNA ANUPPUR MADHYA GOVT. Civil Lines - Pachpedi, 9179792038 praju6181@gm Renewed Application Under EDUCATION , BHOPAL PRAJAPATI COLLIERY WARD PRADESH AUTONMOUS Jabalpur ail.com Process for NO 05 ANUPPUR SCIENCE COLLEGE, Verification at CIVIL LINESR, Institute Level 3 MP201819008030317 BOARD OF SECONDARY SOURABH MAHESH SINGH GENERAL M 40000 GRAM DERKA ASHOKNAGAR MADHYA GOVT. NEHRU Govt. Nehru Degree 7828270629 SOURABHRAGH Renewed Application Under EDUCATION , BHOPAL RAGHUWANSHI ASHOKNAGAR PRADESH DEGREE COLLEGE College, Near Bypass, UWANSHI@GM Process for Eshagarh Road, AIL.COM Verification at Ashoknagar, Ashoknagar Institute Level 4 MP201819008715789 BOARD OF SECONDARY PRIYAM JAIN pawan jain GENERAL F 50000 ward no 4 jain ASHOKNAGAR MADHYA GOVT. NEHRU Govt. Nehru Degree 8827902908 Renewed Application Under EDUCATION , BHOPAL mandir ke pass PRADESH DEGREE COLLEGE College, Near Bypass, Process for piprai Eshagarh Road, Verification at Ashoknagar, Ashoknagar Institute Level 5 MP201819001892162 BOARD OF SECONDARY RISHI KUMAR SAHU shambhu dayal OBC M 40000 near jain ASHOKNAGAR MADHYA NATIONAL National Institute of 8878134349 iitianrishi50@g Renewed Application Under EDUCATION , BHOPAL sahu tempaln ,gram PRADESH INSTITUTE OF Technology Raipur G.E. -
Hospital List for Medicare Under Health Insurance| Royal Sundaram
SL.N STD O. HOSPITAL NAME ADDRESS - 1 ADDRESS - 2 CITY PIN CODE STATE ZONE CODE TEL 1 TEL - 2 FAX - 1 SALUTATION FIRST NAME MIDDLE SURNAME E MAIL ID (NEAR PEERA 1 SHRI JIYALAL HOSPITAL & MATERNITY CENTRE 6, INDER ENCLAVE, ROHTAK ROAD GARHI CHOWK) DELHI 110 087 DELHI NORTH 011 2525 2420 2525 8885 MISS MAHIMA 2 SUNDERLAL JAIN HOSPITAL ASHOK VIHAR, PHASE II DELHI 110 052 DELHI NORTH 011 4703 0900 4703 0910 MR DINESH K KHANDELWAL 3 TIRUPATI STONE CENTRE & HOSPITAL 6,GAGAN VIHAR,NEW DELHI DELHI 110051 DELHI NORTH 011 22461691 22047065 MS MEENU # 2, R.B.L.ISHER DAS SAWHNEY MARG, RAJPUR 4 TIRATH RAM SHAH HOSPITAL ROAD, DELHI 110054 DELHI NORTH 011 23972425 23953952 MR SURESH KUMAR 5 INDRAPRASTHA APOLLO HOSPITALS SARITA VIHAR DELHI MATHURA ROAD DELHI 110044 DELHI NORTH 011 26925804 26825700 MS KIRAN 6 SATYAM HOSPITAL A4/64-65, SECTOR-16, ROHINI, DELHI 110 085 DELHI NORTH 011 27850990 27295587 DR VIJAY KOHLI CS / OCF - 6 (NEAR POPULAR APARTMENT AND SECTOR - 13, 7 BHAGWATI HOSPITAL MOTHER DIARY BOOTH) ROHINI DELHI 110 085 DELHI NORTH 011 27554179 27554179 DR NARESH PAMNANI NETRAYATAN DR. GROVER'S CENTER FOR EYE 8 CARE S 371, GREATER KAILASH 2 DELHI 110 048 DELHI NORTH 011 29212828 29212828 DR VISHAL GROVER 9 SHROFF EYE CENTRE A-9, KAILASH COLONY DELHI 110048 DELHI NORTH 011 29231296 29231296 DR KOCHAR MADHUBAN 10 SAROJ HOSPITAL & HEART INSTITUTE SEC-14, EXTN-2, INSTITUTIONAL AREA CHOWK DELHI 110 085 DELHI NORTH 011 27557201 2756 6683 MR AJAY SHARMA 11 ADITYA VARMA MEDICAL CENTRE 32, CHITRA VIHAR DELHI 110 092 DELHI NORTH 011 2244 8008 22043839 22440108 MR SANOJ GUPTA SWARN CINEMA 12 SHRI RAMSINGH HOSPTIAL AND HEART INSTITUTE B-26-26A, EAST KRISHNA NAGAR ROAD DELHI 110 051 DELHI NORTH 011 209 6964 246 7228 MS ARCHANA GUPTA BALAJI MEDICAL & DIAGNOSTIC RESEARCH 13 CENTRE 108-A, I.P. -
Unpaid Dividend for the Year 08-09.Xlsx
First Name Middle Name Last Name Father/Husba Father/Husband Father/Husband Address Country State District PINCode Folio Number of Investment Type Amount Proposed Date nd First Name Middle Name Last Name Securities Due(in of transfer to Rs.) IEPF (DD-MON- YYYY) INTERNET VALLEY LTD, SANTOSH KR Amount for unclaimed and unpaid INTERNET VALLEY LTD NA NA NA GANGWAL, KH NO. 42/ BAKOLI DELHI INDIA Delhi Delhi 110036 1202300000702522 dividend 2000.00 13-APR-2016 Amount for unclaimed and unpaid YASHWANT VASANT DALVI NA NA NA P O BOX 9 POSTAL CODE 112 RUWI OMAN OMAN NA NA IN30023911663747 dividend 25.00 13-APR-2016 UNITED ARAB Amount for unclaimed and unpaid JEBY MATHEW PHILIP K M PHILIP P.O. BOX 7222 ABUDHABI UAE EMIRATES NA NA IN30023911769652 dividend 50.00 13-APR-2016 UNITED ARAB Amount for unclaimed and unpaid VIJAY TANDON NA NA NA P O BOX 5239 DUBAI UAE UAE EMIRATES NA NA IN30023911960920 dividend 90.00 13-APR-2016 NO:10/39A, THIRUVALLUVAR NAGAR Amount for unclaimed and unpaid ALMAS BEGUM A NA NA NA KUNIAMUTHUR COIMBATORE INDIA Tamil Nadu Coimbatore 1201160100090893 dividend 10.00 13-APR-2016 DOOR NO.11-10-14, BONDADA VEEDHI, Amount for unclaimed and unpaid KAMAL NARAYAN SONI NA NA NA NEAR MAZID, VIZIANAGARAM. INDIA Andhra Pradesh Vizianagaram 1201350000012773 dividend 5.00 13-APR-2016 Amount for unclaimed and unpaid PRATIMA SINGH RANVEER SINGH 17-D MIG NEHRU NAGAR BHOPAL M P INDIA Madhya Pradesh Bhopal 288 dividend 25.00 13-APR-2016 11 SHREE HARI APPT B/H EXPRESS HOTEL Amount for unclaimed and unpaid KETAN SANGHAVI RATILAL SANGHAVI ALKAPURI -
Synthesis and Characterization of Cuo Nanoparticles and Their Use in Water Based Nanofluid for Heat Transfer Applications
International Journal of Applied Engineering Research ISSN 0973-4562 Volume 14, Number 13, 2019 (Special Issue) © Research India Publications. http://www.ripublication.com Synthesis and characterization of CuO nanoparticles and their use in water based nanofluid for heat transfer applications A. Gupta Research Scholar, Department of Physics, Govt. Auto. Holkar Science College, Bhanwar Kua Square, Indore-452002, Madhya Pradesh, India V.V.S. Murty Professor, Department of Physics, Govt. Auto. Holkar Science College, Bhanwar Kua Square, Indore-452002, Madhya Pradesh, India P. Soni Research Scholar, Department of Physics, Govt. Auto. Holkar Science College, Bhanwar Kua Square, Indore-452002, Madhya Pradesh, India K. Purohit Assistant Professor, Department of Physics, Shri Vaishnav Institute of Management, Gumasta Nagar, Indore-452009, Madhya Pradesh, India . Abstract potential applications mostly for heat transport [4-6] In the present study, Copper Oxide (CuO) in various solar collector systems. In all the nanoparticles were synthesized through co- applications enhancement of heat transfer behavior of precipitation method and dispersed in deionized fluid necessitate for advancing the performance water (DI water) to prepare nanofluid using ultra- efficiency. To meet industrial demand, researchers sonication. Copper nitrate was used as a precursor engineered a new class of materials called nanofluids and sodium hydroxide pellets were used as hydrolysis [7], by consistently dispersing nanoparticles of agent. The size, structure, purity and morphology of metals/nonmetals in base fluid usually water or oil. CuO nano particles were investigated. The EDAX Nanoparticles enhance thermal properties of base analysis revealed the formation of pure CuO fluid such as thermal diffusivity, natural convection nanoparticles without any impurity phase and [8], thermal conductivity, overall heat capacity and determined the ratio of Copper and Oxygen in CuO heat transfer coefficient. -
Store Name Address State City West-VS Shop No. G
Store Name Address State City West-VS Shop No. G- 21, Ground Floor, Centre Maharashtra Mumbai One Mall, Sector-30, Vashi Frc30020 1-Jain Nagar Road, Abohar Punjab Punjab Abhohar Cell World 5-9-215/ Bg-5, Shop No.01, Saphari Andhra Pradesh Abids Communications Private Plaza, Chirag Alo Lane , Abids Adrash Kumar & Sons Bhagat Singh Chowk,Near Weear Well, Punjab Abohar Abore,Punjab Pund0040 PUND2114 MOBILE Allen Solly Show room , Circular Road, Punjab Abohar RAJD16048 Purnima NAKODA TOWER,OPP.SHANTI KUNJ, Rajasthan Abu Road Stores Abu MOUNT ROAD, ABUROAD Big C Mobiles Pvt Ltd Ambedkar Chowkopp Ganesh Talkies Andhra Pradesh Adilabad Univercell D No 4 3 6 6 And 43 6 7 Hameedpura Andhra Pradesh Adilabad Telecommunications India Pvt Ltd Univercell Ground Floor D No 744 & 45 Andhra Pradesh Adilabad Telecommunications India Garimillaboundaries Main Road Pvt Ltd Mahchiryala Apex Electronics # 4-2-173/10, Cinema Road, Adilabad. Andhra Pradesh Adilabad Communication(Ses) 504001 Andd12633 Cell World 6-5-84/A And 6-7-77/14/10, Netaji Andhra Pradesh Adilabad Communications Private Chwk, Bhotapur , Adilabad Andd13850 ANDD5080 DIGITAL ZONE 4-3-8/4/5 Cinema Road Andhra Pradesh Adilabad Adilabad,Andhra Pradesh-504001 Sky Mobiles Near Ks Rtc Bus Stand Mc Road Kerala Adoor Adoor,Pathanamthitta Kerd5628 Satisfaction 142, Motorstand Road, Agartala Tripura Agartala G S Electronics (Ses) 160 H.G.B Rd.,Melar Math, Near Tripura Agartala Womens Commission Office Trid0595 Sadar Bazar 4, Taj Road, Sadar Bazar, Agra - Uttar Pradesh Agra Frc30056 Shop No.3, Block 5C, -
Biocon Limited Unpaid Dividend for the Financial Year Interim 2014-15
Biocon Limited Unpaid Dividend For The Financial year Interim 2014-15 Proposed Date Folio Number of Amount of transfer to SLNO First Name Middle Name Last Name Address Country State District PINCode Securities Due(in Rs.) IEPF (DD-MON- YYYY) 1 BELAPUR ROAD, TAL-SHRIRAMPUR, DIST-AHMEDNAGAR, KALYAN BUDHAMAL KUNKULOL SHRIRAMPUR INDIA MAHARASHTRA SHRIRAMPUR 413709 IN30364710000159 225.00 31-MAY-2022 2 C/O KOGINABAIL KALASAPPA NAIK AND CO APMC YARD K RAVINDRANATH SHIMOGA INDIA KARNATAKA SHIMOGA 577204 IN30307710000416 1500.00 31-MAY-2022 3 C/3, H-WING, FLAT NO-81 3RD FLOOR, MAHAVIR NAGAR KIRTI SHAH SHANKER LANE, KANDIVALI-WEST MUMBAI, MAHARASHTRA INDIA MAHARASHTRA MUMBAI 400067 IN30373510001518 5.00 31-MAY-2022 4 UB-11, ANTRIKSH BHAWAN, 22, K. G. MARG, NEW DELHI V T SECURITIESLIMITEDNEW DELHI INDIA DELHI NEW DELHI 110001 IN30142810001937 50.00 31-MAY-2022 5 111/686 N VEES VALLEY VILLAS RUBBER BOARD MINNIE JACOB P.O,POOMATTOM KOTTAYAM,KERALA INDIA KERALA KOTTAYAM 686009 IN30312410002003 125.00 31-MAY-2022 6 ANURADHA GUPTA C/O SANJEEV ENTERPRISES 15 CIVIL LINES MUZAFFARNAGAR INDIA UTTAR PRADESH MUZAFFARNAGAR 251001 IN30092310002091 1500.00 31-MAY-2022 7 BIDHAN CHANDRA 269, Nehru Nagar Patliputra Colony Patna INDIA BIHAR PATNA 800013 IN30058910002155 750.00 31-MAY-2022 8 FLAT NO-104,H NO 3-4-726 SHANTHINIKEHTAN APTS CH RAGHU VEER REDDY NARAYANAGUDA HYDERABAD INDIA ANDHRA PRADESH HYDERABAD 500027 IN30182010002255 50.00 31-MAY-2022 9 ARCHANA AGARWAL 25/161 INDIA HOUSE BYE PASS ROAD AGRA INDIA UTTAR PRADESH AGRA 282004 IN30100610002840 10.00 31-MAY-2022 10 AMIT KHURANA 192 SCHEME NO 10 ALWAR ALWAR RAJASTHAN INDIA RAJASTHAN ALWAR 301001 IN30373510003257 125.00 31-MAY-2022 11 PALASH BANERJEE VILLAGE KASHIPUR POST. -
SLNO First Name Middle Name Last Name Address Country State District Pincode Folio No of Securities Amount Due in Rs. Proposed D
Biocon Limited Unpaid Dividend For The Financial year Interim 2015‐16 Proposed Date of transfer to Folio No of Amount IEPF (DD‐MON‐ SLNO First Name Middle Name Last Name Address Country State District Pincode Securities Due in Rs. YYYY) ICI INDIA LTD 5, MALBAR COURT, B G KHER 1 ASHOK GANGULY ROAD, MALABAR HILL MUMBAI INDIA MAHARASHTRA MUMBAI BIO000151 2500.00 29‐MAR‐2023 A 602 LOVELY HOME APPT SECTOR 5 PLOT NO 2 D K ARORA 5 DWARKA INDIA DELHI NEW DELHI 110075 IN30088814869214 2000.00 29‐MAR‐2023 FLAT NO B 141 BELVEDERE PARK DLF PHASE 3 3 MAN PARTAP SINGH VIRK SIKANDERPUR GHOSI 68 GURGAON HARYANA INDIA HARYANA GURGAON 122002 IN30114310289906 2500.00 29‐MAR‐2023 H.NO. 40 SECTOR ‐ 13 PART ‐ II HISAR 4 SANJEEV KUMAR HUF HARYANA INDIA HARYANA HISSAR 125001 1203720000028369 2000.00 29‐MAR‐2023 5 JASBIR SINGH 236 HARGOBIND NAGAR PHAGWARA INDIA PUNJAB PHAGWARA 144401 IN30184610091535 18000.00 29‐MAR‐2023 6 SHIV KUMAR OHRI HOSHIARPUR ROAD UNA INDIA HIMACHAL PRADESH UNA 174303 IN30184610314411 2000.00 29‐MAR‐2023 7 KAPIL SARAF GOVT GUEST HOUSE CANAL ROAD JAMMU INDIA JAMMU AND KASHMIR JAMMU 180001 IN30234910194184 2500.00 29‐MAR‐2023 8 NEMI CHAND CHAJJER 8 OJHAJI KA BAS PALI MARWAR INDIA RAJASTHAN PALI 306401 IN30112716755296 1500.00 29‐MAR‐2023 KANSARO KA DHORA WARD NO 4 BALOTRA 9 LAL CHAND RAJASTHAN INDIA RAJASTHAN BARMER 344022 1203320007633524 25000.00 29‐MAR‐2023 BUNGLOW NO5 JIVANJYOT ESTATE OPP.SURYAKIRAN APPT GHOD DOD ROAD 10 SHANKERLAL NEBHUMAL UTTAMCHANDANI SURAT INDIA GUJARAT SURAT 395007 IN30133018042736 2500.00 29‐MAR‐2023 33 RIJHUMAL MANSION 15/B PEDDER ROAD 11 BHARAT PAREKH MUMBAI, MUMBAI INDIA MAHARASHTRA MUMBAI 400026 IN30112715889998 1750.00 29‐MAR‐2023 12 GEETA INAMDAR T/154 JUHU KOLIWADA MUMBAI INDIA MAHARASHTRA MUMBAI 400049 IN30051310384519 5000.00 29‐MAR‐2023 SIDDHI GROND FLOOR PLOT NO. -
Cautious Hospitals List
Cautious Hospitals List TPA Name HospitalName Address City State GHPL TPA PULSE HOSPITAL-CHINTAL PLOT NO 10, SY NO 147P, CHINTAL HYDERABAD TELANGANA GHPL TPA MEDICHECK HOSPITAL - FARIDABAD 1C-76 AND 53, N.I.T FARIDABAD HARYANA GHPL TPA NEW MILLENNIUM MULTISPECIALITY HOSPITAL-NAVI MUMBAI PLOT NO.17C, SEC-5, SANPADA NAVI MUMBAI MAHARASHTRA GHPL TPA NANDINI HOSPITAL - SAINIKPURI PLOT NO 156, HI TENSION ROAD, SAINIKPURI X ROAD SECUNDERABAD TELANGANA GHPL TPA SAHASRA HOSPITAL(A UNIT OF SASA HEALTHCARE)-MANJEERA NAGAR MANJEERA NAGAR, MAIN ROAD SANGAREDDY TELANGANA GHPL TPA DIVYA PRASTHA HOSPITAL-PALAM COLONY RZ-37, OPPOSITE BAGH WALA SCHOOL, MAIN ROAD NEW DELHI DELHI GHPL TPA RAJPAL HOSPITAL AND INSTITUTE-KOPERKHAIRANE PLOT NO 13, SECTOR 10 NAVI MUMBAI MAHARASHTRA GHPL TPA YASHODA KRISHNA HOSPITAL - KARIMNAGAR HNO 7-1-324, MANKAMMATHOTA KARIMNAGAR TELANGANA GHPL TPA PENTAMED HOSPITAL-DELHI 7 LOCAL SHOPPING CENTRE DELHI DELHI GHPL TPA VIKAS HOSPITAL PVT LTD-NAJAFGARH 1629-H, THANA ROAD, NAJAFGARH NEW DELHI DELHI GHPL TPA JUPITER HOSPITAL - THANE EASTERN EXPRESS HIGHWAY THANE MAHARASHTRA GHPL TPA INDUS HOSPITAL - AHMEDABAD OPP. ADANI CNG PUMP, OPP. MOTERA CROSS ROAD, BRTS STOP, SABARMATI AHMEDABAD GUJARAT GHPL TPA ISHAN HOSPITAL PVT LTD-ROHINI PLOT NO. 1, POCKET -8B,SECTOER 19,ROHINI DELHI DELHI GHPL TPA ADITYA MULTICARE HOSPITAL-VISAKHAPATNAM D NO 18 7 33 OPP KGH O P GATE VISAKHAPATNAM ANDHRA PRADESH GHPL TPA BATRA HOSPITAL MEDICAL CENTRE 1 TUGHLAKABAD INSTITUTIONAL AREA NEW DELHI DELHI GHPL TPA CONTINENTAL HOSPITALS-GACHIBOWLI PLOT NO.3, ROAD