Techniques for the Generation of 3D Finite Element Meshes of Human Organs
Total Page:16
File Type:pdf, Size:1020Kb
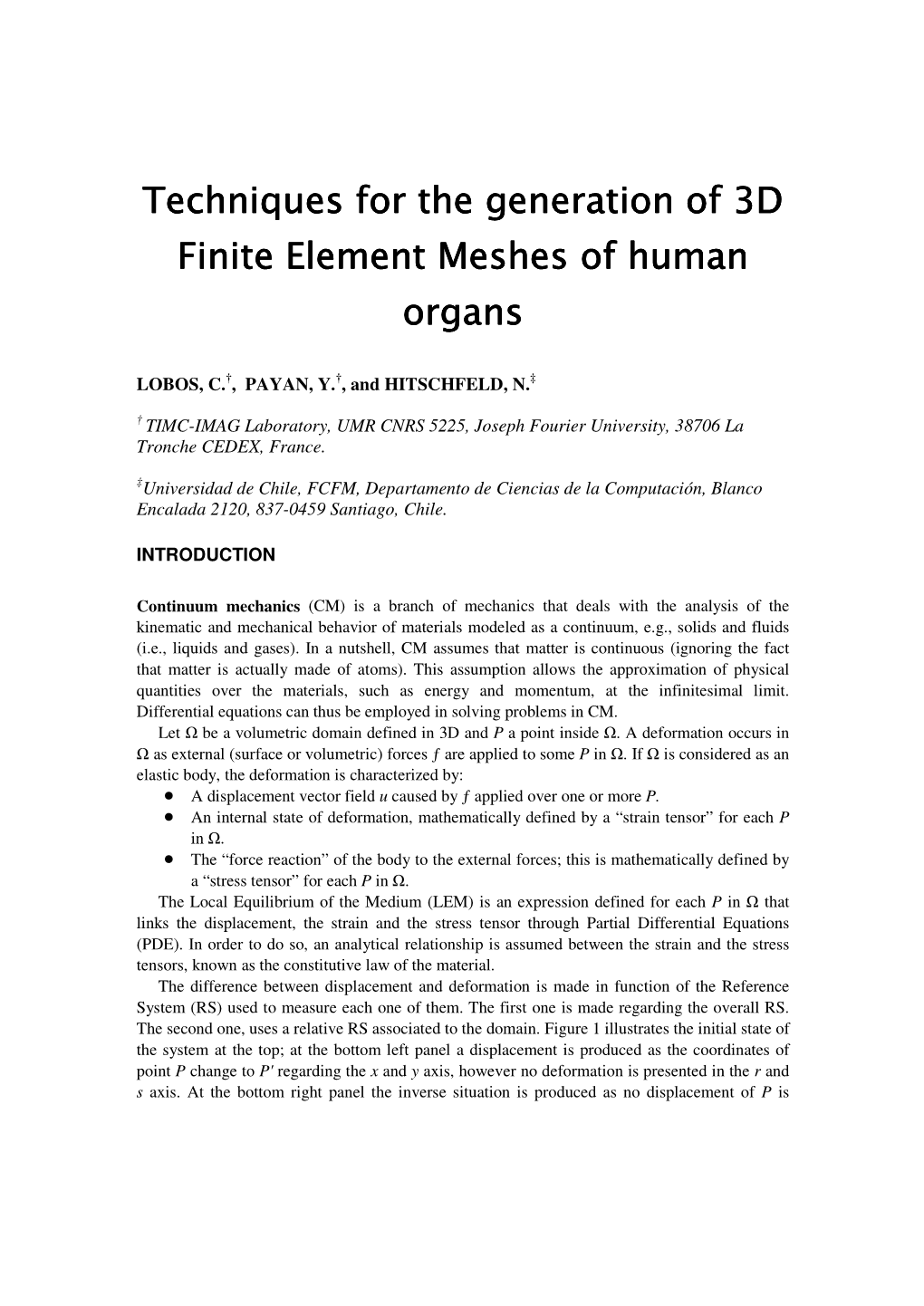
Load more
Recommended publications
-
Models and Algorithms for Physical Cryptanalysis
MODELS AND ALGORITHMS FOR PHYSICAL CRYPTANALYSIS Dissertation zur Erlangung des Grades eines Doktor-Ingenieurs der Fakult¨at fur¨ Elektrotechnik und Informationstechnik an der Ruhr-Universit¨at Bochum von Kerstin Lemke-Rust Bochum, Januar 2007 ii Thesis Advisor: Prof. Dr.-Ing. Christof Paar, Ruhr University Bochum, Germany External Referee: Prof. Dr. David Naccache, Ecole´ Normale Sup´erieure, Paris, France Author contact information: [email protected] iii Abstract This thesis is dedicated to models and algorithms for the use in physical cryptanalysis which is a new evolving discipline in implementation se- curity of information systems. It is based on physically observable and manipulable properties of a cryptographic implementation. Physical observables, such as the power consumption or electromag- netic emanation of a cryptographic device are so-called `side channels'. They contain exploitable information about internal states of an imple- mentation at runtime. Physical effects can also be used for the injec- tion of faults. Fault injection is successful if it recovers internal states by examining the effects of an erroneous state propagating through the computation. This thesis provides a unified framework for side channel and fault cryptanalysis. Its objective is to improve the understanding of physi- cally enabled cryptanalysis and to provide new models and algorithms. A major motivation for this work is that methodical improvements for physical cryptanalysis can also help in developing efficient countermea- sures for securing cryptographic implementations. This work examines differential side channel analysis of boolean and arithmetic operations which are typical primitives in cryptographic algo- rithms. Different characteristics of these operations can support a side channel analysis, even of unknown ciphers. -
Compression and Streaming of Polygon Meshes
Compression and Streaming of Polygon Meshes by Martin Isenburg A dissertation submitted to the faculty of the University of North Carolina at Chapel Hill in partial fulfillment of the requirements for the degree of Doctor of Philosophy in the Department of Computer Science. Chapel Hill 2005 Approved by: Jack Snoeyink, Advisor Craig Gotsman, Reader Peter Lindstrom, Reader Dinesh Manocha, Committee Member Ming Lin, Committee Member ii iii ABSTRACT MARTIN ISENBURG: Compression and Streaming of Polygon Meshes (Under the direction of Jack Snoeyink) Polygon meshes provide a simple way to represent three-dimensional surfaces and are the de-facto standard for interactive visualization of geometric models. Storing large polygon meshes in standard indexed formats results in files of substantial size. Such formats allow listing vertices and polygons in any order so that not only the mesh is stored but also the particular ordering of its elements. Mesh compression rearranges vertices and polygons into an order that allows more compact coding of the incidence between vertices and predictive compression of their positions. Previous schemes were designed for triangle meshes and polygonal faces were triangulated prior to compression. I show that polygon models can be encoded more compactly by avoiding the initial triangulation step. I describe two compression schemes that achieve better compression by encoding meshes directly in their polygonal representation. I demonstrate that the same holds true for volume meshes by extending one scheme to hexahedral meshes. Nowadays scientists create polygonal meshes of incredible size. Ironically, com- pression schemes are not capable|at least not on common desktop PCs|to deal with giga-byte size meshes that need compression the most. -
MASTER THESIS Generating Hollow Offset Surface Meshes From
Department of Information and Computing Sciences Utrecht University The Netherlands MASTER THESIS ICA-3746356 Generating hollow offset surface meshes from segmented CT volumes using distance fields Submitted on 20th August 2019 By M.F.A. Martens Project supervisor (first examiner): prof. dr. R.C. Veltkamp Second examiner: dr. ir. A.F. van der Stappen Daily supervisor: Jan de Vaan Abstract We propose a method to generate hollow offset surface meshes from CT data using distance fields, in general and in the context of the 3mensio software package. Our method improves on several shortcomings of the currently implemented morpholo- gical offsetting method, like a blocky appearance of the offset surface, and uneven distance between the original surface and the offset surface. Our distance field ap- proach is very robust, and performs consistently for a wide range of tested anatomy and across different levels of CT voxel scaling. Our new method is able to return an offset mesh from CT segmentation data in an acceptable amount of time: mostly below 20 seconds, even for very large segmentations. Acknowledgements I want to thank 3mensio Medical Imaging B.V, and my daily supervisor Jan de Vaan in particular, for providing the opportunity to do an internship at their company, and for the support throughout the writing of this thesis report. I also want to thank my main supervisor and first examiner, prof. dr. Remco Veltkamp, for the help with all of my questions and for the feedback on earlier versions of this report. Also I would like to thank dr. ir. Frank van der Stappen, who agreed to by my second examiner. -
An Approach of Using Delaunay Refinement to Mesh Continuous Height Fields
DEGREE PROJECT IN TECHNOLOGY, FIRST CYCLE, 15 CREDITS STOCKHOLM, SWEDEN 2017 An approach of using Delaunay refinement to mesh continuous height fields NOAH TELL ANTON THUN KTH ROYAL INSTITUTE OF TECHNOLOGY SCHOOL OF COMPUTER SCIENCE AND COMMUNICATION An approach of using Delaunay refinement to mesh continuous height fields NOAH TELL ANTON THUN Degree Programme in Computer Science Date: June 5, 2017 Supervisor: Alexander Kozlov Examiner: Örjan Ekeberg Swedish title: En metod att använda Delaunay-raffinemang för att skapa polygonytor av kontinuerliga höjdfält School of Computer Science and Communication Abstract Delaunay refinement is a mesh triangulation method with the goal of generating well-shaped triangles to obtain a valid Delaunay triangulation. In this thesis, an approach of using this method for meshing continuous height field terrains is presented using Perlin noise as the height field. The Delaunay approach is compared to grid-based meshing to verify that the theoretical time complexity O(n log n) holds and how accurately and deterministically the Delaunay approach can represent the height field. However, even though grid-based mesh generation is faster due to an O(n) time complexity, the focus of the report is to find out if De- launay refinement can be used to generate meshes quick enough for real-time applications. As the available memory for rendering the meshes is limited, a solution for providing a co- hesive mesh surface is presented using a hole filling algorithm since the Delaunay approach ends up leaving gaps in the mesh when a chunk division is used to limit the total mesh count present in the application. -
Non-Interactive Key Establishment in Wireless Mesh Networks
Chapter 1 Non-Interactive Key Establishment in Wireless Mesh Networks Zhenjiang Li†, J.J. Garcia-Luna-Aceves †∗ zhjli,jj @soe.ucsc.edu { } †Computer Engineering, University of California, Santa Cruz 1156 high street, Santa Cruz, CA 95064, USA Phone:1-831-4595436, Fax: 1-831-4594829 ∗Palo Alto Research Center (PARC) 3333 Coyote Hill Road, Palo Alto, CA 94304, USA Symmetric cryptographic primitives are preferable in designing security protocols for wireless mesh networks (WMNs) because they are computationally affordable for resource- constrained mobile devices forming a WMN. Most proposed key-establishment schemes for symmetric cryptosystem assume services from a centralized authority (either on-line or off- line), or involve the interaction between communicating parties. However, requiring access 1 c Springer, 2005. This is a revision of the work published in the proceedings of AdhocNow’05, LNCS 3738, pp. 164-177, Cancun," Mexico, Oct. 2005. 2This work was supported in part by the Baskin Chair of Computer Engineering at UCSC, the National Science Foundation under Grant CNS-0435522, the U.S. Army Research Office under grant No. W911NF-05-1-0246. Any opinions, findings, and conclusions are those of the authors and do not necessarily reflect the views of the funding agencies. 1 2CHAPTER 1. NON-INTERACTIVE KEY ESTABLISHMENT IN WIRELESS MESH NETWORKS to a centralized authority, or ensuring that correct routing be established before the key agreement is done, is difficult to attain in wireless networks. We present a new non-interactive key agreement and progression (NIKAP) scheme for wireless networks, which does not require an on-line centralized authority, can establish and update pairwise shared keys between any two nodes in a non-interactive manner, is configurable to operate synchronously (S-NIKAP) or asynchronously (A-NIKAP), and has the ability to provide differentiated security services w.r.t. -
Mesh Segmentation Guided by Seed Points
Bulletin of the JSME Vol.9, No.4, 2015 Journal of Advanced Mechanical Design, Systems, and Manufacturing Mesh segmentation guided by seed points Xue JIAO*, Huixin ZHANG* and Tieru WU* *Institute of Mathematics, Jilin University Changchun, Jilin130012, China E-mail: [email protected] Received 3 January 2015 Abstract Segmenting 3D models into meaningful parts is a fundamental problem in computer graphics. In this paper, we present an algorithm which is guided by the mesh vertices for segmenting a mesh into meaningful sub-meshes. First, a candidate set of feature points is selected to highlight the most significant features of the model. After that, a diversity measure is calculated by using Hausdorff distance. The collection of seed points we defined is a subset of the candidate set. The collection of seed points consists of two parts, namely, the basic point and lucky points. By maximizing the diversity measure between the seed set and candidate set, an appropriate seed point is selected. Based on the collection of seed points, the segmentation process can be guided by these seeds. Because humans generally perceive desirable segmentations at concave regions, and the geodesic distance and curvature are well-known noise sensitive. Considering the above factors, in order to partition the target into meaningful parts, we define a distance function between each pair of mesh vertices. This function is formed by arc length, angular distance and curvature-related correction term. We have tested the method developed in this paper with 3D meshes from the Princeton segmentation benchmark. Moreover, our segmentation method also has been compared with other methods. -
Differential and Linear Attacks on the Full WIDEA-N Block Ciphers (Under
Differential and Linear Attacks on the full WIDEA-n block ciphers (under weak keys) Jorge Nakahara Jr Universit´eLibre de Bruxelles (ULB), Dept. of Computer Science, Belgium [email protected] Abstract. We report on differential and linear analysis of the full 8.5- round WIDEA-n ciphers for n 2 f4; 8g, under weak-key assumptions. The novelty in our attacks include the use of differential and linear rela- tion patterns that allow to bypass the diffusion provided by MDS codes altogether. Therefore, we can attack only a single IDEA instance out of n copies, effectively using a narrow trail for the propagation of differ- ences and masks across WIDEA-n. In fact, the higher the value of n, the better the attacks become. Our analyses apply both to particular MDS matrices, such as the one used in AES, as well as general MDS matrices. Our attacks exploit fixed points of MDS matrices. We also observed a curious interaction between certain differential/linear patterns and the coefficients of MDS matrices for non-trivial fixed points. This interac- tion may serve as an instructive design criterion for block cipher designs such as WIDEA-n. The authors of WIDEA-n suggested a compression function construction using WIDEA-8 in Davies-Meyer mode. In this setting, the weaknesses identified in this paper can lead to free-start col- lisions and even actual collisions depending on the output transformation of the hash function. Keywords: wide-block cipher, cryptanalysis, WIDEA-n, free-start collisions. 1 Introduction In [6], Junod and Macchetti presented a Wide-block version of IDEA cipher [7] called WIDEA-n, combining n instances of the 8.5-round IDEA cipher joined by an n×n matrix derived from a Maximum Distance Separable (MDS) code. -
Ipsec VPN Solutions Using Next Generation Encryption
IPSec VPN Solutions Using Next Generation Encryption Deployment Guide Version 1.5 Authored by: Ben Rosenblum – CCIE #21084 (R&S, SP) IPSec VPN Solutions Using Deployment Guide Next Generation Encryption THE SPECIFICATIONS AND INFORMATION REGARDING THE PRODUCTS IN THIS MANUAL ARE SUBJECT TO CHANGE WITHOUT NOTICE. ALL STATEMENTS, INFORMATION, AND RECOMMENDATIONS IN THIS MANUAL ARE BELIEVED TO BE ACCURATE BUT ARE PRESENTED WITHOUT WARRANTY OF ANY KIND, EXPRESS OR IMPLIED. USERS MUST TAKE FULL RESPONSIBILITY FOR THEIR APPLICATION OF ANY PRODUCTS. THE SOFTWARE LICENSE AND LIMITED WARRANTY FOR THE ACCOMPANYING PRODUCT ARE SET FORTH IN THE INFORMATION PACKET THAT SHIPPED WITH THE PRODUCT AND ARE INCORPORATED HEREIN BY THIS REFERENCE. IF YOU ARE UNABLE TO LOCATE THE SOFTWARE LICENSE OR LIMITED WARRANTY, CONTACT YOUR CISCO REPRESENTATIVE FOR A COPY. The following information is for FCC compliance of Class A devices: This equipment has been tested and found to comply with the limits for a Class A digital device, pursuant to part 15 of the FCC rules. These limits are designed to provide reasonable protection against harmful interference when the equipment is operated in a commercial environment. This equipment generates, uses, and can radiate radio-frequency energy and, if not installed and used in accordance with the instruction manual, may cause harmful interference to radio communications. Operation of this equipment in a residential area is likely to cause harmful interference, in which case users will be required to correct the interference at their own expense. The following information is for FCC compliance of Class B devices: The equipment described in this manual generates and may radiate radio- frequency energy. -
The Celeblain of Celeborn and Galadriel
Volume 9 Number 2 Article 5 6-15-1982 The Celeblain of Celeborn and Galadriel Janice Johnson Southern Illinois University Follow this and additional works at: https://dc.swosu.edu/mythlore Part of the Children's and Young Adult Literature Commons Recommended Citation Johnson, Janice (1982) "The Celeblain of Celeborn and Galadriel," Mythlore: A Journal of J.R.R. Tolkien, C.S. Lewis, Charles Williams, and Mythopoeic Literature: Vol. 9 : No. 2 , Article 5. Available at: https://dc.swosu.edu/mythlore/vol9/iss2/5 This Article is brought to you for free and open access by the Mythopoeic Society at SWOSU Digital Commons. It has been accepted for inclusion in Mythlore: A Journal of J.R.R. Tolkien, C.S. Lewis, Charles Williams, and Mythopoeic Literature by an authorized editor of SWOSU Digital Commons. An ADA compliant document is available upon request. For more information, please contact [email protected]. To join the Mythopoeic Society go to: http://www.mythsoc.org/join.htm Mythcon 51: A VIRTUAL “HALFLING” MYTHCON July 31 - August 1, 2021 (Saturday and Sunday) http://www.mythsoc.org/mythcon/mythcon-51.htm Mythcon 52: The Mythic, the Fantastic, and the Alien Albuquerque, New Mexico; July 29 - August 1, 2022 http://www.mythsoc.org/mythcon/mythcon-52.htm Abstract Reviews the history of Galadriel and Celeborn as revealed in unpublished materials as well as The Lord of the Rings, The Silmarillion, Tolkien’s Letters, and Unfinished alesT , and examines variations and inconsistencies. Additional Keywords Tolkien, J.R.R.—Characters—Celeborn; Tolkien, J.R.R.—Characters—Galadriel; Patrick Wynne This article is available in Mythlore: A Journal of J.R.R. -
Voronoi Meshing Without Clipping
VoroCrust: Voronoi Meshing Without Clipping AHMED ABDELKADER, University of Maryland, College Park CHANDRAJIT L. BAJAJ, University of Texas, Austin MOHAMED S. EBEIDA∗, Sandia National Laboratories AHMED H. MAHMOUD, University of California, Davis SCOTT A. MITCHELL, Sandia National Laboratories JOHN D. OWENS, University of California, Davis AHMAD A. RUSHDI, Sandia National Laboratories 0.00 0.99 0.41 1.00 0.0 0.2 0.4 0.6 0.8 1.0 0.4 0.5 0.6 0.7 0.8 0.9 1.0 Fig. 1. State-of-the-art methods for conforming Voronoi meshing clip Voronoi cells at the bounding surface. The Restricted Voronoi Diagram [Yan et al. 2013] (left) is sensitive to the input tessellation and produces surface elements of very low quality, per the shortest-to-longest edge ratio distribution shown in the inset. In contrast, VoroCrust (right) generates an unclipped Voronoi mesh conforming to a high-quality surface mesh. Polyhedral meshes are increasingly becoming an attractive option algorithm that can handle broad classes of domains exhibiting with particular advantages over traditional meshes for certain arbitrarily curved boundaries and sharp features. In addition, the applications. What has been missing is a robust polyhedral meshing power of primal-dual mesh pairs, exemplified by Voronoi-Delaunay meshes, has been recognized as an important ingredient in numerous ∗ Correspondence address: [email protected]. Author names are listed in alphabetical order. formulations. The VoroCrust algorithm is the first provably-correct This material is based upon work supported by the U.S. Department algorithm for conforming polyhedral Voronoi meshing for non- of Energy, Office of Science, Office of Advanced Scientific Computing convex and non-manifold domains with guarantees on the quality Research (ASCR), Applied Mathematics Program, and the Laboratory of both surface and volume elements. -
Computing Three-Dimensional Constrained Delaunay Refinement Using the GPU
Computing Three-dimensional Constrained Delaunay Refinement Using the GPU Zhenghai Chen Tiow-Seng Tan School of Computing School of Computing National University of Singapore National University of Singapore [email protected] [email protected] ABSTRACT collectively called elements, are split in this order in many rounds We propose the first GPU algorithm for the 3D triangulation refine- until there are no more bad tetrahedra. Each round, the splitting ment problem. For an input of a piecewise linear complex G and is done to many elements in parallel with many GPU threads. The a constant B, it produces, by adding Steiner points, a constrained algorithm first calculates the so-called splitting points that can split Delaunay triangulation conforming to G and containing tetrahedra elements into smaller ones, then decides on a subset of them to mostly of radius-edge ratios smaller than B. Our implementation of be Steiner points for actual insertions into the triangulation T . the algorithm shows that it can be an order of magnitude faster than Note first that a splitting point is calculated by a GPU threadas the best CPU algorithm while using a similar amount of Steiner the midpoint of a subsegment, the circumcenter of the circumcircle points to produce triangulations of comparable quality. of the subface, and the circumcenter of the circumsphere of the tetrahedron. Note second that not all splitting points calculated CCS CONCEPTS can be inserted as Steiner points in a same round as they together can potentially create undesirable short edges in T to cause non- • Theory of computation → Computational geometry; • Com- termination of the algorithm. -
CXCR4-SERINE339 Regulates Cellular Adhesion, Retention and Mobilization, and Is a Marker for Poor Prognosis in Acute Myeloid Leukemia
Leukemia (2014) 28, 566–576 & 2014 Macmillan Publishers Limited All rights reserved 0887-6924/14 www.nature.com/leu ORIGINAL ARTICLE CXCR4-SERINE339 regulates cellular adhesion, retention and mobilization, and is a marker for poor prognosis in acute myeloid leukemia L Brault1, A Rovo´ 2, S Decker3, C Dierks3, A Tzankov4,5 and J Schwaller1,5 The CXCR4 receptor is a major regulator of hematopoietic cell migration. Overexpression of CXCR4 has been associated with poor prognosis in acute myelogenous leukemia (AML). We have previously shown that ligand-mediated phosphorylation of the Serine339 (CXCR4-S339) residue of the intracellular domain by PIM1 is implicated in surface re-expression of this receptor. Here, we report that phosphorylation of CXCR4-S339 in bone marrow (BM) biopsies correlated with poor prognosis in a cohort of AML patients. To functionally address the impact of CXCR4-S339 phosphorylation, we generated cell lines-expressing CXCR4 mutants that mimic constitutive phosphorylation (S339E) or abrogate phosphorylation (S339A). Whereas the expression of CXCR4 significantly increased, both CXCR4-S339E and the CXCR4-S339A mutants significantly reduced the BM homing and engraftment of Kasumi-1 AML cells in immunodeficient mice. In contrast, only expression of the CXCR4-S339E mutant increased the BM retention of the cells and resistance to cytarabine treatment, and impaired detachment capacity and AMD3100-induced mobilization of engrafted leukemic cells. These observations suggest that the poor prognosis in AML patients displaying CXCR4-S339 phosphorylation can be the consequence of an increased retention to the BM associated with an enhanced chemoresistance of leukemic cells. Therefore, CXCR4-S339 phosphorylation could serve as a novel prognostic marker in human AML.