The Development, Construction and Testing of a Piston Expander for Small-Scale Solar Thermal Power Plants
Total Page:16
File Type:pdf, Size:1020Kb
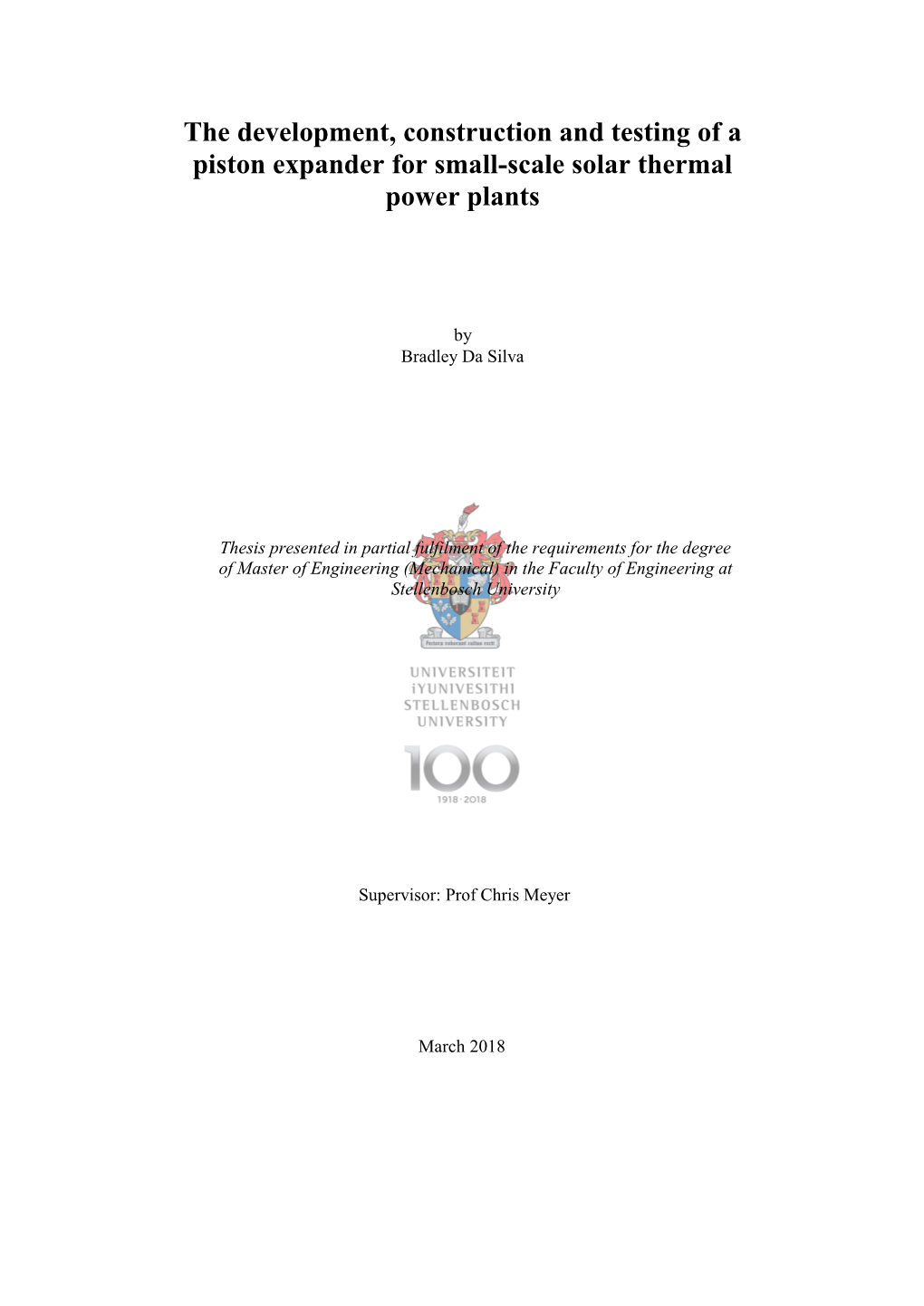
Load more
Recommended publications
-
Engine Components and Filters: Damage Profiles, Probable Causes and Prevention
ENGINE COMPONENTS AND FILTERS: DAMAGE PROFILES, PROBABLE CAUSES AND PREVENTION Technical Information AFTERMARKET Contents 1 Introduction 5 2 General topics 6 2.1 Engine wear caused by contamination 6 2.2 Fuel flooding 8 2.3 Hydraulic lock 10 2.4 Increased oil consumption 12 3 Top of the piston and piston ring belt 14 3.1 Hole burned through the top of the piston in gasoline and diesel engines 14 3.2 Melting at the top of the piston and the top land of a gasoline engine 16 3.3 Melting at the top of the piston and the top land of a diesel engine 18 3.4 Broken piston ring lands 20 3.5 Valve impacts at the top of the piston and piston hammering at the cylinder head 22 3.6 Cracks in the top of the piston 24 4 Piston skirt 26 4.1 Piston seizure on the thrust and opposite side (piston skirt area only) 26 4.2 Piston seizure on one side of the piston skirt 27 4.3 Diagonal piston seizure next to the pin bore 28 4.4 Asymmetrical wear pattern on the piston skirt 30 4.5 Piston seizure in the lower piston skirt area only 31 4.6 Heavy wear at the piston skirt with a rough, matte surface 32 4.7 Wear marks on one side of the piston skirt 33 5 Support – piston pin bushing 34 5.1 Seizure in the pin bore 34 5.2 Cratered piston wall in the pin boss area 35 6 Piston rings 36 6.1 Piston rings with burn marks and seizure marks on the 36 piston skirt 6.2 Damage to the ring belt due to fractured piston rings 37 6.3 Heavy wear of the piston ring grooves and piston rings 38 6.4 Heavy radial wear of the piston rings 39 7 Cylinder liners 40 7.1 Pitting on the outer -
Greensteam Design Report
Greensteam Design Report Double-acting Compound - Phase I Tae Rugh Fall 2020 Initial design CAD, renders, and motivation This is a 2 stage double-acting inline compound engine. This engine replaces the traditional cross-slide by extending the piston rod through the back end of the cylinder, thereby supporting the piston on either end. This increases the amount of required seals by two, but reduces moving mass and engine complexity. Steam enters the high pressure cylinder on both ends through bash valves. After high pressure expansion, steam exits through uniflow ports into a manifold which goes to the low pressure cylinder. Here, the semi-expanded steam expands again before finally exiting through uniflow exhaust ports into the atmosphere. The timing between high and low pressure pistons is slightly offset such that for the first ~5-10% of low pressure power stroke, the low pressure piston acts as a pump to improve the exhaust performance of the high pressure cylinder. For this portion, the low pressure piston is actually doing negative work, but the hope is that this produces more efficiency gains in the exhaust process to offset these losses. This claim is not too far-fetched considering, for example, internal combustion engines also incorporate an exhaust stroke in which the piston acts as a pump to remove the exhaust gas. Of course, this mechanism will need to be validated with further calculations. Part Breakdown The crankshaft has overhung cranks on either end, much like bicycle pedals, in order to avoid the manufacturing complexities that accompany traditional (non-overhung) cranks. o The cranks are offset from each other (currently at 120 ) such that the low pressure piston is slightly ahead of the high pressure piston, which induces the vacuum pump function of the low pressure piston. -
MACHINES OR ENGINES, in GENERAL OR of POSITIVE-DISPLACEMENT TYPE, Eg STEAM ENGINES
F01B MACHINES OR ENGINES, IN GENERAL OR OF POSITIVE-DISPLACEMENT TYPE, e.g. STEAM ENGINES (of rotary-piston or oscillating-piston type F01C; of non-positive-displacement type F01D; internal-combustion aspects of reciprocating-piston engines F02B57/00, F02B59/00; crankshafts, crossheads, connecting-rods F16C; flywheels F16F; gearings for interconverting rotary motion and reciprocating motion in general F16H; pistons, piston rods, cylinders, for engines in general F16J) Definition statement This subclass/group covers: Machines or engines, in general or of positive-displacement type References relevant to classification in this subclass This subclass/group does not cover: Rotary-piston or oscillating-piston F01C type Non-positive-displacement type F01D Informative references Attention is drawn to the following places, which may be of interest for search: Internal combustion engines F02B Internal combustion aspects of F02B 57/00; F02B 59/00 reciprocating piston engines Crankshafts, crossheads, F16C connecting-rods Flywheels F16F Gearings for interconverting rotary F16H motion and reciprocating motion in general Pistons, piston rods, cylinders for F16J engines in general 1 Cyclically operating valves for F01L machines or engines Lubrication of machines or engines in F01M general Steam engine plants F01K Glossary of terms In this subclass/group, the following terms (or expressions) are used with the meaning indicated: In patent documents the following abbreviations are often used: Engine a device for continuously converting fluid energy into mechanical power, Thus, this term includes, for example, steam piston engines or steam turbines, per se, or internal-combustion piston engines, but it excludes single-stroke devices. Machine a device which could equally be an engine and a pump, and not a device which is restricted to an engine or one which is restricted to a pump. -
Small Engine Parts and Operation
1 Small Engine Parts and Operation INTRODUCTION The small engines used in lawn mowers, garden tractors, chain saws, and other such machines are called internal combustion engines. In an internal combustion engine, fuel is burned inside the engine to produce power. The internal combustion engine produces mechanical energy directly by burning fuel. In contrast, in an external combustion engine, fuel is burned outside the engine. A steam engine and boiler is an example of an external combustion engine. The boiler burns fuel to produce steam, and the steam is used to power the engine. An external combustion engine, therefore, gets its power indirectly from a burning fuel. In this course, you’ll only be learning about small internal combustion engines. A “small engine” is generally defined as an engine that pro- duces less than 25 horsepower. In this study unit, we’ll look at the parts of a small gasoline engine and learn how these parts contribute to overall engine operation. A small engine is a lot simpler in design and function than the larger automobile engine. However, there are still a number of parts and systems that you must know about in order to understand how a small engine works. The most important things to remember are the four stages of engine operation. Memorize these four stages well, and everything else we talk about will fall right into place. Therefore, because the four stages of operation are so important, we’ll start our discussion with a quick review of them. We’ll also talk about the parts of an engine and how they fit into the four stages of operation. -
Building a Small Horizontal Steam Engine
Building a Small Horizontal Steam Engine The front cylinder head is a pipe cap, THE small engine described in this the exterior of which is turned to pre- article was built by the writer in sent a more pleasing appearance, and his spare time—about an hour a day for drilled and threaded to receive the stuff- four months—and drives the machinery ing box, Fig. 2. The distance between in a small shop. At 40-lb. gauge pres- the edge of the front-end steam port and sure, the engine runs at 150 r.p.m., under the inner side of the cap, when screwed full load, and delivers a little over .4 home, should be much less than that brake horsepower. A cast steam chest, shown, not over ¼ in., for efficiency, and with larger and more direct steam ports, the same at the rear end. When the to reduce condensation losses; less clear- cap has been permanently screwed on ance in the cylinder ends, and larger the cylinder, one side is flattened, as bearing surfaces in several places, would shown, on the shaper or grinder, and the bring the efficiency of the engine up to a steam ports laid out and drilled. It would much higher point than this. In the be a decided advantage to make these writer's case, however, the engine is de- ports as much larger than given as is livering ample power for the purpose to possible, as the efficiency with ½-in. ports which it is applied, and consequently is far below what it might be. -
Walschaerts Valve-Gear 2 Return Cranks with Steel Screws & Nuts
This pack contains the following parts: - Walschaerts Valve-Gear 2 Return Cranks with steel screws & nuts. 2 Expansion links with bushes & This kit contains parts to construct 2BA nuts. a set of Walschaerts type valve- 2 Lifting arms with grub screws & Allen key. gear as used on ROUNDHOUSE 2 Lifting links. locomotives. It is of a simplified 4 M2 steel screws & nuts. design, which does not use a 6 5BA steel washers. combination lever and is intended 2 Radius rods. for use with the ROUNDHOUSE 2 Weigh shaft brackets 1 Weigh shaft. Cylinder set. 2 Starlock washers 2 Roll pins. NOTE:- Frames, Cylinders, 6 Short crank pins. Coupling Rods, Connecting Rods, 2 Plain crank pins Axles and Outside Cranks are not included with this set of parts. 1 Push Rod Connector, Screw & Starlock. 1 Stainless Steel spring & Long Crank Pin. 1 Reversing lever handle. 1 Reversing lever base. 3 M2 screws and nuts. 2 M3 mounting screws. 1 Steel push rod & quicklink connector. Roundhouse Engineering Co. Ltd 2 Eccentric rods. Units 6 to 9, Churchill Business Park, Churchill Road, Wheatley, Doncaster. DN1 2TF. England. Tel 01302 328035 Fax 01302 761312 Email: [email protected] www.roundhouse-eng.com 1 Walschaerts Valve-Gear Part Number WVG Assembly of Walschaerts type valve-gear 1). Radius Rod. 2). Lifting Link. 3). Lifting Arm. Diagram4). Expansion showing Linkgeneral Bush. arrangement 5). Weigh of Walschaerts Shaft Bracket valve (Penguin). gear. NOTE:- Frames, Coupling rods, connecting rods and outside cranks are not included6). Weigh with this Shaft. set of 7). parts. Starlock Washer. 8). 2BA Nut. -
Steam and You! How Steam Engines Helped the United States to Expand Reading
Name____________________________________ Date ____________ Steam and You! How Steam Engines Helped The United States To Expand Reading How Is Steam Used To Help People? (Please fill in any blank spaces as you read) Have you ever observed steam, also known as water vapor? For centuries, people have observed steam and how it moves. Describe steam on the line below. Does it rise or fall?____________________________________________________________ Steam is _______ and it ___________. When lots of steam moves into a pipe, it creates pressure that can be used to move things. Inventors discovered about 300 years ago that they could use steam to power machines. These machines have transformed human life. Steam is used today to help power ships and to spin large turbines that generate electricity for millions of people throughout the world. The steam engine was one of the most important inventions of the Industrial Revolution that occurred about from about 1760 to 1840. The Industrial Revolution was a time when machine technology rapidly changed society. Steam engines were used to power train locomotives, steamboats, machines in factories, equipment in mines, and even automobiles before other kinds of engines were invented. Boiling water in a tea kettle produces A steamboat uses a steam engine to steam. Steam can power a steam engine. turn a paddlewheel to move the boat. A steam locomotive was powered when A steam turbine is a large metal cylinder coal or wood was burned inside it to boil with large fan blades that can spin when water to make steam. The steam steam flows through its blades. -
Poppet Valve
POPPET VALVE A poppet valve is a valve consisting of a hole, usually round or oval, and a tapered plug, usually a disk shape on the end of a shaft also called a valve stem. The shaft guides the plug portion by sliding through a valve guide. In most applications a pressure differential helps to seal the valve and in some applications also open it. Other types Presta and Schrader valves used on tires are examples of poppet valves. The Presta valve has no spring and relies on a pressure differential for opening and closing while being inflated. Uses Poppet valves are used in most piston engines to open and close the intake and exhaust ports. Poppet valves are also used in many industrial process from controlling the flow of rocket fuel to controlling the flow of milk[[1]]. The poppet valve was also used in a limited fashion in steam engines, particularly steam locomotives. Most steam locomotives used slide valves or piston valves, but these designs, although mechanically simpler and very rugged, were significantly less efficient than the poppet valve. A number of designs of locomotive poppet valve system were tried, the most popular being the Italian Caprotti valve gear[[2]], the British Caprotti valve gear[[3]] (an improvement of the Italian one), the German Lentz rotary-cam valve gear, and two American versions by Franklin, their oscillating-cam valve gear and rotary-cam valve gear. They were used with some success, but they were less ruggedly reliable than traditional valve gear and did not see widespread adoption. In internal combustion engine poppet valve The valve is usually a flat disk of metal with a long rod known as the valve stem out one end. -
History of a Forgotten Engine Alex Cannella, News Editor
POWER PLAY History of a Forgotten Engine Alex Cannella, News Editor In 2017, there’s more variety to be found un- der the hood of a car than ever. Electric, hybrid and internal combustion engines all sit next to a range of trans- mission types, creating an ever-increasingly complex evolu- tionary web of technology choices for what we put into our automobiles. But every evolutionary tree has a few dead end branches that ended up never going anywhere. One such branch has an interesting and somewhat storied history, but it’s a history that’s been largely forgotten outside of columns describing quirky engineering marvels like this one. The sleeve-valve engine was an invention that came at the turn of the 20th century and saw scattered use between its inception and World War II. But afterwards, it fell into obscurity, outpaced (By Andy Dingley (scanner) - Scan from The Autocar (Ninth edition, circa 1919) Autocar Handbook, London: Iliffe & Sons., pp. p. 38,fig. 21, Public Domain, by the poppet valves we use in engines today that, ironically, https://commons.wikimedia.org/w/index.php?curid=8771152) it was initially developed to replace. Back when the sleeve-valve engine was first developed, through the economic downturn, and by the time the econ- the poppet valves in internal combustion engines were ex- omy was looking up again, poppet valve engines had caught tremely noisy contraptions, a concern that likely sounds fa- up to the sleeve-valve and were quickly becoming just as miliar to anyone in the automotive industry today. Charles quiet and efficient. -
Comparative Tests of Illinois Central Railroad Locomotives No. 920 and No
Gibson S Lorenz (Comparative Tests of Illinois Centra! Railroad Locomotives No. 920 & No. 940 Rsilwsv A\cchfii?Jc3.] Engineering univrrsity . 'OV 'J LL. LIBRARY + * ^ ^. UNIVERSITY OF ILLINOIS LIBRARY Class Book Volume Ja 09-20M ^ '.V IF * # 4 Digitized by the Internet Archive in 2013 http://archive.org/details/comparativetestsOOgibs COMPARATIVE TESTS OF ILLINOIS CENTRAL RAILROAD LOCOMOTIVES NO. 920 AND NO. 940 BY MILES OTTO GIBSON FREDERICK AYRES LORENZ THESIS FOR THE DEGREE OF BACHELOR OF SCIENCE IN RAILWAY MECHANICAL ENGINEERING IN THE COLLEGE OF ENGINEERING OF THE UNIVERSITY OF ILLINOIS Presented June, 1909 r!6 UNIVERSITY OF ILLINOIS June 1, 190 9 THIS IS TO CERTIFY THAT THE THESIS PREPARED UNDER MY SUPERVISION BY MILES OTTO GIBSON and FREDERICK AYRES LORENZ ENTITLED COMPARATIVE TESTS OP ILLINOIS CENTRAL RAILROAD LOCOMO- TIVES No. 920 AND No. 940 IS APPROVED BY ME AS FULFILLING THIS PART OF THE REQUIREMENTS FOR THE degree of Bachelor of Science in Railway Mechanical Engineering iWstructor/n Charge. APPROVED: head of department of Railway Engineering 1 45239 i I iLnlih UJb UiJ THiU T 5 , Page I • Introduction 1 II • Object l T T T III • Description of the Locomotives, Engine and Boiler Lata 1 1. Table I. General Dimensions 4 2. Table II. Cylinder " 5 3. Table III. Boiler " G Description of Allfree-Eubbell Valve and Cylinders 7 I V . Preparation. 1. Front end 14T A 2. Reducing apparatus 1 1 3. Bells 141 A 4. Cab arrangements 1 A 5. Water measurements T A 6. Dynamometer oar 14 7. Revolution counters 1 / 8. Observers 1 I T ft . -
Greensteam Design Report: Double-Acting Uniflow Engine Part
Greensteam Design Report: Double-acting Uniflow Engine Tae Rugh, Summer 2020 This is a single-cylinder double-acting uniflow engine with bash valve actuation. The cylinder has steam inlets on both sides, so that while one side is in power stroke, the other is in return stroke. The bash mechanism means that this engine does not need to draw from the shaft’s rotation for valve timing, which significantly reduces the complexity and number of moving parts. The drawback is that control of inlet cutoff is severely limited by geometry such that the inlet must be open before top dead center for the same amount of time as it remains open after top dead center. A single uniflow exhaust port is located in the center of the cylinder block and used for both sides. Part Breakdown The driveshaft consists of an overhung crank, flywheel, and shaft. The crank is overhung in order to reduce complexities in manufacturing. A bronze bushing is pressed into the crank and holds the crank pin, which is pressed into the piston’s connecting rod. The crank is secured to the shaft by a cotter pin. The flywheel is set to the shaft by two set screws, angled at 45°. The cylinder block includes the piston chamber, uniflow exhaust ports, and bash valves. An inner cylinder sleeve is used to maximize the area for exhaust to escape while maintaining guiding rails to keep the piston aligned. The groove on the inner cylinder allows exhaust exiting through any of the slots to continue to flow out through the exhaust port in the cylinder block. -
WSA Engineering Branch Training 3
59 RECIPROCATING STEAM ENGINES Reciprocating type main engines have been used to propel This is accomplished by the guide and slipper shown in the ships, since Robert Fulton first installed one in the Clermont in drawing. 1810. The Clermont's engine was a small single cylinder affair which turned paddle wheels on the side of the ship. The boiler was only able to supply steam to the engine at a few pounds pressure. Since that time the reciprocating engine has been gradually developed into a much larger and more powerful engine of several cylinders, some having been built as large as 12,000 horsepower. Turbine type main engines being much smaller and more powerful were rapidly replacing reciprocating engines, when the present emergency made it necessary to return to the installation of reciprocating engines in a large portion of the new ships due to the great demand for turbines. It is one of the most durable and reliable type engines, providing it has proper care and lubrication. Its principle of operation consists essentially of a cylinder in which a close fitting piston is pushed back and forth or up and down according to the position of the cylinder. If steam is admitted to the top of the cylinder, it will expand and push the piston ahead of it to the bottom. Then if steam is admitted to the bottom of the cylinder it will push the piston back up. This continual back and forth movement of the piston is called reciprocating motion, hence the name, reciprocating engine. To turn the propeller the motion must be changed to a rotary one.