Design of a Simulation Software to Optimize the Train Driving Strategy for Urban Rail Transit Yi-Hong CHANG, Ru NIU, Tao TANG, S
Total Page:16
File Type:pdf, Size:1020Kb
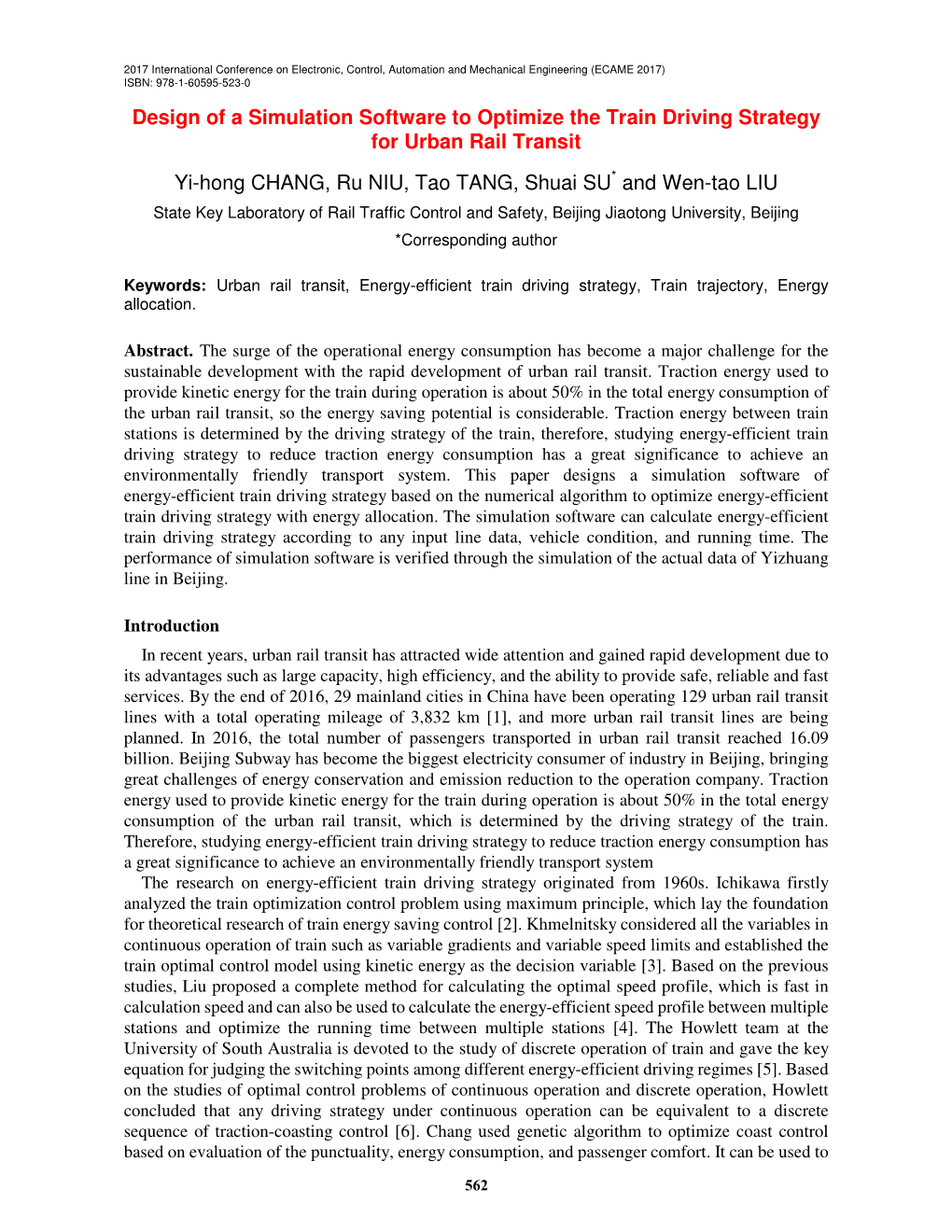
Load more
Recommended publications
-
Smart Train Operation Algorithms Based on Expert Knowledge and Ensemble Cart for the Electric Locomotive,” Knowledge-Based Systems, Vol
PREPRINT VERSION. PUBLISHED IN IEEE TRANSACTIONS ON SYSTEMS, MAN, AND CYBERNETICS: SYSTEMS - https://ieeexplore.ieee.org/abstract/document/9144488. Smart Train Operation Algorithms based on Expert Knowledge and Reinforcement Learning Kaichen Zhou, Student Member, IEEE, Shiji Song, Member, IEEE, Anke Xue, Member, IEEE Keyou You, Member, IEEE and Hui Wu, Student Member, IEEE Abstract—During recent decades, the automatic train operation on the train’s trajectory. And improving the performance of the (ATO) system has been gradually adopted in many subway systems ATO system has become a focus in the field of the transportation for its low-cost and intelligence. This paper proposes two smart system. In most cases, research on the urban subway system train operation algorithms by integrating the expert knowledge with reinforcement learning algorithms. Compared with previous works, can be divided into two parts: the energy-efficient train operation the proposed algorithms can realize the control of continuous action committed to designing an off-line optimized train trajectory, and for the subway system and optimize multiple critical objectives the automatic train tracking method to track the real-time train without using an offline speed profile. Firstly, through learning speed-distance profile. historical data of experienced subway drivers, we extract the expert knowledge rules and build inference methods to guarantee the riding During recent years, lot of studies are devoted to designing comfort, the punctuality, and the safety of the subway system. Then an off-line optimized train trajectory to improve the energy we develop two algorithms for optimizing the energy efficiency of efficiency. For example, Albrecht et al. -
Dynamic Passenger Demand Oriented Metro Train Scheduling with Energy-Efficiency and Waiting Time Minimization: Mixed-Integer Linear Programming Approaches
Transportation Research Part B 97 (2017) 182–213 Contents lists available at ScienceDirect Transportation Research Part B journal homepage: www.elsevier.com/locate/trb Dynamic passenger demand oriented metro train scheduling with energy-efficiency and waiting time minimization: Mixed-integer linear programming approaches ∗ Jiateng Yin a, Lixing Yang a, , Tao Tang a, Ziyou Gao a, Bin Ran b a State Key Laboratory of Rail Traffic Control and Safety, Beijing Jiaotong University, Beijing, 10 0 044, China b Department of Civil and Environmental Engineering, University of Wisconsin-Madison, Madison, WI, 53706, USA a r t i c l e i n f o a b s t r a c t Article history: In the daily operation of metro systems, the train scheduling problem aims to find a set Received 23 July 2016 of space-time paths for multiple trains that determine their departure and arrival times at Revised 4 January 2017 metro stations, while train operations are in charge of selecting the best operational speed Accepted 5 January 2017 to satisfy the punctuality and operation costs. Different from the most existing researches Available online 13 January 2017 that treat these two problems separately, this paper proposes an integrated approach for Keywords: the train scheduling problem on a bi-direction urban metro line in order to minimize the Metro train scheduling operational costs (i.e., energy consumption) and passenger waiting time. More specifically, Energy efficiency we simultaneously consider (1) the train operational velocity choices that correspond to Dynamic passenger demands the energy consumption of trains on each travelling arc, and (2) the dynamic passenger Space-time network demands at each station for the calculation of total passenger waiting time in the planning Regenerative energy horizon. -
Riding Comfort Evaluation Based on Longitudinal Acceleration for Urban Rail Transit—Mathematical Models and Experiments in Beijing Subway
sustainability Article Riding Comfort Evaluation Based on Longitudinal Acceleration for Urban Rail Transit—Mathematical Models and Experiments in Beijing Subway Huiru Ma 1, Dewang Chen 2,∗ and Jiateng Yin 1,∗ 1 State Key Laboratory of Rail Traffic Control and Safety, Beijing Jiaotong University, Beijing 100044, China; [email protected] 2 College of Mathematics and Computer Science, Fuzhou University, Fuzhou 350116, China * Correspondence: [email protected] (D.C.); [email protected] (J.Y.) Received: 12 May 2020; Accepted: 28 May 2020; Published: 3 June 2020 Abstract: Riding comfort is an important index to measure the quality of service for railways, especially for congested urban rail transit systems where the majority of passengers cannot find a seat. Existing studies usually employ the value of longitudinal acceleration as the key indicator to evaluate the riding comfort of vehicles, while there is no validated mathematical models to evaluate the riding comfort of urban rail trains from the perspective of passengers. This paper aims to employ the collected longitudinal acceleration data and passengers’ feedback data in Beijing subway to qualitatively measure and validate the riding comfort of transit trains. First, we develop four regular fuzzy sets based comfort measurement models, where the parameters of the fuzzy sets are determined by experiences of domain experts and the field data. Then a combinational model is given by averaging the four regular fuzzy set models to elaborate a comprehensive measurement for the riding comfort. In order to verify the developed models, we conducted a questionnaire survey in Beijing subway. The surveyed riding comfort data from passengers and the measured acceleration data are used to validate and optimize the proposed models. -
Integrated Line Planning and Train Scheduling for an Urban Rail Transit Line∗
Delft University of Technology Delft Center for Systems and Control Technical report 16-006 Integrated line planning and train scheduling for an urban rail transit line∗ Y. Wang, X. Pan, S. Su, F. Cao, T. Tang, B. Ning, and B. De Schutter If you want to cite this report, please use the following reference instead: Y. Wang, X. Pan, S. Su, F. Cao, T. Tang, B. Ning, and B. De Schutter, “Integrated line planning and train scheduling for an urban rail transit line,” Transportation Research Record, no. 2540, pp. 66–75, 2016. Delft Center for Systems and Control Delft University of Technology Mekelweg 2, 2628 CD Delft The Netherlands phone: +31-15-278.51.19 (secretary) fax: +31-15-278.66.79 URL: http://www.dcsc.tudelft.nl ∗This report can also be downloaded via http://pub.deschutter.info/abs/16_006.html Integrated Line Planning and Train Scheduling for an Urban Rail Transit Line Y. Wang,∗ X. Pan,y S. Su,z F. Cao,x T. Tang,{ B. Ning,k B. De Schutter∗∗ Abstract In this paper, an integrated line planning and train scheduling model based on the circulation of trains is proposed to reduce the passenger dissatisfaction and the operation costs for an urban rail transit line. In the integrated model, the turnaround operations of trains and the departures and arrivals of trains at the depot are included. Furthermore, binary variables are introduced to indicate whether a circulation of a train (i.e., a train service) exists or not and a discrete-event model is used to determine the order of the train services.