Femtosecond-Laser Hyperdoping and Texturing of Silicon for Photovoltaic Applications
Total Page:16
File Type:pdf, Size:1020Kb
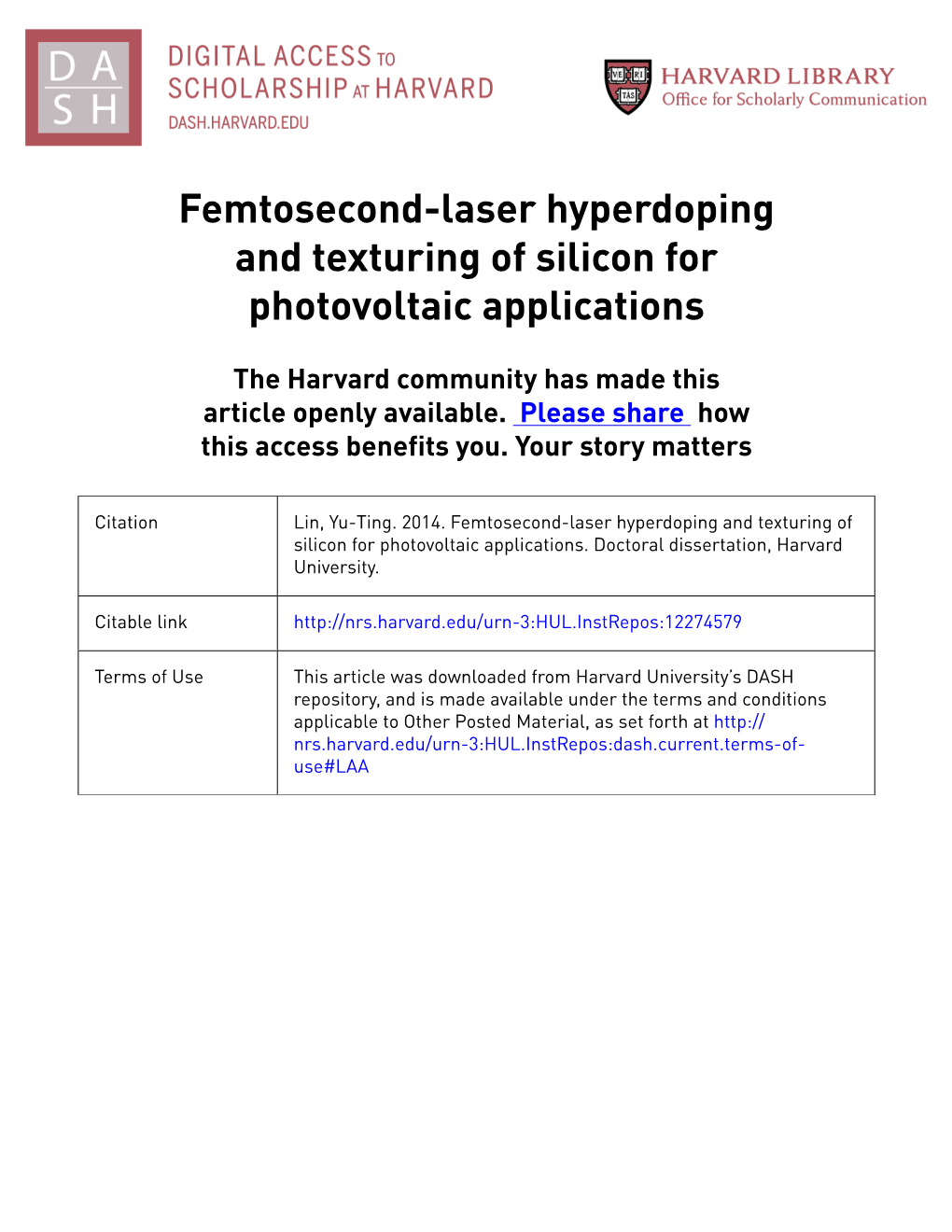
Load more
Recommended publications
-
Call for Papers, 35Th IEEE PVSC[2]
CALL FOR PAPERS THE 35th IEEE PHOTOVOLTAIC SPECIALISTS CONFERENCE June 20-25, 2010 Hawaii Convention Center Honolulu, Hawaii PLEASE CHECK OUR WEB SITE AT www.ieee-pvsc.org Sponsored by the IEEE Electron Devices Society Invitation from the Chair On behalf of the Organizing, Cherry, and International Committees, it is my great pleasure to invite you to join the 35th IEEE Photovoltaic Specialist Conference, June 20-25, 2010, at the Hawaiian Convention Center in Honolulu, Hawaii. We continue our role as the premier technical conference covering all aspects of PV technology from basic material science to installed system performance. We also continue our Industrial Exhibition that brings our PV Specialists together with the PV industry. Set with the backdrop of tremendous progress in Hawaiian renewable energy initiatives and the beautiful location of Waikiki, this will be THE PV conference in 2010. Highlights include: Strong Technical Program: In addition to our traditional eight topical areas, we have created a separate Area for Organic Photovoltaics, and we created a new area titled: “Advances in Characterization of Photovoltaics”. Full Day of Tutorials: We will have nine tutorials this time, consisting of half-day lectures taught by experts in the field. The topics will range from the basic physics of solar cell operation to details about the latest trends in the industry that will be valuable to newcomers to PV as well as seasoned veterans. Industrial Exhibition: Within the gorgeous Hawaiian Convention Center, our exhibit space will be designed to bring together the commercial sector and the Photovoltaic Technologist. Our focus will be on measurement and characterization tools, and we will be highlighting space PV applications. -
Handbook of Photovoltaic Science and Engineering
Handbook of Photovoltaic Science and Engineering Edited by Antonio Luque Instituto de Energ´ıa Solar, Universidad Polit´ecnica de Madrid, Spain and Steven Hegedus Institute of Energy Conversion, University of Delaware, USA Copyright 2003 John Wiley & Sons Ltd, The Atrium, Southern Gate, Chichester, West Sussex PO19 8SQ, England Telephone (+44) 1243 779777 Email (for orders and customer service enquiries): [email protected] Visit our Home Page on www.wileyeurope.com or www.wiley.com All Rights Reserved. No part of this publication may be reproduced, stored in a retrieval system or transmitted in any form or by any means, electronic, mechanical, photocopying, recording, scanning or otherwise, except under the terms of the Copyright, Designs and Patents Act 1988 or under the terms of a licence issued by the Copyright Licensing Agency Ltd, 90 Tottenham Court Road, London W1T 4LP, UK, without the permission in writing of the Publisher. Requests to the Publisher should be addressed to the Permissions Department, John Wiley & Sons Ltd, The Atrium, Southern Gate, Chichester, West Sussex PO19 8SQ, England, or emailed to [email protected], or faxed to (+44) 1243 770620. This publication is designed to provide accurate and authoritative information in regard to the subject matter covered. It is sold on the understanding that the Publisher is not engaged in rendering professional services. If professional advice or other expert assistance is required, the services of a competent professional should be sought. Other Wiley Editorial Offices John Wiley & Sons Inc., 111 River Street, Hoboken, NJ 07030, USA Jossey-Bass, 989 Market Street, San Francisco, CA 94103-1741, USA Wiley-VCH Verlag GmbH, Boschstr. -
Amorphous Silicon Based Solar Cells
Syracuse University SURFACE Physics College of Arts and Sciences 2003 Amorphous Silicon Based Solar Cells Xunming Deng University of Toledo Eric A. Schiff Syracuse University Follow this and additional works at: https://surface.syr.edu/phy Part of the Physics Commons Recommended Citation "Amorphous Silicon Based Solar Cells," Xunming Deng and Eric A. Schiff, in Handbook of Photovoltaic Science and Engineering, Antonio Luque and Steven Hegedus, editors (John Wiley & Sons, Chichester, 2003), pp. 505 - 565. This Book Chapter is brought to you for free and open access by the College of Arts and Sciences at SURFACE. It has been accepted for inclusion in Physics by an authorized administrator of SURFACE. For more information, please contact [email protected]. 12 Amorphous Silicon–based Solar Cells Xunming Deng1 and Eric A. Schiff2 1University of Toledo, Toledo, OH, USA, 2Syracuse University, Syracuse, NY, USA 12.1 OVERVIEW 12.1.1 Amorphous Silicon: The First Bipolar Amorphous Semiconductor Crystalline semiconductors are very well known, including silicon (the basis of the inte- grated circuits used in modern electronics), Ge (the material of the first transistor), GaAs and the other III-V compounds (the basis for many light emitters), and CdS (often used as a light sensor). In crystals, the atoms are arranged in near-perfect, regular arrays or lattices. Of course, the lattice must be consistent with the underlying chemical bonding properties of the atoms. For example, a silicon atom forms four covalent bonds to neigh- boring atoms arranged symmetrically about it. This “tetrahedral” configuration is perfectly maintained in the “diamond” lattice of crystal silicon. -
Fullspectrum Sixth Framework Program
FULLSPECTRUM SIXTH FRAMEWORK PROGRAM Project no. SES6-CT-2003-502620 FULLSPECTRUM A new PV wave making more efficient use of the solar spectrum Instrument: Integrated Project Thematic Priority: Sustainable development, global change and ecosystems Sub-priority: Sustainable energy systems Publishable Executive Summary of Fullspectrum updated after the 5th period Period covered: from 1/11/2006 to 31/10/2007 Date of preparation: 5/12/2008 Start date of project: 1/11/2003 Duration: 60 months Project coordinator name: Prof. Antonio Luque López Project coordinator organisation name: Instituto de Energía Solar – Universidad Politécnica de Madrid (IES-UPM) Version 1_0_0 Filed as IES-UPM internal report 0822 Publishable executive summary: FULLSPECTRUM A new PV wave making more efficient use of the solar spectrum Sponsored by the European Commission: 6th Framework Program: SES6-CT-2003-502620 FULLSPECTRUM is a project sponsored by the European Commission whose primary objective is to make use of the FULL solar SPECTRUM to produce electricity. The necessity for this research is easily understood, for example, from the fact that present commercial solar cells used for terrestrial applications are based on single gap semiconductor solar cells. These cells can by no means make use of the energy of below bandgap energy photons since these simply cannot be absorbed by the material. Partnership involves nineteen Research Centres and Institutions, namely: − IES-UPM Instituto de Energía Solar - Universidad http://www.ies.upm.es Politécnica de Madrid (Coordinator) -
Solar Energy in Spain
New Technologies in Spain Solar Energy As researchers continue to explore new ways to promote and improve solar power, Spanish companies are becoming world leaders in this emerging field. Innovation in Motion Spain is now the world’s eighth-largest economy and the fastest growing in the European Union. It represents more than 2.5% of the world’s total GDP and a third of all new jobs created in the Eurozone last year. Spain is fast becoming a leader in in- novation and generating advanced solutions in the industries of aerospace, renewable energies, water treatment, rail, biotechnol- ogy, industrial machinery and civil engineering. Spanish firms are innovators in the field of public-works finance and management, where six of the world’s top ten companies are from Spain. Where innovation thrives, so will the successful global enterprises of the 21st century. To find out more about technology opportunities in Spain, visit: www.spainbusiness.com To find out more about New Technologies in Spain, visit: www.technologyreview.com/spain/solar Mirrors focus the power of about 600 suns on a receiver at the top of the Solúcar tower. Solar Energy in Spain Spain is forging ahead with plans to build concentrating solar power plants, establishing the country and Spanish companies as world leaders in the emerging field. At the same time, the number of installed photovoltaic systems is growing exponentially, and researchers continue to explore new ways to promote and improve solar power. This is the seventh in an eight-part series highlighting new technologies in Spain and is produced by Technology Review, Inc.’s custom-publishing division in partnership with the Trade Commission of Spain. -
High-Efficiency Multi-Junction Solar Cells: Current Status and Future Potential
High-efficiency multi-junction solar cells: Current status and future potential Natalya V. Yastrebova, Centre for Research in Photonics, University of Ottawa, April 2007 Table of contents Introduction................................................................................................................................. 2 Basic principles of multi-junction solar cells.............................................................................. 6 Bandgaps .................................................................................................................................. 6 Lattice constants ....................................................................................................................... 8 Current matching ..................................................................................................................... 9 Fabrication of present-day multi-junction solar cells................................................................ 9 Future design improvements .................................................................................................... 12 Design optimization of the existing layers .............................................................................. 12 Increasing the number of junctions ....................................................................................... 12 Inclusion of semiconductor quantum dots ............................................................................. 13 Concentrator photovoltaics ..................................................................................................... -
Laura Barrutia Poncela Licenciada En Ciencias Físicas 2017
UNIVERSIDAD POLITÉCNICA DE MADRID ESCUELA TÉCNICA SUPERIOR DE INGENIEROS DE TELECOMUNICACIÓN OPTIMIZATION PATHWAYS TO IMPROVE GaInP/GaInAs/Ge TRIPLE JUNCTION SOLAR CELLS FOR CPV APPLICATIONS TESIS DOCTORAL Laura Barrutia Poncela Licenciada en Ciencias Físicas 2017 UNIVERSIDAD POLITÉCNICA DE MADRID Instituto de Energía Solar Departamento de Electrónica Física Escuela Técnica Superior de Ingenieros de Telecomunicación TESIS DOCTORAL OPTIMIZATION PATHWAYS TO IMPROVE GaInP/GaInAs/Ge TRIPLE JUNCTION SOLAR CELLS FOR CPV APPLICATIONS AUTOR Laura Barrutia Poncela Licenciada en Ciencias Físicas DIRECTORES Carlos Algora del Valle Doctor en Ciencias Físicas Ignacio Rey-Stolle Prado Doctor Ingeniero de Telecomunicación 2017 Tribunal nombrado por el Magfco. Y Excmo. Sr Rector de la Universidad Politécnica de Madrid. PRESIDENTE: VOCALES: SECRETARIO: SUPLENTES: Realizado el acto de defensa y lectura de la Tesis en Madrid, el día ___de_____de 2017 Calificación: EL PRESIDENTE LOS VOCALES EL SECRETARIO A la memoria de mi abuela Ole, por todo el cariño y esfuerzo que siempre puso en nosotras. A mi familia, a Andrés, por todo su amor y apoyo constante. i “Hay una fuerza motriz más poderosa que el vapor, la electricidad y la energía atómica: la voluntad ” Albert Einstein iii Agradecimientos Muchas veces pienso en cómo he llegado hasta aquí y me vienen a la cabeza muchas personas que con su conocimiento y cariño me ayudaron poco a poco a ir descubriendo mi camino. Maruja me enseñó mis primeros conocimientos de la física e influyó en gran parte a que decidiese estudiar Físicas en la Universidad Complutense de Madrid. Allí conocí a muy buenos profesores. Me quedo especialmente con el afecto de Pedro Hidalgo, que consiguió que no solo estudiase la carrera, sino que me adentrase y me gustase un poco más el mundo de la ciencia realizando un trabajo académicamente dirigido con él. -
Concentrator Photovoltaics
Springer Series in Optical Sciences 130 Concentrator Photovoltaics Bearbeitet von Antonio Luque López, Viacheslav M. Andreev 1. Auflage 2007. Buch. xiv, 346 S. Hardcover ISBN 978 3 540 68796 2 Format (B x L): 15,5 x 23,5 cm Gewicht: 767 g Weitere Fachgebiete > Technik > Energietechnik, Elektrotechnik > Solarenergie, Photovoltaik Zu Inhaltsverzeichnis schnell und portofrei erhältlich bei Die Online-Fachbuchhandlung beck-shop.de ist spezialisiert auf Fachbücher, insbesondere Recht, Steuern und Wirtschaft. Im Sortiment finden Sie alle Medien (Bücher, Zeitschriften, CDs, eBooks, etc.) aller Verlage. Ergänzt wird das Programm durch Services wie Neuerscheinungsdienst oder Zusammenstellungen von Büchern zu Sonderpreisen. Der Shop führt mehr als 8 Millionen Produkte. 1 Past Experiences and New Challenges of PV Concentrators G. Sala and A. Luque 1.1 Introduction The general idea of a photovoltaic (PV) concentrator is to use optics to focus sunlight on a small receiving solar cell (Fig. 1.1); thus, the cell area in the focus of the concentrator can be reduced by the concentration ratio. At the same time the light intensity on the cell is increased by the same ratio. In other words, cell surface is replaced by lens or mirror surface in PV concentrators and the efficiency and price of both determine the optimum configuration. Medium- and high-concentration systems require accurate tracking to maintain the focus of the light on the solar cells as the sun moves through- out the day. This adds extra costs and complexity to the system and also increases the maintenance burden during operation. For systems with small solar cells, or using low concentration, passive cooling (interchange of heat with the surrounding air) is feasible. -
Understanding Intermediate-Band Solar Cells
Understanding intermediate-band solar cells Antonio Luque , Antonio Marti and Colin Stanley The intermediate-band solar cell is designed to provide a large photogenerated current while maintaining a high output voltage. To make this possible, these cells incorporate an energy band that is partially filled with electrons within the forbidden bandgap of a semiconductor. Photons with insufficient energy to pump electrons from the valence band to the conduction band can use this intermediate band as a stepping stone to generate an electron-hole pair. Nanostructured materials and certain alloys have been employed in the practical implementation of intermediate-band solar cells, although challenges still remain for realizing practical devices. Here we offer our present understanding of intermediate-band solar cells, as well as a review of the different approaches pursed for their practical implementation. We also discuss how best to resolve the remaining technical issues. he intermediate-band (IB) solar cell consists of an IB to the initial detailed balance analysis of the IB solar cell4,6-8 have material sandwiched between two ordinary n- and p-type confirmed its potential for high efficiency. It is the high value of the T semiconductors1, which act as selective contacts to the IB solar cells limiting efficiency that has attracted many scientists to conduction band (CB) and valence band (VB), respectively (Fig. la). work in this field. In an IB material, sub-bandgap energy photons are absorbed through transitions from the VB to the IB and from the IB to the Quantum dot IB solar cells CB, which together add up to the current of conventional photons The energy levels of the confined states in a quantum dot (QD) can absorbed through the VB-CB transition. -
Basic Research Needs for Solar Energy Utilization
On the Cover: One route to harvesting the energy of the sun involves learning to mimic natural photosynthesis. Here, sunlight falls on a porphyrin, one member of a family of molecules that includes the chlorophylls, which play a central role in capturing light and using its energy for photosynthesis in green plants. Efficient light-harvesting of the solar spectrum by porphyrins and related molecules can be used to power synthetic molecular assemblies and solid- state devices — applying the principles of photosynthesis to the produc- tion of hydrogen, methane, ethanol, and methanol from sunlight, water, and atmospheric carbon dioxide. BASIC RESEARCH NEEDS FOR SOLAR ENERGY UTILIZATION Report on the Basic Energy Sciences Workshop on Solar Energy Utilization Chair: Nathan S. Lewis, California Institute of Technology Co-chair: George Crabtree, Argonne National Laboratory Panel Chairs: Solar Electric Arthur J. Nozik, National Renewable Energy Laboratory Solar Fuels Michael R. Wasielewski, Northwestern University Cross-cutting Paul Alivisatos, Lawrence Berkeley National Laboratory Office of Basic Energy Sciences Contact: Harriet Kung, Basic Energy Sciences, U.S. Department of Energy Special Assistance Technical: Jeffrey Tsao, Sandia National Laboratories Elaine Chandler, Lawrence Berkeley National Laboratory Wladek Walukiewicz, Lawrence Berkeley National Laboratory Mark Spitler, National Renewable Energy Laboratory Randy Ellingson, National Renewable Energy Laboratory Ralph Overend, National Renewable Energy Laboratory Jeffrey Mazer, Solar Energy Technologies, U.S. Department of Energy Mary Gress, Basic Energy Sciences, U.S. Department of Energy James Horwitz, Basic Energy Sciences, U.S. Department of Energy Administrative: Christie Ashton, Basic Energy Sciences, U.S. Department of Energy Brian Herndon, Oak Ridge Institute for Science and Education Leslie Shapard, Oak Ridge Institute for Science and Education Publication: Renée M. -
7 Spanish Conference on Electron Devices 2009 Technical Program and Contents
7th Spanish Conference on Electron Devices 2009 Technical Program and Contents Tuesday Feb, 10 2009 17:00 CDE 2009 Registration. 20:00 Welcome reception. Wednesday Feb 11, 2009 09:00 CDE 2009 Registration. 10:00 Opening and Welcome. 10:30 Invited talk: Simulation of Statistical Variability in NanoCMOS Devices, Asen Asenov (University of Glasgow, UK). 11:30 Coffee break. Session 1: Materials, technology and process simulation. Chairperson: Albert Romano (Universitat de Barcelona) 12:00 GaN/AlN Axial Multi Quantum Well Nanowires for Optoelectronic Devices. 1 Sonia` Conesa-Boj (Universitat de Barcelona), Jordi Arbiol (Universitat de Barcelona), Francesca Peiro´ (Universitat de Barcelona), Joan Ramon´ Morante (Universitat de Barcelona), Florian Furtmayr (WSI, Technische Universitat¨ Munchen),¨ C. Stark (WSI, Technische Universitat¨ Munchen),¨ S. Schafer¨ (WSI, Technische Universitat¨ Munchen),¨ M. Stutzmann (WSI, Technische Universitat¨ Munchen),¨ M. Eickhoff (WSI, Technische Universitat¨ Munchen).¨ 12:20 High Quality Ti-Implanted Si Layers above Solid Solubility Limit. 3 Javier Olea (UCM), David Pastor (UCM), Mar´ıa Toledano-Luque (UCM), Enrique San Andres´ (UCM), Ignacio Martil´ (UCM), German´ Gonzalez-D´ ´ıaz (Universidad Complutense de Madrid). 12:40 Improved Integrated Capacitive Elements Based on Porous Silicon. 5 Ana Sancho (CEIT), Javier Gracia (CEIT). 13:00 Study of Atomic Layer Deposited Zirconium Oxide Thin Films by Using Mono-Cyclopentadienyl Based 7 Precursors. Helena Castan´ (Universidad de Valladolid), Salvador Duenas˜ (Universidad de Valladolid), Hector´ Garc´ıa (Universidad de Valladolid), Alfonso Gomez´ (Universidad de Valladolid), Luis Bailon´ (Universidad de Valladolid), K. Kukli (University of Helsinki), J. Niinisto¨ (University of Helsinki), M. Ritala (University of Helsinki), M. Leskela¨ (University of Helsinki). 13:20 Growth of SiNx on Si by ECR Plasma Nitridation. -
The Growth of Solar Concentrator Photovoltaic Markets in the Southwest US Author
MP Title: The Growth of Solar Concentrator Photovoltaic Markets in the Southwest US Author: Sean Connor Advisor: Lincoln Pratson Date: April, 2008 Abstract: Worldwide solar photovoltaic (PV) markets have grown at an average rate at 38% over the past ten years. While polysilicon flat panel PV modules have traditionally dominated the overall solar market, a range of different solar energy conversion technologies are starting to gain market share. One such class of solar technologies, concentrator photovoltaics (CPV), is in its commercial infancy but offers a module manufacturing paradigm to greatly lower the cost of solar electricity production. This paper examines the attributes of CPV and analyzes how it might compete within the overall solar market. The Southwest US is used as a case study to examine specific subsidies, regulations, and business models that will affect the success of CPV. In addition, a financial model was created to examine important factors influencing retail and wholesale PV and CPV project costs under various scenarios. I. INTRODUCTION The global solar electricity market has experienced a second wave of 38 % average annual growth over the past 10 years (Maycock, 2007)spurred on by the lure of a self supporting industry providing clean electricity to the masses. For entrepreneurs, the race is to build cheaper solar systems and take advantage of the current subsidy-dependent demand growth while keeping their sights on making unsubsidized solar competitive with conventional fossil fuel electricity generation. This point of parity is expected to enable solar to take a significant percentage of the enormous market for new electricity generation. With the prize of enormous growth at stake, a multitude of companies have entered the market offering technological innovations and reformulated designs.