Signs and Markings Supervisor
Total Page:16
File Type:pdf, Size:1020Kb
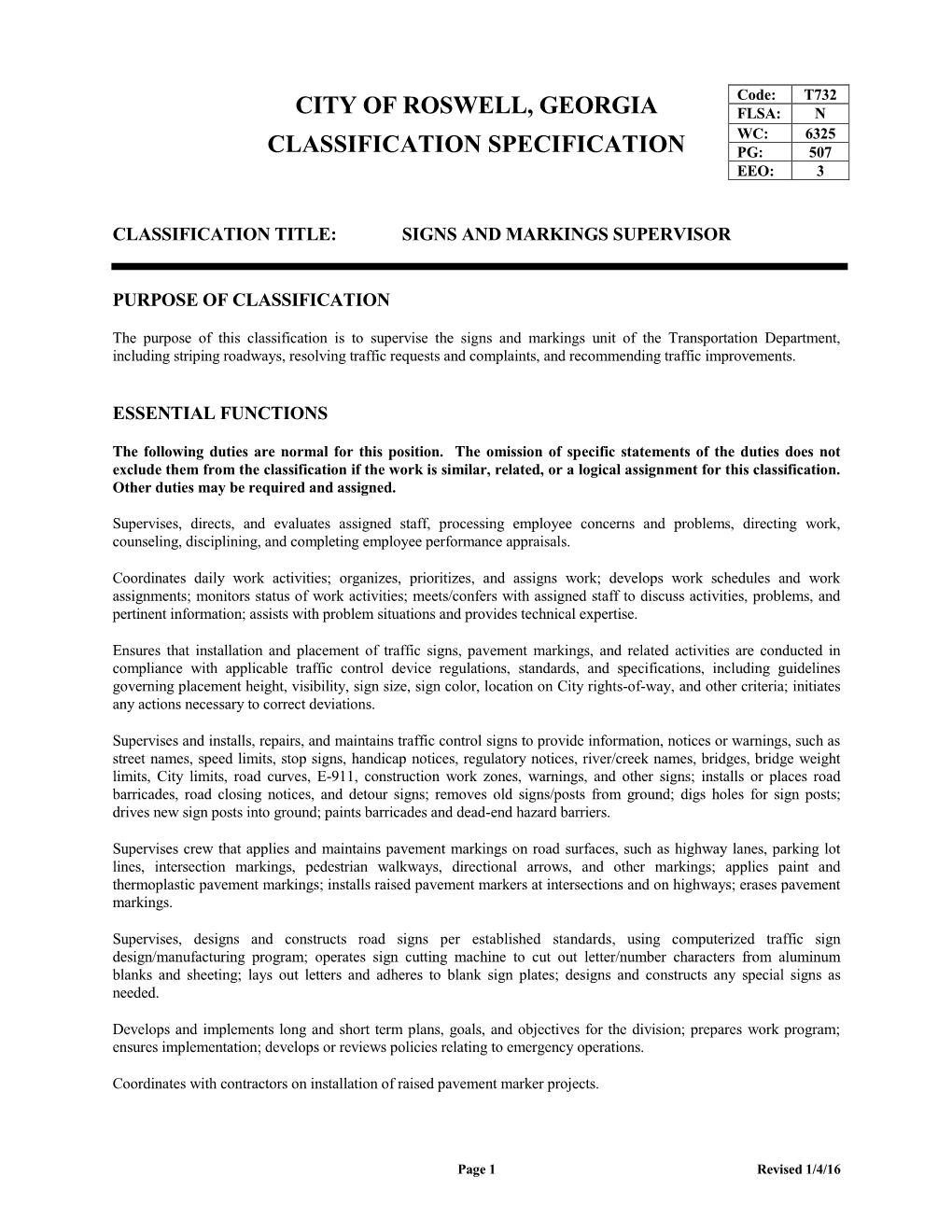
Load more
Recommended publications
-
GDOT Signing and Marking Design Guidelines
Signing and Marking Design Guidelines 8/10/2021 Revision 6.1 Atlanta, GA 30308 This document was developed as part of the continuing effort to provide guidance within the Georgia Department of Transportation in fulfilling its mission to provide a safe, efficient, and sustainable transportation system through dedicated teamwork and responsible leadership supporting economic development, environmental sensitivity and improved quality of life. This document is not intended to establish policy within the Department, but to provide guidance in adhering to the policies of the Department. Your comments, suggestions, and ideas for improvements are welcomed. Please send comments to: State Design Policy Engineer Georgia Department of Transportation One Georgia Center 600 West Peachtree Street, N.W., 26th Floor Atlanta, Georgia 30308 DISCLAIMER The Georgia Department of Transportation maintains this printable document and is solely responsible for ensuring that it is equivalent to the approved Department guidelines. Signing and Marking Design Guidelines Revision History Revision Number Revision Date Revision Summary All - Revised and Combined Interstate and Limited Access 2.0 11/2008 Roadway Signing and Marking Design Guidelines and Non- Interstate Signing and Marking Design Guidelines 2.1 1/2011 All - Revised Figures Chapter 2 - Removed section 2.6 Detail Estimate Chapter 3 - Added Bicycle Warning and Share the Road Sign Guidance and Revised Figures Specified 36” for Warning Signs on State Routes Appendix A - Revised Legend and Figures 3.0 12/2013 All – Major Revision 3.1 10/2015 Section 2.4 - Changed General Notes location. Section 2.5 - Changed the Reflective Sheeting Section 3.1- Removed pavement marking plans Section 3.1.2 - Changed “or” to “and/or”. -
PAVEMENT MARKERS (Rpms) from ROAD SURFACES
GEORGIA DOT RESEARCH PROJECT 10-25 FINAL REPORT DEVELOPMENT OF A METHOD TO REMOVE RAISED- PAVEMENT MARKERS (RPMs) FROM ROAD SURFACES OFFICE OF RESEARCH 15 Kennedy Drive Forest Park, Ga 30297 TECHNICAL REPORT STANDARD TITLE PAGE 1.Report No.: FHWA- 2. Government Accession 3. Recipient's Catalog No.: N/A GA-12-1025 No.: N/A 4. Title and Subtitle: 5. Report Date: June 2012 Development of a Method to Remove Raised- Pavement Markers (RPMs) From Road Surfaces 6. Performing Organization Code: N/A 7. Author(s): Jonathan Holmes 8. Performing Organ. Report No.: 10-25 9. Performing Organization Name and Address: 10. Work Unit No.: N/A Georgia Tech Research Institute Georgia Institute of Technology 11. Contract or Grant No.: 0010280 School of Civil and Environmental Engineering Atlanta, GA 30332-0355 12. Sponsoring Agency Name and Address: 13. Type of Report and Period Covered: Georgia Department of Transportation Final; December 2010 – June 2012 Office of Research 14. Sponsoring Agency Code: N/A 15 Kennedy Drive Forest Park, GA 30297-2534 15. Supplementary Notes: Prepared in cooperation with the U.S. Department of Transportation, Federal Highway Administration. 16. Abstract: The Georgia Department of Transportation (GDOT) uses raised pavement markers (RPMs) widely on roads throughout the State to increase road safety. Each of the approximate 3 million RPMs in Georgia was placed manually. Unfortunately, RPMs do not last as long as the road surface meaning they need to be replaced several times throughout the life of a road. There is a strong desire to remove the RPMs prior to placing new ones. -
Automated Roadway Pavement Marker Placement System
Automated Roadway Pavement Marker Placement System Final Project Report August 2011 FHWA-HIF-11-048 Notice This document is disseminated under the sponsorship of the U.S. Department of Transportation in the interest of information exchange. The U.S. Government assumes no liability for the use of the information contained in this document. This report does not constitute a standard, specification, or regulation. The U.S. Government does not endorse products or manufacturers. Trademarks or manufacturers’ names appear in this report only because they are considered essential to the objective of the document. Trade names mentioned in this report are not intended as an endorsement of any machine, contractor, process, or product. Quality Assurance Statement The Federal Highway Administration (FHWA) provides high-quality information to serve Government, industry, and the public in a manner that promotes public understanding. Standards and policies are used to ensure and maximize the quality, objectivity, utility, and integrity of its information. The FHWA periodically reviews quality issues and adjusts its programs and processes to ensure continuous quality improvement. 1 1. Report No. 2. Government Accession No. 3. Recipient’s Catalog No. FHWA-HIF-11-048 4. Title and Subtitle 5. Report Date Automated Roadway Pavement Marker Placement System: Final Project August 2011 Report 6. Performing Organization Code 7. Authors 8. Performing Organization Report No. Carmine Dwyer 9. Performing Organization Name and Address 10. Work Unit No. (TRAIS) C6B Applied Research Associates, Inc. 100 Trade Centre Drive, Suite 200 11. Contract or Grant No. Champaign, IL 61820 DTFH61-08-G-00004 12. Sponsoring Agency Name and Address 13. -
Markings on Highways and on Private Roads Open to Public Travel Have Important Functions in Providing Guidance and Information for the Road User
DE MUTCD Page 3A-1 CHAPTER 3A. GENERAL Section 3A.01 Functions and Limitations Support: 01 Markings on highways and on private roads open to public travel have important functions in providing guidance and information for the road user. Major marking types include pavement and curb markings, delineators, colored pavements, channelizing devices, and islands. In some cases, markings are used to supplement other traffic control devices such as signs, signals, and other markings. In other instances, markings are used alone to effectively convey regulations, guidance, or warnings in ways not obtainable by the use of other devices. 02 Markings have limitations. Visibility of the markings can be limited by snow, debris, and water on or adjacent to the markings. Marking durability is affected by material characteristics, traffic volumes, weather, and location. However, under most highway conditions, markings provide important information while allowing minimal diversion of attention from the roadway. Section 3A.02 Standardization of Application Standard: 01 Each standard marking shall be used only to convey the meaning prescribed for that marking in this Manual. When used for applications not described in this Manual, markings shall conform in all respects to the principles and standards set forth in this Manual. Guidance: 02 Before any new highway, private road open to public travel (see definition in Section 1A.13), paved detour, or temporary route is opened to public travel, all necessary markings should be in place. Standard: 03 Markings that must be visible at night shall be retroreflective unless ambient illumination assures that the markings are adequately visible. All markings on Interstate highways shall be retroreflective. -
Research on Raised Pavement Markers
56 TRANSPORTATION RESEARCH RECORD 1230 Research on Raised Pavement Markers JOHN T. TIELKING AND JAMES S. NOEL The results of a study directed toward increasing the retention markers are usually found by the roadside, intact and with a time of raised pavement markers on asphalt concrete pavement "divot" of pavement attached to the base. They can become are described. Retention time is believed to be largely limited by a road hazard. A displaced marker thrown through a wind fatigue strength of the pavement surface. The kinematics of a tire shield by a mower resulted in a lawsuit in a Texas highway striking a raised pavement marker were studied by high-speed photography to guide development of a laboratory apparatus that district. simulates pavement fatigue loading by a tire rolling over a marker. A distinct shape effect on retention has been observed (3). A laboratory investigation of the effect of adhesive type on fatigue On all pavements, round ceramic markers (traffic buttons) strength of asphalt pavement was made. It was found that bitu are retained much better than the square-base plastic markers. minous adhesive is distinctly superior to epoxy adhesive on new The retention problem is more serious on asphalt concrete asphalt surfaces. The distinction between bituminous and epoxy pavement (ACP) than on portland cement concrete (PCC) adhesive is less pronounced on stiffer (seasoned) pavements. An instrumented pavement marker to record the number of tire hits pavement. Surveys of square-base markers on ACP have found was also developed during the study. The circuitry is described, loss rates of up to 80 percent in 18 months. -
Pavement Marking
DE MUTCD Page 3A-1 CHAPTER 3A. GENERAL Section 3A.01 Functions and Limitations Support: 01 Markings on highways and on private roads open to public travel have important functions in providing guidance and information for the road user. Major marking types include pavement and curb markings, delineators, colored pavements, channelizing devices, and islands. In some cases, markings are used to supplement other traffic control devices such as signs, signals, and other markings. In other instances, markings are used alone to effectively convey regulations, guidance, or warnings in ways not obtainable by the use of other devices. 02 Markings have limitations. Visibility of the markings can be limited by snow, debris, and water on or adjacent to the markings. Marking durability is affected by material characteristics, traffic volumes, weather, and location. However, under most highway conditions, markings provide important information while allowing minimal diversion of attention from the roadway. Section 3A.02 Standardization of Application Standard: 01 Each standard marking shall be used only to convey the meaning prescribed for that marking in this Manual. When used for applications not described in this Manual, markings shall conform in all respects to the principles and standards set forth in this Manual. Guidance: 02 Before any new highway, private road open to public travel (see definition in Section 1A.13), paved detour, or temporary route is opened to public travel, all necessary markings should be in place. Standard: 03 Markings that must be visible at night shall be retroreflective unless ambient illumination assures that the markings are adequately visible. All markings on Interstate highways shall be retroreflective. -
May 21, 2019 SPECIFICATIONS Pavement Restriping Macon-Bibb
DATE: May 21, 2019 SPECIFICATIONS Pavement Restriping Macon-Bibb County NUMBER TITLE PAGES Division 1 - General Requirements 01005 Statement of Work 01005-1 thru 01005-2 Technical Specifications 652 Painting Traffic Stripe 1-4 653 Thermoplastic Traffic Stripe 1-9 654 Raised Pavement Markers 1-3 656 Marking Removal 1-2 868 Bituminous Adhesive for Raised Pavement Markers 1-4 870 Paint 1-15 886 Epoxy Resin Additives 1-3 919 Raised Pavement Markers 1-3 <<<<< END OF INDEX >>>>> 01005 - STATEMENT OF WORK PART 1 - GENERAL 1.01 STATEMENT OF WORK: This is a general overview of the project. Follow details shown by the specifications and drawings, interpreted in accordance with contract clauses. A. Accomplish Work at locations shown in Attachment A. This describes the road segments and provides some detail on number of lanes and other features that will alert the contractor to features which will require work. The contractor must investigate the road segments on his own and determine the quantity of striping required for each road segment. B. Omitted C. Provide all labor, material, plant, equipment, supplies, and coordination required to restripe various roads in Macon-Bibb County. The contractor shall also repaint existing crosswalks, turn arrows and words, stop bars, railroad markings and other miscellaneous features. The contractor shall use thermoplastic or a combination of paint and thermoplastic as described in the technical specifications. The contractor shall also install raised pavement markings on those segments indicated in Attachment A. D. General Congestion: 1. Work area is restricted to the area shown. Congestion will vary from road to road. -
12 Raised Markers Raised Pavement Markers
DISCLAIMER: The use of this standard is governed by the "Texas Engineering Practice Act". No warranty of any kind is made by TxDOT for any purpose whatsoever. TxDOT assumes no responsibility for the conver- DATE: 9/25/2018 8:02:41 PM sion of this standard to other formats or for incorrect results or damages resulting from its use. FILE: pw:\\txdot.projectwiseonline.com:TxDOT3\Documents\10 - TYL\Design Projects\069702039\4 - Design\Plan Set\8. Traffic\Standards\PM(2)-12 1"-4" 4" EDGELINEORCENTERLINE FOR FOURLANETWO-WAYHIGHWAYS 4" 4" CENTERLINE &LANELINES DETAIL "A" 12"+ 1" Type II-A-A Type II-A-A 3‚" +ƒ" 2 to3" CENTERLINE FORALLTWOLANEROADWAYS 80' Type II-A-A 10' OR OPTIONAL 6"EDGE LINEORCENTERLINE 6" 18"+ 1" DETAIL "B" 2 to3" Type I-C 40' 5•"+ •" NOTE: with aposted speedlimit of45MPH orless. Profile markings shallnotbeplacedonroadways 80' REFLECTORIZED PROFILE A quickfieldcheckforthethickness ofbase USING REFLECTIVEPROFILEPAVEMENTMARKINGS SEE DETAIL"A" equal toastackof5quarters maximum line andprofilemarkingisapproximately 1"-4" 4" 4" 1"-4" 4" be placedon80-footcenters. face towardnormaltraffic,shall Raised pavementmarkerTypeI-C,clear PATTERN DETAIL CENTER OREDGELINE 40' height of7quarters. 3-4" Type II-A-A Type II-A-A 4" 4" REFLECTIVE RAISEDPAVEMENTMARKERS FOR VEHICLEPOSITIONINGGUIDANCE 30' DETAIL "C" SEE DETAIL"C" SEE DETAIL"B" 40' 300 to500mil in height 1"-2" 1"-2" 4" 4" LANELINE CENTERLINE ANDLANELINESFORTWO-WAYLEFTTURN 2 to3" LANE LINESFORONE-WAYROADWAY(NON-FREEWAYFACILITIES) Continuous two-wayleftturnlane BROKEN LANELINE 3‚"+ ƒ" 12"+ 1" OR toward normaltrafficandredfacewrong-waytraffic. Raised pavementmarkersTypeII-C-Rshallhaveclearface Type I-CorII-C-R Type I-CorII-C-R Centerline OPTIONAL 6"LANE LINE 6" Type I-C 40' 2 to3" 5•"+ •" 40' Symmetrical aroundcenterline GENERAL NOTES 2. -
Markings Technical Committee Recommendations Approved by NCUTCD Council June 21, 2008 Yellow Highlight Indicates Recommended Changes to the NPA
ATTACHMENT 4b PART 3. MARKINGS CHAPTER 3B. PAVEMENT AND CURB MARKINGS Markings Technical Committee Recommendations Approved by NCUTCD Council June 21, 2008 Yellow highlight indicates recommended changes to the NPA. Section 3B.01 Yellow Centerline Center Line Pavement Markings and 3B.01 Warrants Approved by NC with Standard: revisions to Centerline Center line pavement markings, when used, shall be the pavement NPA. markings used to delineate the separation of traffic lanes that have opposite Approved directions of travel on a roadway and shall be yellow. revision Option: highlighted in Centerline Center line pavement markings may be placed at a location that is not yellow. the geometric center of the roadway. On roadways without continuous centerline center line pavement markings, short sections may be marked with centerline center line pavement markings to control the position of traffic at specific locations, such as around curves, over hills, on approaches to highway-railroad grade crossings, at highway-railroad grade crossings, and at bridges. Standard: The centerline center line markings on two-lane, two-way roadways shall be one of the following as shown in Figure 3B-1: A. Two-direction passing zone markings consisting of a normal broken yellow line where crossing the centerline center line markings for passing with care is permitted for traffic traveling in either direction; Editorial B. One-direction no-passing zone markings consisting of a double yellow line of which one is a normal broken yellow line and the other is a normal solid yellow line where crossing the centerline center line markings for passing with care is permitted for the traffic traveling adjacent to the broken line, but is prohibited for traffic traveling adjacent to the solid line; and or edited to increase accuracy C. -
RAISED PAVEMENT MARKERS Overview
HPS-TCP C1 ROLL APPLICATION GUIDE RAISED PAVEMENT MARKERS Overview This procedure outlines the recommended steps for the installation of the Stimsonite Model C80 & 980 Raised Pavement Markers with EF Bituminous Marker Adhesive. Storage: Keep materials in dry, protected areas. For maximum results, keep out of direct sunlight. PPE: The following PPE equipment is recommended during the different stages of application. Operators must fully understand the SDS’ (available from www.ennisflintapac.com) prior to works beginning. Safety Precautions: EF Bituminous Marker Adhesive in its packaged state is not a hazardous material. However, at operating temperature, it is potentially a hazardous product. Applicators and crew must review and understand SDS’ for all products being used prior to application. EQUIPMENT Surface prep & layout Installation • Stiff broom • Appropriate PPE • Blower • Compliant Glue Heater • Measuring tape • EF Spot Marker General Requirements: EF Bituminous Marker Adhesive can be applied on stable, well compacted asphalt or non-bituminous concrete surfaces, such as Portland cement concrete. New substrates should be allowed to age harden or cure for minimum 28 days before installation. The pavement surface must be clean, dry and have had no rainfall for 24hrs prior to installation. Use a wire brush, if necessary, to loosen and remove dirt. Brush or blow clean the location where the marker is to be placed. Pavement surface must be completely free of dirt, debris, moisture, curing compounds and other contaminants that can affect adhesion. Chemical contaminants such as vehicle fluids must be completely removed well in advance using a degreasing solution and power washer, ensuring all residues are removed. -
CHAPTER 6 CONSTRUCTION English Revised
TDOT ROADWAY DESIGN GUIDELINES CHAPTER 6 CONSTRUCTION English Revised: CHAPTER 6 CONSTRUCTION TDOT ROADWAY DESIGN GUIDELINES CHAPTER 6 CONSTRUCTION English Revised: CHAPTER 6 - CONSTRUCTION Table of Contents INTRODUCTION ....................................................................................................................... 1 CHAPTER 6 – CONSTRUCTION .............................................................................................. 3 SECTION 1 – PREPARING CONSTRUCTION PLANS ............................................................. 3 6-100.00 GENERAL NOTES ON PLANS ........................................................................... 3 6-101.00 SPECIAL NOTES ON PLANS ............................................................................. 3 6-102.00 REVIEW OF PAVEMENT DESIGN ..................................................................... 4 6-103.00 CHECKING DRAINAGE PLANS PRIOR TO CONSTRUCTION .......................... 4 SECTION 2 – PAVEMENT MARKINGS ..................................................................................... 5 6-200.00 PAVEMENT MARKING GUIDELINES ................................................................ 5 6-201.00 TEMPORARY PAVEMENT MARKINGS ............................................................. 5 6-201.01 TEMPORARY PAVEMENT MARKING FOR USE ON PAVEMENT SURFACE OTHER THAN FINAL ........................................................... 6 6-202.00 PERMANENT PAVEMENT MARKINGS ............................................................. 9 6-203.00 RAISED -
Part 3 Markings
Including Errata No. 1 dated June 14, 2001 December 2000 Page TC3-1 PART 3. MARKINGS TABLE OF CONTENTS Page CHAPTER 3A. GENERAL . Dec. 2000 Section 3A.01 Functions and Limitations...................................................................3A-1 Section 3A.02 Standardization of Application............................................................3A-1 Section 3A.03 Materials..............................................................................................3A-2 Section 3A.04 Colors ..................................................................................................3A-2 Section 3A.05 Colors of Longitudinal Pavement Markings.......................................3A-3 Section 3A.06 Widths and Patterns of Longitudinal Pavement Markings .................3A-3 CHAPTER 3B. PAVEMENT AND CURB MARKINGS . Dec. 2000 Section 3B.01 Yellow Centerline and Left Edge Line Pavement Markings and Warrants...............................................................................................3B-1 Section 3B.02 No-Passing Zone Pavement Markings and Warrants..........................3B-6 Section 3B.03 Other Yellow Longitudinal Pavement Markings...............................3B-11 Section 3B.04 White Lane Line and Right Edge Line Pavement Markings and Warrants ......................................................................................3B-14 Section 3B.05 Other White Longitudinal Pavement Markings ................................3B-15 Section 3B.06 Edge Line Pavement Markings .........................................................3B-19