Effect of Silica Content on Mechanical and Microstructure Behaviour of Resistance Spot Welded Advanced Automotive TRIP Steels
Total Page:16
File Type:pdf, Size:1020Kb
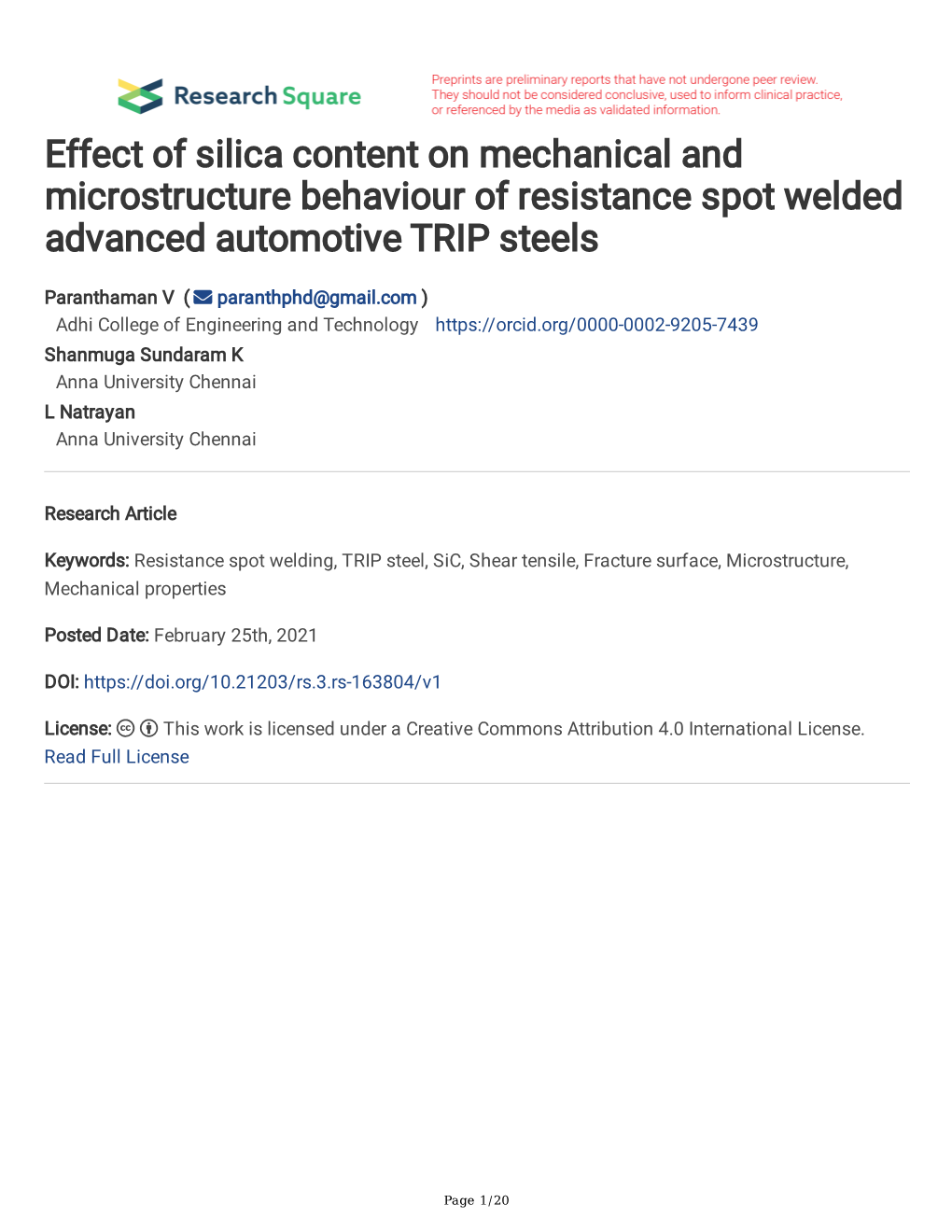
Load more
Recommended publications
-
Understanding of Deformation and Fracture Behavior in Next Generation High Strength-High Ductility Steels
University of Texas at El Paso DigitalCommons@UTEP Open Access Theses & Dissertations 2019-01-01 Understanding Of Deformation And Fracture Behavior In Next Generation High Strength-High Ductility Steels Venkata Sai Yashwanth Injeti University of Texas at El Paso, [email protected] Follow this and additional works at: https://digitalcommons.utep.edu/open_etd Part of the Materials Science and Engineering Commons, and the Mechanics of Materials Commons Recommended Citation Injeti, Venkata Sai Yashwanth, "Understanding Of Deformation And Fracture Behavior In Next Generation High Strength-High Ductility Steels" (2019). Open Access Theses & Dissertations. 93. https://digitalcommons.utep.edu/open_etd/93 This is brought to you for free and open access by DigitalCommons@UTEP. It has been accepted for inclusion in Open Access Theses & Dissertations by an authorized administrator of DigitalCommons@UTEP. For more information, please contact [email protected]. UNDERSTANDING OF DEFORMATION AND FRACTURE BEHAVIOR IN NEXT GENERATION HIGH STRENGTH-HIGH DUCTILITY STEELS VENKATA SAI YASHWANTH INJETI Doctoral Program in Materials Science and Engineering APPROVED: Devesh Misra, Ph.D., Chair Guikuan Yue, Ph.D. Srinivasa Rao Singamaneni, Ph.D. Charles Ambler, Ph.D. Dean of the Graduate School Copyright © by Venkata Sai Yashwanth Injeti 2019 UNDERSTANDING OF DEFORMANTION AND FRACTURE BEHAVIOR IN NEXT GENERATION HIGH STRENGTH-HIGH DUCTILITY STEELS by VENKATA SAI YASHWANTH INJETI DISSERTATION Presented to the Faculty of the Graduate School of The University of Texas at El Paso in Partial Fulfillment of the Requirements for the Degree of DOCTOR OF PHILOSOPHY Materials Science and Engineering THE UNIVERSITY OF TEXAS AT EL PASO May 2019 Acknowledgements At the outset, I would like to thank the Almighty for providing me ample patience, zeal and strength that enabled me to complete my Ph.D successfully. -
Trip Steels: Constitutive Modeling and Computational Issues
TRIP STEELS: CONSTITUTIVE MODELING AND COMPUTATIONAL ISSUES by IOANNIS CHRISTOU PAPATRIANTAFILLOU Submitted to the Department of Mechanical & Industrial Engineering of UNIVERSITY OF THESSALY In Partial Fulfillment of the Requirements for the Degree of DOCTOR OF PHILOSOPHY UNIVERSITY OF THESSALY JUNE 2005 Institutional Repository - Library & Information Centre - University of Thessaly 08/12/2017 08:18:44 EET - 137.108.70.7 Πανεπιστήμιο Θεσσαλίας ΒΙΒΛΙΟΘΗΚΗ & ΚΕΝΤΡΟ ΠΛΗΡΟΦΟΡΗΣΗΣ Ειδική Συλλογή «Γκρίζα Βιβλιογραφία» Αριθ. Εισ.: 4549/1 Ημερ. Εισ.: 20-07-2005 Δωρεά: Συγγραφέα Ταξιθετικός Κωδικός: _Δ________ 669.961 42 ΠΑΠ Institutional Repository - Library & Information Centre - University of Thessaly 08/12/2017 08:18:44 EET - 137.108.70.7 TRIP STEELS: CONSTITUTIVE MODELING AND COMPUTATIONAL ISSUES by IOANNIS CHRISTOU PAPATRIANTAFILLOU Submitted to the Department of Mechanical & Industrial Engineering of UNIVERSITY OF THESSALY In Partial Fulfillment of the Requirements for the Degree of DOCTOR OF PHILOSOPHY UNIVERSITY OF THESSALY JUNE 2005 Institutional Repository - Library & Information Centre - University of Thessaly 08/12/2017 08:18:44 EET - 137.108.70.7 ABSTRACT TRIP STEELS: CONSTITUTIVE MODELING AND COMPUTATIONAL ISSUES Abstract TRIP (TRansformation Induced Plasticity) of multi-phase steels is a new generation of low- alloy steels that exhibit an enhanced combination of strength and ductility. These steels make use of the TRIP phenomenon, i.e., the transformation of retained austenite to martensite with plastic deformation, which is responsible -
Materials Technology – Placement
MATERIAL TECHNOLOGY 01. An eutectoid steel consists of A. Wholly pearlite B. Pearlite and ferrite C. Wholly austenite D. Pearlite and cementite ANSWER: A 02. Iron-carbon alloys containing 1.7 to 4.3% carbon are known as A. Eutectic cast irons B. Hypo-eutectic cast irons C. Hyper-eutectic cast irons D. Eutectoid cast irons ANSWER: B 03. The hardness of steel increases if it contains A. Pearlite B. Ferrite C. Cementite D. Martensite ANSWER: C 04. Pearlite is a combination of A. Ferrite and cementite B. Ferrite and austenite C. Ferrite and iron graphite D. Pearlite and ferrite ANSWER: A 05. Austenite is a combination of A. Ferrite and cementite B. Cementite and gamma iron C. Ferrite and austenite D. Pearlite and ferrite ANSWER: B 06. Maximum percentage of carbon in ferrite is A. 0.025% B. 0.06% C. 0.1% D. 0.25% ANSWER: A 07. Maximum percentage of carbon in austenite is A. 0.025% B. 0.8% 1 C. 1.25% D. 1.7% ANSWER: D 08. Pure iron is the structure of A. Ferrite B. Pearlite C. Austenite D. Ferrite and pearlite ANSWER: A 09. Austenite phase in Iron-Carbon equilibrium diagram _______ A. Is face centered cubic structure B. Has magnetic phase C. Exists below 727o C D. Has body centered cubic structure ANSWER: A 10. What is the crystal structure of Alpha-ferrite? A. Body centered cubic structure B. Face centered cubic structure C. Orthorhombic crystal structure D. Tetragonal crystal structure ANSWER: A 11. In Iron-Carbon equilibrium diagram, at which temperature cementite changes fromferromagnetic to paramagnetic character? A. -
Me8491 - Engineering Metallurgy Unit- I / Alloys and Phase Diagrams Part-A
ME8491 - ENGINEERING METALLURGY UNIT- I / ALLOYS AND PHASE DIAGRAMS PART-A: 1. Write the constitution of austenite. Austenite is a primary solid solution based on γ iron having FCC structure. The 0 maximum solubility of carbon in FCC iron is about 2% at 1140 C. 2. Classify plain carbon steel. Low carbon steel – less than 0.25% carbon, Medium carbon steel – 0.25% to 0.60% carbon, High carbon steel – more than 0.60% carbon. 3. Define Alloy. It is a mixture of two or more metals or a metal and a non metal 4. What are alloying elements? The element which is present in the largest proportion is called the base metal and all other elements presents are called alloying base elements. 5. How will you explain peretectic reaction? In peretectic reaction, up on cooling, a solid and a liquid phase transform isothermally and reversibly to a solid phase having a different composition. Liquid + Solid1== solid2 6. What is steel? Steel is a composition unto 0.008% carbon is regarded as commercially pure iron those from 0.008-2% Carbon represent the steel. 7. State the condition for Gibb‟s phase rule. Pressure variable is kept constant at one atmosphere Gibb phase rule F=c-p+2; F=c-p+1(condensed Gibb phase rule). 8. Explain base metal. The element which present in the largest proportion is called the base metal 9. Differential between substitution and interstitial solid solutions. When the solute (Impurities) substitutes for parent solvent atoms in a crystal lattice, they are called substitution atoms, and the manure of the two elements is called a substitution solid solution. -
Microstructure–Property Relationships in Thermomechanically Processed Medium-Mn Steels with High Al Content
metals Article Microstructure–Property Relationships in Thermomechanically Processed Medium-Mn Steels with High Al Content Adam Grajcar 1,* , Andrzej Kilarski 2 and Aleksandra Kozlowska 1 1 Institute of Engineering Materials and Biomaterials, Silesian University of Technology, 18A Konarskiego Street, 44-100 Gliwice, Poland; [email protected] 2 Opel Manufacturing Poland Sp. z o.o., Purchasing G5, 1 Adama Opla Street, 44-121 Gliwice, Poland; [email protected] * Correspondence: [email protected]; Tel.: +48-32-2372-933 Received: 18 October 2018; Accepted: 7 November 2018; Published: 9 November 2018 Abstract: Detailed studies on microstructure–property relationships of thermomechanically processed medium-Mn steels with various manganese contents were carried out. Microscopic techniques of different resolution (LM, SEM, TEM) and X-Ray diffraction methods were applied. Static tensile tests were performed to characterize mechanical properties of the investigated steels and to determine the tendency of retained austenite to strain-induced martensitic transformation. Obtained results allowed to characterize the microstructural aspects of strain-induced martensitic transformation and its effect on the mechanical properties. It was found that the mechanical stability of retained austenite depends significantly on the manganese content. An increase in manganese content from 3.3% to 4.7% has a significant impact on the microstructure, stability of γ phase and mechanical properties of the investigated steels. The initial amount of retained austenite was higher for the 3Mn-1.5Al steel in comparison to 5Mn-1.5%Al steel—17% and 11%, respectively. The mechanical stability of retained austenite is significantly affected by the morphology of this phase. Keywords: medium Mn steel; bainitic steel; retained austenite; thermomechanical processing; strain-induced martensitic transformation 1. -
Effect of Retained Austenite and Non-Metallic Inclusions On
metals Article Effect of Retained Austenite and Non-Metallic Inclusions on the Mechanical Properties of Resistance Spot Welding Nuggets of Low-Alloy TRIP Steels Víctor H. Vargas Cortés 1, Gerardo Altamirano Guerrero 2,*, Ignacio Mejía Granados 1, Víctor H. Baltazar Hernández 3 and Cuauhtémoc Maldonado Zepeda 1 1 Instituto de Investigación en Metalurgia y Materiales, Universidad Michoacana de San Nicolás de Hidalgo, Edificio “U3”, Ciudad Universitaria, Morelia 58030, Michoacán, Mexico; [email protected] (V.H.V.C.); [email protected] (I.M.G.); [email protected] (C.M.Z.) 2 Instituto Tecnológico de Saltillo. Blvd, Venustiano Carranza #2400, Col. Tecnológico, Saltillo C.P. 25280, Mexico 3 Materials Science and Engineering Program, Autonomous University of Zacatecas, López Velarde 801, Zacatecas 9800, Zacatecas, Mexico; [email protected] * Correspondence: [email protected]; Tel.: +844-438-95-39; Fax: +844-438-95-16 Received: 2 July 2019; Accepted: 2 September 2019; Published: 30 September 2019 Abstract: The combination of high strength and formability of transformation induced plasticity (TRIP) steels is interesting for the automotive industry. However, the poor weldability limits its industrial application. This paper shows the results of six low-alloy TRIP steels with different chemical composition which were studied in order to correlate retained austenite (RA) and non-metallic inclusions (NMI) with their resistance spot welded zones to their joints’ final mechanical properties. RA volume fractions were quantified by X-ray microdiffraction (µSXRD) while the magnetic saturation technique was used to quantify NMI contents. Microstructural characterization and NMI of the base metals and spot welds were assessed using scanning electron microscopy (SEM). -
TRIP-Assisted Thin Sheet Steel with a Bainitic And/Or Martensitic Matrix
TECHNISCHE UNIVERSITÄT MÜNCHEN Fakultät für Maschinenwesen Lehrstuhl für Werkstoffkunde und Werkstoffmechanik mit Materialprüfamt für den Maschinenbau TRIP-assisted Thin Sheet Steel with a Bainitic and/or Martensitic Matrix Effects of Alloying Elements and Heat Treatment on Phase Transformations, Microstructures, and Mechanical Properties Katharina Maria Angelika Hausmann Vollständiger Abdruck der von der Fakultät für Maschinenwesen der Technischen Universität München zur Erlangung des akademischen Grades eines Doktor-Ingenieurs (Dr.-Ing.) genehmigten Dissertation. Vorsitzender: Univ.-Prof. Dr.-Ing. Markus Lienkamp Prüfer: 1. Univ.-Prof. Dr. mont. habil. Dr. h. c. Ewald Werner 2. Univ.-Prof. Dr.-Ing. Wolfgang Bleck, RWTH Aachen Die Dissertation wurde am 15.10.2014 bei der Technischen Universität München eingereicht und durch die Fakultät für Maschinenwesen am 13.03.2015 angenommen. Meiner Familie gewidmet... To my family... ii Danksagung Zuallererst danke ich Herrn Prof. Dr. Ewald Werner, Inhaber des Lehrstuhls für Werkstoffkunde und Werkstoffmechanik an der Technischen Universität München, für die Unterstützung und Förderung dieser Arbeit und die Übernahme des Hauptreferats. Herrn Prof. Dr. Wolfgang Bleck, Leiter des Instituts für Eisenhüttenkunde an der Rheinisch-Westfälischen Technischen Hochschule Aachen, danke ich für die Übernahme des Koreferats. Mein besonderer Dank gilt Herrn Dr. Andreas Pichler, Leiter der Forschung und Entwicklung Business Unit Band der voestalpine Stahl GmbH, für die Möglichkeit, an diesem Thema arbeiten und durch viele interessante Diskussionen und Anregungen von ihm lernen zu dürfen. Ich danke Herrn Dr. Daniel Krizan, Projektleiter der Werkstoffentwicklung Kaltband voestalpine Stahl GmbH, besonders für die Einführung in das Thema und die Erfahrungsweitergabe. Für die finanzielle Unterstützung und die Möglichkeit, in Forschung, Entwicklung und Produktion zu arbeiten, danke ich der voestalpine Stahl GmbH. -
International Conference on TRIP-Aided High Strength Ferrous Alloys
International Conference on TRIP-Aided High Strength Ferrous Alloys Editor: Prof. Bruno C. De Cooman GRIPS' Sparkling World of Steel Vol. 1: Proceedings Table of contents Table of contents De Cooman, Bruno C: 11 Preface Bleck, Wolfgang: 13 Using the TRIP effect - the dawn of a promising group of cold formable steels Low and high alloy TRIP steels. Phase transformations. Austenite stability. Strainharden- ing. Temperature sensitivity. Strength-ductility relationship. Energy absorption. Micro- structure optimization. Fundamental Materials Science of the TRIP Phenomenon Kruijver, Suzelotte; Zhao, Lie; Sietsma, Jilt; Offerman, Erik; van Dijk, Niels; Margulies, 25 Lawrence; Lauridsen, Erik; Grigull, Stephan; Poulsen, Henning; van derZwaag, Sybrand: In situ observations on the austenite stability in TRIP-steel during tensile testing TRIP steel. Synchrotron radiation. Austenite stability. Deformation. Diffraction. Carbon concentration. Austenite fraction. Crystal orientation. lung, Thierry; Drillet, Jos&e; Couturier, Audrey; Olier, Christopher: 31 Detailed study of the transformation mechanisms in ferrous TRIP aided steels TRIP. Bainite transformation. Cementite composition. Austenite stability. Size effect Furnemont, Quentin; Jacques, Pascal J.; Pardoen, Thomas; Lani, Frederic; Godet, 39 Stephane; Harlet, Philippe; Conlon, Kelly and Delannay, Francis. The macro- and micromechanics of TRIP-assisted multiphase steels, experiments and modelling TRIP-assisted multiphase steels. Multiphase microstructure. Nanohardness. Neutrons dif- fraction. Mechanical properties. Multi-scale approach. Modelling. Sugimoto, Koh-ichi; Kikuchi, Ryo; Hashimoto, Shun-ichi: 45 Development of high strength low alloy TRIP-aided steels with annealed martensite matrix Microstructure. Retained austenite. TRIP. Annealed martensite. Ductility. Formability. High strength steel Allain, Sebastien; Chateau, Jean-Philippe; Bouaziz, Olivier: 51 Constitutive model of the TWIP effect in a polycrystalline high manganese content austenitic steel Steel. -
Overcoming Strength-Ductility Trade-Off at Cryogenic Temperature of Low Carbon Low Alloy Steel Via Controlling Retained Austenite Stability
metals Article Overcoming Strength-Ductility Trade-Off at Cryogenic Temperature of Low Carbon Low Alloy Steel via Controlling Retained Austenite Stability Xuelin Wang 1, Zhenjia Xie 1,* , Chengjia Shang 1,* and Gang Han 2 1 Collaborative Innovation Center of Steel Technology, University of Science and Technology Beijing, Beijing 100083, China; [email protected] 2 Institute of Advanced Materials and Technology, University of Science and Technology Beijing, Beijing 100083, China; [email protected] * Correspondence: [email protected] (Z.X.); [email protected] (C.S.) Abstract: Stress–strain behavior of a low carbon low alloy multiphase steel with ferrite, tempered bainite, and retained austenite was studied at different cryogenic temperatures. Results indicated that both strength and ductility were enhanced with decreasing tensile testing temperature. The enhancement of both strength and ductility was attributed to the decreased mechanical stability of retained austenite with decreasing temperature, resulting in sufficient transformation induced plasticity (TRIP) effect for increasing work hardening rate. Keywords: multiphase steel; retained austenite stability; work hardening rate; ductility; low temper- ature property Citation: Wang, X.; Xie, Z.; Shang, C.; Han, G. Overcoming 1. Introduction Strength-Ductility Trade-Off at High strength low alloy (HSLA) steels have attracted great interest for wide fields of Cryogenic Temperature of Low applications, due to their excellent strength–toughness balance, economy, and weldabil- Carbon Low Alloy Steel via ity [1–3]. With applied fields of HSLA steels extending to low temperature environment, Controlling Retained Austenite low temperature toughness is of significant importance in consideration of safety. Generally, Stability. Metals 2021, 11, 157. yield strength of HSLA steels increases dramatically to be higher than fracture strength https://doi.org/10.3390/met110 with decreasing temperature, thus sudden brittle fracture takes place without ductile plastic 10157 deformation [4]. -
Relation Between Microstructure and Mechanical Properties of a Low-Alloyed TRIP Steel
Relation between Microstructure and Mechanical Properties of a Low-alloyed TRIP steel Von der Fakultat¨ fur¨ Georessourcen und Materialtechnik der Rheinisch-Westfalischen¨ Technischen Hochschule Aachen zur Erlangung des akademischen Grades eines Doktors der Ingenieurwissenschaften genehmigte Dissertation vorgelegt von M.Sc. Kemal DAVUT aus Kadikoy,¨ Turkei¨ Berichter: PD Dr.-Ing. Stefan Zaefferer Professor Dr.-Ing. Dierk Raabe Univ.-Prof. Dr.-Ing. Wolfgang Bleck Tag der mundlichen¨ Prufung:¨ 12. Februar 2013 Diese Dissertation ist auf den Internetseiten der Hochschulbibliothek online verfugbar.¨ WICHTIG: D 82 überprüfen !!! Berichte aus der Materialwissenschaft Kemal Davut Relation between Microstructure and Mechanical Properties of a Low-alloyed TRIP steel Shaker Verlag Aachen 2013 Bibliographic information published by the Deutsche Nationalbibliothek The Deutsche Nationalbibliothek lists this publication in the Deutsche Nationalbibliografie; detailed bibliographic data are available in the Internet at http://dnb.d-nb.de. Zugl.: D 82 (Diss. RWTH Aachen University, 2013) Copyright Shaker Verlag 2013 All rights reserved. No part of this publication may be reproduced, stored in a retrieval system, or transmitted, in any form or by any means, electronic, mechanical, photocopying, recording or otherwise, without the prior permission of the publishers. Printed in Germany. ISBN 978-3-8440-1782-3 ISSN 1618-5722 Shaker Verlag GmbH • P.O. BOX 101818 • D-52018 Aachen Phone: 0049/2407/9596-0 • Telefax: 0049/2407/9596-9 Internet: www.shaker.de • e-mail: [email protected] Preface This thesis is submitted in partial fulfillment of a Dr.-Ing degree from the RWTH Aachen University. The work presented in the thesis was carried out during the pe- riod April 2008 to September 2012 at the Max-Planck-Institut fuer Eisenforschung (MPIE), in the Department of Microstructure Physics and Alloy Design, under the supervisions of Associate Professor Dr.-Ing Stefan Zaefferer and Professor Dr.-Ing Dierk Raabe. -
The Causes of “Shear Fracture” of Dual-Phase Steels
The Causes of “Shear Fracture” of Dual-Phase Steels Dissertation Presented in Partial Fulfillment of the Requirements for the Degree of Doctor of Philosophy in the Graduate School of The Ohio State University By Ji-Hyun Sung, M.S. Graduate Program in Mechanical Engineering The Ohio State University 2010 Dissertation Committee: Robert H. Wagoner, Advisor June Key Lee Sudarsanam Suresh Babu Rebecca B. Dupaix ⓒ Copyright by Ji-Hyun Sung 2010 ABSTRACT Dual Phase (DP) steels are a class of advanced high strength steel (AHSS) in increasing use for sheet formed automotive parts. In spite of attractive combinations of high strength, high ductility, and low cost, the widespread adoption of DP steels has been limited because practical die tryouts exhibit forming failures far earlier than predicted by standard industrial methods. These failures, often referred to as “shear fractures,” occur in regions of high curvature and with little apparent necking, in contrast to “normal” or tensile fractures. Conventional wisdom attributes shear fractures to a postulated damage mechanism related to the special microstructure of DP steels. In order to reproduce, characterize, and analyze such fractures in a laboratory setting and to understand their origin of the inability to predict them, a novel draw-bend formability (DBF) test was devised based on displacement control. DP steels from several suppliers with tensile strengths ranging from 590 to 980 MPa were tested over a range of rates and bend ratios (R/t, inner bend radius / sheet thickness). The new DBF test reliably reproduced three kinds of fractures identified as Type I, II, and III, corresponding to tensile fracture, transitional fracture, and shear fracture, respectively. -
Design of an Effective Heat Treatment Involving Intercritical Hardening for High Strength/High Elongation of 0.2C–3Al
metals Article Design of an Effective Heat Treatment Involving Intercritical Hardening for High Strength/High Elongation of 0.2C–3Al–(6–8.5)Mn–Fe TRIP Steels: Microstructural Evolution and Deformation Behavior 1, 1, , 1 2 1 Yanjie Mou y, Zhichao Li * y, Xiaoteng Zhang , Devesh Misra , Lianfang He and Huiping Li 1,* 1 School of Materials Science and Engineering, Shandong University of Science and Technology, Qingdao 266590, China; [email protected] (Y.M.); [email protected] (X.Z.); [email protected] (L.H.) 2 Laboratory for Excellence in Advanced Steel Research, Department of Metallurgical, Materials and Biomedical Engineering, University of Texas at El Paso, El Paso, TX 79968, USA; [email protected] * Correspondence: [email protected] (Z.L.); [email protected] (H.L.); Tel.: +86-0532-8068-1145 (Z.L.); +86-0532-8605-7920 (H.L.) These two authors contributed equally to this work. y Received: 19 October 2019; Accepted: 26 November 2019; Published: 28 November 2019 Abstract: High strength/high elongation continues to be the primary challenge and focus for medium-Mn steels. It is elucidated herein via critical experimental analysis that the cumulative contribution of transformation-induced plasticity (TRIP) and microstructural constituents governs high strength/high elongation in 0.2C–3Al–(6–8.5)Mn–Fe steels. This was enabled by an effective heat treatment involving a combination of intercritical hardening and tempering to obtain high strength/high ductility. An excellent combination of high ultimate tensile strength of 935–1112 MPa and total elongation of 35–40% was obtained when the steels were subjected to intercritical hardening in the temperature range of 700–750 ◦C and low tempering at 200 ◦C.