On the Application of Design of Experiments to Accelerated Life Testing
Total Page:16
File Type:pdf, Size:1020Kb
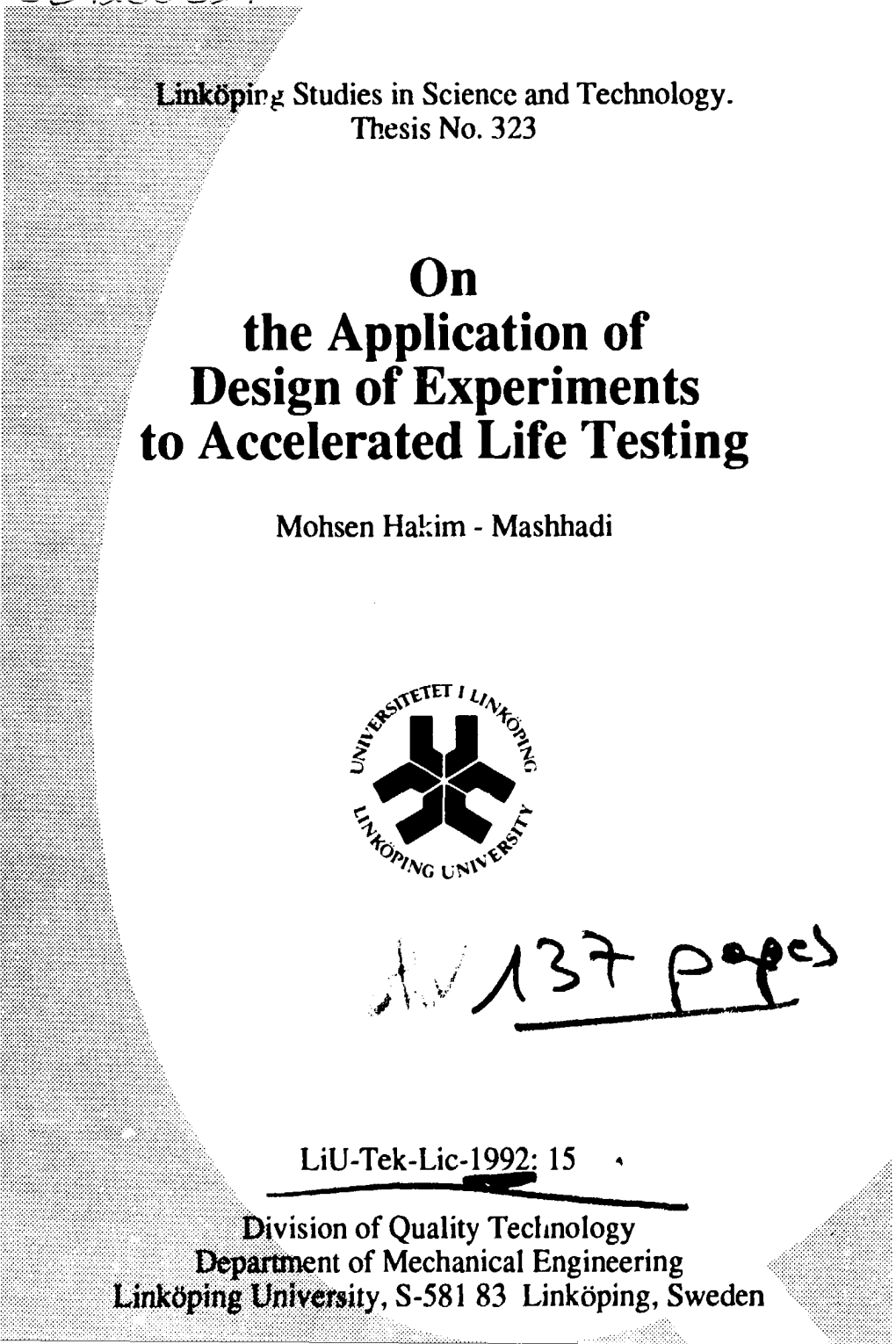
Load more
Recommended publications
-
What Is Test Reliability/Precision?
CHAPTER 6 What Is Test Reliability/Precision? LEARNING OBJECTIVES After completing your study of this chapter, you should be able to distributedo the following: •• Define reliability/precision, and describe three methods for estimating the reliability/ precision of a psychological test and its scores. or •• Describe how an observed test score is made up of the true score and random error, and describe the difference between random error and systematic error. •• Calculate and interpret a reliability coefficient, including adjusting a reliability coef- ficient obtained using the split-half method. •• Differentiate between the KR-20 and coefficientpost, alpha formulas, and understand how they are used to estimate internal consistency. •• Calculate the standard error of measurement, and use it to construct a confidence interval around an observed score. •• Identify four sources of test error and six factors related to these sources of error that are particularly importantcopy, to consider. •• Explain the premises of generalizability theory, and describe its contribution to esti- mating reliability.not “My statistics instructor let me take the midterm exam a second time because I was distracted by noise in the hallway.Do I scored 2 points higher the second time, but she says my true score probably didn’t change. What does that mean?” “I don’t understand that test. It included the same questions—only in different words—over and over.” “The county hired a woman firefighter even though she scored lower than someone else on the qualify- ing test. A man scored highest with a 78, and this woman only scored 77! Doesn’t that mean they hired a less qualified candidate?” “The psychology department surveyed my class on our career plans. -
Study on Lindley Distribution Accelerated Life Tests: Application and Numerical Simulation
S S symmetry Article Study on Lindley Distribution Accelerated Life Tests: Application and Numerical Simulation E. H. Hafez 1,*, Fathy H. Riad 2,3, Sh. A. M. Mubarak 4 and M. S. Mohamed 5,6 1 Department of Mathematics, Faculty of Science, Helwan University, P.O. Box 11731, Cairo 11795, Egypt 2 Department of Mathematics, College of Science, Jouf University, P.O. Box 2014, Sakaka 72393, Saudi Arabia; [email protected] 3 Department of Mathematics, Faculty of Science, Minia University, Minia 61111, Egypt 4 The High Institute of Engineering and Technology, Ministry of Higher Education, El-Minia 61111, Egypt; [email protected] 5 Department of Mathematics, College of Science, Taif University, P.O. Box 11099, Taif 21944, Saudi Arabia; [email protected] 6 Department of Mathematics, Faculty of Science, Al-Azher University, Nasr City 11884, Egypt * Correspondence: [email protected]; Tel.: +20-109-4506-495 Received: 18 November 2020; Accepted: 10 December 2020; Published: 15 December 2020 Abstract: Saving money and time are very important in any research project, so we must find a way to decrease the time of the experiment. This method is called the accelerated life tests (ALT) under censored samples, which is a very efficient method to reduce time, which leads to a decrease in the cost of the experiment. This research project includes inference on Lindley distribution in a simple step-stress ALT for the Type II progressive censored sample. The paper contains two major sections, which are a simulation study and a real-data application on the experimental design of an industry experiment on lamps. -
Reliability and Validity Analysis of Statistical Reasoning Test Survey Instrument Using the Rasch Measurement Model
INTERNATIONAL ELECTRONIC JOURNAL OF MATHEMATICS EDUCATION e-ISSN: 1306-3030. 2019, Vol. 14, No. 3, 535-546 OPEN ACCESS https://doi.org/10.29333/iejme/5755 Reliability and Validity Analysis of Statistical Reasoning Test Survey Instrument using the Rasch Measurement Model Siti Shahirah Saidi 1, Nyet Moi Siew 1* 1 Faculty of Psychology and Education, Universiti Malaysia Sabah, Sabah, MALAYSIA * CORRESPONDENCE: [email protected] ABSTRACT This study is an assessment of the reliability and validity analysis of Statistical Reasoning Test Survey (SRTS) instrument using the Rasch Measurement Model. The SRTS instrument was developed by the researchers to assess students’ statistical reasoning in descriptive statistics among Tenth Grade science- stream students in rural schools. SRTS was a combination of a subjective test and an open-ended format questionnaire which contained of 12 items. The respondents’ statistical reasoning was assessed based on these four constructs: Describing Data, Organizing Data, Representing Data and Analyzing and Interpreting Data. The sample comprised of 115 (76%) girls and 36 (24%) boys aged 15-16 years old from a rural district in Sabah, Malaysia. Overall, the SRTS instrument was found to have a high reliability with a Cronbach’s alpha value (KR-20) of 0.81. Results also showed that SRTS has an excellent item reliability and high item separation value of 0.99 and 9.57 respectively. SRTS also has a good person reliability and person separation value of 0.81 and 2.04 respectively. Meanwhile, the validity of the SRTS instrument was appropriately established through the item fit, person fit, variable map, and unidimensionality. In conclusion, this study indicates that the SRTS is a reliable and valid instrument for measuring the statistical reasoning of science-stream students from rural secondary schools. -
Accuracy Vs. Validity, Consistency Vs. Reliability, and Fairness Vs
Accuracy vs. Validity, Consistency vs. Reliability, and Fairness vs. Absence of Bias: A Call for Quality Accuracy vs. Validity, Consistency vs. Reliability, and Fairness vs. Absence of Bias: A Call for Quality Paper Presented at the Annual Meeting of the American Association of Colleges of Teacher Education (AACTE) New Orleans, LA. February 2008 W. Steve Lang, Ph.D. Professor, Educational Measurement and Research University of South Florida St. Petersburg Email: [email protected] Judy R. Wilkerson, Ph.D. Associate Professor, Research and Assessment Florida Gulf Coast University email: [email protected] Abstract The National Council for Accreditation of Teacher Education (NCATE, 2002) requires teacher education units to develop assessment systems and evaluate both the success of candidates and unit operations. Because of a stated, but misguided, fear of statistics, NCATE fails to use accepted terminology to assure the quality of institutional evaluative decisions with regard to the relevant standard (#2). Instead of “validity” and ”reliability,” NCATE substitutes “accuracy” and “consistency.” NCATE uses the accepted terms of “fairness” and “avoidance of bias” but confuses them with each other and with validity and reliability. It is not surprising, therefore, that this Standard is the most problematic standard in accreditation decisions. This paper seeks to clarify the terms, using scholarly work and measurement standards as a basis for differentiating and explaining the terms. The paper also provides examples to demonstrate how units can seek evidence of validity, reliability, and fairness with either statistical or non-statistical methodologies, disproving the NCATE assertion that statistical methods provide the only sources of evidence. The lack of adherence to professional assessment standards and the knowledge base of the educational profession in both the rubric and web-based resource materials for this standard are discussed. -
Eurasian Journal of Educational Research
Eurasian Journal of Educational Research 68 (2017) 1-17 Eurasian Journal of Educational Research www.ejer.com.tr Applying Bootstrap Resampling to Compute Confidence Intervals for Various Statistics with R C. Deha DOGAN1 A R T I C L E I N F O A B S T R A C T Article History: Background: Most of the studies in academic journals use p values to represent statistical Received: 13 October 2016 significance. However, this is not a good Received in revised form: 02 December 2016 indicator of practical significance. Although Accepted: 22 January 2017 confidence intervals provide information about the precision of point estimation, they are, DOI: http://dx.doi.org/10.14689/ejer.2017.68.1 unfortunately, rarely used. The infrequent use of Keywords confidence intervals might be due to estimation Confidence Interval difficulties for some statistics. The bootstrap P value method enables researchers to calculate confidence intervals for any statistics. Bootstrap Bootstrapped resampling resampling is an effective method of computing Methods of bootstrapping confidence intervals for nearly any estimate, but R software it is not very commonly used. This may be because this method is not well known or people may think that it is complex to calculate. On the other hand, researchers may not be familiar with R and be unable to write proper codes. Purpose: The purpose of this study is to present the steps in the bootstrap resampling method to calculate confidence intervals using R. It is aimed toward guiding graduate students and researchers who wish to implement this method. Computations of bootstrapped confidence interval for mean, median and Cronbach’s alpha coefficients were explained with the R syntax step-by-step. -
Proportional Hazard Model Applications in Reliability
Proportional Hazard Model Applications in Reliability A Dissertation Presented by Alexandre C. Mendes to The Graduate School of Engineering In partial fulfillment of the requirements for the degree of Doctor of Philosophy in Industrial Engineering Boston, Massachusetts April 2014 ABSTRACT This dissertation proposes two main methods as a modification of the semi-parametric Proportional Hazard Model (PHM) with innovative application for reliability testing. The first method developed uses a median of lifetime survival history for subjects with multiple occurrences to be modeled using the non-recurrent PHM method. The second method developed proposes censoring of influential observations, applying recurrent PHM theory. Both methods are validated using small electromechanical appliances with covariates identifying typical user performance as part of accelerated reliability testing. The Median PHM method is developed to allow the treatment of time-dependent covariates and competing failure types, which is fairly often necessary to properly model reliability studies. The advantages of this method are discussed and verified to provide the statistics or reliability engineer practitioners with the ability to evaluate multiple stresses, multiple covariates in accelerated reliability testing without the need to fit a physical model for the failure type and define a parametric distribution to model the acceleration parameter of interest. The analysis is presented in terms of hazard ratios that have immediate application for categorical covariates test levels and is easily extended for continuous covariates. Immediate plots for reliability and hazard curves are produced to enhance the analysis of the reliability model. Mendes develops the likelihood function with time-dependent covariates and presents a method to lay out the data and correct the input for the time-dependent covariate value derived from multiple measures for the II original subject with multiple failure occurrences. -
Confidence Intervals for Population Reliability Coefficients: Evaluation of Methods, Recommendations, and Software for Composite Measures
Psychological Methods © 2016 American Psychological Association 2016, Vol. 21, No. 1, 69–92 1082-989X/16/$12.00 http://dx.doi.org/10.1037/a0040086 Confidence Intervals for Population Reliability Coefficients: Evaluation of Methods, Recommendations, and Software for Composite Measures Ken Kelley Sunthud Pornprasertmanit University of Notre Dame Texas Tech University Acompositescoreisthesumofasetofcomponents.Forexample,atotaltestscorecanbedefinedasthesum of the individual items. The reliability of composite scores is of interest in a wide variety of contexts due to their widespread use and applicability to many disciplines. The psychometric literature has devoted consid- erable time to discussing how to best estimate the population reliability value. However, all point estimates of areliabilitycoefficientfailtoconveytheuncertaintyassociatedwiththeestimateasitestimatesthepopulation value. Correspondingly, a confidence interval is recommended to convey the uncertainty with which the population value of the reliability coefficient has been estimated. However, many confidence interval methods for bracketing the population reliability coefficient exist and it is not clear which method is most appropriate in general or in a variety of specific circumstances. We evaluate these confidence interval methods for 4 reliability coefficients (coefficient alpha, coefficient omega, hierarchical omega, and categorical omega) under avarietyofconditionswith3large-scaleMonteCarlosimulationstudies.Ourfindingsleadustogenerally recommend bootstrap confidence -
Imprecise Statistical Methods for Accelerated Life Testing
Imprecise Statistical Methods for Accelerated Life Testing Abdullah Ali H. Ahmadini A Thesis presented for the degree of Doctor of Philosophy Statistics and Probability Department of Mathematical Sciences University of Durham England April 2019 Dedicated to To Allah my God. To my father and mother. To my son Mohammed. Imprecise statistical methods for accelerated life testing Abdullah Ali H. Ahmadini Submitted for the degree of Doctor of Philosophy April 2019 Abstract Accelerated Life Testing (ALT) is frequently used to obtain information on the lifespan of devices. Testing items under normal conditions can require a great deal of time and expense. To determine the reliability of devices in a shorter period of time, and with lower costs, ALT can often be used. In ALT, a unit is tested under levels of physical stress (e.g. temperature, voltage, or pressure) greater than the unit will experience under normal operating conditions. Using this method, units tend to fail more quickly, requiring statistical inference about the lifetime of the units under normal conditions via extrapolation based on an ALT model. This thesis presents a novel method for statistical inference based on ALT data. The method quantifies uncertainty using imprecise probabilities, in particular it uses Nonparametric Predictive Inference (NPI) at the normal stress level, combin- ing data from tests at that level with data from higher stress levels which have been transformed to the normal stress level. This has been achieved by assuming an ALT model, with the relation between different stress levels modelled by a sim- ple parametric link function. We derive an interval for the parameter of this link function, based on the application of classical hypothesis tests and the idea that, if data from a higher stress level are transformed to the normal stress level, then these transformed data and the original data from the normal stress level should not be distinguishable. -
Optimal Step-Stress Plans for Accelerated Life Testing Considering
OPTIMAL STEP-STRESS PLANS FOR ACCELERATED LIFE TESTING CONSIDERING RELIABILITY/LIFE PREDICTION A Dissertation Presented by Chenhua Li to The Department of Mechanical and Industrial Engineering in partial fulfillment of the requirement for the degree of Doctor of Philosophy in Industrial Engineering Northeaster University Boston, Massachusetts April 2009 Abstract Products or materials are often tested at higher levels of stress than operational conditions to quickly obtain information on the life distribution or product performance under normal use. Such testing could save much time and money. In step-stress accelerated life test (SSALT), the stress for survival units is generally changed to a higher stress level at a pre-determined time. Determination of the stress change times is one of the most important design problems in SSALT. In this dissertation research, we focus on the SSALT design problem for Weibull failure data because of its broad application in industry. The optimal simple SSALT, which involves only two stress levels, is first derived. Log-linear life stress relationship is assumed. Two different types of optimization criteria are presented, considering life estimate and reliability estimate. Optimal SSALT plan is proposed by minimizing the Asymptotic Variance (AV) of the desired life/reliability estimate. In many applications and for various reasons, it is desirable to use more than one accelerating stress variable. Integration of Weibull failure data with multiple stress variables results in more complexity in the Fisher information matrix, and a more complicated problem to solve. Two stress variables are considered first, leading to the bivariate SSALT model. Bivariate SSALT model is then extended to a more generalized model: multi-variate SSALT, which includes k steps and m stress variables. -
Reliability and Generalization Studies Reliability
RELIABILITY AND GENERALIZATION STUDIES RELIABILITY: ARGUMENTS FOR MULTIPLE PERSPECTIVES AND POTENTIAL PROBLEMS WITH GENERALIZATION ACROSS STUDIES DIMITER M. DIMITROV Kent State University The present article addresses reliability issues in light of recent studies and debates focused on psychometrics versus datametrics terminology and reliability generalization (RG) introduced by Vacha-Haase. The purpose here was not to moderate arguments pre- sented in these debates but to discuss multiple perspectives on score reliability and how they may affect research practice, editorial policies, and RG across studies. Issues of classical error variance and reliability are discussed across models of classical test the- ory, generalizability theory, and item response theory. Potential problems with RG across studies are discussed in relation to different types of reliability, different test forms, different number of items, misspecifications, and confounding independent vari- ables in a single RG analysis. The editorial policies of Educational and Psychological Measurement (EPM) have become a focal point of recent studies and debates related to im- portant issues of reliability, effect size, and confidence intervals in reporting research. The purpose of this article was not to reiterate or moderate datametrics-psychometrics arguments presented in these debates (e.g., Thompson, 1994; Sawilowski, 2000; Thompson & Vacha-Haase, 2000) but to discuss issues concerning the assessment of score reliability and how they may affect (current or future) research practice, editorial policies, and reli- ability generalization (RG) across studies introduced by Vacha-Haase (1998). The discussion is organized in three parts. The first part presents mul- tiple perspectives on classical standard error of measurement (SEM) and reli- I would like to thank the two anonymous reviewers and an acting editor for their helpful com- ments and suggestions. -
Some Aspects of Classical Reliability Theory & Classical Test Theory
Some aspects of classical reliability theory & classical test theory Brian W. Junker Department of Statistics Carnegie Mellon University Pittsburgh PA 15213 [email protected] March 1, 2012 1 Reliability Reliability is the extent to which the test would produce consistent results if we gave it again under the same circumstances. This seems like a simple idea: why would we give a test if the results were not likely to replicate if we gave the test again? It is also an important idea statistically: when we use tests that are unreliable, statistical hypothesis testing is less powerful, correlations are smaller than they should be, etc. It turns out that a basic discussion of reliability can be based on a very simple mathemati- cal/statistical model, and for that reason this section is more mathematical than most of the rest of this essay. I hope that the main points of this section are clear even if you “read around” the places that are more mathematical. However, in reading the basic discussion in the next several subsections, please keep in mind: The model being discussed, the classical test theory model, is so simple as to hardly ever • be plausible, and yet, hardly ever falsifiable. Therefore, although it is useful for developing important insights about the role and consequences of reliability, and also for developing quantitative indices of reliability, its conclusions must be treated with a grain of salt. It is a fine first approximation in many settings, but there is almost always a more refined model that will produce a clearer picture of the functioning of the test. -
Reliability, Repeatability, and Reproducibility of Pulmonary Transit Time Assessment by Contrast Enhanced Echocardiography Ingeborg H
Herold et al. Cardiovascular Ultrasound (2016) 14:1 DOI 10.1186/s12947-015-0044-1 RESEARCH Open Access Reliability, repeatability, and reproducibility of pulmonary transit time assessment by contrast enhanced echocardiography Ingeborg H. F. Herold1*, Salvatore Saporito2, R. Arthur Bouwman1, Patrick Houthuizen3, Hans C. van Assen2, Massimo Mischi2 and Hendrikus H. M. Korsten1,2 Abstract Background: The aim of this study is to investigate the inter and intra-rater reliability, repeatability, and reproducibility of pulmonary transit time (PTT) measurement in patients using contrast enhanced ultrasound (CEUS), as an indirect measure of preload and left ventricular function. Methods: Mean transit times (MTT) were measured by drawing a region of interest (ROI) in right and left cardiac ventricle in the CEUS loops. Acoustic intensity dilution curves were obtained from the ROIs. MTTs were calculated by applying model-based fitting on the dilution curves. PTT was calculated as the difference of the MTTs. Eight raters with different levels of experience measured the PTT (time moment 1) and repeated the measurement within a week (time moment 2). Reliability and agreement were assessed using intra-class correlations (ICC) and Bland-Altman analysis. Repeatability was tested by estimating the variance of means (ANOVA) of three injections in each patient at different doses. Reproducibility was tested by the ICC of the two time moments. Results: Fifteen patients with heart failure were included. The mean PTT was 11.8 ± 3.1 s at time moment 1 and 11.7 ± 2.9 s at time moment 2. The inter-rater reliability for PTT was excellent (ICC = 0.94). The intra-rater reliability per rater was between 0.81–0.99.