Initial Study Polystyrene Foam Disposable Food Service Ware
Total Page:16
File Type:pdf, Size:1020Kb
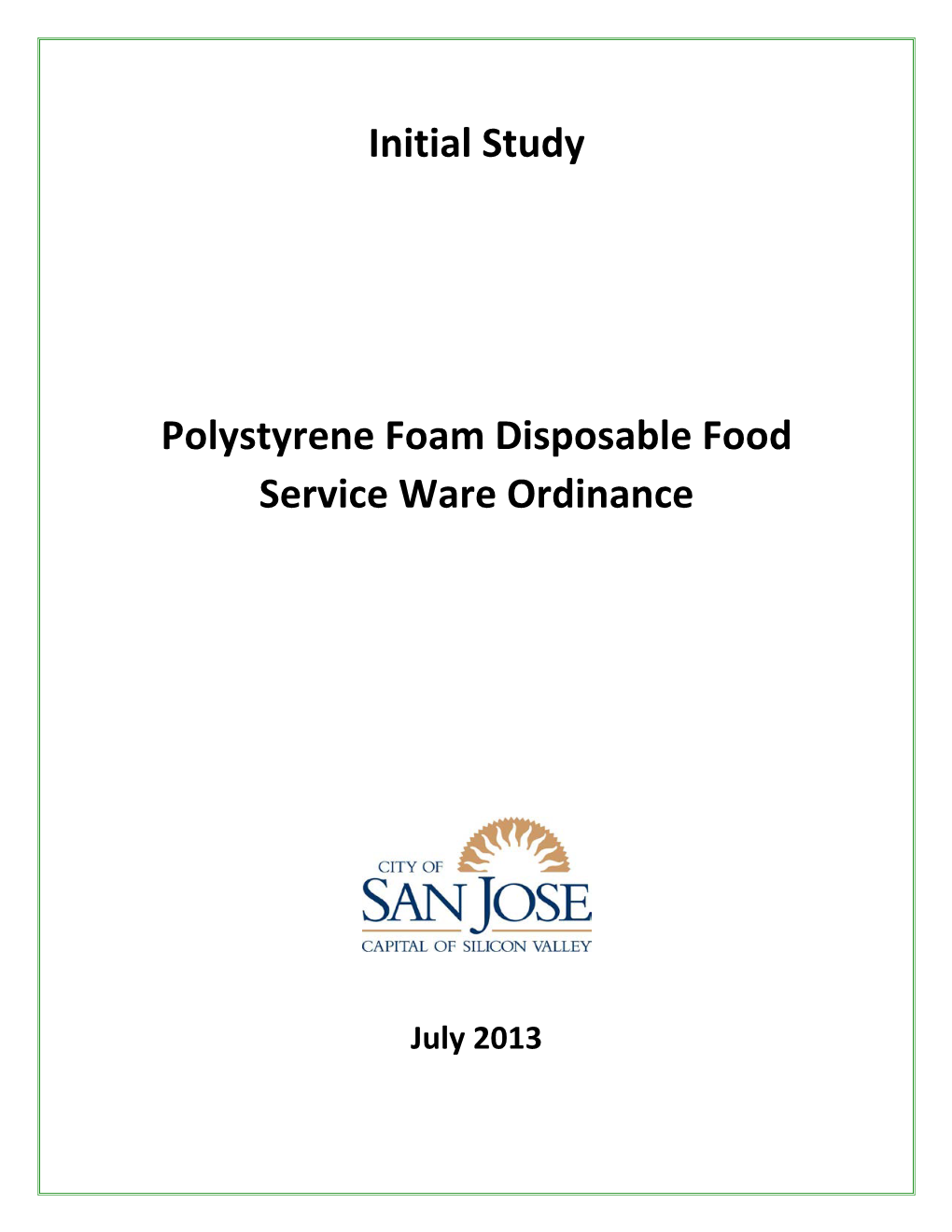
Load more
Recommended publications
-
Seaweed Polysaccharide in Food Contact Materials (Active Packaging, Intelligent Packaging, Edible Films, and Coatings)
foods Review Seaweed Polysaccharide in Food Contact Materials (Active Packaging, Intelligent Packaging, Edible Films, and Coatings) Kalpani Y. Perera 1,2,† , Shubham Sharma 1,2,†, Dileswar Pradhan 1,2,†, Amit K. Jaiswal 1,2,* and Swarna Jaiswal 1,2 1 School of Food Science and Environmental Health, College of Sciences and Health, Technological University Dublin—City Campus, Central Quad, Grangegorman, Dublin D07 ADY7, Ireland; [email protected] (K.Y.P.); [email protected] (S.S.); [email protected] (D.P.); [email protected] (S.J.) 2 Environmental Sustainability and Health Institute (ESHI), Technological University Dublin—City Campus, Grangegorman, Dublin D07 H6K8, Ireland * Correspondence: [email protected] † These authors contributed equally. Abstract: Food contact materials (FCMs) are materials that come in contact with food products such as food packaging which play a significant role in the food quality and safety. Plastic, which is a major food packaging material, harms the eco-system, wildlife, and the environment. As a result, numerous researches have been in progress on alternative polymers, which has similar properties as plastic but is also environmentally friendly (biodegradable). In recent years, the utilization of seaweed polysaccharides has piqued interest due to its biodegradability, non-toxicity, antioxidant capabilities, and excellent film formation ability. However, it has a number of drawbacks such as low tensile strength, water solubility, and moderate antibacterial characteristics, among others. The Citation: Perera, K.Y.; Sharma, S.; addition of other biopolymers, nanoparticles, or natural active agents improves these features. In Pradhan, D.; Jaiswal, A.K.; Jaiswal, S. this review article, we have summarized the current state of seaweed polysaccharide research in Seaweed Polysaccharide in Food active packaging, intelligent packaging, edible films, and coatings. -
Food Packaging Technology
FOOD PACKAGING TECHNOLOGY Edited by RICHARD COLES Consultant in Food Packaging, London DEREK MCDOWELL Head of Supply and Packaging Division Loughry College, Northern Ireland and MARK J. KIRWAN Consultant in Packaging Technology London Blackwell Publishing © 2003 by Blackwell Publishing Ltd Trademark Notice: Product or corporate names may be trademarks or registered Editorial Offices: trademarks, and are used only for identification 9600 Garsington Road, Oxford OX4 2DQ and explanation, without intent to infringe. Tel: +44 (0) 1865 776868 108 Cowley Road, Oxford OX4 1JF, UK First published 2003 Tel: +44 (0) 1865 791100 Blackwell Munksgaard, 1 Rosenørns Allè, Library of Congress Cataloging in P.O. Box 227, DK-1502 Copenhagen V, Publication Data Denmark A catalog record for this title is available Tel: +45 77 33 33 33 from the Library of Congress Blackwell Publishing Asia Pty Ltd, 550 Swanston Street, Carlton South, British Library Cataloguing in Victoria 3053, Australia Publication Data Tel: +61 (0)3 9347 0300 A catalogue record for this title is available Blackwell Publishing, 10 rue Casimir from the British Library Delavigne, 75006 Paris, France ISBN 1–84127–221–3 Tel: +33 1 53 10 33 10 Originated as Sheffield Academic Press Published in the USA and Canada (only) by Set in 10.5/12pt Times CRC Press LLC by Integra Software Services Pvt Ltd, 2000 Corporate Blvd., N.W. Pondicherry, India Boca Raton, FL 33431, USA Printed and bound in Great Britain, Orders from the USA and Canada (only) to using acid-free paper by CRC Press LLC MPG Books Ltd, Bodmin, Cornwall USA and Canada only: For further information on ISBN 0–8493–9788–X Blackwell Publishing, visit our website: The right of the Author to be identified as the www.blackwellpublishing.com Author of this Work has been asserted in accordance with the Copyright, Designs and Patents Act 1988. -
Insulated-Systainer®
systainer® A brilliant idea with a wide range of advantages Safely packed, clearly organised and quickly transported. Stackable and linkable Systematic design down to the very last detail Quality: 100% ABS, sturdy and impact- resistant, dust and splashwater-proof The systainer® will convince you in no time in everyday use! T-Loc One-hand operation Opening when linked Lock Open Connect Classic Line Innovative labelling Additional front handle Compatibility Fields of application Hospital Laboratory Medical Technology Anaesthesia Dental Emergency Medicine Pharmaceutical Veterinary Medicine Possibilities of use Hospital Laboratory Medical Technology Anaesthesia Dental Emergency Medicine Pharmaceutical Veterinary Medicine Insulated-systainer® The Insulated-systainer® are especially suitable for the safe dispatch of diagnostic samples of the material class UN 3373, fully correspond the packing regulation P 650 and were tested and approved by the BAM in Berlin (Federal Institute for Materials Research and Testing). Our Neopor and EPP inlays are equipped with a groove on 1 4 both sides to optionally attach dividers. Thus cooling packs can be inserted without having to touch neither the sample nor the cooling pack. Advantages of the referring inlay: In contrast to common styrofoam inserts the Neopor inlay has far better insulation properties. In addition it offers more stability for only a small difference in price. 2 5 The EPP inlay is characterized by its extreme sturdiness. It can be easily cleaned in industrial dish washers. 36 7 1 Insulated-systainer® -
RECYCLED PLASTIC in FOOD CONTACT MATERIALS - Policy Report by Safe Food Advocacy Europe
Brussels, December 2020 RECYCLED PLASTIC IN FOOD CONTACT MATERIALS - Policy Report by Safe Food Advocacy Europe - Food contact materials (FCMs) are defined as all the materials and articles that are intended to be put into contact with food and beverages or will presumably be in contact with food or beverages1. They include food packaging, kitchen equipment, tableware, machinery used in processing food, and objects that are used to transport food. These items can be made from a variety of materials including plastics, rubber, paper, and metal. Numerous concerns have been raised regarding the health risks FCMs might pose for consumers during exposure, as well as the efficiency of EU legislation in ensuring the safety of these materials. Among them, SAFE focuses on the emerging high-risk issue of the increasing use of recycled plastics in FCMs, which could negatively affect human health through the migration of harmful chemical substances, integrated before and/or during recycling processes, from FCMs into food. Drawing attention to health risks associated with recycled plastics in FCMs and the shortcomings of relevant legislation, SAFE would like to urge the European Commission to use the upcoming FCMs Regulations revision to ensure European consumers’ health. The policy report is produced within SAFE’s working area of food packaging, financially supported by LIFE Programme, aiming to advocate for better food packaging that is able to reduce its environmental impacts and maintain consumers health at the core of the decision-making process. 1. RECYCLED PLASTICS IN FCMs: A CURRENT AND INCREASING HIGH-RISK ISSUE Recycled plastics can be defined as plastic packaging that has passed through a mechanical recycling process which includes cleaning, grinding, re-melting, and re-granulating steps. -
Implementing Sustainability
Implementing Sustainability Sustainable Design Lab MSc 1/2 - 2018/19 Prof. Muck Petzet Assistants Laura Magri and Irene Tassinari Università Sustainable design / della Progettazione sostenibile Svizzera italiana Università della Svizzera italiana Accademia di architettura di Mendrisio 1 Section Implementing sustainability at AAM/USI The sustainable design LAB 2019/2020 Muck Petzet This applied research was conceived and performed in the ‚pre corona‘ semester 2019/2020 with the students of the ‚sustainable design lab‘ at the AAM/USI. Today’s perspectives have shifted under the unprecedented pressure of a global pandemic: what we yesterday would not have thought A critical summary of to be possible - is now a reality: the nearly complete suspension of air travel, the re-erection of borders inside of Europe - or the prohibition of social gatherings and the freeze and standstill of the students research* our economies with massive consequences for the whole system. In our school: the switch to online lectures / online design studios and even an online diploma. Students and teachers working together from their homes all around the globe. The virus with his infections has made global movements very visible - but also global dependencies: some stocks have crashed - some have soared, unemployment has jumped (especially in the US) - goods are piling up in the harbors, whole harvests have to be ploughed under because the supply chains cannot be adapted fast enough. Oil consumption has gone down drastically - resulting in ‚negative‘ prices for crude - and a massive storage problem. Pollution has gone down in the affected areas during lockdowns to levels that have not been measured for decades. -
Food Contact Materials and Chemical
Updated May 2019 F O O D C O N T A C T M A T E R I A L S A N D C H E M I C A L C O N T A M I N A T I O N There are multiple health concerns related to chemicals in food contact materials in Europe. This briefing looks at the current legislative system in the European Union for these materials and defines what is missing in the existing system and what must be changed if public health is to be protected. It also outlines the policy opportunities that are on the horizon. Have you ever wondered whether chemicals in the plastic wrapper on your meat or cheese can leach into the food you are about to eat? Or whether it is safer to buy your yogurt in a plastic pot or in a glass jar with a plastic lid? There are thousands of chemicals in food contact materials which can potentially migrate into food or drink and some are hazardous. Consumers tend to assume that they are protected from harmful chemicals in food and drink packaging, let alone the materials used in food processing and for cooking. In fact, the current European Union (EU) legislation on food contact materials is not fully effective in protecting public health. HEALTH AND ENVIRONMENT ALLIANCE 0 1 T H E H E A L T H P R O B L E M Currently, hazardous chemicals are present in plastics and other materials that come into contact with food. -
Technical Guide on Paper and Board Materials and Articles for Food Contact – DRAFT
European Committee for Food Contact Materials and Articles (Partial Agreement) (CD-P-MCA) 1 TECHNICAL GUIDE ON PAPER AND BOARD MATERIALS AND ARTICLES FOR 2 FOOD CONTACT 3 Draft CD-P-MCA request for stakeholder consultation 5 December 2019 Start of stakeholder consultation 5 February 2020 Deadline for comments 16 March 2020 Please use this comment form to enter your comments. Comments should be sent to: [email protected]. European Directorate for the Quality of Medicines & HealthCare (EDQM), Council of Europe Department of Biological Standardisation, OMCL Network & HealthCare (DBO) Address: 7, Allée Kastner | Cs 30026 | F-67081 Strasbourg (FRANCE) Internet address: www.edqm.eu Technical guide on paper and board materials and articles for food contact – DRAFT 4 Table of Contents 5 1. Scope and Definitions ......................................................................................................................... 1 6 1.1 Scope ....................................................................................................................................... 1 7 1.2 Definitions ............................................................................................................................... 1 8 2. Requirements ....................................................................................................................................... 1 9 2.1 General requirements .............................................................................................................. 1 10 2.2 Specific requirements -
Food Contact Materials: Migration and Analysis. Challenges and Limitations on Identification and Quantification
molecules Editorial Food Contact Materials: Migration and Analysis. Challenges and Limitations on Identification and Quantification Emmanouil D. Tsochatzis 1,2 1 Department of Food Science, Aarhus University, Agro Food Park 48, 8200 Aarhus, Denmark; [email protected]; Tel.: +45-41893130 2 CiFOOD, Aarhus University Centre for Innovative Food Research, 8200 Aarhus, Denmark Food contact materials (FCM) are defined as the objects and materials intended to come into direct or indirect contact with foodstuff, while food contact articles are defined as objects, being equipment, containers, packaging and various utensils which are clearly intended to be used for the manufacture, preparation, conservation, flow, transport or handling of foodstuffs [1,2]. Plastic materials are widely used in food packaging applica- tions; however, there is an increasing concern because of the possible release of undesirable components into foodstuffs. During the production of these plastics, several compounds can occur, either intentionally added substances (IAS) like monomers and production chemicals (i.e., antioxidants) or the so-called non-intentionally added substances (NIAS), which are generated as a result of reaction and degradation processes or due to the presence of impurities in the raw materials used for the packaging production. This category of substances might include up to several thousands of compounds, from which the vast majority is unknown. Safety could be threatened by this potentially large number of unknown substances occurring in virgin, processed or recycled plastic FCM. Consequently, Citation: Tsochatzis, E.D. Food concerns have been raised among research communities worldwide regarding FCMs safety Contact Materials: Migration and and possible adverse health effects on human health, given their abundant presence. -
Food Contact Materials and Articles: Printing Inks
TemaNord 2012:521 TemaNord Ved Stranden 18 DK-1061 Copenhagen K www.norden.org Food contact materials and articles: Printing Inks Food contact materials and articles: Printing Inks Check lists for compliance in industry and trade and control by food inspection Check lists for compliance in industry and trade and control by food inspection In-house control and the documentation of it is the basis for the assu- rance of compliance with legislation, in the food area and in the area of food contact materials (FCM). Safe use of FCM is a complicated area, in general, and specifically the use of printing inks and the critical points in the printing process. One of the goals for this check list is to contribute to the development of more uniform control and requirements for in-house control. Printing inks used in FCM are regulated by these general requirements and some uses are addressed more specifically , and as there is no specific legislation in the area in EU yet. In-house documentation is based on the assumption, that each link in the supply chain ensures compliance. The check lists set a frame with minimum requirements to all relevant links in the supply chain from producers to food industry and trade. The check lists are guidance to industry and trade in order to ensure compliance with the requirements in the FCM. TemaNord 2012:521 ISBN 978-92-893-2348-2 TN2012521 omslag.indd 1 27-04-2012 08:21:54 Food contact materials and articles: Printing Inks Check lists for compliance in industry and trade and control by food inspection Gitte Alsing -
Food Contact Substances and Chemicals of Concern
Food contact substances and chemicals of concern: A comparison of inventories Birgit Geueke,* Charlotte C. Wagner,* Jane Muncke Food Packaging Forum, Zurich, Switzerland Correspondence details: Food Packaging Forum Foundation, Staffelstrasse 12, 8045 Zurich, Switzerland, Phone +41 44 515 5255, e-mail: [email protected] (corresponding author), [email protected]; [email protected] *Both authors contributed equally. Disclosure statement All authors are employees at the Food Packaging Forum Foundation, a charitable non-profit organization. It is funded largely by donations from the packaging industry, but works independently of donors’ special interests. The employer does not restrict the study authors’ freedom to design, conduct, interpret, and publish research results in any way. Abstract Food contact materials (FCMs) are intended to be in contact with food during production, handling or storage. They are one possible source of food contamination, because chemicals may migrate from the material into the food. More than 6000 FCM substances appear on regulatory or non-regulatory lists. Some of these substances have been linked to chronic diseases, whilst many others lack (sufficient) toxicological evaluation. The aim of this study was the identification of known FCM substances which were also considered to be chemicals of concern (COCs). The investigation was based on the following three FCM lists: (i) the 2013 Pew Charitable Trusts database of direct and indirect food additives legally used in the U.S. (short: Pew), (ii) the current EU-wide positive list for plastic FCMs (short: Union), and (iii) the 2011 non-plastics FCM substances database published by EFSA (short: ESCO). -
Food Service Disposable
DISTRIBUTION LIST Job Name USSIV00086389 2018 Facility Solutions Cat ◊ Pricing File Name USSIV00086389_P3_CARTON UNPRICED_F0550_C0551 P3 Proof Date January 5, 2018 3:05 PM PAGE CONTROL CARTON Page Info BLEED +0p9 TRIM 7.9375 × 10.375 550 0551 UNPRICED SUBCATEGORY_2 PAPER CUPS & LIDS CUPS & LIDS CUTLERY DINNERWARE NAPKINS & DISPENSERS PARTY SUPPLIES FOOD STORAGE & CONTAINERS FOOD WRAP PAPER & BAGS CLEANING & SANITIZING CUPS 18-FA-CU-RNU 18-FA-CU-RNU FOODSERVICE DISPOSABLES 550 CAN’T FIND WHAT YOU NEED? CALL & LET US HELP. ••• DISTRIBUTION LIST Job Name USSIV00086389 2018 Facility Solutions Cat ◊ Pricing File Name USSIV00086389_P3_CARTON UNPRICED_F0551_C0552 P3 Proof Date January 5, 2018 3:08 PM PAGE CONTROL CARTON Page Info BLEED +0p9 TRIM 7.9375 × 10.375 551 0552 UNPRICED SUBCATEGORY_2 BUYING GUIDE GLOVES FOR FOODSERVICE See pages 314-317, 608 for our selection of foodservice gloves. Use our Feature Key to find gloves that help you maintain safety and hygiene standards. 1 Thin 5 High Dexterity 2 Medium Thickness 6 Powdered for Easy On/Off 3 Thick 7 Embossed/Textured Grip 4 High Protection/Tear Strength 8 Fits Either Hand Latex Synthetic No. Features How to Order No. Features How to Order BWK 355SBX 2 5 6 8 See p. 316 BWK 315SBX 3 7 8 See p. 317 BWK 355MBX 2 5 6 8 See p. 316 BWK 315MBX 3 7 8 See p. 317 BWK 355LBX 2 5 6 8 See p. 316 BWK 315LBX 3 7 8 See p. 317 BWK 345MBX 2 5 8 See p. 316 BWK 315XLBX 3 7 8 See p. 317 BWK 345LBX 2 5 8 See p. -
Fragment Migration Into Food and Drink Simulants from Poly(Styrene) Packaging
foods Article An Insight into the Growing Concerns of Styrene Monomer and Poly(Styrene) Fragment Migration into Food and Drink Simulants from Poly(Styrene) Packaging Asmaa Ajaj 1, Shayma J’Bari 1, Anthonia Ononogbo 1, Federico Buonocore 1, Joseph C. Bear 1, Andrew G. Mayes 2 and Huda Morgan 1,* 1 School of Life Sciences, Pharmacy and Chemistry, Kingston upon Thames, London KT1 2EE, UK; [email protected] (A.A.); [email protected] (S.J.); [email protected] (A.O.); [email protected] (F.B.); [email protected] (J.C.B.) 2 School of Chemistry, University of East Anglia, Norwich Research Park, Norwich, Norfolk NR4 7TJ, UK; [email protected] * Correspondence: [email protected] Abstract: Poly(styrene) (PS) has been heavily utilised in disposable food packaging due to its insulating properties, optical translucency, and long-shelf life. Despite these desirable characteristics, (PS) poses toxicity concerns to human’s health through styrene monomer leaching into foodstuffs. Environmental and marine hazards are another growing concerns due to improper and/or absence of recycling strategies and facilities. This preliminary work aims to investigate the effect of temperature, Citation: Ajaj, A.; J’Bari, S.; food composition and contact times on the migration of the styrene monomer from poly(styrene) food Ononogbo, A.; Buonocore, F.; Bear, contact materials into food simulants. Poly(styrene) cups showed a relatively low level of styrene J.C.; Mayes, A.G.; Morgan, H. An migration with the highest being 0.110 µg/mL, whereas food containers showed a much higher level Insight into the Growing Concerns of of styrene leaching with up to 6 µg/mL.