Underwater Inspection of Bridge Substructures Using Imaging Technology
Total Page:16
File Type:pdf, Size:1020Kb
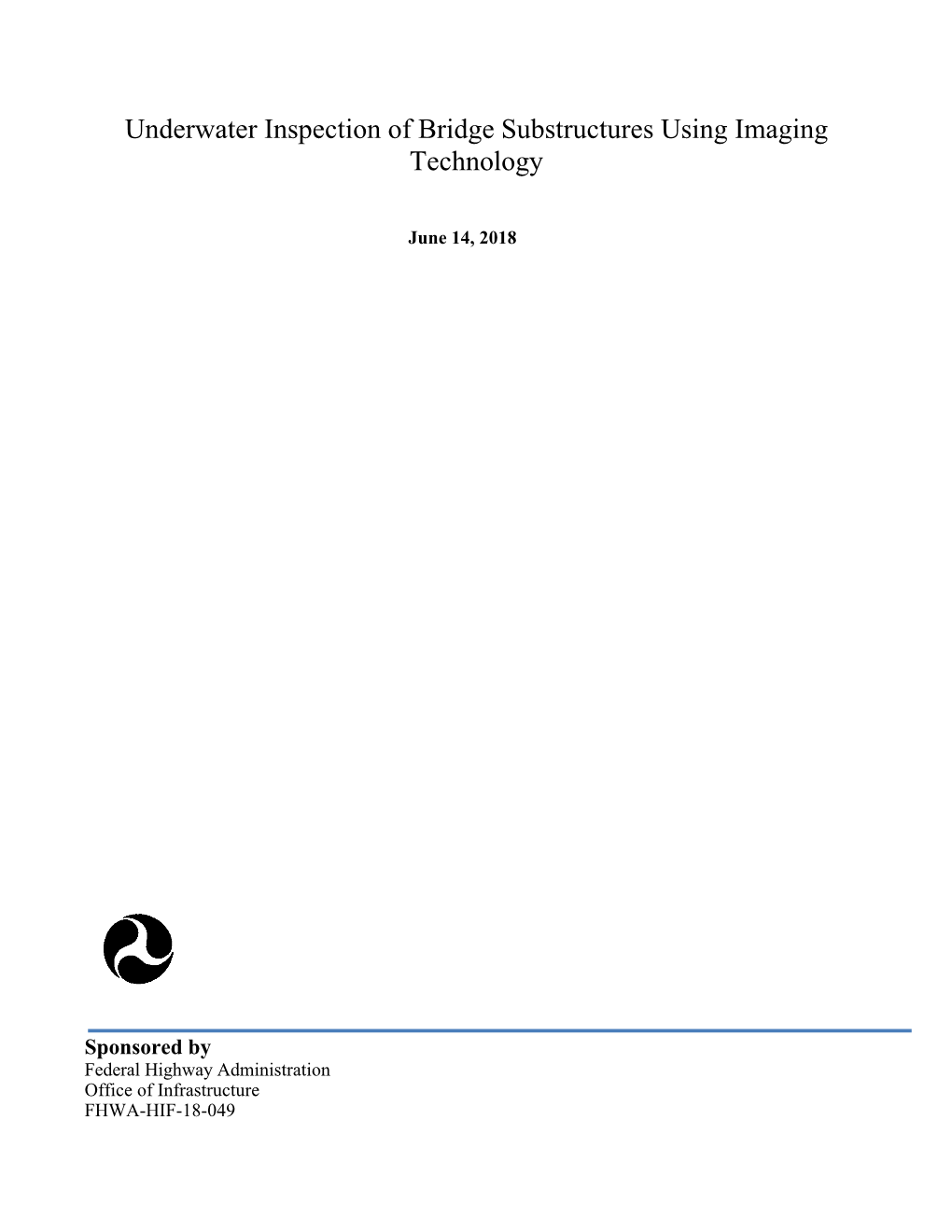
Load more
Recommended publications
-
2019-20 Media Guide
www.NAVYSPORTS.com NAVY SWIMMING & DIVING 2019-20 MEDIA GUIDE 2018 PATRIOT LEAGUE CHAMPIONS 2019-20 NAVY SWIMMING & DIVING Table of Contents Women’s Team Facts Men’s Team Facts Program Information 1 Coaching Staff Coaching Staff Coaching / Support Staff 2-7 Head Swimming Coach John Morrison Head Swimming Coach Bill Roberts 2019-20 Schedule / NCAA Meet Standards 8 Alma Mater North Carolina ‘93 Alma Mater Springfield ‘92 Year at Navy as Head Coach 16th Year at Navy as Head Coach 17th 2019-20 Women’s Team 9 Year at Navy 20th Year at Navy 20th Roster 9 Navy Record 138-36 (15 Seasons) Navy Record 169-56 (16 Seasons) Women’s Bios 10-19 Career Record 169-63 (18 Seasons) Career Record 208-93 (19 Seasons) Phone (410) 293-3081 Phone (410) 293-3012 E-Mail [email protected] E-Mail [email protected] 2019-20 Men Team 20 Head Diving Coach Rich MacDonald Head Diving Coach Rich MacDonald Roster 20 Alma Mater Rhode Island ‘97 Alma Mater Rhode Island ‘97 Men’s Bios 21-30 Year at Navy Seventh Year at Navy Seventh Phone (410) 293-2970 Phone (410) 293-2970 2018-19 Season in Review 31 E-Mail [email protected] E-Mail [email protected] Season Results / Event Victories 31 Assoc. Head Swimming Coach Rob Lias Jr. Assistant Swimming Coach Mark Liscinsky Championship Meet Results 32-37 Alma Mater Mount Union ‘00 Alma Mater American ‘04 Top Times 37 Year at Navy 14th Year at Navy Seventh Honors and Award Winners 38 Phone (410) 293-3013 Phone (410) 293-5834 E-Mail [email protected] E-Mail [email protected] History & Records 39 Women’s W-L Records / Captains / Coaches 39 -
Standard Operating Procedures for Scientific Diving
Standard Operating Procedures for Scientific Diving The University of Texas at Austin Marine Science Institute 750 Channel View Drive, Port Aransas Texas 78373 Amended January 9, 2020 1 This standard operating procedure is derived in large part from the American Academy of Underwater Sciences standard for scientific diving, published in March of 2019. FOREWORD “Since 1951 the scientific diving community has endeavored to promote safe, effective diving through self-imposed diver training and education programs. Over the years, manuals for diving safety have been circulated between organizations, revised and modified for local implementation, and have resulted in an enviable safety record. This document represents the minimal safety standards for scientific diving at the present day. As diving science progresses so must this standard, and it is the responsibility of every member of the Academy to see that it always reflects state of the art, safe diving practice.” American Academy of Underwater Sciences ACKNOWLEDGEMENTS The Academy thanks the numerous dedicated individual and organizational members for their contributions and editorial comments in the production of these standards. Revision History Approved by AAUS BOD December 2018 Available at www.aaus.org/About/Diving Standards 2 Table of Contents Volume 1 ..................................................................................................................................................... 6 Section 1.00 GENERAL POLICY ........................................................................................................................ -
Caverns Measureless to Man: Interdisciplinary Planetary Science & Technology Analog Research Underwater Laser Scanner Survey (Quintana Roo, Mexico)
Caverns Measureless to Man: Interdisciplinary Planetary Science & Technology Analog Research Underwater Laser Scanner Survey (Quintana Roo, Mexico) by Stephen Alexander Daire A Thesis Presented to the Faculty of the USC Graduate School University of Southern California In Partial Fulfillment of the Requirements for the Degree Master of Science (Geographic Information Science and Technology) May 2019 Copyright © 2019 by Stephen Daire “History is just a 25,000-year dash from the trees to the starship; and while it’s going on its wild and woolly but it’s only like that, and then you’re in the starship.” – Terence McKenna. Table of Contents List of Figures ................................................................................................................................ iv List of Tables ................................................................................................................................. xi Acknowledgements ....................................................................................................................... xii List of Abbreviations ................................................................................................................... xiii Abstract ........................................................................................................................................ xvi Chapter 1 Planetary Sciences, Cave Survey, & Human Evolution................................................. 1 1.1. Topic & Area of Interest: Exploration & Survey ....................................................................12 -
South Slough Salmon Rearing Habitat Enhancement Project
South Slough Salmon Rearing Habitat Enhancement Project South Slough NERR Coos Watershed Association Oregon Department of Fish and Wildlife Oregon Department of Transportation 2004 Funding: FishAmerica Foundation / U.S. Fish and Wildlife Service Coos Bay South Slough National Estuarine Research Reserve North Bend Coos Bay Charleston South Slough NERR South Slough Watershed Project Location Tree Source Area South Slough Reserve Boundary South Slough Watershed Boundary Project Location Tree Source Area Helicopter flight path Helicopter Refueling Area Tree Placement Area Project Goals: 1. To evaluate the effectiveness of placing large wood in estuarine channels for improved habitat for juvenile salmonids. 2. To contribute to the development estuarine wetland restoration and management recommendations for placement of large wood in tidal channels for watershed councils, natural resource agencies / scientific community and the general public. Project Goals: 1. To evaluate the effectiveness of placing large wood in estuarine channels for improved habitat for juvenile salmonids. 2. To develop recommendations for placing large wood in tidal channels for habitat restoration/enhancement purposes (mainly targeting watershed councils, natural resource agencies / scientific community). N A B D C South Slough NERR administrative boundary A1 A2 A3 A1 A4 6 Trees 29” Bottom 38” 36” 27” Top 35” 29” 36” 27” 25” 35” 38” Bottom 25” Top N 32” Bottom *26” Top A3 18” 5 Trees 32” *26” 23” 23” 18” 18” *Short A1 18” A2 A3 A4 N Tree Source Destination Study Locations 11 . Mouth of Tom’s and A1 43 Dalton Creeks 1 43 . In tidal channels A2 7 . Mainstem Winchester 9 Creek 8 2 5 A3 6 12 A4 10 Restoration Monitoring Questions: . -
6. Annular Space & Sealing
6. Annular Space & Sealing (this page left intentionally blank) 6. Annular Space & Sealing Chapter Table of Contents Chapter Table of Contents Chapter Description ......................................................................................................................................................................................... 6 Regulatory Requirements – Annular Space & Sealing of a New Well ..................................................................................................... 6 Relevant Sections – The Wells Regulation.............................................................................................................................................. 6 The Requirements – Plainly Stated .......................................................................................................................................................... 6 Well Record – Relevant Sections............................................................................................................................................................14 Best Management Practice – Report use of Centralizers .......................................................................................................... 15 Key Concepts ..................................................................................................................................................................................................16 The Annular Space ...................................................................................................................................................................................16 -
It's Not the Most Glamorous Job in the World, and It's Not the Highest Profile
Tidal Thames.qxd 9/24/07 2:22 PM Page 8 n the bottom Thames Estuary. As commercial diving a falling tide, but leave them the diver, a stand-by diver and a Kevin said: “She gives us a large of the He rarely knows what goes, the PLA team doesn’t vulnerable on rising tides. So tender or dive assistant. deck area to work on and her speed’s Thames, the day will hold or, once go deep - typically around everything we do has to be timed They can dive from any vessel; very important. In an emergency we Mick he’s under the water, what eight to 20 metres. But poor precisely, according to where in the but they prefer to use their own may only have a narrow tidal window Russell is will loom out of the visibility and shifting river we’re expected to work.” specially designed boat PLA Diver. It to work in, if we miss it, we could be blind. darkness - driftwood, currents in some of the The divers get their jobs from was built in 1992 by Searle Williams waiting up to 11 hours before the The water’s disturbed wartime busiest port waters in either the PLA’s Marine Services team, on a Blyth 33 hull. At 10 metres long conditions are right again - so it’s thick with silt and, just a explosives, the occasional Britain, makes the Thames a Vessel Traffic Services (VTS) officers, and with a displacement of seven vital we get on scene quickly.” few inches from where he’s corpse. -
Underwater Inspection and Repair of Bridge Substructures
[.Tl [•1•] NATIONAL COOPERATIVE HIGHWAY RESEARCH PROGRAM SYNTHESIS OF HIGHWAY PRACTICE UNDERWATER INSPECTION AND REPAIR OF BRIDGE SUBSTRUCTURES Supv ) ç J j p1 JUNO 81982 3 up2Leder I.T.D. DIV OF H!GHWAYS BRIDGE SECTION FUe_OUT MAIL TRANSPORTATION RESEARCH BOARD NATIONAL RESEARCH COUNCIL TRANSPORTATION RESEARCH BOARD EXECUTIVE COMMITTEE 1981 Officers Chairman THOMAS D. LARSON Secretary, Pennsylvania Department of Transportation Vice Chairman DARRELL V MANNING, Director, Idaho Transportation Department Secretary THOMAS B. DEEN, Executive Director, Transportation Research Board Members RAY A. BARNHART, Federal Highway Administrator, U.S. Department of Transportation (cx officio) ROBERT W. BLANCHETTE, Federal Railroad Administrator, U.S. Department of Transportation (cx officio) FRANCIS B. FRANCOIS, Executive Director, American Association of State Highway and Transportation Officials (cx officio) WILLIAM J. HARRIS, JR., Vice President—Research and lest Department, Association of American Railroad.. (ex officio) J. LYNN HELMS, Federal Aviation Administrator, U.S. Department of Transportation (cx officio) PETER G. KOLTNOW, President, Highway Users Federation for Safety and Mobility (cx officio. Past Chairman, 1979) ELLIOTT W. MONTROLL, Chairman, Co,n,nission on Sociotechnical Systems, National Research Council (cx officio) RAYMOND A. PECK, JR., National Highway Traffic Safety Administrator, U.S. Department of Transportation (cx officio) ARTHUR E. TEELE, JR., Urban Mass Transportation Administrator, U.S. Department of Transportation (cx officio) JOHN F. WING, Senior Vice President, Booz. Allen & Hamilton. Inc. (cx officio, MTRB liaison) CHARLEY V. WOOTAN. Director, Texas Transportation Institute, Texas A&M University (cx officio, Past Chairman 1980) GEORGE J. BEAN. Director of Aviation, Hilisborough County (Florida) Aviation Authority THOMAS W. BRADSHAW, JR., Secretary, North Carolina Department of Transportation RICHARD P. -
Diving Safety Manual Revision 3.2
Diving Safety Manual Revision 3.2 Original Document: June 22, 1983 Revision 1: January 1, 1991 Revision 2: May 15, 2002 Revision 3: September 1, 2010 Revision 3.1: September 15, 2014 Revision 3.2: February 8, 2018 WOODS HOLE OCEANOGRAPHIC INSTITUTION i WHOI Diving Safety Manual DIVING SAFETY MANUAL, REVISION 3.2 Revision 3.2 of the Woods Hole Oceanographic Institution Diving Safety Manual has been reviewed and is approved for implementation. It replaces and supersedes all previous versions and diving-related Institution Memoranda. Dr. George P. Lohmann Edward F. O’Brien Chair, Diving Control Board Diving Safety Officer MS#23 MS#28 [email protected] [email protected] Ronald Reif David Fisichella Institution Safety Officer Diving Control Board MS#48 MS#17 [email protected] [email protected] Dr. Laurence P. Madin John D. Sisson Diving Control Board Diving Control Board MS#39 MS#18 [email protected] [email protected] Christopher Land Dr. Steve Elgar Diving Control Board Diving Control Board MS# 33 MS #11 [email protected] [email protected] Martin McCafferty EMT-P, DMT, EMD-A Diving Control Board DAN Medical Information Specialist [email protected] ii WHOI Diving Safety Manual WOODS HOLE OCEANOGRAPHIC INSTITUTION DIVING SAFETY MANUAL REVISION 3.2, September 5, 2017 INTRODUCTION Scuba diving was first used at the Institution in the summer of 1952. At first, formal instruction and proper information was unavailable, but in early 1953 training was obtained at the Naval Submarine Escape Training Tank in New London, Connecticut and also with the Navy Underwater Demolition Team in St. -
OCEANS ´09 IEEE Bremen
11-14 May Bremen Germany Final Program OCEANS ´09 IEEE Bremen Balancing technology with future needs May 11th – 14th 2009 in Bremen, Germany Contents Welcome from the General Chair 2 Welcome 3 Useful Adresses & Phone Numbers 4 Conference Information 6 Social Events 9 Tourism Information 10 Plenary Session 12 Tutorials 15 Technical Program 24 Student Poster Program 54 Exhibitor Booth List 57 Exhibitor Profiles 63 Exhibit Floor Plan 94 Congress Center Bremen 96 OCEANS ´09 IEEE Bremen 1 Welcome from the General Chair WELCOME FROM THE GENERAL CHAIR In the Earth system the ocean plays an important role through its intensive interactions with the atmosphere, cryo- sphere, lithosphere, and biosphere. Energy and material are continually exchanged at the interfaces between water and air, ice, rocks, and sediments. In addition to the physical and chemical processes, biological processes play a significant role. Vast areas of the ocean remain unexplored. Investigation of the surface ocean is carried out by satellites. All other observations and measurements have to be carried out in-situ using research vessels and spe- cial instruments. Ocean observation requires the use of special technologies such as remotely operated vehicles (ROVs), autonomous underwater vehicles (AUVs), towed camera systems etc. Seismic methods provide the foundation for mapping the bottom topography and sedimentary structures. We cordially welcome you to the international OCEANS ’09 conference and exhibition, to the world’s leading conference and exhibition in ocean science, engineering, technology and management. OCEANS conferences have become one of the largest professional meetings and expositions devoted to ocean sciences, technology, policy, engineering and education. -
D5.3 Interaction Between Currents, Wave, Structure and Subsoil
Downloaded from orbit.dtu.dk on: Oct 05, 2021 D5.3 Interaction between currents, wave, structure and subsoil Christensen, Erik Damgaard; Sumer, B. Mutlu; Schouten, Jan-Joost; Kirca, Özgür; Petersen, Ole; Jensen, Bjarne; Carstensen, Stefan; Baykal, Cüneyt; Tralli, Aldo; Chen, Hao Total number of authors: 19 Publication date: 2015 Document Version Publisher's PDF, also known as Version of record Link back to DTU Orbit Citation (APA): Christensen, E. D., Sumer, B. M., Schouten, J-J., Kirca, Ö., Petersen, O., Jensen, B., Carstensen, S., Baykal, C., Tralli, A., Chen, H., Tomaselli, P. D., Petersen, T. U., Fredsøe, J., Raaijmakers, T. C., Kortenhaus, A., Hjelmager Jensen, J., Saremi, S., Bolding, K., & Burchard, H. (2015). D5.3 Interaction between currents, wave, structure and subsoil. General rights Copyright and moral rights for the publications made accessible in the public portal are retained by the authors and/or other copyright owners and it is a condition of accessing publications that users recognise and abide by the legal requirements associated with these rights. Users may download and print one copy of any publication from the public portal for the purpose of private study or research. You may not further distribute the material or use it for any profit-making activity or commercial gain You may freely distribute the URL identifying the publication in the public portal If you believe that this document breaches copyright please contact us providing details, and we will remove access to the work immediately and investigate your -
Optimal Breathing Gas Mixture in Professional Diving with Multiple Supply
Proceedings of the World Congress on Engineering 2021 WCE 2021, July 7-9, 2021, London, U.K. Optimal Breathing Gas Mixture in Professional Diving with Multiple Supply Orhan I. Basaran, Mert Unal compressors and cylinders, it was limited to surface air Abstract— Professional diving existed since antiquities when supply lines. In 1978, Fleuss introduced the first closed divers collected resources from the bottom of the seas and circuit oxygen breathing apparatus which removed carbon lakes. With technological advancements in the recent century, dioxide from the exhaled gas and did not form bubbles professional diving activities also increased significantly. underwater. In 1943, Cousteau and Gangan designed the Diving has many adverse effects on human physiology which first proper demand-regulated air supply from compressed are widely investigated in order to make dives safer. In this air cylinders worn on the back. The scuba equipment with study, we focus on optimizing the breathing gas mixture minimizing the dive costs while ensuring the safety of the the high-pressure regulator on the cylinder and a single hose divers. The methods proposed in this paper are purely to a demand valve was invented in Australia and marketed theoretical and divers should always have appropriate training by Ted Eldred in the early 1950s [1]. and certificates. Also, divers should never perform dives With the use of Siebe dress, the first cases of decompression without consulting professionals and medical doctors with expertise in related fields. sickness began to be documented. Haldane conducted several experiments on animal and human subjects in Index Terms—-professional diving; breathing gas compression chambers to investigate the causes of this optimization; dive profile optimization sickness and how it can be prevented. -
Instructor Development Course Award Winning Padi
INSTRUCTOR DEVELOPMENT COURSE AWARD WINNING PADI 5-STAR IDC CENTRE www.facebook.com/IDCKohTaoThailand WELCOME TO THE INSTRUCTOR DEVELOPMENT COURSE!!! MEET YOUR COURSE DIRECTOR: Marcel van den Berg Platinum PADI Course Director / EFR Instructor Trainer #492721 "Let me introduce myself; my name is Marcel van den Berg. I’m originally from the Netherlands and have now been living in Thailand for almost a decade. In 2003, I decided to take a diving course to experience the hype that everyone was talking about. It only took me 20 minutes on my first Open Water dive to realize that you can have a fantastic career in this amazing underwater realm. From that moment on, I actively pursued my career in diving. I hold a tremendous passion towards diving which I have been able to share with others during my teaching and turning thousands of students into divers. It didn’t take long to decide to advance in my career and I continued my education towards Course Director and Specialty Instructor Trainer. Within the first year I achieved Platinum Status from PADI and kept that until this day. Now I’m able to teach the success I had to new Instructors and I look forward to share my passion and success in Diving with you! Come and join us for your professional diving training at Sairee Cottage Diving and let me teach you an award winning program that far exceeds the minimum standards of the dive industry” Marcel van den Berg 2 Teaching Experience: Taught over 4500 students on all PADI levels Certifications: PADI Platinum Course Director #492721 Emergency