The Development of Microstructure in Duplex Stainless Steel Welds
Total Page:16
File Type:pdf, Size:1020Kb
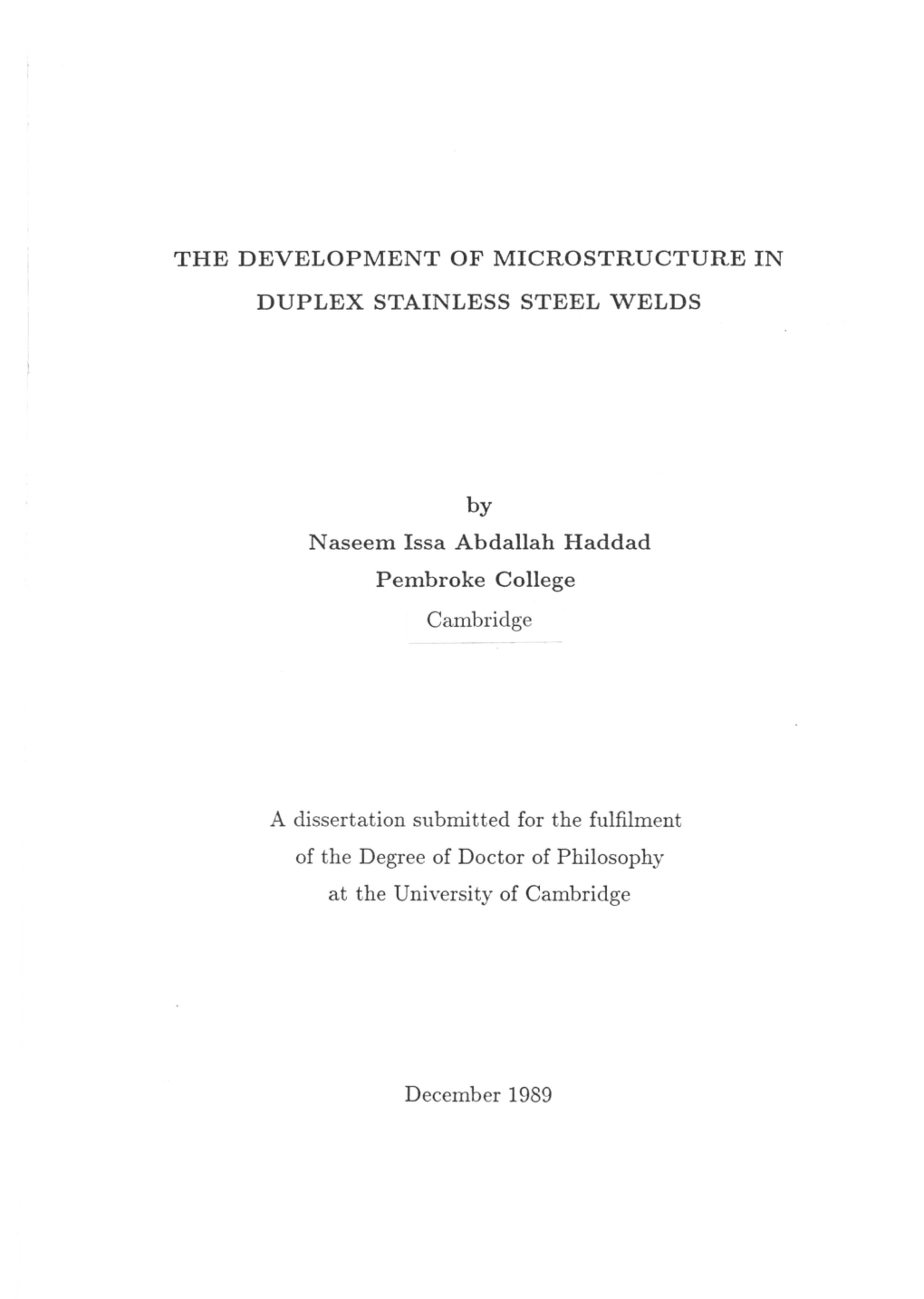
Load more
Recommended publications
-
The Superalloys: Fundamentals and Applications
Follow us in Telegram: @SpecialAlloys This page intentionally left blank The Superalloys Superalloys are unique high temperature materials used in gas turbine engines, which dis- play excellent resistance to mechanical and chemical degradation. This book presents the underlying metallurgical principles which have guided their development and practical as- pects of component design and fabrication from an engineering standpoint. The topics of alloy design, process development, component engineering, lifetime estimation and mate- rials behaviour are described, with emphasis on critical components such as turbine blades and discs. The first introductory text on this class of materials, it will provide a strong grounding for those studying physical metallurgy at the advanced level, as well as practising engineers. Included at the end of each chapter are exercises designed to test the reader’s understanding of the underlying principles presented. Additional resources for this title are available at www.cambridge.org/9780521859042. roger c. reed is Professor and Chair in Materials Science and Engineering at Imperial College London. From 1994 to 2002, he was Assistant Director of Research in the Rolls- Royce University Technology Centre at the University of Cambridge. From 2002 to 2005, he held a Canada Research Chair in the Department of Materials Engineering at the University of British Columbia, Vancouver. He is widely known in the gas turbine community for his work on the physical metallurgy of the superalloys, and has taught extensively in this field. The Superalloys Fundamentals and Applications Roger C. Reed cambridge university press Cambridge, New York, Melbourne, Madrid, Cape Town, Singapore, São Paulo Cambridge University Press The Edinburgh Building, Cambridge cb2 2ru, UK Published in the United States of America by Cambridge University Press, New York www.cambridge.org Information on this title: www.cambridge.org/9780521859042 © R. -
Awards Dinner
Awards Dinner TUESDAY, OCTOBER 25, 2016 HILTON SALT LAKE CITY CENTER SALT LAKE CITY, UTAH RECEPTION – 6:15 P.M. DINNER – 7:00 P.M. PRESIDENT’S RECEPTION – 9:30 P.M. 9639 KINSMAN ROAD | MATERIALS PARK, OHIO 44073 WWW.ASMINTERNATIONAL.ORG ASM2016_Awards_Dinner_Covers_Spreads.indd MS&T Dinner Covers_Paint.indd 2 1 9/29/2016 11:10:21 AM ASM MS&T Dinner Covers_Paint.indd 3 9/29/201610/4/2016 11:10:21 3:03:31 AM PM Nominations are now being accepted for the following awards Award Annual Nomination Deadline Would you like to change Fellow ASM November 30 Edward DeMille Campbell Memorial Lecture February 1 the future? ASM/TMS Distinguished Lecture in Materials & Society September 1 Distinguished Life Member February 1 Become an ASM Foundation champion. William Hunt Eisenman Award February 1 Engineering Materials Achievement Awards March 1 Get involved! Gold Medal February 1 Historical Landmarks February 1 Honorary Membership February 1 Volunteering couldn’t be easier! Contact us at [email protected] Medal for the Advancement of Research February 1 Allan Ray Putnam Service Award February 1 You can make a di erence and inspire students to become Albert Sauveur Achievement Award February 1 the materials pioneers of the future. Your generous donations, Bradley Stoughton Award for Young Teachers March 1 whether monetary or in-kind, help us further our mission. Albert Easton White Distinguished Teacher Award February 1 Make your donation by texting (888) 630-6063. J. Willard Gibbs Phase Equilibria Award February 1 The Silver Medal Award February 1 The Bronze Medal Award February 1 Links to Nomination requests and rules can be found at www.asminternational.org Click on Membership & Committees—then www.asmfoundation.org Awards & Nominations 2016_Awards_Dinner_Covers_Spreads.indd 2 10/4/2016 3:03:31 PM CONTENTS Officers of ASM International ..................................................................................................... -
Order of the Companions of Honour Members of the Order of the Companions of Honour
Order of the Companions of Honour Members of the Order of the Companions of Honour Sir Neville MARRINER, CBE Conductor. For services to Music. (London) The Right Honourable the Lord Harry Kenneth WOOLF, FBA (Hon) For services to the public and community relations. (London) 1 Knights Bachelor Knighthoods Henry ANGEST National Treasurer, Conservative Party. For political service. (London) Professor Harshad Kumar Dharamshi BHADESHIA, FRS FREng Tata Steel Professor of Metallurgy, University of Cambridge. For services to Science and Technology. (Cambridgeshire) The Right Honourable Simon Hugh McGuigan BURNS, MP Member of Parliament for Chelmsford. For parliamentary and political service. (Essex) Dr Philip Henry Montgomery CAMPBELL Editor in Chief, Nature. For services to Science. (London) Dr Kevan Arthur COLLINS Chief Executive, Education Endowment Foundation. For services to Education. (London) Dr Naim Eliahou DANGOOR, CBE Philanthropist. For charitable services. (London) Michael Lawrence DAVIS Chair, Prime Minister's Holocaust Mick Commission. For services to Holocaust Commemoration and Education. (London) Ciaran Gearoid DEVANE Lately Chief Executive, Macmillan Cancer Support. For services to Cancer Patients. (London) Professor Charles Peter DOWNES, OBE FRSE Principal and Vice-Chancellor, University of Dundee. For services to Higher Education and Life Sciences. (Newport-on-Tay, Fife) Gareth Owen EDWARDS, CBE For services to Sport and for charitable services. (Bridgend, Mid Glamorgan) 2 Bernard Peter GRAY Chief of Defence Materiel, Ministry of Defence. For public service, particularly to Defence. (Oxfordshire) Patrick HEAD, FREng Lately Director, Williams Hybrid Power Ltd. For services to Motorsport. (London) Lenworth George HENRY, CBE Actor and Comedian. For services to Drama and charity. (London) The Right Honourable Simon Henry Ward HUGHES Lately Member of Parliament for Bermondsey and Old Southwark. -
Grain Boundary Serration in Nickel-Based Superalloy Inconel 600: Generation and Effects on Mechanical Behavior
TOPICAL COLLECTION: SUPERALLOYS AND THEIR APPLICATIONS Grain Boundary Serration in Nickel-Based Superalloy Inconel 600: Generation and Effects on Mechanical Behavior YUANBO T. TANG, ANGUS J. WILKINSON, and ROGER C. REED Grain boundary serration in the superalloy Inconel 600 was studied. Two microstructural variants, one with nonserrated and the other with serrated grain boundaries were generated by altering the heat-treatment conditions, while keeping other aspects of the microstructure unchanged. The effect on the creep response between 700 °C and 900 °C was measured, and the different failure modes and accumulated damage were quantified using high-angular resolution electron backscatter diffraction analysis in the scanning electron microscope and also by X-ray computed tomography. It is found that serration plays a more crucial role in the high-tem- perature/low-stress regime when an intergranular cracking mechanism involving cavitation is operative; here it plays a role in improving both creep life and creep ductility. Any effect of serration is less prevalent at low temperatures where transgranular failure is dominant. https://doi.org/10.1007/s11661-018-4671-7 Ó The Author(s) 2018 I. INTRODUCTION composition.[3–11] The study of Koul & Gessinger on the Inconel 738, Nimonic 115 and Nimonic 105 alloys,[3] SERRATION of grain boundaries in metals and involving an impressive combination of experimentation alloys, for example the nickel-based superalloys of the and modeling, identified the role of c0 migration on type studied here, is intriguing for various reasons. First, serration. The role of the c0 phase has since been there is complexity arising from the inapplicability of the confirmed by a number of researchers.[6,12–15] But what generally accepted picture of smooth or gently curved happens in the absence of the c0 phase? Alloys contain- grain boundaries, as observed on the microscale. -
Annual Review Annex 2017/18 Annex to the Annual Review
Annual Review Annex 2017/18 Annex to the Annual Review Contents Fellows elected in 2017 2 RAEng-Royal Commission 1851 Enterprise Fellowships 23 International Fellows 2 GCRF Frontiers of Engineering for Honorary Fellows 2 Development Seed Funding 24 Fellows 2 Leaders in Innovation Fellowships 27 Trustee Board 4 GCRF Africa Catalyst 27 Academy Governance Committees 5 Higher Education Partnerships in Sub-Saharan Africa 28 Academy Operating Committees 8 Industry-Academia Partnership Programme 29 Academy other committees 11 UK-China Urban Flooding Research Impact Programme 34 Grants, fellowships and programmes 12 Distinguished Visiting Fellowships Research Chairs 12 and Missions in Turkey 35 Senior Research Fellowships 14 Distinguished Visiting Fellowships 36 Chairs in Emerging Technologies 15 Africa Prize for Engineering Innovation 38 Daphne Jackson Trust Fellowships 15 Ingenious Public Engagement Awards 39 Research Fellowships 16 Engineering Leaders Scholarships 40 RAEng/Lloyd’s Register Foundation Visiting Professors 43 Research Fellowships 18 Sainsbury Management Fellowships 44 Engineering for Development Connecting STEM Teachers 44 Research Fellowships 18 Queen Elizabeth Prize for Engineering 46 UK IC Postdoctoral Research Fellowships 18 Panel of judges 46 Industrial Fellowships 19 Trustees 46 Leverhulme Trust Senior Research Fellowships 20 Donors 47 APEX Awards 20 Search group 47 Enterprise Fellowships 21 Development and fundraising 48 Blavatnik Family Foundation Enterprise Development Advisory Board 48 Fellowship Alumni Awards 22 Contributors to Academy programmes 49 SME Leaders Programme 22 Royal Academy of Engineering Launchpad Competition 22 2017 Annual Fund 50 RAEng-ERA Foundation Entrepreneurs Award 23 1 Fellows Fellows of the Academy are leading engineers in the UK drawn from academia, industry and the not-for-profit sectors.