A Report on Worldwide Hydrogen Bus Demonstrations, 2002-2007
Total Page:16
File Type:pdf, Size:1020Kb
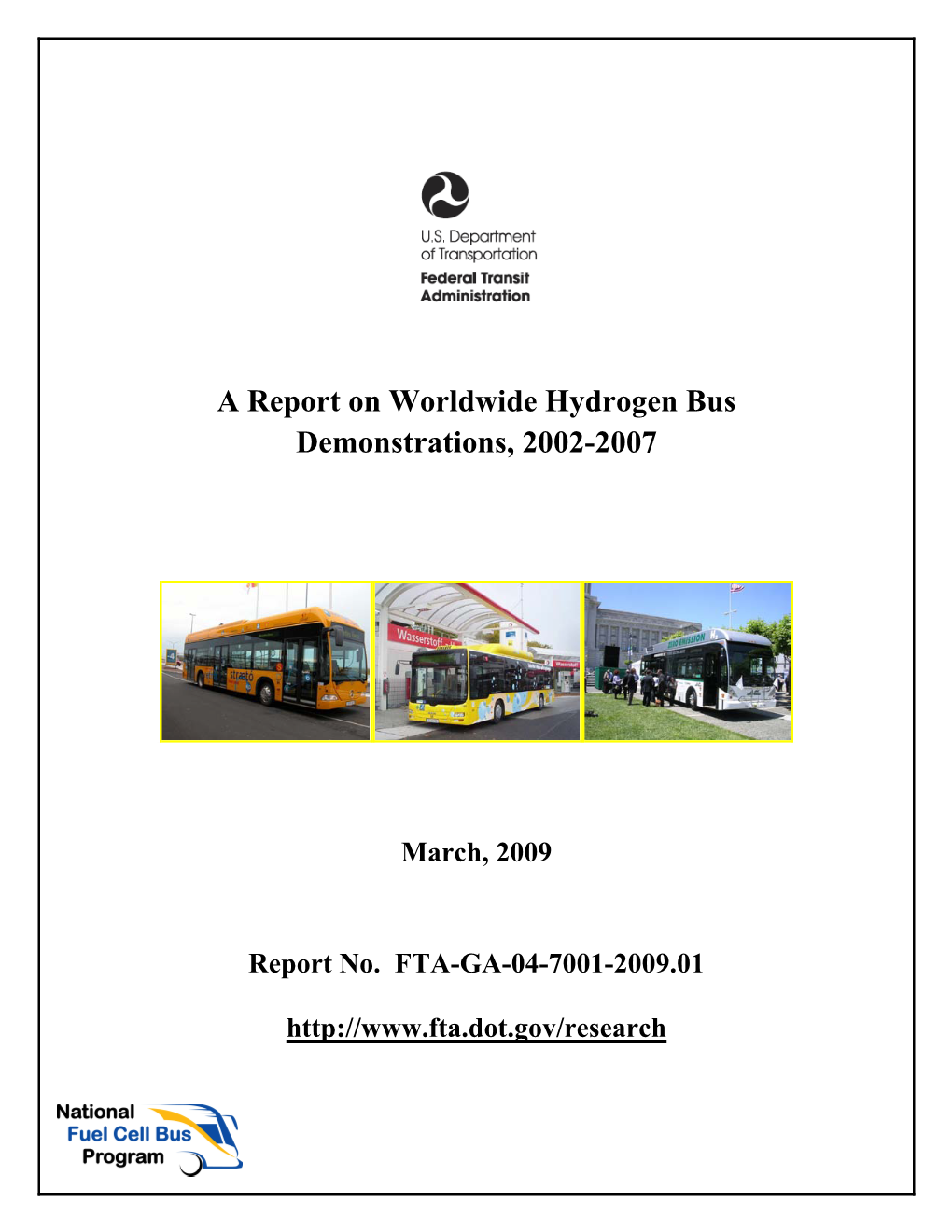
Load more
Recommended publications
-
90929 CEC Hydrogen Technology Workshop Subset
DOCKET 09-ALT-1 DATE 9/29/2009 RECD. 9/30/2009 Hydrogen fueled Heavy Duty Transport Paul B. Scott, CSO, ISE Corporation, Poway, CA pscott @isecorp.com Presentation to CEC Investment Plan Staff Workshop 29 September 2009 1 Preview: • Five introductory slides on the Company, ISE • Some hard facts…. • Hydrogen transportation technology assessment • Critical challenges • Money: cost & volume estimates • Closing suggestions in summary 2 ISE has pioneered in electric drive transit vehicle development 3 ISE Detail: • Focused exclusively on electric drive heavy duty vehicles and components therefor, Clean Vehicles for a Clean Planet, since 1995 • 140 employees, most in Poway, CA, designing & fabricating drive system assemblies to be installed by bus manufacturers • Approaching 300 vehicles in revenue service every day, cumulative mileage in excess of 10 million miles, • Privately held Long Beach Transit operated New Flyer Gasoline Hybrid – “x-ray vision” reveals ultra-capacitors, cooling atop, generator & engine below 4 What does ISE do? ISEISE’s’s Partners Partners && ISE:ISE: LeaderLeader inin IntegratedIntegrated HybridHybrid DriveDrive SystemsSystems CustomersCustomers && SuppliersSuppliers MarketsMarkets ISE designs, integrates, installs and services its own energy management ISE sources complementary systems, accessories and control software with third party components into a ISE systems are designed into components from complete series hybrid-electric drive system optimized for heavy duty vehicles and sold with the platforms of market-leading -
Fuel Cell Transit Buses: Thunderpower Bus Evaluation at Sunline Transit Agency
Hydrogen, Fuel Cells & Infrastructure Technologies Program Fuel Cell Transit Buses ThunderPower Bus Evaluation at SunLine Transit Agency A Strong Energy Portfolio for a Strong America Energy effi ciency and clean, renewable energy will mean a stronger economy, a cleaner en- vironment, and greater energy independence for America. By investing in technology break- throughs today, our nation can look forward to a more resilient economy and secure future. Far-reaching technology changes will be essential to America’s energy future. Working with a wide array of state, community, industry, and university partners, the U.S. Department of Energy’s Offi ce of Energy Effi ciency and Renewable Energy invests in a portfolio of energy technologies that will: • Conserve energy in the residential, commercial, industrial, government, and transportation sectors • Increase and diversify energy supply, with a focus on renewable domestic sources • Upgrade our national energy infrastructure • Facilitate the emergence of hydrogen technologies as vital new “energy carriers.” The Opportunities Biomass Program Hydrogen, Fuel Cells & Infrastructure Using domestic, plant-derived resources to Technologies Program meet our fuel, power, and chemical needs Paving the way toward a hydrogen econo- my and net-zero carbon energy future Building Technologies Program Homes, schools, and businesses that Industrial Technologies Program use less energy, cost less to operate, and Boosting the productivity and competi- ultimately, generate as much power as tiveness of U.S. industry -
An Attractive Value Proposition for Zero-Emission Buses in Denmark
Fuel Cell Electric Buses An attractive Value Proposition for Zero-Emission Buses In Denmark - April 2020 - Photo: An Attractive Line Bloch Value Klostergaard, Proposition North for Denmark Zero-Emission Region Buses. in Denmark Executive Summary Seeking alternatives to diesel buses are crucial for realizing the Danish zero Zero–Emission Fuel Cell emission reduction agenda in public transport by 2050. In Denmark alone, public transport and road-transport of cargo account for ap- proximately 25 per cent of the Danish CO2 emissions. Thus, the deployment of zero emission fuel cell electric buses (FCEBs) will be an important contribution Electric Buses for Denmark. to the Danish climate law committed to reaching 70 per cent below the CO2 emissions by 2030 and a total carbon neutrality by 2050. In line with the 2050 climate goals, Danish transit agencies and operators are being called to implement ways to improve air quality in their municipalities while maintaining quality of service. This can be achieved with the deployment of FCEBs and without compromising on range, route flexibility and operability. As a result, FCEBs are now also being included as one of the solutions in coming zero emission bus route tenders Denmark. Danish municipalities play an important role in establishing the public transport system of the future, however it is also essential that commercial players join forces to realize the deployment of zero-emission buses. In order to push the de- velopment forward, several leading players in the hydrogen fuel cell value chain have teamed up and formed the H2BusEurope consortium committed to support the FCEB infrastructure. -
National Fuel Cell Bus Program: Accelerated Testing Evaluation
Form Approved REPORT DOCUMENTATION PAGE OMB No. 0704-0188 Public reporting burden for this collection of information is estimated to average one hour per response, including the time for reviewing instructions, searching existing data sources, gathering and maintaining the data needed, and completing and reviewing the collection of information. Send comments regarding this burden estimate or any other aspect of this collection of information, including suggestions for reducing this burden, to Washington Headquarters Services, Directorate for Information Operations and Reports, 1215 Jefferson Davis Highway, Suite 1204, Arlington, VA 22202-4302, and to the Office of Management and Budget, Paperwork Reduction Project (0704-0188), Washington, DC 20503. 1. AGENCY USE ONLY (Leave 2. REPORT DATE 3. REPORT TYPE AND DATES blank) January 2009 COVERED Appendices, January 2009 4. TITLE AND SUBTITLE 5. FUNDING NUMBERS National Fuel Cell Bus Program: Accelerated Testing Report, AC Transit Appendices 6. AUTHOR(S) Kevin Chandler*, Leslie Eudy,** 7. PERFORMING ORGANIZATION NAME(S) AND ADDRESS(ES) 8. PERFORMING ORGANIZATION REPORT National Renewable Energy Laboratory, 1617 Cole Blvd., Golden, CO 80401 NUMBER Battelle, 505 King Ave. Columbus, OH 43201 9. SPONSORING/MONITORING AGENCY NAME(S) AND ADDRESS(ES) 10. SPONSORING/ Office of Research, Demonstration, and Innovation MONITORING Federal Transit Administration, 1200 New Jersey Ave, S.E., Washington, D.C. 20590 AGENCY REPORT NUMBER FTA-CO-26-7004-2009.1A 11. SUPPLEMENTARY NOTES *Battelle Memorial Institute **National Renewable Energy Laboratory 12a. DISTRIBUTION/AVAILABILITY STATEMENT 12b. DISTRIBUTION CODE No Restrictions. Available From: National Technical Information Service/NTIS, Springfield, Virginia, 22161. Phone 703.605.6000, Fax 703.605.6900, Email [[email protected]] 13. -
Fuel Cell Electric Buses Are in Operation Between Versailles and Jouy-En-Josas
INFORMATIONAL April 2020 Fuel Cell Electric Buses An attractive value proposition for zero emission buses in France Zero–Emission Fuel Cell Buses for France Van Hool fuel cell electric buses are in operation between Versailles and Jouy-en-Josas 2 Executive Summary France has recognized the importance of sustainable transportation. With the knowledge that mobility is a key contributor to air pollution, there is immense pressure to reduce CO2 emis- sions. Evidence of this is the ban on diesel and petrol car sales from 2040 and the strategy for clean mobility put forward in the “Loi de Transition Energétique pour la Croissance Verte.” French cities are also leading initiatives to reduce local emissions, such as Paris’ ambition to ban diesel cars as early as 2023. There is no doubt that the future of public transportation is going to be zero emission. Transit agencies and operators in France are being called to find ways to improve air quality in their communities while maintaining quality of service. The choice that faces cities and transit au- thorities is what technology to deploy. Transit operators can consider two zero emission elec- tric bus solutions: fuel cell electric buses (FCEBs) or battery electric buses (BEBs). FCEBs are electric buses which offer all the benefits of BEBs while facilitating large scale de- ployments. FCEBs fueled with hydrogen are the only zero-emission technology to match diesel fleets with complete route flexibility, short refueling time and similar depot space utilization. With more than 15 years on the road and millions of kilometers in passenger service, FCEBs have proven their performance. -
Leading Players Enabling True Zero-Emission Hydrogen Solution For
PRESS RELEASE 3 June 2019 Leading players enabling true zero-emission hydrogen solution for public transportation Everfuel, Wrightbus, Ballard Power Systems, Hexagon Composites, Nel Hydrogen and Ryse Hydrogen, leading players in the hydrogen fuel cell electric value chain, announce today that they are joining forces to form the H2Bus Consortium. The members are committed to deploying 1,000 hydrogen fuel cell electric buses, along with supporting infrastructure, in European cities at commercially competitive rates. This ground breaking hydrogen fuel cell electric bus solution will be the most cost-effective truly zero-emission option available, with a single-decker bus price below €375,000 after funding, a hydrogen price between €5 and €7 per kilogram and a service cost of €0.30 per kilometre. The zero-tailpipe emission feature of the fuel cell bus’ operation will be complemented by zero-emission hydrogen production from renewable energy sources, yielding a “well-to-wheel” emission-free transportation solution. “It is essential that commercial players join forces to realize the true zero-emission mobility society,” says David Barnett, Business Development Director at Wrightbus. “The hydrogen fuel cell electric bus is the ideal substitute for fossil solutions, without compromising range, operational ability or cost. Wrightbus is also expanding its product offering to include a fuel cell electric double decker bus, 12-meter single-decker bus and articulated bus in order to serve a wider customer base. We are currently witnessing the transformation of public transport for the benefit of both current and coming generations and we feel privileged to be part of this transition together with the other consortium members.” The first phase of the project, totalling 600 buses, is supported by €40 million from the EU’s Connecting Europe Facility (CEF1). -
CHBC Hydrogen Fuel Cell Electric Bus Workshop September 27, 2017
CHBC Hydrogen Fuel Cell Electric Bus Workshop September 27, 2017 Emanuel Wagner, Jeff Serfass, Hosted at CalEPA Peter Thompson, Cory Shumaker Acknowledgements Planning Committee This workshop was planned by the members of the Public Transport Sector Action Group within the CHBC, under its leadership by Lauren Skiver, General Manager of SunLine Transit, and Nicolas Pocard, Director of Marketing at Ballard Power Systems. Workshop Sponsors We thank the following organizations for their financial contribution, without which this workshop would not have been possible to develop and execute. Disclaimer This Workshop Report is a summary compiled by CHBC staff. Staff seeks to represent the discussions as complete and accurate as possible; however, staff cannot and does not take responsibility for a fully accurate representation of the discussions at the workshop. Questions? Contact the California Hydrogen Business Council via mail at 18847 Via Sereno Yorba Linda, CA 92886 310-455-6095 or email at [email protected] or phone at 310-455-6095 1 | P a g e Contents Welcome and Overview of the Workshop ............................................................................................................. 3 Jeff Serfass, Executive Director, California Hydrogen Business Council ......................................................................... 3 Current Deployment Status, System Performance, Fueling Options ........................................................................ 3 Nicolas Pocard, Director of Marketing, Ballard Power -
October 2009 Transit Research Update
Transit Research and Industry News Update Contents – October 2009 To view any item listed, use the mouse and control/click on title. SPECIAL............................................................................................................................ 3 Highlights of FTA Impact on Public Transportation.................................................. 3 Federal Transit Administration Launches Bus Safety and Security Website for Small Urban and Rural Transit Agencies......................................................................... 3 Proterra Shows All-Electric Bus in D.C. .................................................................... 3 RESEARCH IN PROGRESS............................................................................................. 4 Dual Variable Output Fuel Cell Hybrid Bus Validation Testing and Demonstration (Proterra Bus) Project............................................................................................. 4 National Bus Rapid Transit Institute........................................................................... 4 ITS Pilot Project at the Ohio State University ............................................................ 5 FROM THE TRI RESEARCH CORNER......................................................................... 6 Delegation from UK Meeting with USDOT Representatives .................................... 6 Distracted Driving Summit ......................................................................................... 6 Meeting with Delegation from the Czech -
(ZEBA) Fuel Cell Bus Demonstration: First Results Report Kevin Chandler Battelle Leslie Eudy National Renewable Energy Laboratory
Zero Emission Bay Area (ZEBA) Fuel Cell Bus Demonstration: First Results Report Kevin Chandler Battelle Leslie Eudy National Renewable Energy Laboratory NREL is a national laboratory of the U.S. Department of Energy, Office of Energy Efficiency & Renewable Energy, operated by the Alliance for Sustainable Energy, LLC. Technical Report NREL/TP-5600-52015 August 2011 Contract No. DE-AC36-08GO28308 Zero Emission Bay Area (ZEBA) Fuel Cell Bus Demonstration: First Results Report Kevin Chandler Battelle Leslie Eudy National Renewable Energy Laboratory Prepared under Task No. H270.8150 NREL is a national laboratory of the U.S. Department of Energy, Office of Energy Efficiency & Renewable Energy, operated by the Alliance for Sustainable Energy, LLC. National Renewable Energy Laboratory Technical Report 1617 Cole Boulevard NREL/TP-5600-52015 Golden, Colorado 80401 August 2011 303-275-3000 • www.nrel.gov Contract No. DE-AC36-08GO28308 NOTICE This report was prepared as an account of work sponsored by an agency of the United States government. Neither the United States government nor any agency thereof, nor any of their employees, makes any warranty, express or implied, or assumes any legal liability or responsibility for the accuracy, completeness, or usefulness of any information, apparatus, product, or process disclosed, or represents that its use would not infringe privately owned rights. Reference herein to any specific commercial product, process, or service by trade name, trademark, manufacturer, or otherwise does not necessarily constitute or imply its endorsement, recommendation, or favoring by the United States government or any agency thereof. The views and opinions of authors expressed herein do not necessarily state or reflect those of the United States government or any agency thereof. -
Fuel Cell Electric Bus Initiative
THE 100-BUS FUEL CELL ELECTRIC BUS INITIATIVE PREPARED BY THE CENTER FOR TRANSPORTATION AND THE ENVIRONMENT The 100-Bus Fuel Cell Electric Bus Initiative (100-Bus Initiative) is a Center for Transportation and the Environment (CTE)-led consortium including leading transit agencies from California, bus original equipment manufacturers (OEMs), technology companies, and fueling infrastructure providers focused on accelerating the commercialization of fuel cell electric buses (FCEBs) in California. Background FCEBs have proven out the technology in deployments all over the world, with more than 10 million miles of passenger service. The deployments have demonstrated the performance, reliability, and durability required for commercial operation of the technology, achieving significant commercial milestones including: Buy America compliance, Federal Transit Administration (FTA) Altoona testing, and a burgeoning competitive landscape between bus OEMs and fuel cell engine suppliers, all indicators of the technology’s readiness for widespread commercialization. The pace of implementation has increased dramatically over the last few years, both globally and in North America, where only a few barriers remain to the large-scale adoption of FCEBs within both public transit agencies and other adjacent markets. FCEBs offerfour distinct advantages, including: 300-340 miles Proven range (300 to 340 miles, Significant reduction Fast refueling 1:1 replacement of with advanced in vehicle weight speeds conventional buses fueling technology and vehicle axle comparable to enabling full flexibility that can extend this weight to maximize conventional diesel for route planning range by almost passenger loads and CNG buses and operations double) There are currently two primary FCEB fleets operating in California. SunLine Transit in the Coachella Valley operates five buses and there are 13 buses in operation at the Alameda-Contra Costa Transit District (AC Transit) in Oakland, CA. -
Characteristics of Bus Rapid Transit for Decision-Making
Project No: FTA-VA-26-7222-2004.1 Federal United States Transit Department of August 2004 Administration Transportation CharacteristicsCharacteristics ofof BusBus RapidRapid TransitTransit forfor Decision-MakingDecision-Making Office of Research, Demonstration and Innovation NOTICE This document is disseminated under the sponsorship of the United States Department of Transportation in the interest of information exchange. The United States Government assumes no liability for its contents or use thereof. The United States Government does not endorse products or manufacturers. Trade or manufacturers’ names appear herein solely because they are considered essential to the objective of this report. Form Approved REPORT DOCUMENTATION PAGE OMB No. 0704-0188 Public reporting burden for this collection of information is estimated to average 1 hour per response, including the time for reviewing instructions, searching existing data sources, gathering and maintaining the data needed, and completing and reviewing the collection of information. Send comments regarding this burden estimate or any other aspect of this collection of information, including suggestions for reducing this burden, to Washington Headquarters Services, Directorate for Information Operations and Reports, 1215 Jefferson Davis Highway, Suite 1204, Arlington, VA 22202-4302, and to the Office of Management and Budget, Paperwork Reduction Project (0704-0188), Washington, DC 20503. 1. AGENCY USE ONLY (Leave blank) 2. REPORT DATE 3. REPORT TYPE AND DATES August 2004 COVERED BRT Demonstration Initiative Reference Document 4. TITLE AND SUBTITLE 5. FUNDING NUMBERS Characteristics of Bus Rapid Transit for Decision-Making 6. AUTHOR(S) Roderick B. Diaz (editor), Mark Chang, Georges Darido, Mark Chang, Eugene Kim, Donald Schneck, Booz Allen Hamilton Matthew Hardy, James Bunch, Mitretek Systems Michael Baltes, Dennis Hinebaugh, National Bus Rapid Transit Institute Lawrence Wnuk, Fred Silver, Weststart - CALSTART Sam Zimmerman, DMJM + Harris 8. -
Fuel Cell Zero-Emission Buses for Aberdeen, Scotland Fuel Cell Zero-Emission Buses for Aberdeen, Scotland
CASE STUDY Fuel Cell Zero-Emission Buses for Aberdeen, Scotland Fuel Cell Zero-Emission Buses for Aberdeen, Scotland Situation The City of Aberdeen, Scotland has a world-wide reputation hydrogen technologies. It is part of the larger H2 Aberdeen in the energy industry. With the discovery of significant oil initiative, which provides the opportunity to create a new deposits in the North Sea, Aberdeen became the centre of industry and greater choice in energy production and usage. Europe’s petroleum industry. However, downturns in the oil and gas sector have impacted the economy and city leaders Implementation of the fleet of hydrogen fuel cell buses in are repositioning he city as the “Energy Capital of Europe,” with Aberdeen was co-financed through two projects funded by the a focus on the development of new energy sources. The launch European Fuel Cell and Hydrogen Joint Undertaking (FCH JU): High V.LO-City and HyTransit. Other Scottish, UK and European partners came together to co-fund the balance of the project, including the UK’s innovation agency, Innovate UK; the Scottish Government; Scottish Enterprise;Aberdeen City Council; transit operators First and Stagecoach; Scottish Hydro Electric Power Distribution;and Scotland Gas Network. BOC, a member of Linde Group, has invested in the hydrogen production and refueling station.Europe. 3Emotion is also funded by the EU through FCH JU. Site Aberdeen, Scotland Ten zero-emission hydrogen fuel cell Application buses, Europe’s largest fleet of the Strategy Framework “A Hydrogen Economy for Aberdeen 150kW FCveloCity®-HD power City Region” in 2013 reflects Aberdeen’s ambition to become a System modules integrated onto Van Hool chassis leading European region in the early deployment of hydrogen technologies.