UNITE-D STATESJPATBNT Omen .V
Total Page:16
File Type:pdf, Size:1020Kb
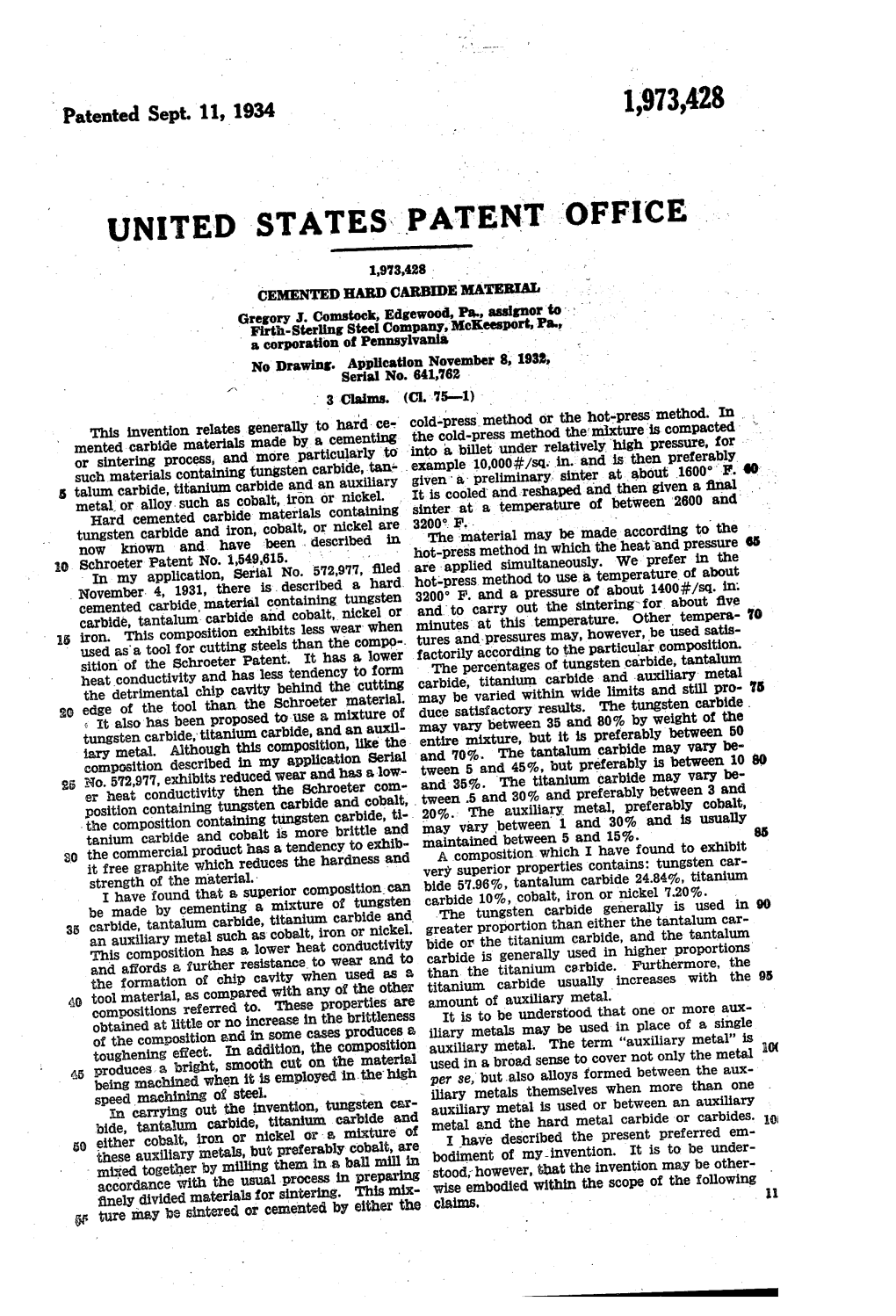
Load more
Recommended publications
-
Method for Producing Thick Ceramic Films by a Sol Gel
Europäisches Patentamt *EP000815285B1* (19) European Patent Office Office européen des brevets (11) EP 0 815 285 B1 (12) EUROPEAN PATENT SPECIFICATION (45) Date of publication and mention (51) Int Cl.7: C23C 18/12 of the grant of the patent: // C04B41/87, C04B41/50 22.08.2001 Bulletin 2001/34 (86) International application number: (21) Application number: 96901675.7 PCT/CA96/00088 (22) Date of filing: 13.02.1996 (87) International publication number: WO 96/29447 (26.09.1996 Gazette 1996/43) (54) METHOD FOR PRODUCING THICK CERAMIC FILMS BY A SOL GEL COATING PROCESS VERFAHREN ZUR HERSTELLUNG DICKER KERAMIKFILMS DURCH SOL-GEL-BESCHICHTUNGSPROZESS PROCEDE DE FABRICATION DE FILMS DE CERAMIQUE EPAIS METTANT EN UVRE UN PROCESSUS DE REVETEMENT SOL-GEL (84) Designated Contracting States: (74) Representative: AT BE CH DE DK ES FR GB GR IE LI NL PT SE Simpson, Alison Elizabeth Fraser et al Urquhart-Dykes & Lord, (30) Priority: 22.03.1995 US 409127 30 Welbeck Street London W1G 8ER (GB) (43) Date of publication of application: 07.01.1998 Bulletin 1998/02 (56) References cited: EP-A- 0 433 915 EP-A- 0 482 659 (73) Proprietor: QUEEN’S UNIVERSITY AT KINGSTON EP-A- 0 564 866 WO-A-96/00198 Kingston Ontario K7L 3N6 (CA) US-A- 4 921 731 (72) Inventors: • TECHNICAL DISCLOSURE BULLETIN, vol. 37, • BARROW, David No 09, September 1994, "Low Leakage, Ajax, Ontario L1S 6Z4 (CA) Temperature Invariant, High Dielectric Constant • PETROFF, Edward, T. Films, using Multilayered Sol-Gel Fabrication", Scarborough, Ontario M1T 1V8 (CA) page 27 - page 28 • SAYER, Michael • PATENT ABSTRACTS OF JAPAN, vol. -
The Titanium Industry: a Case Study in Oligopoly and Public Policy
THE TITANIUM INDUSTRY: A CASE STUDY IN OLIGOPOLY AND PUBLIC POLICY DISSERTATION Presented in Partial Fulfillment of the Requirements for the Degree Doctor of Philosophy In the Graduate School of the Ohio State University by FRANCIS GEORGE MASSON, B.A., M.A. The Ohio State University 1 9 5 k Content* L £MR I. INTRODUCTION............................................................................................... 1 II. THE PRODUCT AND ITS APPLICATIONS...................................... 9 Consumption and Uses ................................. 9 Properties ........................................................ ...... 16 III. INDUSTRY STRUCTURE................................................................................ 28 Definition of the I n d u s t r y ............................................ 28 Financial Structure. ..••••••.••. 32 Alloys and Carbide Branch. ........................... 3 k Pigment Branch .............................................................................. 35 Primary Metal Branch ................................. 1*0 Fabrication Branch ................................. $0 IT. INDUSTRY STRUCTURE - CONTINUED............................................. $2 Introduction ................................ $2 World Production and Resources ................................. $3 Nature of the Demand for Ram Materials . $8 Ores and Concentrates Branch. ••••••• 65 Summary.................................................................. 70 V. TAXATION. ANTITRUST AND TARIFF POLICY............................ -
Pdf 1007.44 K
IJE TRANSACTIONS B: Applications Vol. 29, No. 5, (May 2016) 677-687 International Journal of Engineering Journal Homepage: www.ije.ir A Review on Titanium Nitride and Titanium Carbide Single and Multilayer Coatings Deposited by Plasma Assisted Chemical Vapor Deposition a, A. Sabour Rouhaghdamb, S. Ahangaranic٭M. Azadi a Faculty of metallurgical Engineering and material, Semnan University, Semnan, Iran b Faculty of Engineering, Materials Engineering Department, Surface Engineering Laboratory ,Tarbiat Modares University, Tehran, Iran c Advanced Materials and Renewable Energies Department, Iranian Research Organization for Science and Technology, Tehran, Iran P A P E R I N F O ABSTRACT Paper history: In this paper, we reviewed researches about the titanium nitride (TiN) and titanium carbide (TiC) Received 21 September 2015 single and multilayer coatings. These coatings were deposited by the plasma assisted chemical vapor Received in revised form 06 February 2016 deposition (PACVD) technique. Plasma-based technologies are used for the processing of thin films Accepted 4 March 2016 and coatings for different applications such as automobile and aerospace parts, computer disc drives, food industry and surgical/medical instruments. We describe the state of the performance of different Keywords: coating systems and thin film architectures in PACVD suitable for industrial-scale or laboratory Titanium Nitride applications. Mechanical properties of coatings such as wear resistance, hardness and the scratch Titanium Carbide resistance, structural characteristics, physical and chemical properties like coatings adhesion into Multilayer Coatings different substrates, wetting behavior and corrosion resistance were studied. Thus, this paper represents Hard Coatings a source of information for those who want to familiarize with the status of knowledge in the area of Plasma Assisted Chemical Vapor Deposition materials science of functional coatings, in particular TiN/TiC coatings that was deposited by a new Plasma-based technologies. -
Synthesis of Titanium Carbide by Means of Pressureless Sintering
ceramics Article Synthesis of Titanium Carbide by Means of Pressureless Sintering Tatiana Kvashina 1,*, Nikolai Uvarov 1,2 and Arina Ukhina 2 1 Department of Chemistry and Chemical Technology, Novosibirsk State Technical University, 630073 Novosibirsk, Russia; [email protected] 2 Institute of Solid State Chemistry and Mechanochemistry SB RAS, 630090 Novosibirks, Russia; [email protected] * Correspondence: [email protected]; Tel.: +7-923-129-9892 Received: 4 June 2020; Accepted: 14 August 2020; Published: 18 August 2020 Abstract: In this study, titanium carbide was obtained by low-temperature pressureless (at pressure less than 1 MPa) sintering of a mixture of elementary titanium and graphite powders in a hot-pressing plant with a preliminary mechanical treatment of the initial mixture. The sintering was carried out at temperatures of 900 and 1000 ◦C in argon media. As a result, cubic modification (Fm3m) of titanium carbide was obtained. The content of impurities was about 12–13 wt.% Keywords: titanium carbide; mechanical activation; synthesis of elements; pressureless sintering 1. Introduction Currently, the synthesis of high-melting compounds for high technology applications is one of the topical problems of material sciences. Titanium carbide exhibits such properties as high values of hardness, crack and wear resistance, fatigue limit and modulus of elasticity, and heat resistance, and is a promising compound of this type [1]. Titanium carbide is widely used as an abrasive material, a component of hard-alloy tools, cutting tools, and carbidosteels, as well as in the manufacture of dispersed-hardened alloys, metal alloying, and ceramics. A new and prospective application of titanium carbide is the synthesis of MAX phases Ti2AlC and Ti3AlC2. -
Low-Cost Synthesis and Consolidation of Titanium Carbide
Project Fact Sheet LOW-COST SYNTHESIS AND CONSOLIDATION OF TITANIUM CARBIDE BENEFITS NEW MECHANOCHEMICAL PROCESS DELIVERS • Enhances mechanical properties and ULTRA FINE TITANIUM-CARBIDE POWDER FOR USE IN wear resistance of TiC composites THE FABRICATION OF CUTTING TOOLS by reducing particle size • Significantly reduces production Titanium carbide (TiC) is a model structural material due to its hardness, high- temperature stability, and low density. However, the widespread use of TiC in energy by shortening processing cutting tools and other applications has been limited because the production of TiC time through use of ambient- has not been cost effective and the fracture strength of the material has resulted in temperature processing poor fracture toughness. • Reduces high cost of synthesized The insufficient fracture toughness of conventionally produced TiC is characteristic TiC powder, making it cost effective of the synthesis process used, which involves reduction of titanium dioxide by for use in creating cutting tools carbon black at high temperatures. These high process temperatures, in addition to • Eliminates CO gas by-product of increasing costs, also result in the formation of the large carbide particles that can cause failure of TiC-based cemented carbides. However, the use of smaller carbide conventional TiC synthesis particles for the production of fine-grained composites is prohibitively expensive. A new technology, low-cost synthesis and consolidation of TiC, is being developed APPLICATIONS as a cost-effective mechanochemical processing method that yields an ultra fine Low-cost processing of TiC would titanium-carbide powder. In this process, mechanical milling fosters an ambient- temperature reaction to produce extremely fine TiC powder, which is then combined allow its use in the cutting-tool industry with low-cost, iron-based alloy powders. -
Atmospheric Pressure Chemical Vapor Deposition of Tin from Tetrakis(Dimethylamido)Titanium and Ammonia Joshua N
Journal of MATERIALS RESEARCH Welcome Comments Help Atmospheric pressure chemical vapor deposition of TiN from tetrakis(dimethylamido)titanium and ammonia Joshua N. Musher and Roy G. Gordon Department of Chemistry, Harvard University, Cambridge, Massachusetts 02138 (Received 15 December 1994; accepted 28 October 1995) Near stoichiometric titanium nitride (TiN) was deposited from tetrakis(dimethylamido)titanium (TDMAT) and ammonia using atmospheric pressure chemical vapor deposition. Experiments were conducted in a belt furnace; static experiments provided kinetic data and continuous operation uniformly coated 150-mm substrates. Growth rate, stoichiometry, and resistivity are examined as functions of deposition temperature (190–420 ±C), ammonia flow relative to TDMAT (0–30), and total gas-flow rate (residence time 0.3–0.6 s). Films were characterized by sheet resistance measurements, Rutherford Backscattering Spectrometry, and X-Ray Photoelectron Spectrometry. Films deposited without ammonia were substoichiometric (NyTi , 0.6–0.75), contained high levels of carbon (CyTi 0.25–0.40) and oxygen (OyTi 0.6–0.9), and grew slowly. Small amounts of ammonia (NH3yTDMAT > 1) brought impurity levels down to CyTi , 0.1 and OyTi 0.3–0.5. Ammonia increased the growth rates by a factor of 4–12 at temperatures below 400 ±C. Films 500 A˚ thick had resistivities as low as 1600 mV-cm when deposited at 280 ±C and 1500 mV-cm when deposited at 370 ±C. Scanning electron micrographs indicate a smooth surface and poor step coverage for films deposited with high ammonia concentrations. I. INTRODUCTION Three problems are associated with this process: Nitrides are technologically important materials be- chlorine contamination, HCl by-products, and high sub- cause of their hardness, stability at high temperatures, strate temperatures. -
Titanium Carbide Mxene Shows an Electrochemical Anomaly in Water-In-Salt Electrolytes
Titanium carbide MXene shows an electrochemical anomaly in water-in-salt electrolytes Xuehang Wang,a Tyler S. Mathis,a Yangyunli Sun,b Wan-Yu Tsai,c Netanel Shpigel,d Hui Shao,e Danzhen Zhang,a Kanit Hantanasirisakul,a Fyodor Malchick,d,f Nina Balke,g De-en Jiang,b Patrice Simon,e Yury Gogotsia* a A. J. Drexel Nanomaterials Institute, and Department of Materials Science and Engineering, Drexel University, Philadelphia, Pennsylvania 19104, USA. b Department of Chemistry, University of California, Riverside, California 92521, USA. c Chemical Sciences Division, Oak Ridge National Laboratory, Oak Ridge, Tennessee 37831, USA. d Department of Chemistry, Bar-Ilan University, Ramat-Gan 52900, Israel e Materials Science Department - CIRIMAT, Université Toulouse III Paul Sabatier, 118 route de Narbonne, 31062 Toulouse, France. f Center for physical and chemical methods of research and analysis, al-Farabi Kazakh National University, 050040 Almaty, Kazakhstan. g Center for Nanophase Materials Sciences, Oak Ridge National Laboratory, Oak Ridge, Tennessee 37830, USA. 1 KEYWORDS: Titanium carbide MXene, water-in-salt electrolytes, desolvation-free cation insertion, abnormal electrochemical behavior ABSTRACT: Identifying and understanding charge storage mechanisms is important for advancing energy storage, especially when new materials and electrolytes are explored. Well- separated peaks in cyclic voltammograms (CVs) are considered key indicators of diffusion- controlled electrochemical processes with distinct Faradic charge transfer. Herein, we report on an electrochemical system with separated CV peaks, accompanied by surface-controlled partial charge transfer, in 2D Ti3C2Tx MXene in water-in-salt electrolytes. The process involves the insertion/desertion of desolvation-free cations, leading to an abrupt change of the interlayer spacing between MXene sheets. -
Processing & Characterization of Titanium Carbide & Titanium Oxide
International Journal of Scientific & Engineering Research, Volume 5, Issue 10, October-2014 1372 ISSN 2229-5518 Processing & Characterization of Titanium Carbide & Titanium Oxide Particulate Reinforced Aluminium Metal Matrix Composite for Aerospace Applications Mr. Azeem Dafedar, Prof. Rahul Bhandari, Dr. T. R. Vijayaram Abstract—In this research, a composite material containing Aluminium (Al), Titanium Oxide (TiO2), and Titanium Carbide (TiC) are mechanically manufactured by method of powder metallurgy which will be effective in aerospace application. The composites will be tested by using different percentage composition of materials. The process will start by mixing Aluminium matrix with Titanium Oxide and titanium Carbide reinforced with different percentage composition and the results will be compared with the values of pure Aluminium. The phase composition and morphology of material will be evaluated from hardness test. The microstructure of specimens will be revealed to investigate on continuous distribution of TiO2 and TiC in the metal matrix, which will be responsible for enhancement of tensile strength of the material. This feature is very likely and due to addition of Titanium Carbide (TiC) and Titanium Oxide (TiO2) in Aluminium (Al) matrix, there will be a good interface bonding of uniformly dispersed submicron size of reinforced materials. Good stiffness, high strength to weight ratio, good thermal properties which are very beneficial for aerospace applications are emphasized in the current paper. Index Terms— matrix, composites, sintering, micro structures, Brinell hardness —————————— —————————— 1 INTRODUCTION Since from last couple of years metal matrix composites processing technique for cold workability of the have drawn the attention of many scientists. They are having MMC’s has been developed with compaction process. -
Security Council Distr.: General 28 November 2001
U nited N ations S /2001/1120 Security Council Distr.: General 28 November 2001 Original: English Letter dated 27 November 2001 from the Deputy Permanent Representative of the United States of America to the United Nations addressed to the President of the Security Council I have the honour to draw your attention to the dual-use list issued on 27 November 2001 (see annex). I should be grateful if you would have the text of this letter and its annex circulated as a document of the Security Council. (Signed) Jam es B. Cunnigham Am bassador 01-66645 (E) 291101 S/2001/1120 Annex to the letter dated 27 Novem ber 2001 from the Deputy Permanent Representative of the United States of America to the United Nations addressed to the President of the Security Council Dual-use goods and technologies Contents Page List of dual-use goods and technologies - General Technology and General Software Notes ...................... 3 - Category 1. Materials............................................. 4 - Category 2. Materials Processing ................................... 20 - Category 3. Electronics ........................................... 39 - Category 4. Computers ........................................... 51 - Category 5. Part 1 Telecom m unications .............................. 62 - Category 5. Part 2 Inform ation Security .............................. 68 - Category 6. Sensors and Lasers ..................................... 72 - Category 7. Navigation and Avionics ................................ 96 -Category 8. Marine............................................. -
Mechanism of the High Temperature Oxidation of Titanium Carbide
Mechanism of the High Temperature Oxidation of Titanium Carbide V.B. Voitovich Institute for Problems of Materials Science, Kiev, Krzhyzhanovsky Str. 3, 252680, GSP. Ukraine ABSTRACT should resist high-temperature corrosion better than the simple Co-binder in the WC-based cermets 111. These High-temperature oxidation of titanium carbide in features have led to the intensive studies of high- the temperature range of 600-1200°C in air has been temperature oxidation of titanium carbide. studied by TGA, XRD, SEM, and AES methods. High-temperature oxidation of titanium carbide was Oxidation kinetics is multistage. The time intervals and studied by many investigators /3-17/. Nevertheless, temperature dependence of the rate constants of three oxidation mechanism has not been clearly studied up to parabolic and linear stages for oxidation at tempera- the present day. The oxidation mechanism was inter- tures 900-1200°C were determined. According to SEM preted as diffusion of oxygen through rutile (Ti02.x) and XRD data, a two-layer scale was formed at scale /7,9-ll/. The effect of titanium diffusion on temperatures exceeding 1000°C. The outer scale titanium carbide oxidation was not essentially consisted mainly of Ti02 (rutile). The inner scale considered. consisted of various titanium oxides. The effect of Oxidation of titanium carbide at temperatures above diffusion of both titanium and oxygen on the oxidation 900°C follows a parabolic kinetics /6-12/. It indicates processes was studied. The mechanism of the oxidation that diffusion processes control the oxidation rate. process is discussed. Parabolic oxidation was interpreted as a one-step process with an activation energy from 181.4 to 204.8 kJ/mole/9,11-13/. -
(12) United States Patent (10) Patent No.: US 6,482,476 B1 Liu (45) Date of Patent: Nov
USOO6482476B1 (12) United States Patent (10) Patent No.: US 6,482,476 B1 Liu (45) Date of Patent: Nov. 19, 2002 (54) LOW TEMPERATURE PLASMA ENHANCED 5,876,808 A * 3/1999 Hall et al. CVD CERAMIC COATING PROCESS FOR 6,110,571. A * 8/2000 Yaginuma et al. METAL, ALLOY AND CERAMIC MATERALS FOREIGN PATENT DOCUMENTS (75) Inventor: Shengzhong Frank Liu, 6084 Pond JP O7-216548 * 8/1995 plway, Mechanicsville, VA (US) OTHER PUBLICATIONS (73) Assignee: Shengzhong Frank Liu, Musher et al., J. Mater. Res., vol. 11, No. 4, Apr., 1996, pp. Mechanicsville, VA (US) 989-1OO1. (*) Notice: Subject to any disclaimer, the term of this * cited by examiner patent is extended or adjusted under 35 U.S.C. 154(b) by 0 days. Primary Examiner Timothy Meeks (21) Appl. No.: 09/465,405 (57) ABSTRACT (22) Filed: Dec. 16, 1999 A low temperature, high growth rate plasma enhanced O O chemical vapor deposition proceSS is demonstrated for Related U.S. Application Data ceramic coatings on metal, alloy and ceramic Substrates. The deposition process is carried out at low temperatures (<350 (63) Continuation-in-part of application No. 08/947.528, filed on degC.) to prevent the bulk Substrate properties from being Oct. 6, 1997, now abandoned. adversely affected. The Substrates are treated with gas Sur (51) Int. Cl. ................................................ C23C 16/30 face hardening processes before deposition. Bonding (52) U.S. Cl. ....................... 427,1535; 427/576; 427/577; strength (adhesion) between the coating and the Substrate is 427/585; 427/255.18; 427/255.31; 427/255.38; improved by combining Surface heat treating processes with 427/255.394 the coating processes. -
Titanium Carbide and Titanium Carbonitride Obtained by Chemical Vapor Deposition from Orgranometallic Precursor in the Range 450-800°C J
Titanium carbide and titanium carbonitride obtained by chemical vapor deposition from orgranometallic precursor in the range 450-800°C J. Slifirski, F. Teyssandier To cite this version: J. Slifirski, F. Teyssandier. Titanium carbide and titanium carbonitride obtained by chemical vapor deposition from orgranometallic precursor in the range 450-800°C. Journal de Physique IV Proceed- ings, EDP Sciences, 1993, 03 (C3), pp.C3-367-C3-374. 10.1051/jp4:1993350. jpa-00251407 HAL Id: jpa-00251407 https://hal.archives-ouvertes.fr/jpa-00251407 Submitted on 1 Jan 1993 HAL is a multi-disciplinary open access L’archive ouverte pluridisciplinaire HAL, est archive for the deposit and dissemination of sci- destinée au dépôt et à la diffusion de documents entific research documents, whether they are pub- scientifiques de niveau recherche, publiés ou non, lished or not. The documents may come from émanant des établissements d’enseignement et de teaching and research institutions in France or recherche français ou étrangers, des laboratoires abroad, or from public or private research centers. publics ou privés. JOURNAL DE PHYSIQUE IV Colloque C3, suppl6ment au Journal de Physique 11, Volume 3, aoilt 11993 Titanium carbide and titanium carbonitride obtained by chemical vapor deposition from organometallic precursor in the range 450-800 OC J. SLIFIRSKI and E TEYSSANDIER* Etablissement Techniaue Central de I%lrmement, 16 bis avenue Priacr de la C6te d'a 94114 Arcueil fedex, France Institut de Science et de G6nk des Matkriaux et Proc&i, Univem'td de Perpignan, 52 avenue de Villeneuve, 66860 Perpignan cedex, France Abstract: Titanium carbide coatings have been deposited on steel in a cold wall reactor from titanocene dichloride vaporized in a hydrogen carrier gas.