Advanced LPCVD Zno - Challenges in Application for Thin Film Solar Cells and Modules These`
Total Page:16
File Type:pdf, Size:1020Kb
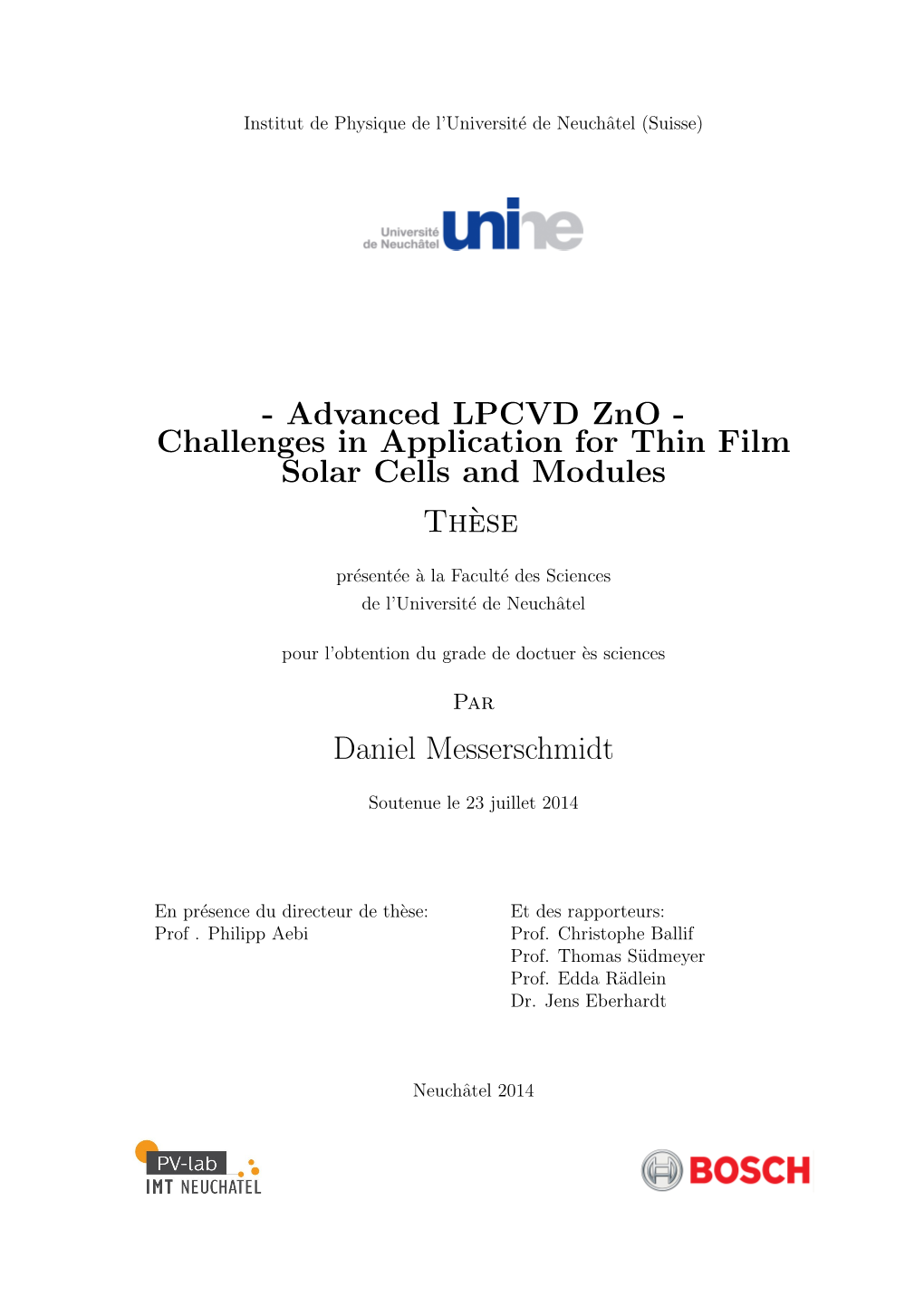
Load more
Recommended publications
-
28Th European Photovoltaic Solar Energy Conference and Exhibition
28th European Photovoltaic Solar Energy Conference and Exhibition Proceedings of the international Conference held in Paris, France 30 September - 04 October 2013 Edited by: A. MINE President of SER SOLER Paris, France A. JÄGER-WALDAU European Commission - DG JRC Ispra, Italy P. HELM WIP Munich, Germany More photos: Coordination of the Technical Programme: European Commission - DG Joint Research Centre Via E. Fermi 1 21020 Ispra (VA) Italy Institutional Support: The European Commission UNESCO – United Nations Educational, Scientific and Cultural Organization, Natural Sciences Sector WCRE – World Council for Renewable Energy Institutional PV Industry Partner for the Conference: SER – Syndicat des Energies Renouvelables, SOLER Supporting Organisations: EDF – Energies Nouvelles ESA – European Space Agency OME – Observatoire Méditerranéen de l'Energie REN21 – Renewable Energy Policy Network for the 21st Century European Photovoltaic Technology Platform ARE – Alliance for Rural Electrification Institutional PV Industry Cooperation: EPIA – European Photovoltaic Industry Association IPVEA – International Photovoltaic Equipment Association Supporting Associations: APVIA – Asian Photovoltaic Industry Association TPVIA – Taiwan Photovoltaic Industry Association EPIC – European Photonics Industry Consortium AIE – European Association of Electrical Contractors CABA – Continental Automated Buildings Association EU PVSEC realised by: WIP Sylvensteinstr. 2, 81369 München, Germany Tel: +49 89 720 12 735, Fax: +49 89 720 12 791 eMail: [email protected] www.photovoltaic-conference.com www.wip-munich.de Proceedings on DVD produced and published by: WIP Sylvensteinstr. 2, 81369 München, Germany Tel: +49 89 720 12 735, Fax: +49 89 720 12 791 eMail: [email protected] www.photovoltaic-conference.com www.wip-munich.de Legal notice Neither the European Commission, the Organiser or the Publisher nor any person acting on their behalf is responsible for the use which might be made of the following information. -
Copper Indium Gallium Selenide Thin Film Solar Cells Copper Indium Gallium Selenide Thin Film Solar Cells
ProvisionalChapter chapter 9 Copper Indium Gallium Selenide Thin Film Solar Cells Copper Indium Gallium Selenide Thin Film Solar Cells Yang Tang Yang Tang Additional information is available at the end of the chapter Additional information is available at the end of the chapter http://dx.doi.org/10.5772/65291 Abstract The solar energy as one of the new energy sources and a regenerated energy is abundant and pollution-free. Most photovoltaic devices (solar cells) sold in the market today are based on silicon wafers, the so-called "first generation" technology. The market at present is on the verge of switching to a "second generation" of thin film solar cell technology which offers prospects for a large reduction in material costs by eliminating the costs of the silicon wafers. Cadmium telluride (CdTe), amorphous silicon (a-Si) and copper indium gallium selenide (CIGS) are three thin film technologies which have achieved commercial production. This chapter gives the review of the CIGS solar cells regarding the heterostructures, materials, technology and research advances. It also states the key findings in our research and provides suggestions for future research. Keywords: Cu(In,Ga)(S,Se)2, solar cell, thin film, photon management, carrier collec- tion, nanostructure 1. Introduction Nowadays the development of the society and economy raises up the dependence upon the energy sources. However, the energy crisis and the environmental problems induced by using the fossil energy sources have attached much attention. A consensus about developing new energy as well as the reduction of the fossil energy consumption has been reached all over the world. -
Comparison of LPCVD and Sputter-Etched Zno Layers Applied As Front Electrodes in Tandem Thin-Film Silicon Solar Cells
Comparison of LPCVD and sputter-etched ZnO layers applied as front electrodes in tandem thin-film silicon solar cells Etienne Moulin1, Karsten Bittkau2, Michael Ghosh2, Grégory Bugnon1, Michael Stuckelberger1, Matthias Meier2, Franz-Josef Haug1, Jürgen Hüpkes2, Christophe Ballif1 1Ecole Polytechnique Fédérale de Lausanne (EPFL), Institute of Microengineering (IMT), Photovoltaics and Thin-Film Electronics Laboratory, rue de la Maladière 71b, 2002 Neuchâtel, Switzerland 2IEK5-Photovoltaik, Forschungszentrum Jülich GmbH, 52425 Jülich, Germany Abstract: Aluminum-doped zinc oxide (ZnO:Al) layers deposited by sputtering and boron-doped zinc oxide (ZnO:B) layers deposited by low-pressure chemical vapor deposition (LPCVD) are well-established materials for front electrodes in thin-film silicon solar cells. In this study, both types of front electrodes are evaluated with respect to their inherent properties and their surface textures in micromorph tandem solar cells in the superstrate configuration. The silicon layer stack investigated here consists of a 220-nm-thick amorphous silicon top cell, a 40-nm-thick intermediate reflector and a 1.1-µm-thick microcrystalline silicon bottom cell; for this specific silicon layer stack, the LPCVD ZnO:B provides higher power conversion efficiency than its sputtered ZnO:Al counterpart. The growth-friendly surface topography of ZnO:Al yields better electrical performance. However, the optical performance is the limiting factor. Detailed analysis of the experimental results allows us to clearly distinguish the origin of the observed differences. Several possible upgrades are discussed to further improve performance of cells grown on sputter-etched ZnO:Al. 1. Introduction: The thin-film silicon (TF-Si) solar technology offers many advantages, including low production costs (<0.5 $/Wp [1]), the abundance and non-toxicity of the base materials and low material usage (thicknesses in the µm range). -
Laser Welding of Silicon Foils for Thin-Film Solar Cell Manufacturing
Laser Welding of Silicon Foils for Thin-Film Solar Cell Manufacturing Laserschweißen von Siliziumfolien zur Herstellung von Dünnschicht-Solarzellen Der Technischen Fakultät der Friedrich-Alexander-Universität Erlangen-Nürnberg zur Erlangung des Doktorgrades Dr.-Ing. vorgelegt von Thomas Maik Heßmann aus Zschopau Als Dissertation genehmigt von der Technischen Fakultät der Friedrich-Alexander-Universität Erlangen-Nürnberg Tag der mündlichen Prüfung: 30.09.2014 Vorsitzende des Promotionsorgangs: Prof. Dr.-Ing. habil. Marion Merklein Gutachter: Prof. Dr. techn. Christoph J. Brabec Prof. Dr.-Ing. Rolf Brendel Abstract Thin-film solar module manufacturing is one of the most promising recent developments in photovoltaic research and has the potential to reduce production costs. As the necessity for competitive prices on the world market increases and manufacturers endeavor to bring down the cost of solar modules, thin-film technology is becoming more and more attractive. In this work a special technique was investigated which makes solar cell manufacturing more compatible with an industrial roll-to-roll process. This technique allows the creation of the first monocrystalline band substrate by welding several monocrystalline silicon wafers together, so that the size restriction of float-zone grown wafers can be overcome. Currently the size is 8 inches in diameter. Float-zone grown material is well suited as feedstock for high efficiency solar cells and it has also been very intensively studied in the past. This makes it the perfect feedstock material for thin-film solar modules. Unfortunately this material is quite expensive and therefore it should only serve as feedstock to generate the band substrate. After this step the necessary silicon layers to produce solar cells are grown epitaxially on top of the band substrate using chemical vapor deposition. -
Characterization of Thin Film Modules
Characterisation of Performance of Thin-film Photovoltaic Technologies Report IEA-PVPS T13-02:2014 Outdoor test facility for the comparison of energy yield measurements of different photovoltaic module technologies. Courtesy of TÜV Rheinland, Energie und Umwelt GmbH, Cologne, Germany. INTERNATIONAL ENERGY AGENCY PHOTOVOLTAIC POWER SYSTEMS PROGRAMME Characterisation of Performance of Thin-film Photovoltaic Technologies IEA PVPS Task 13, Subtask 3.1 Final Report IEA-PVPS T13-02:2014 May 2014 ISBN 978-3-906042-17-6 Authors: Timothy J Silverman National Renewable Energy Laboratory, Golden, CO, USA Ulrike Jahn TÜV Rheinland Energie und Umwelt GmbH, Cologne, Germany Gabi Friesen and Mauro Pravettoni SUPSI ISAAC, Canobbio, Switzerland Marco Apolloni TEL Solar, Trübbach, Switzerland A Louwen and WGJHM van Sark Utrecht University, Copernicus Institute of Sustainable Development, Utrecht, the Netherlands Markus Schweiger TÜV Rheinland Energie und Umwelt GmbH, Cologne, Germany G. Belluardo, J. Wagner, A. Tetzlaff, P. Ingenhoven, D. Moser EURAC Research Institute for Renewable Energy, Bolzano, Italy iii Further contributions and data from: Anne Gerd Imenes, Teknova, Norway Lionel Sicot, Guillaume Razongles, CEA INES, France Tom Betts, CREST, United Kingdom George E. Georghiou, University of Cyprus Mike van Iseghem, Didier Binesti, EDF R&D, France This report is supported by: Austrian Federal Ministry for Transport, Innovation and Technology (BMVIT) under FFG contract No. 828105 German Federal Ministry for Economic Affairs and Energy under Contract No.0325194A (BMWi) Swiss Federal Office of Energy (SFOE) “FLASH”, a Perspectief programme funded by Technology Foundation STW (http://stw.nl/en/) under project number 12172 and U.S. Department of Energy under Contract No. DE-AC36-08-GO28308 with the National Renewable Energy Laboratory (NREL) iv Table of Contents 1 Foreword .......................................................................................................................... -
Strategies for Doped Nanocrystalline Silicon Integration in Silicon Heterojunction Solar Cells Johannes P
1132 IEEE JOURNAL OF PHOTOVOLTAICS, VOL. 6, NO. 5, SEPTEMBER 2016 Strategies for Doped Nanocrystalline Silicon Integration in Silicon Heterojunction Solar Cells Johannes P. Seif, Antoine Descoeudres, Gizem Nogay, Simon Hanni,¨ Silvia Martin de Nicolas, Niels Holm, Jonas Geissbuhler,¨ A¨ıcha Hessler-Wyser, Martial Duchamp, Rafal E. Dunin-Borkowski, Martin Ledinsky, Stefaan De Wolf, and Christophe Ballif Abstract—Carrier collection in silicon heterojunction (SHJ) so- (PECVD) features nanometer-sized silicon crystals embedded lar cells is usually achieved by doped amorphous silicon layers of in an amorphous silicon (a-Si:H) matrix. This material has al- a few nanometers, deposited at opposite sides of the crystalline sil- ready been studied for several decades and found its way into icon wafer. These layers are often defect-rich, resulting in modest doping efficiencies, parasitic optical absorption when applied at the several important applications including photovoltaic devices front of solar cells, and high contact resistivities with the adjacent [1]–[8], thin-film transistors [9], and microelectromechanical transparent electrodes. Their substitution by equally thin doped systems [10]. Significant effort was put on the experimental nanocrystalline silicon layers has often been argued to resolve [11]–[16] and theoretical [17] investigation of its growth pro- these drawbacks. However, low-temperature deposition of highly cess [4], [18], as well as its electrical [19]–[21] and optical crystalline doped layers of such thickness on amorphous surfaces demands sophisticated deposition engineering. In this paper, we properties [2], [15]. review and discuss different strategies to facilitate the nucleation In the case of solar cells, μc-Si:H was for a long time mainly of nanocrystalline silicon layers and assess their compatibility with used as absorbing material of the bottom cell in so-called mi- SHJ solar cell fabrication. -
Instructions and Formatting Rules for Authors of Majlesi Journal of Electrical Engineering
Journal of Communications Technology, Electronics and Computer Science, Issue 20, 2018 ISSN 2457-905X An Evolution Review in Solar Photovoltaic Materials Dr. Sandeep Gupta Department of Electrical Engineering, JECRC University, Jaipur, Rajasthan 303905, INDIA [email protected] Abstract—The sensitivity towards the environmental the local climate by reducing heat is land effect. Solar energy concerns among the humans is picking up the pace. An energy as a non-conventional energy source is a very good option source, which meets the development goals without for not only bulk electricity production but also for the off- compromising with this source for the next generation, is the grid purposes. Rural population contributes to about 80% of need of the current time. Renewable energy sources are the only the world’s population. The use of off-grid plants is very solution of this problem. Solar energy is the most abundant form of renewable energy. Since the last decade, the solar useful in the electrification of the rural areas. They are also energy generation costs have shown a sharp decline. There are helpful in avoiding the long-distance transmission costs [2, many reasons include use of better materials, improved 3]. technologies and increased efficiencies of the solar panels. This This paper presents the overall evolution review in solar paper discusses about various solar photovoltaic (SPV) photovoltaic materials. The first half of the paper mainly materials being used throughout the globe. A brief description focused on the structure, efficiencies and manufacturing of both, the fully developed and under-developing PV material processes of the conventionally used solar cells. -
Photovoltaic Materials – Present Efficiencies and Future Challenges
RESEARCH ◥ losses. In contrast, thin-film single-crystalline REVIEW SUMMARY GaAs cells (28.8%) show only minimal recom- bination losses but can be improved by better light management. Polycrystalline CdTe thin- PHOTOVOLTAICS film cells (21.5%) offer excellent light absorption but have relatively high recombination losses; perovskite cells (21.0%) and Cu(In,Ga)(Se,S)2 Photovoltaic materials: Present (CIGS) cells (21.7%) have poorer light manage- ment, although CIGS displays higher electrical efficiencies and future challenges quality. Aside from these five materials (Si, GaAs, CdTe, Albert Polman,* Mark Knight, Erik C. Garnett, Bruno Ehrler, Wim C. Sinke CIGS, perovskite) with efficiencies of >20%, a broad range of other thin-film materials have been developed with efficiencies of 10 to 12%: BACKGROUND: Photovoltaics, which directly tries and illuminated under the standard AM1.5 micro/nanocrystalline and amorphous Si, Cu convert solar energy into electricity, offer a solar spectrum, and compare these to the fun- ◥ (Zn,Sn)(Se,S)2 (CZTS), dye- practical and sustainable solution to the chal- damental limits based on the S-Q model. Cells ON OUR WEBSITE sensitized TiO , organic J 2 lenge of meeting the increasing global energy that show a short-circuit current ( sc)lower polymer materials, and demand. According to the Shockley-Queisser than the S-Q limit suffer from incomplete light Read the full article at http://dx.doi. quantum dot solids. So far, (S-Q) detailed-balance model, the limiting absorption or incomplete collection of gener- org/10.1126/ cell designs based on these photovoltaic energy conversion efficiency for ated carriers, whereas a reduced open-circuit science.aad4424 materials all suffer from V FF ................................................. -
Pvps Annual Report 2012
P HOTOVOLTAIC P OWER S YSTEMS P ROGRAMME ANNUAL REPORT 2012 2 COVER PHOTO AND ABOVE: Solar façade at an office building in Sursee, LU, Switzerland. An 18 kWp solar façade with 180 m2 over all generates about 12 600 kWh per year. This PV system was built with Megasol mono-crystalline modules and Kostal inverters. Architect and Owner: BF berger + frank ag, Sursee, Switzerland. Planned and installed by: Schürch-Egli AG, Sempach, Switzerland. Photo by: BF berger + frank ag. CHAIRMAN’S MESSAGE 3 CHAIRMAN’S MESSAGE I am pleased to present the IEA Photovoltaic Power Systems Programme’s 2012 annual report. 2012 has been a very dynamic and challenging year for the photovoltaic sector: The rapid cost reduction of photovoltaic power systems has continued throughout the year, leading to the emergence of new markets and market models on the one hand. The market has continued to grow but at a slower pace than in the years before. At the end of 2012, about 100 GW of photovoltaics were installed worldwide, with contributions up to 6 % of the electricity supply of some countries. The photovoltaic industry, on the other hand, has had the most difficult time of its young history, leading to a marked consolidation of the sector. As a leading international network of expertise, IEA PVPS has the mission to cooperate on a global level in this rapidly evolving technology area. Working on both technical and non-technical issues, IEA PVPS undertakes key collaborative projects related to technology and performance assessment, cost reduction, best practice in various applications, rapid deployment of photovoltaics and key issues such as grid integration and environmental aspects. -
Solar Cell Efficiency Tables (Version
PROGRESS IN PHOTOVOLTAICS: RESEARCH AND APPLICATIONS Prog. Photovolt: Res. Appl. 2014; 22:701–710 Published online in Wiley Online Library (wileyonlinelibrary.com). DOI: 10.1002/pip.2525 ACCELERATED PUBLICATION Solar cell efficiency tables (version 44) Martin A. Green1*, Keith Emery2, Yoshihiro Hishikawa3, Wilhelm Warta4 and Ewan D. Dunlop5 1 Australian Centre for Advanced Photovoltaics, University of New South Wales, Sydney, 2052, Australia 2 National Renewable Energy Laboratory, 15013 Denver West Parkway, Golden, CO, 80401, USA 3 Research Center for Photovoltaic Technologies (RCPVT), National Institute of Advanced Industrial Science and Technology (AIST), Central 2, Umezono 1-1-1, Tsukuba, Ibaraki, 305-8568, JAPAN 4 Department of Materials and Technology, Solar Cells, Fraunhofer Institute for Solar Energy Systems, Heidenhofstr. 2; D-79110 Freiburg, Germany 5 Joint Research Centre, Renewable Energy Unit, Institute for Energy, European Commission, Via E. Fermi 2749, IT-21027 Ispra (VA), Italy ABSTRACT Consolidated tables showing an extensive listing of the highest independently confirmed efficiencies for solar cells and modules are presented. Guidelines for inclusion of results into these tables are outlined and new entries since January 2014 are reviewed. Copyright © 2014 John Wiley & Sons, Ltd. KEYWORDS solar cell efficiency; photovoltaic efficiency; energy conversion efficiency *Correspondence Martin A. Green, School of Photovoltaic and Renewable Energy Engineering, University of New South Wales, Sydney, 2052, Australia. E-mail: [email protected] -
Pvps Annual Report 2013
P HOTOVOLTAIC P OWER S YSTEMS P ROGRAMME ANNUAL REPORT 2013 2 COVER PHOTO AND ABOVE: Multicolored transparent photovoltaic façade at the SwissTech Convention Center, Swiss Federal Institute of Technology in Lausanne EPFL, Switzerland. This 300 m2 PV installation is the world’s first multicolored Dye Solar Cell Façade, composed of “Grätzel Cells,” which encompasses a length of 36 meters and a maximum height of 15 meters. Annual production is estimated at 2,000 kWh. PV Installation Planned and Produced by: Solaronix SA, Aubonne, Switzerland; with the support of Romande Energie. Architects: Richter · Dahl Rocha & Associés architectes SA, Lausanne, Switzerland. General Contractor: HRS Real Estate SA, Crissier, Switzerland. Photo: © IEA PVPS / DanielForster.com CHAIRMAN’S MESSAGE 3 CHAIRMAN’S MESSAGE The IEA Photovoltaic Power Systems Programme IEA PVPS is pleased to present its 2013 annual report. 2013 has been a turning point in many aspects for the global development of photovoltaics: On the one hand, the rapid cost reduction of photovoltaic power systems of the last years has continued throughout the year, but at a slower pace. At the same time market support has become more constrained in a number of countries, namely in Europe. On the other hand, markets in Asia and the USA have continued to grow vigorously. Together with the increasing cost-competitiveness of photovoltaics, the worldwide market has reached a new maximum with close to 38 GW installed in 2013, well above the roughly 30 GW of 2012. Asia has seen a larger market than Europe for the first time. Close to 140 GW of photovoltaic systems were installed worldwide at the end of 2013, enough to cover roughly 1 % of the global electricity supply. -
Phd Thesis | Asiel Corpus 2015
Department of Electronic and Electrical Engineering Thesis submitted to obtain the Degree of Doctor of Philosophy Influence of the p-type layer on the performance and stability of thin film silicon solar cells Asiel Neftalí Corpus Mendoza March 2017 Supervisor: Prof. M. M. De Souza Abstract The poor lateral conductance of amorphous silicon necessitates the use of a contact covering the entire surface of thin film silicon solar cells to minimise the resistance. This contact must be highly conductive, as well as transparent to allow absorption of light in the inner layers. In recent years this has paved way for transparent conducting oxides (TCOs) to be used in solar technology. However, the absence of a p-type TCO complicates the fabrication of an Ohmic contact to a-Si:H(p). Moreover, the difference in bandgap between the two materials results in a Schottky interface which has not been investigated comprehensively in terms of on-state/optical performance and stability before. This thesis describes the physics of thin film silicon solar cells and their Schottky interface with zinc oxide (ZnO). Here, current-voltage-temperature (I-V-T) measurements and computer simulations are used in order to evaluate the Schottky barrier height of ZnO/a- Si:H(p) and ZnO/μc-Si:H(p) heterojunctions. It is observed that a high doping concentration of the p-layer can reduce the effective Schottky barrier height by increasing the tunnelling transport mechanism at the interface. The same heterojunctions are also tested in ZnO/p- layer/a-Si:H(i)/a-Si:H(n)/ZnO/Ag solar cells.