Hinton Lecture Bob Dudley BP CEO
Total Page:16
File Type:pdf, Size:1020Kb
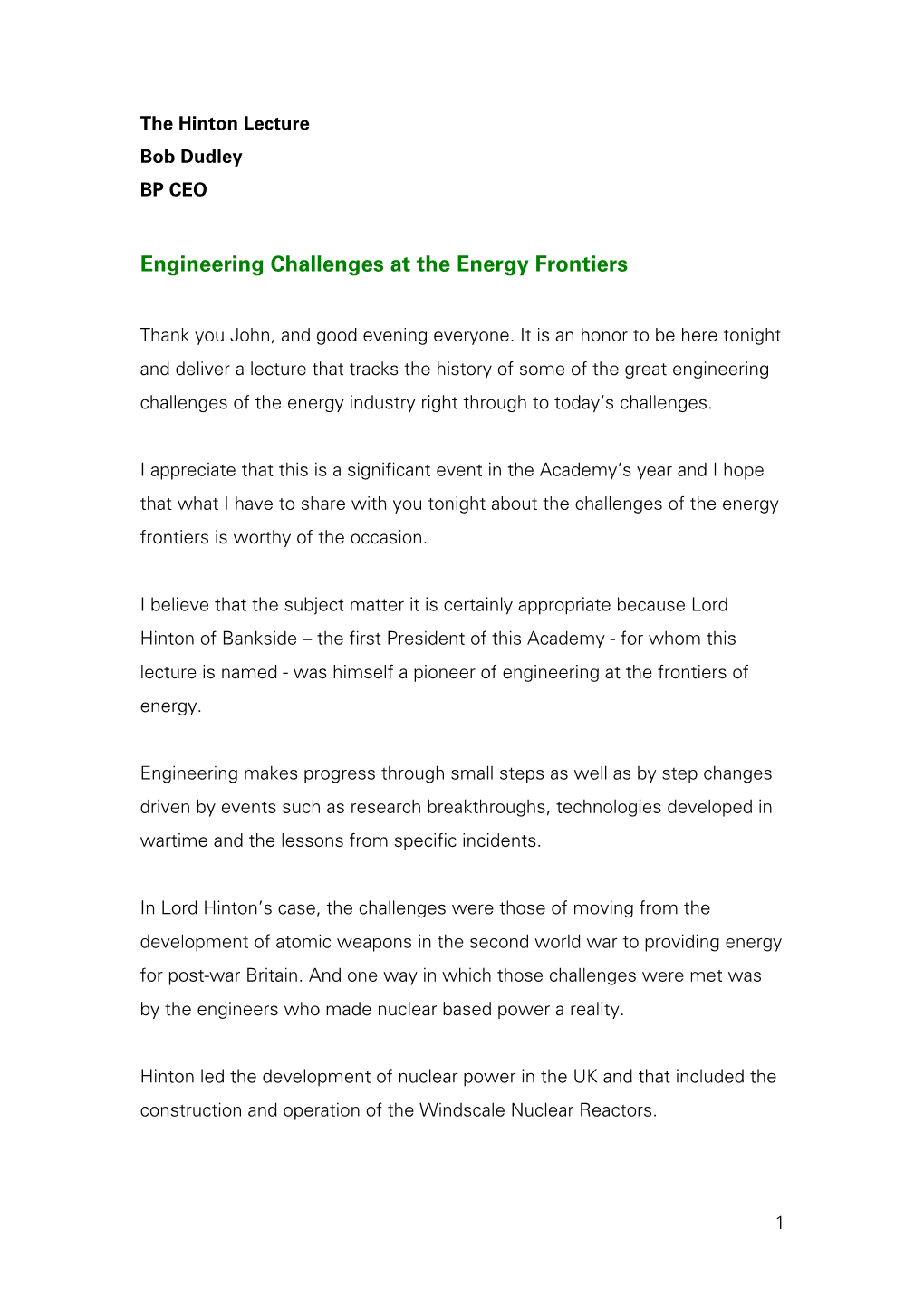
Load more
Recommended publications
-
United States District Court Southern District of Texas Houston Division
Case 4:10-md-02185 Document 113 Filed in TXSD on 02/14/11 Page 1 of 182 UNITED STATES DISTRICT COURT SOUTHERN DISTRICT OF TEXAS HOUSTON DIVISION In re BP plc Securities Litigation No. 4:10-md-02185 Honorable Keith P. Ellison LEAD PLAINTIFFS NEW YORK AND OHIO’S CONSOLIDATED CLASS ACTION COMPLAINT FOR ALL PURCHASERS OF BP SECURITIES FROM JANUARY 16, 2007 THROUGH MAY 28, 2010 Case 4:10-md-02185 Document 113 Filed in TXSD on 02/14/11 Page 2 of 182 TABLE OF CONTENTS Page I. INTRODUCTION ...............................................................................................................2 II. JURISDICTION AND VENUE ........................................................................................11 III. THE PARTIES ..................................................................................................................11 A. Plaintiffs .................................................................................................................11 B. Defendants .............................................................................................................12 C. Non-Party ...............................................................................................................17 IV. BACKGROUND ...............................................................................................................17 A. BP’s Relevant Operations ......................................................................................17 B. BP’s Process Safety Controls Were Deficient Prior to the Class Period ...............18 -
2021 Annual General Meeting and Proxy Statement 2020 Annual Report
2020 Annual Report and Proxyand Statement 2021 Annual General Meeting Meeting General Annual 2021 Transocean Ltd. • 2021 ANNUAL GENERAL MEETING AND PROXY STATEMENT • 2020 ANNUAL REPORT CONTENTS LETTER TO SHAREHOLDERS NOTICE OF 2021 ANNUAL GENERAL MEETING AND PROXY STATEMENT COMPENSATION REPORT 2020 ANNUAL REPORT TO SHAREHOLDERS ABOUT TRANSOCEAN LTD. Transocean is a leading international provider of offshore contract drilling services for oil and gas wells. The company specializes in technically demanding sectors of the global offshore drilling business with a particular focus on ultra-deepwater and harsh environment drilling services, and operates one of the most versatile offshore drilling fleets in the world. Transocean owns or has partial ownership interests in, and operates a fleet of 37 mobile offshore drilling units consisting of 27 ultra-deepwater floaters and 10 harsh environment floaters. In addition, Transocean is constructing two ultra-deepwater drillships. Our shares are traded on the New York Stock Exchange under the symbol RIG. OUR GLOBAL MARKET PRESENCE Ultra-Deepwater 27 Harsh Environment 10 The symbols in the map above represent the company’s global market presence as of the February 12, 2021 Fleet Status Report. ABOUT THE COVER The front cover features two of our crewmembers onboard the Deepwater Conqueror in the Gulf of Mexico and was taken prior to the COVID-19 pandemic. During the pandemic, our priorities remain keeping our employees, customers, contractors and their families healthy and safe, and delivering incident-free operations to our customers worldwide. FORWARD-LOOKING STATEMENTS Any statements included in this Proxy Statement and 2020 Annual Report that are not historical facts, including, without limitation, statements regarding future market trends and results of operations are forward-looking statements within the meaning of applicable securities law. -
Transocean Ltd. Provides Quarterly Fleet Status Report
Transocean Ltd. Provides Quarterly Fleet Status Report STEINHAUSEN, Switzerland—February 12, 2021—Transocean Ltd. (NYSE: RIG) today issued a quarterly Fleet Status Report that provides the current status of, and contract information for, the company’s fleet of offshore drilling rigs. As of February 12, the company’s total backlog is approximately $7.8 billion. This quarter’s report includes the following updates: Deepwater Corcovado – Customer exercised a 680-day option in Brazil; Deepwater Mykonos – Customer exercised a 815-day option in Brazil; Development Driller III – Awarded a one-well contract extension in Trinidad; Development Driller III – Awarded a one-well contract, plus a one-well option in Trinidad; Transocean Norge – Awarded a one-well contract in Norway; Transocean Barents – Awarded a three-well contract in Norway; Paul B Loyd, Jr. – Awarded a 78-day contract extension in the U.K. North Sea; Dhirubhai Deepwater KG1– Customer exercised a seven-well option in India; and Deepwater Nautilus – Customer provided notice of termination of its drilling contract in Malaysia. Additionally, the company has retired the Leiv Eiriksson. The rig is classified as held for sale. The report can be accessed on the company’s website: www.deepwater.com. About Transocean Transocean is a leading international provider of offshore contract drilling services for oil and gas wells. The company specializes in technically demanding sectors of the global offshore drilling business with a particular focus on ultra-deepwater and harsh environment drilling services, and operates one of the most versatile offshore drilling fleets in the world. Transocean owns or has partial ownership interests in, and operates a fleet of, 37 mobile offshore drilling units consisting of 27 ultra-deepwater floaters and 10 harsh environment floaters. -
Dr. Walter Cruickshank Acting Director Bureau of Ocean Energy Management 1849 C Street, NW Washington, D.C. 20240 March 9, 2018
Dr. Walter Cruickshank Acting Director Bureau of Ocean Energy Management 1849 C Street, NW Washington, D.C. 20240 March 9, 2018 Re: Comments on the 2019 – 2024 National Outer Continental Shelf Oil and Gas Leasing Draft Proposed Program [BOEM-2017-0074] – Opposition to New Leasing Dear Dr. Cruickshank: On behalf of Heal the Bay, an environmental nonprofit dedicated to making the coastal waters and watersheds of greater Los Angeles safe, healthy, and clean, we are strongly opposed to the expansion of oil and gas activities in the Pacific and other regions listed in the Draft Proposed 2019-2024 National Outer Continental Shelf Oil and Gas Leasing Program (Draft Proposed Program). Heal the Bay respectfully urges the Bureau of Ocean Energy Management to abandon its wasteful scoping and planning efforts for the Draft Proposed Program and related Programmatic Environmental Impact Statement (PEIS). We are opposed to new leasing in the Pacific (2 lease sales each for Northern California, Central California, and Southern California, and 1 for Washington/Oregon), the Atlantic (3 lease sales each for the Mid- and South Atlantic, 2 for the North Atlantic, and 1 for the Straits of Florida), the Gulf of Mexico (2 lease sales), and all waters off Alaska (19 lease sales) and urge you to offer no new oil and gas leases in federal waters. The Administration’s proposal to expand offshore drilling to nearly all U.S. waters, encompassing over 90% of total Outer Continental Shelf acreage – the largest number of potential offshore lease sales ever proposed – is shortsighted and reckless. Offshore oil and gas drilling is inherently dangerous, and threatens the nation’s ocean economy and environment. -
Oversight Hearing Committee on Natural Resources U.S
FINAL REPORT OF THE PRESIDENT’S NATIONAL COMMISSION ON THE BP DEEPWATER HORIZON OIL SPILL AND OFFSHORE DRILLING OVERSIGHT HEARING BEFORE THE COMMITTEE ON NATURAL RESOURCES U.S. HOUSE OF REPRESENTATIVES ONE HUNDRED TWELFTH CONGRESS FIRST SESSION Wednesday, January 26, 2011 Serial No. 112-1 Printed for the use of the Committee on Natural Resources ( Available via the World Wide Web: http://www.gpoaccess.gov/congress/index.html or Committee address: http://naturalresources.house.gov U.S. GOVERNMENT PRINTING OFFICE 63-876 PDF WASHINGTON : 2011 For sale by the Superintendent of Documents, U.S. Government Printing Office Internet: bookstore.gpo.gov Phone: toll free (866) 512–1800; DC area (202) 512–1800 Fax: (202) 512–2104 Mail: Stop IDCC, Washington, DC 20402–0001 VerDate Nov 24 2008 13:18 Mar 14, 2011 Jkt 000000 PO 00000 Frm 00001 Fmt 5011 Sfmt 5011 L:\DOCS\63876.TXT Hresour1 PsN: KATHY COMMITTEE ON NATURAL RESOURCES DOC HASTINGS, WA, Chairman EDWARD J. MARKEY, MA, Ranking Democrat Member Don Young, AK Dale E. Kildee, MI John J. Duncan, Jr., TN Peter A. DeFazio, OR Louie Gohmert, TX Eni F.H. Faleomavaega, AS Rob Bishop, UT Frank Pallone, Jr., NJ Doug Lamborn, CO Grace F. Napolitano, CA Robert J. Wittman, VA Rush D. Holt, NJ Paul C. Broun, GA Rau´ l M. Grijalva, AZ John Fleming, LA Madeleine Z. Bordallo, GU Mike Coffman, CO Jim Costa, CA Tom McClintock, CA Dan Boren, OK Glenn Thompson, PA Gregorio Kilili Camacho Sablan, CNMI Jeff Denham, CA Martin Heinrich, NM Dan Benishek, MI Ben Ray Luja´n, NM David Rivera, FL Donna M. -
Esso Offshore Projects
Esso offshore projects Esso Australia, a subsidiary of ExxonMobil The drilling program is expected to start in the Australia, is undertaking a program of work across second half of 2018 and continue for some of its offshore assets, including those owned approximately 60 days, using the Ocean jointly by the Gippsland Basin Joint Venture and Monarch mobile offshore drilling unit the Kipper Unit Joint Venture, in 2018 and 2019. (MODU). This program forms part of Esso’s ongoing The exploration wells will determine the extent of investment in exploring for domestic gas any gas reserves contained within the field and development opportunities to ensure that we can the potential for development of much needed continue to meet Australia’s energy needs. new gas supplies from the Gippsland Basin, which has been producing for more than 45 years. This fact sheet provides high level details about the projects, regulatory requirements and The Baldfish and Hairtail wells are located outside consultation that is occurring to facilitate the Bass Strait "Area to be Avoided” as defined on information sharing and stakeholder engagement. marine chart AUS357 and temporary fairways have been established to protect the rig and other Projects marine users (see figure below). VIC/P70 drilling program Temporary petroleum safety zones will also be in Esso is undertaking an exploration drilling program place for the duration of the drilling program, to in the VIC/P70 block, approximately 90km off the further provide protection. (VIC/P70 well East Gippsland Victorian coast. The program will coordinates: Baldfish Latitude 38° 36’ south, involve drilling two exploration wells, known as Longitude 148° 35’ east / Hairtail Latitude 38° 36’ Baldfish and Hairtail. -
Deepwater Horizon Oil Spill: Recent Activities and Ongoing Developments
Deepwater Horizon Oil Spill: Recent Activities and Ongoing Developments Updated April 17, 2015 Congressional Research Service https://crsreports.congress.gov R42942 Deepwater Horizon Oil Spill: Recent Activities and Ongoing Developments Summary In the wake of the explosion of the Deepwater Horizon offshore drilling rig in the Gulf of Mexico on April 20, 2010, federal agencies, state and local government agencies, and responsible parties faced an unprecedented challenge. An oil discharge continued for 87 days, resulting in the largest ever oil spill in U.S. waters. Led by the U.S. Coast Guard, response activities were extensive for several years but have diminished substantially: At the height of operations (summer of 2010), response personnel numbered over 47,000. As of April 2015, 30 response personnel, including federal officials and civilians, are working on activities related to the Deepwater Horizon incident. In February 2015, a Coast Guard memorandum announced that in March 2015, the Gulf Coast Incident Management Team (GCIMT) would “transition from Phase III (Operations) ... and reconstitute as a Phase IV Documentation Team.” As part of that transition, Coast Guard field unit commanders would respond to reports of oil spills in their respective areas of responsibility. As one of the responsible parties, BP has spent over $14 billion in cleanup operations. In addition, BP has paid over $15 billion to the federal government, state and local governments, and private parties for economic claims and other expenses, including reimbursements for response costs related to the oil spill. BP and other responsible parties have agreed to civil and/or criminal settlements with the Department of Justice (DOJ). -
Offshore Drilling: Putting the Nation’S Coastline at Risk
APRIL 2020 FS: 20-04-B FACT SHEET OFFSHORE DRILLING: PUTTING THE NATION’S COASTLINE AT RISK America’s oceans sustain life, both in the water and on land. They are home to a vast array of marine life, provide a vital food source for millions of people, and support a thriving way of life for coastal communities dependent on clean and healthy waters and beaches. The expansion of offshore drilling in U.S. waters would threaten countless marine species and harm tens of millions of Americans. As we saw in 2010 when the BP offshore drilling rig Deepwater Horizon spilled as much as 4.9 million barrels of oil into the Gulf of Mexico, catastrophic oil spills devastate coastal communities and ocean and coastal wildlife.1 The Deepwater Horizon calamity killed 11 workers, injured 17 others, pushed critically endangered marine species toward extinction, and cost local economies billions of dollars.2 © Randall Vermillion/123RF For more information, please contact: www.nrdc.org Jacob Eisenberg, [email protected] www.facebook.com/NRDC.org Alex Adams, [email protected] www.twitter.com/NRDC © USCG However, it’s not just huge oil spills that are harmful; the offshore oil and gas industry frequently spills smaller amounts of oil into the Gulf, risking human health and damaging the marine environment.3 Moreover, offshore drilling requires significant onshore infrastructure, such as pipelines and refineries, that change the character of seaside communities, hasten the loss of wetlands, and heighten the impacts of storm surge and sea level rise.4 Additionally, continuing to open new areas to offshore oil drilling would lock America into a future of dirty fuels. -
Check out This Factsheet on the Project
The GETFACTS ABOUT PLAINSPIPELINE’S NEW THREAT TO COASTAL CALIFORNIA Plains All American Pipeline caused California’s worst coastal oil spill in 25 years – the Refugio Oil Spill of 2015 – and now it wants a second chance to spill again. anta Barbara County is processing Plains’ application to build another coastal oil pipeline that would restart Sdrilling from six decrepit offshore oil platforms in the Santa Barbara Channel. Houston-based Plains was criminally negligent in allowing its previous coastal oil pipeline to become corroded and fail, coating Santa Barbara area beaches in crude and killing hundreds of birds and marine mammals. It doesn’t deserve another opportunity to kill threatened wildlife, poison our communities and wreck the climate. THE PROJECT • Plains All American Pipeline is proposing to build more than 123 miles of new oil pipeline through Santa Barbara (73 miles), San Luis Obispo (37 miles) and Kern counties (14 miles), transporting heavy crude pumped from offshore drilling platforms to onshore processing facilities. Plains also proposes to abandon in place about 123 miles of its old failed oil pipelines. • The new pipeline will mostly follow the same route as the old broken pipeline – which was built based on environmental studies done in the late ‘80s – in a rapidly changing coastal zone that is now being affected by coastal erosion, sea level rise and other impacts from climate change. HISTORY OF VIOLATIONS • Investigators responding to a massive coastal oil spill near Refugio State Beach in 2015 found the source, Plains’ Pipeline 901, to be severely corroded and poorly maintained. In September 2018, a Santa Barbara jury found Plains guilty of a felony for failing to properly maintain its pipeline and eight misdemeanor charges for a delay in reporting the spill and for its deadly impact on protected wildlife. -
Environmental, Health, and Safety Guidelines for Offshore Oil and Gas Development
ENVIRONMENTAL, HEALTH, AND SAFETY GUIDELINES OFFSHORE OIL AND GAS DEVELOPMENT June 5, 2015 ENVIRONMENTAL, HEALTH, AND SAFETY GUIDELINES FOR OFFSHORE OIL AND GAS DEVELOPMENT INTRODUCTION 1. The Environmental, Health, and Safety (EHS) Guidelines are technical reference documents with general and industry-specific examples of Good International Industry Practice (GIIP).1 When one or more members of the World Bank Group are involved in a project, these EHS Guidelines are applied as required by their respective policies and standards. These industry sector EHS guidelines are designed to be used together with the General EHS Guidelines document, which provides guidance to users on common EHS issues potentially applicable to all industry sectors. For complex projects, use of multiple industry sector guidelines may be necessary. A complete list of industry sector guidelines can be found at: www.ifc.org/ehsguidelines. 2. The EHS Guidelines contain the performance levels and measures that are generally considered to be achievable in new facilities by existing technology at reasonable costs. Application of the EHS Guidelines to existing facilities may involve the establishment of site-specific targets, with an appropriate timetable for achieving them. 3. The applicability of the EHS Guidelines should be tailored to the hazards and risks established for each project on the basis of the results of an environmental assessment in which site-specific variables, such as host country context, assimilative capacity of the environment, and other project factors, are taken into account. The applicability of specific technical recommendations should be based on the professional opinion of qualified and experienced persons. 4. When host country regulations differ from the levels and measures presented in the EHS Guidelines, projects are expected to achieve whichever are more stringent. -
Oil Spill by the Oil Rig “Deepwater Horizon”
Case 2:10-md-02179-CJB-DPC Document 26924 Filed 02/23/21 Page 1 of 9 UNITED STATES DISTRICT COURT EASTERN DISTRICT OF LOUISIANA In Re: Oil Spill by the Oil Rig * MDL 2179 “Deepwater Horizon” in the Gulf of Mexico, on April 20, 2010 * SECTION: J(2) Applies to: * JUDGE BARBIER All Cases in the B3 Pleading Bundle * MAG. JUDGE CURRAULT CASE MANAGEMENT ORDER FOR THE B3 BUNDLE This multidistrict litigation (“MDL”) arose from the blowout, explosions, and fire on the mobile offshore drilling unit DEEPWATER HORIZON on April 20, 2010, and the massive oil spill that resulted in the Gulf of Mexico. Early on, the Court organized the various types of claims into “pleading bundles.” (See PTO 11, Rec. Doc. 569; PTO 25, Rec. Doc. 983). Relevant here is the “B3 bundle,” which consists of claims for personal injury and wrongful death due to exposure to oil and/or other chemicals used during the oil spill response (e.g., dispersant).1 “B3 plaintiff/claim/case” refers to a plaintiff, claim, or case in this bundle. Approximately 810 of the 839 cases remaining in the MDL are in the B3 bundle.2 On November 17, 2020, the Court held a status conference to discuss future case management for the B3 bundle. (See 11/17/20 Minute Entry, Rec. Doc. 26784; Transcript, Rec. Doc. 26788). After hearing counsels’ arguments—and having 1 While all of the remaining B3 cases assert chemical exposure claims, approximately 60 also allege a non-exposure injury (e.g., slip and fall while performing cleanup work). -
American Real Estate Society 35Th Annual Meeting 2019 PROGRAM
35th American Real Estate Society Annual Meeting, April 9-13 2019 JW Marriott, Camelback Inn, Paradise Valley, Arizona American Real Estate Society 35th Annual Meeting 2019 PROGRAM J W Marriott Camelback Inn Paradise Valley Arizona April 9-13 2019 35th American Real Estate Society Annual Meeting, April 9-13 2019 JW Marriott, Camelback Inn, Paradise Valley, Arizona 35th American Real Estate Society Annual Meeting April 9th – 13th 2019 - Program Overview Tuesday April 9th 6.00pm-9.00pm Camelback Patio Event Board of Directors Reception Wednesday April 10th 7.45am-5.00pm Arizona Ballroom Registration Desk Registration North 8.00am-12.00pm Salons A-B Event ARES Board of Directors Meeting (by invitation) 11.00am-1.00pm Salons E Event Center Directors/Chairholders Meeting (by invitation) 12.00pm-1.00pm Camelback Patio Event ARES Foundation Meeting (by invitation) 1.00pm-5.30pm Salons H-I Session 1 Critical Issues Seminar 5.30pm-6.30pm Salon B Event IRES Board Meeting 6.30pm-9.00pm Camelback Patio Event Welcome Reception Thursday April 11th 7.00am-10.00am Salon G Event C-WI(RE)2 Caucas Networking Followed by Panel 7.00am-8.30am Camelback Patio Event Networking 7.45am-5.00pm Arizona Ballroom Registration Desk Registration North 8.00am-10.00am Salon A Session 2 Big Data, Residential Valuation & Data Modeling Salon B Session 3 House Price Diffusion Salon C Session 4 Investment Strategies in Exchange Traded Markets Salon D Session 5 Asset Management: Investment Perspectives Salon E Session 6 Real Estate Agents and Brokerage Salon G Session 7 C-WI(RE)2