Iconic Building Using White Portland Cement
Total Page:16
File Type:pdf, Size:1020Kb
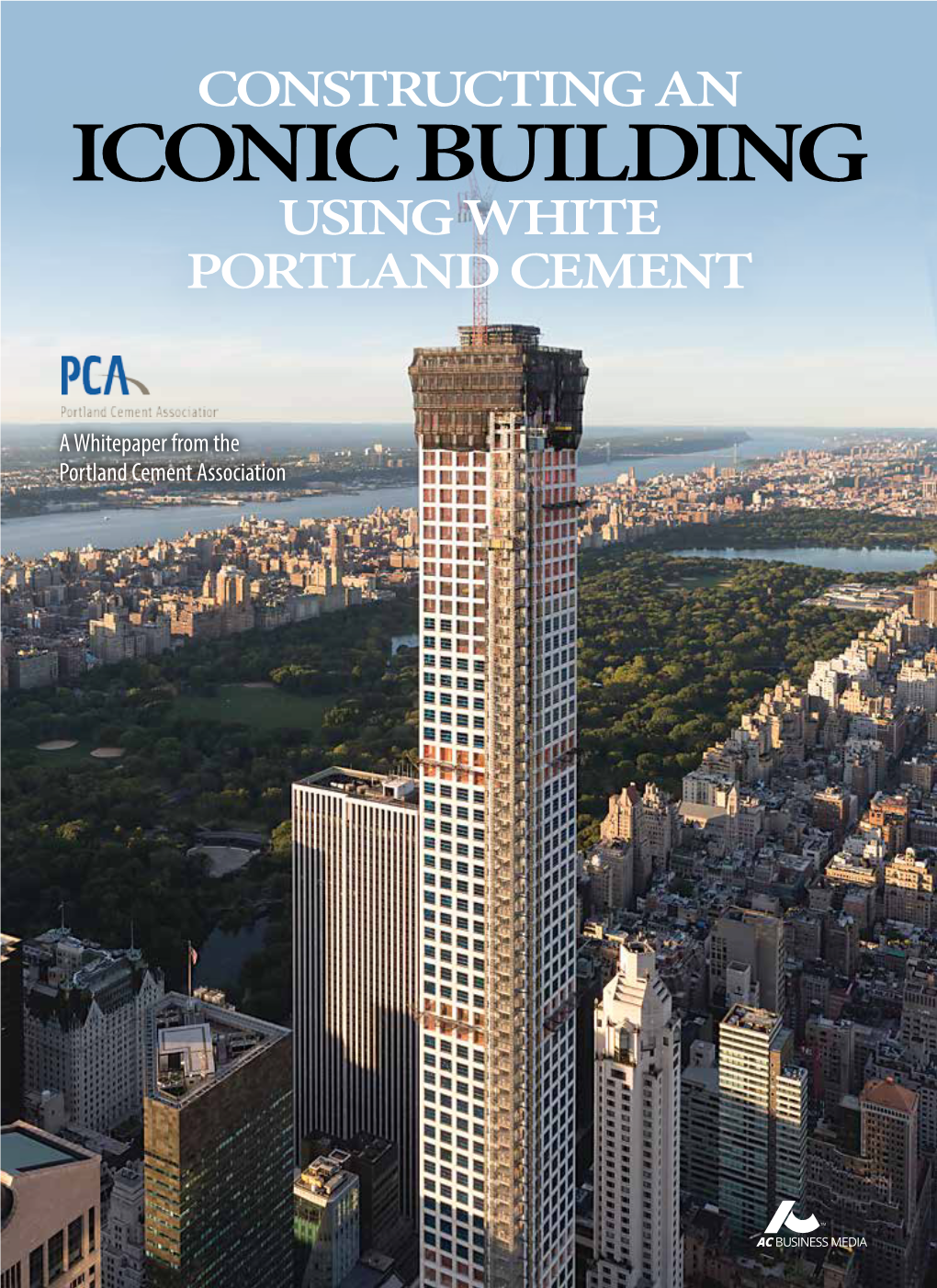
Load more
Recommended publications
-
One West End, 432 Park Avenue, and One57 Are the Top-Selling Condo Buildings in New York City So Far This Year, According to Research from Cityrealty
By CityRealty Staff Friday, July 13, 2018 L to R: One West End, 432 Park Avenue, One57 One West End, 432 Park Avenue, and One57 are the top-selling condo buildings in New York City so far this year, according to research from CityRealty. Closings in the three buildings together have accounted for more than half a billion dollars in sales. Recorded sales in One West End so far this year have totaled $207 million over 57 units. The average sales price in the building this year is $3.6 million, and the average price/ft2 is $2,064. The Elad Group and Silverstein Properties-developed building, where closings started last year, is approaching sell-out status, with 193 of the 246 units having closed already, including one four-bedroom now belonging to Bruce Willis and his wife Emma Heming Willis. // One West End interiors (DBOX / Pelli Clarke Pelli Architects) https://www.cityrealty.com/nyc/market-insight/features/get-to-know/2018039s-top-selling-condos-so-far-one-west- end-beats-432-park-avenue/19263 Even though there have only been 8 closings recorded so far this year in 432 Park Avenue, the world's tallest residential building is the second-highest selling building of 2018 so far, with $185 million in sales. The average price of the closed sales in 432 Park this year is $23.1 million, while the average price/ft2 is $6,509. J.Lo & A-Rod's new condo (Douglas Elliman) In February, developers CIM Group and Macklowe Properties announced that the Billionaire's Row supertall is the single best-selling building in New York City, with $2 billion under its belt at the time. -
Active Control of Pendulum Tuned Mass Dampers for Tall
ACTIVE CONTROL OF PENDULUM TUNED MASS DAMPERS FOR TALL BUILDINGS SUBJECT TO WIND LOAD Dissertation Submitted to The School of Engineering of the UNIVERSITY OF DAYTON In Partial Fulfillment of the Requirements for The Degree of Doctor of Philosophy in Engineering By Mohamed A. Eltaeb, M.S. UNIVERSITY OF DAYTON Dayton, Ohio December, 2017 ACTIVE CONTROL OF PENDULUM TUNED MASS DAMPERS FOR TALL BUILDINGS SUBJECT TO WIND LOAD Name: Eltaeb, Mohamed Ali APPROVED BY: ------------------------------------- ------------------------------------- Reza Kashani, Ph.D. Dave Myszka, Ph.D. Committee Chairperson Committee Member Professor Associate Professor Department of Mechanical Department of Mechanical and Aerospace Engineering and Aerospace Engineering ------------------------------------- ------------------------------------- Elias Toubia, Ph.D. Muhammad Islam, Ph.D. Committee Member Committee Member Assistant Professor Professor Department of Civil and Department of Mathematics Environmental Engineering ------------------------------------- ------------------------------------- Robert J. Wilkens, Ph.D., P.E. Eddy M. Rojas, Ph.D., M.A., P.E. Associate Dean for Research and Innovation Dean, School of Engineering Professor School of Engineering ii © Copyright by Mohamed A. Eltaeb All rights reserved 2017 ABSTRACT ACTIVE CONTROL OF PENDULUM TUNED MASS DAMPERS FOR TALL BUILDINGS SUBJECT TO WIND LOAD Name: Eltaeb, Mohamed A. University of Dayton Advisor: Dr. Reza Kashani Wind induced vibration in tall structures is an important problem that needs effective and practical solutions. TMDs in either passive, active or semi-active form are the most common devices used to reduce wind-induced vibration. The objective of this research is to investigate and develop an effective model of a single multi degree of freedom (MDOF) active pendulum tuned mass damper (APTMD) controlled by hydraulic system in order to mitigate the dynamic response of the proposed tall building perturbed by wind loads in different directions. -
PERSHING SQUARE VIADUCT (Park Avenue Viaduct), Park Avenue from 40Th Street to Grand Central Terminal (42Nd Street), Borough of Manhattan
Landmarks Preservation Commission September 23, 1980, Designation List 137 LP-1127 PERSHING SQUARE VIADUCT (Park Avenue Viaduct), Park Avenue from 40th Street to Grand Central Terminal (42nd Street), Borough of Manhattan. Built 1917-19; architects Warren & Wetmore. Landmark Site: The property bounded by a line running easward parallel with the northern curb line of East 40th Street, a line running northward to the edge of Tax Map Block 1280, Lot 1, parallel with the eastern wall of the viaduct, a line running westward along the edge of Tax Map Block 1280, Lot 1, and a line running southward parallel with the western wall of the viaduct to the point of beginning. On March 11, 1980, the Landmarks Preservation Commission held a public hearing on the proposed designation as a Landmark of the Pershing Square Viaduct (Park Avenue Viaduct) and the proposed designation of the related Landmark Site (Item No. 9). The hearing had been duly advertised in accordance with the provisions of law. Four witnesses spoke in favor of designation. There were no speakers in opposition to designation. DESCRIPTION AND ANALYSIS Located at Park Avenue and 42nd Street, tfie Pershing Square Viaduct was constructed tn 1917-1919. The viaduct extends from 40th Street to Grand Central Terminal at 42nd Street, linking upper and lower Park Avenue by way of elevated drives that make a circuit around the terminal building and descend to ground level at 45th Street. Designed in 1912 by the architectural firm of Warren & Wetmore, the viaduct was conceived as part of the original 1903 plan for the station by the firm of Reed & Stem. -
New York Ny Midtown East
MIDTOWN EAST NEW YORK NY 60 EAST 56TH STREET CONCEPTUAL RENDERING SPACE DETAILS LOCATION GROUND FLOOR South block between Park and Madison Avenues APPROXIMATE SIZE Ground Floor 2,595 SF FRONTAGE 30 FT on East 56th Street POSSESSION Immediate SITE STATUS Currently Così NEIGHBORS Chop’t Creative Salad Co., Roast Kitchen, TD Bank, The Walking Company, Robert Marc, First Republic Bank, Lacoste, Breitling, Victoria’s Secret, Windsor Jewelers, 2,595 SF Jacob & Co., Chase Bank, IBM, Alfred Dunhill, BLT Steak, Bomber Ski, Wells Fargo, Giorgio Armani, Dolce & Gabbana, Omega, Breguet, Gucci, Tiffany & Co., Bonhams, Tourneau, Niketown, Pret a Manger, Papyrus, Allen Edmonds, Roger Dubuis, and Oscar Blandi COMMENTS High traffic commercial area with luxury retail, high-end residential and office populations Surrounded by 33,683,250 SF of office space within a quarter mile radius Across from 432 Park Avenue with 104 luxury condominion units 30 FT EAST 56TH STREET MIDTOWN47th - 60th Street, Second - Fifth Avenue NEW YORK | NY 02.13.201New9 York, NY October 2017 EAST 47TH-EAST 60TH STREET, THIRD-FIFTH AVENUE EAST 60TH STREET EAST 60TH STREET Avra Rotisserie Le Bilboquet Canaletto Lerebours ALT Box Gerorgette Antiques Cinemas 1, 2 & 3 Savoir Manhattan à McKinnon Beds Cabinetry Renny & Reed and Harris The Rug Company Delmonico Gourmet Mastour Janus George N Food Market Carpet et Cie Antiques EAST 59TH STREET EAST 59TH STREET Argosy N Michael Book Store Dawkins D&D R Antiques W Samuel & Sons AREA RETAIL Evolve Foundry Illume EAST 58TH STREET EAST 58TH STREET -
Leseprobe 9783791384900.Pdf
NYC Walks — Guide to New Architecture JOHN HILL PHOTOGRAPHY BY PAVEL BENDOV Prestel Munich — London — New York BRONX 7 Columbia University and Barnard College 6 Columbus Circle QUEENS to Lincoln Center 5 57th Street, 10 River to River East River MANHATTAN by Ferry 3 High Line and Its Environs 4 Bowery Changing 2 West Side Living 8 Brooklyn 9 1 Bridge Park Car-free G Train Tour Lower Manhattan of Brooklyn BROOKLYN Contents 16 Introduction 21 1. Car-free Lower Manhattan 49 2. West Side Living 69 3. High Line and Its Environs 91 4. Bowery Changing 109 5. 57th Street, River to River QUEENS 125 6. Columbus Circle to Lincoln Center 143 7. Columbia University and Barnard College 161 8. Brooklyn Bridge Park 177 9. G Train Tour of Brooklyn 195 10. East River by Ferry 211 20 More Places to See 217 Acknowledgments BROOKLYN 2 West Side Living 2.75 MILES / 4.4 KM This tour starts at the southwest corner of Leonard and Church Streets in Tribeca and ends in the West Village overlooking a remnant of the elevated railway that was transformed into the High Line. Early last century, industrial piers stretched up the Hudson River from the Battery to the Upper West Side. Most respectable New Yorkers shied away from the working waterfront and therefore lived toward the middle of the island. But in today’s postindustrial Manhattan, the West Side is a highly desirable—and expensive— place, home to residential developments catering to the well-to-do who want to live close to the waterfront and its now recreational piers. -
True to the City's Teeming Nature, a New Breed of Multi-Family High Rises
BY MEI ANNE FOO MAY 14, 2016 True to the city’s teeming nature, a new breed of multi-family high rises is fast cropping up around New York – changing the face of this famous urban jungle forever. New York will always be known as the land of many towers. From early iconic Art Deco splendours such as the Empire State Building and the Chrysler Building, to the newest symbol of resilience found in the One World Trade Center, there is no other city that can top the Big Apple’s supreme skyline. Except itself. Tall projects have been proposed and built in sizeable numbers over recent years. The unprecedented boom has been mostly marked by a rise in tall luxury residential constructions, where prior to the completion of One57 in 2014, there were less than a handful of super-tall skyscrapers in New York. Now, there are four being developed along the same street as One57 alone. Billionaire.com picks the city’s most outstanding multi-family high rises on the concrete horizon. 111 Murray Street This luxury residential tower developed by Fisher Brothers and Witkoff will soon soar some 800ft above Manhattan’s Tribeca neighborhood. Renderings of the condominium showcase a curved rectangular silhouette that looks almost round, slightly unfolding at the highest floors like a flared glass. The modern design is from Kohn Pedersen Fox. An A-team of visionaries has also been roped in for the project, including David Mann for it residence interiors; David Rockwell for amenities and public spaces and Edmund Hollander for landscape architecture. -
Citicorp Center + Citigroup Center + 601 Lexington (Current)
http://www.601lexington.com/gallery/?pp_fID_1156=504 Ana Larranaga | Allie McGehee | Lisa Valdivia | Madison Van Pelt | Yiwen Zhang Location: 601 Lexington Avenue + 54th Street, New York NY 10022 Other Names: CitiCorp Center + CitiGroup Center + 601 Lexington (Current) Architects: Hugh Stubbins, William LeMessurier Chief Structural Engineer: William LeMessurier Years Built: 1974 - 1977 Year Opened: 1977 Cost: $195,000,000 http://adamkanemacchia.com/gallery/home/_akm0205-edit/ - CitiCorp Center is the first skyscraper in the U.S to be built with a tuned mass damper - The tower is the 6th highest building in NYC - The building was built for commercial office - Design for the building was drawn by William LeMessurier on his restaurant napkin - The office lobby was renovated in 1997 and a new lobby was built in 2010 - The structure was being fixed secretly at night Born: January 11th, 1912 - July 5th 2006 Birthplace: Birmingham, Alabama Education: Georgia Institute of Technology(Undergrad) Harvard University (Masters) Firm: Hugh Stubbins and Associates (won one of the 1st AIA Firm Awards) Projects: CitiCorp Center, Boston’s Federal Reserve Bank, Ronald Reagan Presidential Library, Landmark tower in Yokohama Awards: Gold Medal (Tau Sigma Delta), Honor Award AIA 1979 Born: June 1926 - June 2007 Birthplace: Pontiac, Michigan Education: Harvard University(BA Mathematics), Harvard Graduate School of Design, MIT (Masters in Engineering) Firm: LeMessurier Consultants Projects: Mah - LeMessurier System, Staggered Truss System, Tuned Mass Damper, -
Modern Engineering Tools and Tech
odern engineering tools and tech- as partitions, glazing, and the façade. Beyond niques enable structural engineers any noticeable harm caused by a single large dis- STRUCTURAL to continually redefine the limits placement, the accumulation of many cycles of of possibility. Nowhere is this amplitude can also cause fatigue failures. Mmore evident than in supertall buildings, where Wind-induced movement can cause two other PERFORMANCE controlling wind-induced sway has become a significant problems that affect a building’s critical aspect of project success. usability. The first, audible creaking and groan- The use of tuned mass damping systems has ing, seems to be especially prevalent where there performance issues relative become a mainstay in attaining this control, in is the greatest amount of relative motion between to extreme events large part because each custom-designed system building parts as the building deflects. Often can be tuned to match the as-built characteristics of occurring on the lower levels, these potentially the building. They also provide a much more effi- loud noises can make even a new building sound cient solution than adding more mass or stiffness. like a rickety old ship. One recent example is the Shanghai Tower which, The most common problem, however, is the when it opened in 2014, became China’s tallest perception of movement that comes from the building and the second tallest building in the acceleration of the ®building as it sways back and world. Even though the design of the 2,073-foot forth. This is an issue that designers must address (632-meter) tower was optimized to reduce wind to ensure occupants remain comfortable even as effects, the developer also chose to include a tuned the building moves. -
Manhattan New Construction & Proposed Multifamily Projects 4Q20
Manhattan New Construction & Proposed Multifamily Projects 4Q20 83 85 82 12 41 62 ID PROPERTY UNITS 6 30 Morningside Drive 205 Total Lease Up 205 12 HAP Seven NY 129 15 418 West 126th Street 75 19 Victoria Theatre 191 15 Total Under Construction 395 19 37 Broadway Development 130 6 41 210 Wadsworth Avenue 98 46 Total Planned 228 43 96th Street 171 43 46 Frederick Douglass Blvd 100 37 62 4037 Broadway 132 82 The Heights on Broadway 171 83 Sherman Plaza 272 85 3875 9th Avenue 614 Total Prospective 1,460 2000 ft Source: Yardi Matrix LEGEND Lease-Up Under Construction Planned Prospective Manhattan New Construction & Proposed Multifamily Projects 4Q20 44 73 ID PROPERTY UNITS 1 The Smile 233 3 Convivium 140 45 4 Sixty 125 141 4 39 23 26 5 Two Waterline Square 435 Total Lease Up 949 1 74 13 75 10 Sendero Verde Phase II 361 22 24 13 One East Harlem 404 25 Total Under Construction 765 49 22 15 West 118th Street 51 38 23 1971 Madison Avenue 93 10 24 72 East 120th Street 218 77 25 77 East 118th Street 202 47 26 East 127th Street 152 38 La Hermosa Tower 160 39 2031-2033 5th Avenue 240 Total Planned 1,116 48 44 58 West 135th Street 100 45 64-74 West 125th Street 200 47 1987-1991 3rd Avenue 59 76 48 1988-1996 2nd Avenue 185 49 248 East 120th Street 86 50 308 East 86th Street 68 78 52 Lenox Hill Hospital 200 73 Lenox Terrace Phase II 1,642 74 1800 Park Avenue 670 50 75 2460 2nd Avenue 730 3 76 321 East 96th Street 1,100 77 East River Plaza 1,100 52 5 78 Holmes Towers NextGen Development 339 Total Prospective 6,479 1000 ft Source: Yardi Matrix LEGEND -
Download the 2019 Map & Guide
ARCHITECTURAL AND CULTURAL Map &Guide FRIENDS of the Upper East Side Historic Districts Architectural and Cultural Map and Guide Founded in 1982, FRIENDS of the Upper East Side Historic Districts is an independent, not-for-profit membership organization dedicated to preserving the architectural legacy, livability, and sense of place of the Upper East Side by monitoring and protecting its seven Historic Districts, 131 Individual Landmarks, and myriad significant buildings. Walk with FRIENDS as we tour some of the cultural and architectural sites that make the Upper East Side such a distinctive place. From elegant apartment houses and mansions to more modest brownstones and early 20th-century immigrant communities, the Upper East Side boasts a rich history and a wonderfully varied built legacy. With this guide in hand, immerse yourself in the history and architecture of this special corner of New York City. We hope you become just as enchanted by it as we are. FRIENDS’ illustrated Architectural and Cultural Map and Guide includes a full listing of all of the Upper East Side’s 131 Individual Landmarks. You can find the location of these architectural gems by going to the map on pages 2-3 of the guide and referring to the numbered green squares. In the second section of the guide, we will take you through the history and development of the Upper East Side’s seven Historic Districts, and the not landmarked, though culturally and architecturally significant neighborhood of Yorkville. FRIENDS has selected representative sites that we feel exemplify each district’s unique history and character. Each of the districts has its own color-coded map with easy-to-read points that can be used to find your own favorite site, or as a self-guided walking tour the next time you find yourself out strolling on the Upper East Side. -
Manhattan Year BA-NY H&R Original Purchaser Sold Address(Es)
Manhattan Year BA-NY H&R Original Purchaser Sold Address(es) Location Remains UN Plaza Hotel (Park Hyatt) 1981 1 UN Plaza Manhattan N Reader's Digest 1981 28 West 23rd Street Manhattan Y NYC Dept of General Services 1981 NYC West Manhattan * Summit Hotel 1981 51 & LEX Manhattan N Schieffelin and Company 1981 2 Park Avenue Manhattan Y Ernst and Company 1981 1 Battery Park Plaza Manhattan Y Reeves Brothers, Inc. 1981 104 W 40th Street Manhattan Y Alpine Hotel 1981 NYC West Manhattan * Care 1982 660 1st Ave. Manhattan Y Brooks Brothers 1982 1120 Ave of Amer. Manhattan Y Care 1982 660 1st Ave. Manhattan Y Sanwa Bank 1982 220 Park Avenue Manhattan Y City Miday Club 1982 140 Broadway Manhattan Y Royal Business Machines 1982 Manhattan Manhattan * Billboard Publications 1982 1515 Broadway Manhattan Y U.N. Development Program 1982 1 United Nations Plaza Manhattan N Population Council 1982 1 Dag Hammarskjold Plaza Manhattan Y Park Lane Hotel 1983 36 Central Park South Manhattan Y U.S. Trust Company 1983 770 Broadway Manhattan Y Ford Foundation 1983 320 43rd Street Manhattan Y The Shoreham 1983 33 W 52nd Street Manhattan Y MacMillen & Co 1983 Manhattan Manhattan * Solomon R Gugenheim 1983 1071 5th Avenue Manhattan * Museum American Bell (ATTIS) 1983 1 Penn Plaza, 2nd Floor Manhattan Y NYC Office of Prosecution 1983 80 Center Street, 6th Floor Manhattan Y Mc Hugh, Leonard & O'Connor 1983 Manhattan Manhattan * Keene Corporation 1983 757 3rd Avenue Manhattan Y Melhado, Flynn & Assocs. 1983 530 5th Avenue Manhattan Y Argentine Consulate 1983 12 W 56th Street Manhattan Y Carol Management 1983 122 E42nd St Manhattan Y Chemical Bank 1983 277 Park Avenue, 2nd Floor Manhattan Y Merrill Lynch 1983 55 Water Street, Floors 36 & 37 Manhattan Y WNET Channel 13 1983 356 W 58th Street Manhattan Y Hotel President (Best Western) 1983 234 W 48th Street Manhattan Y First Boston Corp 1983 5 World Trade Center Manhattan Y Ruffa & Hanover, P.C. -
Analysis of Technical Problems in Modern Super-Slim High-Rise Residential Buildings
Budownictwo i Architektura 20(1) 2021, 83-116 DOI: 10.35784/bud-arch.2141 Received: 09.07.2020; Revised: 19.11.2020; Accepted: 15.12.2020; Avaliable online: 09.02.2020 © 2020 Budownictwo i Architektura Orginal Article This is an open-access article distributed under the terms of the CC-BY-SA 4.0 Analysis of technical problems in modern super-slim high-rise residential buildings Jerzy Szołomicki1, Hanna Golasz-Szołomicka2 1 Faculty of Civil Engineering; Wrocław University of Science and Technology; 27 Wybrzeże Wyspiańskiego st., 50-370 Wrocław; Poland, [email protected] 0000-0002-1339-4470 2 Faculty of Architecture; Wrocław University of Science and Technology; 27 Wybrzeże Wyspiańskiego St., 50-370 Wrocław; Poland [email protected] 0000-0002-1125-6162 Abstract: The purpose of this paper is to present a new skyscraper typology which has developed over the recent years – super-tall and slender, needle-like residential towers. This trend appeared on the construction market along with the progress of advanced struc- tural solutions and the high demand for luxury apartments with spectacular views. Two types of constructions can be distinguished within this typology: ultra-luxury super-slim towers with the exclusivity of one or two apartments per floor (e.g. located in Manhattan, New York) and other slender high-rise towers, built in Dubai, Abu Dhabi, Hong Kong, Bangkok, and Melbourne, among others, which have multiple apartments on each floor. This paper presents a survey of selected slender high-rise buildings, where structural improvements in tall buildings developed over the recent decade are considered from the architectural and structural view.