Ultra-High Performance Concrete: a State-Of-The-Art Report for the Bridge Community
Total Page:16
File Type:pdf, Size:1020Kb
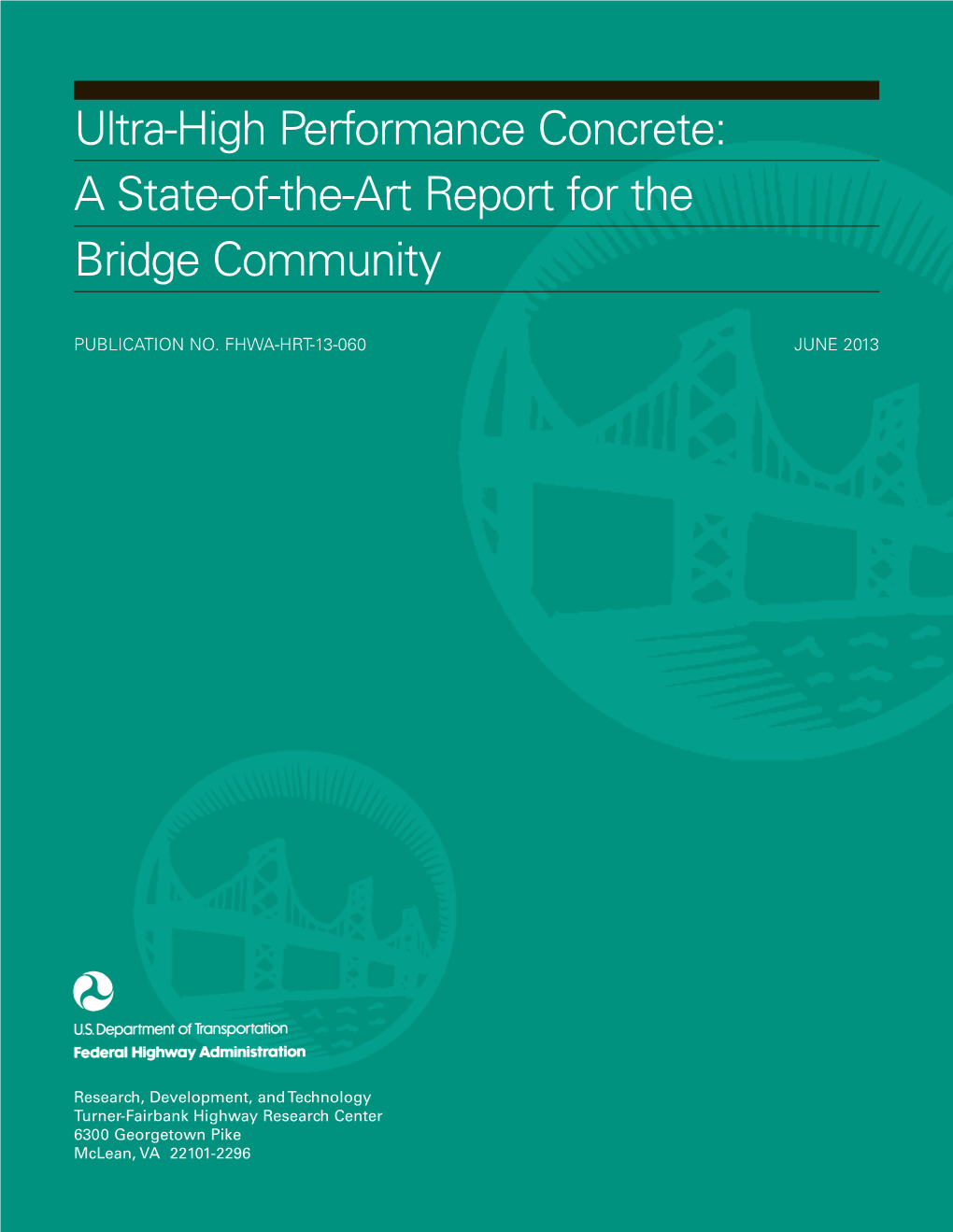
Load more
Recommended publications
-
Two-Way Joist (Waffle Slab) Concrete Floor System Analysis and Design
Two-Way Joist Concrete Slab Floor (Waffle Slab) System Analysis and Design Version: May-18-2017 Two-Way Joist Concrete Slab Floor (Waffle Slab) System Analysis and Design Design the concrete floor slab system shown below for an intermediate floor with partition weight of 50 psf, and unfactored live load of 100 psf. The lateral loads are independently resisted by shear walls. A flat plate system will be considered first to illustrate the impact longer spans and heavier applied loads. A waffle slab system will be investigated since it is economical for longer spans with heavy loads. The dome voids reduce the dead load and electrical fixtures can be fixed in the voids. Waffle system provides an attractive ceiling that can be left exposed when possible producing savings in architectural finishes. The Equivalent Frame Method (EFM) shown in ACI 318 is used in this example. The hand solution from EFM is also used for a detailed comparison with the model results of spSlab engineering software program from StructurePoint. Figure 1 - Two-Way Flat Concrete Floor System Version: May-18-2017 Contents 1. Preliminary Member Sizing ..................................................................................................................................... 1 2. Flexural Analysis and Design................................................................................................................................. 13 2.1. Equivalent Frame Method (EFM) .................................................................................................................. -
UNIVERSITY of CALIFORNIA, IRVINE Flexural Behavior of Two
UNIVERSITY OF CALIFORNIA, IRVINE Flexural Behavior of Two-Way Sandwich Slabs THESIS submitted in partial satisfaction of the requirements for the degree of MASTER OF SCIENCE in CIVIL ENGINEERING by JIVAN VILAS PACHPANDE Thesis Committee: Professor Ayman S. Mosallam, Chair Associate Professor Farzin Zareian Assistant Professor Mohammad Javad Abdolhosseini Qomi 2015 © 2015 Jivan Vilas Pachpande DEDICATION It is with my deepest gratitude and warmest affection that I dedicated this thesis to our Professor Dr. Ayman S. Mosallam Who has been a constant source of Knowledge and Inspiration. ii TABLE OF CONTENT Page LIST OF FIGURES v LIST OF TABLES viii ACKNOWLEDGMENTS ix ABSTRACT OF THE THESIS x Chapter 1 INTRODUCTION 1 1.1 CEMENTITIOUS COMPOSITE FLOOR PANELS WITH EPS FOAM 2 CORE 1.2 MATERIALS DATA 2 1.3 REINFORCEMENT SCHEDULE 5 1.4 MOTIVATION AND PURPOSE OF STUDY 7 1.5 DESCRIPTION OF EXPERIMENT PROGRAM 8 Chapter 2 STRUCTURAL BEHAVIOR OF TWO-WAY SLABS 17 2.1 TYPES OF TWO WAY SLABS 19 2.2 BEHAVIOR OF TWO-WAY SLABS 22 2.3 ANALYSIS METHODS FOR TWO WAY SLABS 25 2.4 REVIEW OF ELASTIC PLATE BENDING THEORY 32 2.3 FINITE ELEMENT ANALYSIS FOR TWO-WAY SLABS 38 Chapter 3 THEORETICAL ANALYSIS OF TWO-WAY EPS CONCRETE SLAB 40 3.1 COMPOSITE BEHAVIOR OF 3D CEMENTITIOUS SANDWICHED 40 PANEL iii 3.2 CAPACITY PREDICTION FOR EPS CONCRETE PANEL 42 3.3 PREDICTION OF FAILURE LOAD BY YIELD LINE METHOD 46 Chapter 4 FINITE ELEMENT MODELLING OF TWO-WAY SANDWICHED 52 SLABS 4.1 INTRODUCTION 52 4.2 MATERIAL DEFINITIONS AND TYPE OF ELEMENT 53 4.3 MESH SIZE,LOADING AND BOUNDARY -
Development of a Sustainability Approach for the Structural Design of Buildings
University of Wollongong Research Online University of Wollongong Thesis Collection 2017+ University of Wollongong Thesis Collections 2017 Development of a sustainability approach for the structural design of buildings Mehdi Robati University of Wollongong Follow this and additional works at: https://ro.uow.edu.au/theses1 University of Wollongong Copyright Warning You may print or download ONE copy of this document for the purpose of your own research or study. The University does not authorise you to copy, communicate or otherwise make available electronically to any other person any copyright material contained on this site. You are reminded of the following: This work is copyright. Apart from any use permitted under the Copyright Act 1968, no part of this work may be reproduced by any process, nor may any other exclusive right be exercised, without the permission of the author. Copyright owners are entitled to take legal action against persons who infringe their copyright. A reproduction of material that is protected by copyright may be a copyright infringement. A court may impose penalties and award damages in relation to offences and infringements relating to copyright material. Higher penalties may apply, and higher damages may be awarded, for offences and infringements involving the conversion of material into digital or electronic form. Unless otherwise indicated, the views expressed in this thesis are those of the author and do not necessarily represent the views of the University of Wollongong. Recommended Citation Robati, Mehdi, Development of a sustainability approach for the structural design of buildings, Doctor of Philosophy thesis, Sustainable Buildings Research Centre, University of Wollongong, 2017. -
FORMWORK for a CONCRETE SLAB the Bulk of the Work in Laying a New Slab for a Domestic Building Is in the Excavation and Preparation of the Formwork
Page 20. VU20981 – Formwork for concreting FORMWORK FOR A CONCRETE SLAB The bulk of the work in laying a new slab for a domestic building is in the excavation and preparation of the formwork. In this unit you will be constructing formwork for a 'L' shaped dwelling using appropriate materials and techniques that include: external corner internal corner edge rebate Plan for a 'L' shaped dwelling The importance of getting the formwork for a concrete slab right, cannot be overstated. The formwork must be rigid and thick enough so as not to bend under the load of fresh concrete placed against it. The formwork will lay out the dimensions of the home. 22216VIC – Certificate II in Building and Construction (Carpentry) Copyright LAPtek Pty. Ltd. VU20981 – Formwork for concreting Page 21. CONCRETE SLABS A concrete slab forms the foundation of a house or building and is made using concrete. The type of slab used depends on the nature of the soil on the site and the kind of house being built. There are two main types of concrete slabs, raft or ground slab and waffle slab. Raft or Ground Level Slab Raft foundation consists of a concrete slab Moreover, raft foundation serves to avoid differential settlement which otherwise would occur if pad or strip foundation is adopted. Raft or ground level slab Waffle Pod Slab A waffle pod slab is constructed entirely above the ground by pouring concrete over a grid of polystyrene blocks known as 'void forms'. Waffle pod slabs are generally suitable for sites with less reactive soil and use about 30% less concrete and 20% less steel than a raft or ground level slab Waffle pod slabs are only suitable for very flat ground. -
IS063 Floor Systems
BUILDINGS An Engineers Guide to: Economical Concrete Floor Systems Numerous types of cast-in-place and precast concrete floor systems From concept to are available to satisfy virtually any span and loading condition. completion, the 21 story mixed-use Astor Place Reinforced concrete allows a wide range of structural options and Tower, New York, New provides cost-effective solutions for a multitude of situations—from York is a show-case residential buildings with moderate live loads and spans of about for the versatility of 25 ft, to commercial buildings with heavier live loads and spans reinforced concrete in ranging from 40 ft to 50 ft and beyond. Shorter floor-to-floor heights building construction. and inherent fire and vibration resistance are only a few of the many advantages that concrete floor systems offer, resulting in sig- nificant reductions in both structural and nonstructural costs. Since the cost of the floor system can be a major part of the struc- tural cost of a building, selecting the most effective system for a given set of constraints is vital in achieving overall economy. This is especially important for buildings of low-and medium heights and for buildings subjected to relatively low wind or seismic forces, since the cost of lateral load resistance in these cases is minimal. The information provided below will help in selecting an economical cast-in-place concrete floor system for a variety of span lengths and superimposed gravity loads. Also presented is basic information on the advantages of the systems, as well as general information on practical framing layouts and formwork. -
Flexural Strength of Prestressed Reinforced Concrete Piles Using High-Strength Material
Third International fib Congress incorporating the PCI Annual Convention and Bridge Conference 2010 Washington, DC, USA 29 May - 2 June 2010 Volume 1 of 6 ISBN: 978-1-61782-821-8 Printed from e-media with permission by: Curran Associates, Inc. 57 Morehouse Lane Red Hook, NY 12571 Some format issues inherent in the e-media version may also appear in this print version. Copyright© (2010) by the Precast Prestressed Concrete Institute All rights reserved. Printed by Curran Associates, Inc. (2011) For permission requests, please contact the Precast Prestressed Concrete Institute at the address below. Precast Prestressed Concrete Institute 200 W. Adams St. #2100 Chicago, IL 60606-6938 Phone: (312) 786-0300 Fax: (312) 621-1114 [email protected] Additional copies of this publication are available from: Curran Associates, Inc. 57 Morehouse Lane Red Hook, NY 12571 USA Phone: 845-758-0400 Fax: 845-758-2634 Email: [email protected] Web: www.proceedings.com TABLE OF CONTENTS VOLUME 1 BRIDGES AND TRANSPORTATION FLEXURAL STRENGTH OF PRESTRESSED REINFORCED CONCRETE PILES USING HIGH-STRENGTH MATERIAL ........................................................................................................................................................................................................1 M. Akiyama, M. Suzuki, R. Abe DESIGN & BUILD FOR PALM JUMEIRAH MONORAIL INFRASTRUCTURES IN DUBAI, U.A.E. ...........................................15 H. Omi, S. Ohno, N. Horikoshi RECENT CHANGES THAT HAVE IMPROVED THE QUALITY OF POSTTENSIONING IN BRIDGE CONSTRUCTION -
Prestressed Waffle Slab Bridges
TRANSPORTATION RESEARCH RECORD 1118 29 Prestressed Waffle Slab Bridges JOHN B. KENNEDY Design engineers Intuitively regard the two-way structural system of a waffle slab to be Incompatible with the one-way load-transferring action of a bridge. However, in relatively wide bridges, In bridges on Isolated supports, and in skew bridges, large twisting and transverse moments are present. !n this paper it Is shown that a waffle slab bridge through its geometry of cross section can provide efficiently the required resistance moments in two orthogonal directions. Results from a feasibility study indicate that a waffle slab bridge (a) has the potential of being a more economical alternative to solid-slab and slab-on-girder bridges; and (b) provides excellent access to prestresslng cables for both inspection and maintenance pur poses. Tools for design and analysis of waffle slab bridges for both serviceability and ultimate limit states are presented. Solid-slab bridges are economical for spans up to about 50 ft; however, for longer spans the redundant dead weight makes these bridges less economical. To enhance structural efficiency, voided-slab bridges were introduced. Observations of the per formance of voided-slab bridges have revealed several disad FIGURE 1 Geometry of a waffle slab. vantages, namely: accessibility to the inside of the voids is poor making it difficult to assess any damage to prestressing steel because of corrosion from exposure to deicing salts; the struc shown (3) that the most efficient way of designing for these ture does not lend itself to readily applicable remedial mea large moments is by providing moments of resistance of similaf sures; and the structure is quite prone to cracking ( 1 ), requiring magnitude in two perpendicular directions. -
Optimum Dimension of Post-Tension Concrete Waffle Slabs
ISSN: 2319-8753 International Journal of Innovative Research in Science, Engineering and Technology (An ISO 3297: 2007 Certified Organization) Vol. 3, Issue 7, July 2014 Optimum Dimension of Post-tension Concrete Waffle Slabs Dr. Alaa C. Galeb, Tariq E. Ibrahim Department of Civil Engineering, University of Basrah, Iraq ABSTRACT: This paper aims to find the optimum dimensions of post-tension concrete (two-way ribbed) waffle slabs using standard dome size. Equivalent frame design method is used for the structural analysis and design of slab. The total cost represents the cost of concrete, strand tendons, steel, duct, grout, anchorages device and formwork for the slab. The effect of the total depth of the slab, ribs width, the spacing between ribs, the top slab thickness, the area of strand tendons and the area of steel. On the total cost of slab are discussed. The result showed that: the span to depth ratio 1/23 to 1/25 give an economic slab cost, and using 750*750 dome with 150mm rib giving minimum cost and weight. It is concluded that, the increasingin balance load, slab thickness, steel weight and total weight decrease, tendon weight increase and the 95% balance load give minimum cost. KEYWORDS: optimum dimension, prestressed waffle slabs I. INTRODUCTION Waffle slab construction consists of rows of concrete joists at right angles to each other with solid heads at the column needed for shear requirements Fig (1). Waffle slab construction allows a considerable reduction in dead load as compared to conventional flat slab construction since the slab thickness can be minimized due to the short span between the joists. -
The Use of a Multi-Criteria Decision Model to Choose Between Different Structural Forms Within Modern Office Construction
Technological University Dublin ARROW@TU Dublin Masters Built Environment 2009-08-01 The Use of a Multi-Criteria Decision Model to Choose Between Different Structural Forms Within Modern Office Construction Margaret Rogers Technological University Dublin Follow this and additional works at: https://arrow.tudublin.ie/builtmas Part of the Other Architecture Commons Recommended Citation Rogers, M. (2010). The Use of a Multi-Criteria Decision Model to Choose Between Different Structural Forms Within Modern Office Construction.Masters dissertation. Dublin Institute of Technology. doi:10.21427/D7NC99 This Theses, Masters is brought to you for free and open access by the Built Environment at ARROW@TU Dublin. It has been accepted for inclusion in Masters by an authorized administrator of ARROW@TU Dublin. For more information, please contact [email protected], [email protected]. This work is licensed under a Creative Commons Attribution-Noncommercial-Share Alike 4.0 License The use of a multi-criteria decision model to choose between different structural forms within modern office construction MPhil Thesis Name: Margaret Rogers Supervisor: Dr. Tom Dunphy Date of Submission: 29/09/2010 1 | Page Declaration I certify that this thesis which I now submit for examination for the award of _____________________, is entirely my own work and has not been taken from the work of others, save and to the extent that such work has been cited and acknowledged within the text of my work. This thesis was prepared according to the regulations for postgraduate study by research of the Dublin Institute of Technology and has not been submitted in whole or in part for another award in any Institute. -
About Flat Plate Voided Concrete Slab Systems
ENGINEERING Frequently Asked Questions ETN-B-4-17 (FAQ) About Flat Plate Voided Concrete Slab Systems Introduction a Flat plate voided concrete slab systems, which have been used for many years in Europe and other parts of the world, are becoming increasingly popular in the U.S. because of many inherent benefits. Such benefits include reduced weight, which results in smaller seismic forces and larger allowable superimposed loads for given span lengths; economical lon- ger spans without beams; reduced floor- b to-floor heights; accelerated construction schedules; and inherent fire resistance that meets the fire-rating requirements in the International Building Code (IBC). Various types of flat plate voided concrete slabs have been used throughout the years, including one-way Sonotube systems and two-way joist (waffle slab) systems that are constructed using dome forms (Mota c 2010). Contemporary proprietary systems pioneered by BubbleDeck® and Cobiax® utilize hollow, plastic balls made of high- density, recycled polyethylene (HDPE) that are spaced regularly within the over- all thickness of the concrete slab. These are commonly referred to as void formers. Technical Note Technical The BubbleDeck® system is usually con- Figure 1 — Void formers (a) BubbleDeck® – Semi- structed as a semi-precast system (Figure precast system (b) BubbleDeck® – Cast-in-place 1a); however, a cast-in-place system is also system (c) Cobiax USA® – Cast-in-place system (Photos courtesy of BubbleDeck and Cobiax USA). available (Figure 1b). The Cobiax® system is typically employed as a cast-in-place sys- tem (Figure 1c). More information on this publication can be obtained by visiting www.crsi.org. -
Flat Plate Voided Slabs: a Lightweight Concrete Floor System Alternative
Flat Plate Voided Slabs: A Lightweight Concrete Floor System Alternative by Hunter Wheeler B.S., Kansas State University, 2018 A REPORT submitted in partial fulfillment of the requirements for the degree MASTER OF SCIENCE Department of Architectural Engineering College of Engineering KANSAS STATE UNIVERSITY Manhattan, Kansas 2018 Approved by: Major Professor Bill Zhang, Ph.D., P.E., S.E., LEED AP Copyright © Hunter Wheeler 2018. Abstract In structural engineering, it can be challenging to incorporate a sustainable design without sacrificing structural integrity. However, flat plate voided slabs are an interesting alternative to standard flat plate concrete slab systems due to the reduction in concrete and the recycled plastic void formers that are located inside the slab. This research is necessary because an increased use of voided slabs in concrete structures would help fight climate change by reducing the CO 2 emissions caused from cement production. This report will discuss the advantages and disadvantages of implementing plastic void formers into solid flat plate slabs and examine a parametric study comparing voided flat plate slabs to solid flat plate slabs. The design of the voided slabs follows the CRSI Design Guide for Voided Concrete Slabs while also referencing the ACI 318-14 Building Code Requirements for Structural Concrete . Three different slabs for typical square bay sizes of 25 feet, 30 feet, and 35 feet are designed to compare the effectiveness of voided slabs to traditional solid slabs. Table of Contents List of Figures -
Automatic Waffle Slab Technique for High-Tech Factory
24th International Symposium on Automation & Robotics in Construction (ISARC 2007) Construction Automation Group, I.I.T. Madras AUTOMATIC WAFFLE SLAB TECHNIQUE FOR HIGH-TECH FACTORY Samuel Y.L. Yin H. Ping Tserng Professor, Dept. of Civil Engineering Professor and Associate Chair, Dept. of Civil National Taiwan Univ. Engineering, National Taiwan Univ. No. 1 Roosevelt Rd., Sec. 4, Taipei, Taiwan No. 1 Roosevelt Rd., Sec. 4, Taipei, Taiwan [email protected] [email protected] W. Jue Hong Ph.D. Student, Dept. of Civil Engineering National Taiwan Univ. No. 1 Roosevelt Rd., Sec. 4, Taipei, Taiwan [email protected] ABSTRACT Under the continuous compression of life cycles for products from the high-tech industry, all investors expect to recoup an enormous amount of investment within the shortest possible timeframe and raise production rapidly, so they can acquire more market opportunities and improve market share. In view of this, investors desire to shorten plant construction as much as possible. The return air floor slab for the clean room is one of the key construction projects. This floor is a common design used in high-tech plants to control the cleanliness and humidity of the air. Concentrated openings and large thickness are the two major requirements for it. Under these two requirements, levelness and resistance to minor vibration of the floor slab must also be considered; this has caused significant difficulties in construction, where many vendors are also confronted with pressures for construction time and quality. In order to solve the difficulties in waffle slab construction, this study has proposed a technique of precast waffle slab to meets the requirements for the high-tech industry on construction time and quality under intense market competition.