Fiber Bragg Grating Based Thermometry
Total Page:16
File Type:pdf, Size:1020Kb
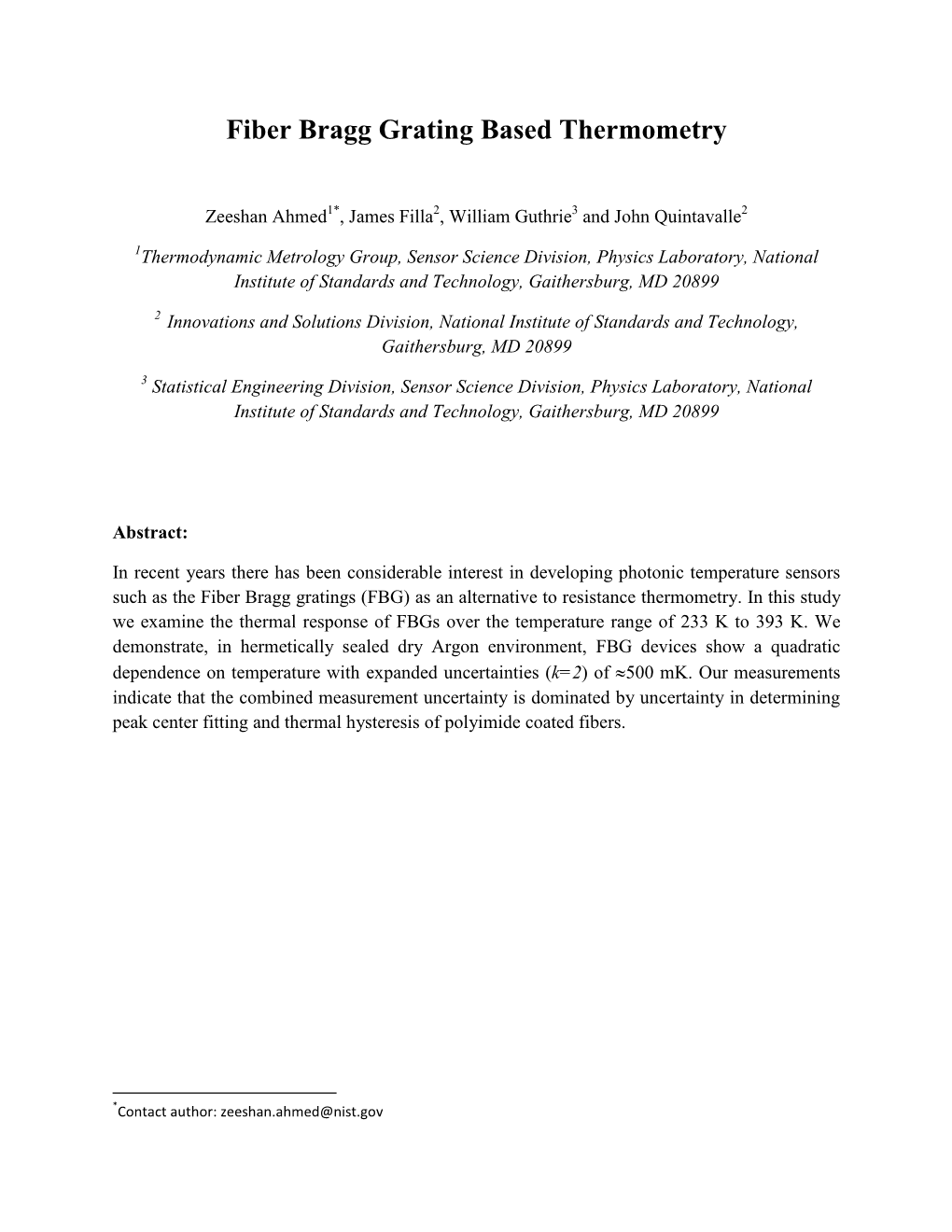
Load more
Recommended publications
-
High-Efficiency Inscription of Fiber Bragg Grating Array with High-Energy Nanosecond-Pulsed Laser Talbot Interferometer
sensors Letter High-Efficiency Inscription of Fiber Bragg Grating Array with High-Energy Nanosecond-Pulsed Laser Talbot Interferometer Zhe Zhang 1,2, Baijie Xu 1,2, Jun He 1,2,3,* , Maoxiang Hou 1,4, Weijia Bao 1,2,3 and Yiping Wang 1,2,3 1 Guangdong and Hong Kong Joint Research Centre for Optical Fiber Sensors, College of Physics and Optoelectronic Engineering, Shenzhen University, Shenzhen 518060, China; [email protected] (Z.Z.); [email protected] (B.X.); [email protected] (M.H.); [email protected] (W.B.); [email protected] (Y.W.) 2 Guangdong Laboratory of Artificial Intelligence and Digital Economy (SZ), Shenzhen University, Shenzhen 518060, China 3 Key Laboratory of Optoelectronic Devices and Systems of Ministry of Education and Guangdong Province, Shenzhen University, Shenzhen 518060, China 4 School of Electromechanical Engineering, Guangdong University of Technology, Guangzhou 510006, China * Correspondence: [email protected]; Tel.: +86-755-2672-8702 Received: 17 June 2020; Accepted: 30 July 2020; Published: 1 August 2020 Abstract: A high-energy nanosecond-pulsed ultraviolet (UV) laser Talbot interferometer for high-efficiency, mass production of fiber Bragg grating (FBG) array was experimentally demonstrated. High-quality FBG arrays were successfully inscribed in both H2-free and H2-loaded standard single-mode fibers (SMFs) with high inscription efficiency and excellent reproducibility. Compared with the femtosecond pulse that had a coherent length of several tens of micrometers, a longer coherent length (~10 mm) of the employed laser rendered a wider FBG wavelength versatility over 700 nm band (1200–1900 nm) without the need for optical path difference (OPD) compensation. -
Fiber Bragg Grating Technology Fundamentals and Overview Kenneth O
JOURNAL OF LIGHTWAVE TECHNOLOGY, VOL. 15, NO. 8, AUGUST 1997 1263 Fiber Bragg Grating Technology Fundamentals and Overview Kenneth O. Hill and Gerald Meltz, Member, IEEE (Invited Paper) Abstract— The historical beginnings of photosensitivity and the cladding with two intersecting beams of UV light; now, the fiber Bragg grating (FBG) technology are recounted. The basic period of the interference maxima and the index change was techniques for fiber grating fabrication, their characteristics, and set by the angle between the beams and the UV wavelength the fundamental properties of fiber gratings are described. The many applications of fiber grating technology are tabulated, and rather than by the visible radiation which was launched into some selected applications are briefly described. the fiber core. Moreover, the grating formation was found to be orders-of-magnitude more efficient. Index Terms—Bragg gratings, optical fiber devices, optical fiber dispersion, optical fiber filters, optical fiber sensors, optical planar At first, the observation of photo-induced refractivity in waveguides and components, photosensitivity. fibers was only a scientific curiosity, but over time it has become the basis for a technology that now has a broad and important role in optical communications and sensor systems. I. INTRODUCTION Research into the underlying mechanisms of fiber photosen- FIBER Bragg grating (FBG) is a periodic perturbation sitivity and its uses is on-going in many universities and Aof the refractive index along the fiber length which industrial laboratories in Europe, North and South America, is formed by exposure of the core to an intense optical Asia, and Australia. Several hundred photosensitivity and fiber interference pattern. -
Fabrication and Applications of Fiber Bragg Grating- a Review
Adv. Eng. Tec. Appl. 4, No. 2, 15-25 (2015) 15 Advanced Engineering Technology and Application An International Journal http://dx.doi.org/10.12785/aeta/040202 Fabrication and Applications of Fiber Bragg Grating- A Review Sanjeev Dewra1, Vikas2 and Amit Grover2,∗ SBSSTC Ferozepur, Punjab, 152004, India Received: 24 Sep. 2014, Revised: 17 Mar. 2015, Accepted: 19 Mar. 2015 Published online: 1 May 2015 Abstract: In this paper, the brief introduction of Fiber Bragg Grating, its significant applications, sensing principles, properties, fabrication and the basic designing of FBG have been discussed. FBG’s are relatively simple to manufacture, small in dimension, low cost and exhibits good immunity from the electromegnatic radiations. The former inceptions and the essential techniques of fiber Bragg grating fabrication are described. This paper presents a comprehensive and systematic overview of FBG technology. Keywords: Fiber Bragg grating, Current applications of Fiber Bragg Grating, Fiber Bragg Grating sensors. 1 Introduction A Fiber Bragg Grating is revealing the core of SMF to a periodic model of passionate ultra violet light. The spotlight generates a stable increase in the refractive index of the core of fiber to produce a fixed index modulation in the direction of the exposure pattern and this fixed index modulation is known as grating. At each periodic refraction small amount of light is reflected. When the grating period is about half the input wavelength of light, all the reflected light signals merge comprehensibly to Fig. 1: Fiber Bragg grating in optical fiber[3] one large reflection at a specific channel. This is known as the Bragg condition. -
Dual Wavelength Differential Detection of Fiber Bragg Grating Sensors with a Pulsed DFB Laser
sensors Article Dual Wavelength Differential Detection of Fiber Bragg Grating Sensors with a Pulsed DFB Laser François Ouellette * , Zhonghua Ou and Jianfeng Li State Key Laboratory of Electronic Thin Films and Integrated Devices, School of Optoelectronic Science and Engineering, University of Electronic Science and Technology of China (UESTC), Chengdu 610054, China; [email protected] (Z.O.); [email protected] (J.L.) * Correspondence: [email protected] Received: 15 July 2020; Accepted: 21 August 2020; Published: 24 August 2020 Abstract: We show how dual wavelength differential detection can be used to measure fiber Bragg grating sensors using nanosecond pulses from a single DFB laser diode, by taking advantage of its dynamic chirp. This can be performed in two ways: by measuring the reflected power from two separate pulses driven by two different currents, or by taking two delayed digitized samples within a single pulse. A prototype instrument using fast digitizing and processing with an FPGA is used to characterize the chirp, from which the performance can be optimized for both measurement schemes. Keywords: fiber Bragg grating; fiber optic sensor; dynamic chirp; DFB laser 1. Introduction Fiber Bragg grating (FBG) sensors have been used for three decades now [1], in applications as varied as aircraft wing shape measurements [2], temperature monitoring in medical treatments [3], pressure and temperature sensing in oil wells [4], or strain sensing in biomechanics [5]. FBG sensors have traditionally been measured either with a combination of a broadband optical source and a spectrometer, or a wavelength-swept source and a photodiode [1]. Both techniques involve acquiring a set of data points covering the entire range of wavelengths potentially reached by the sensor. -
Fiber Bragg Grating (FBG) Sensors in a High-Scattering Optical Fiber Doped with Mgo Nanoparticles for Polarization-Dependent Temperature Sensing
applied sciences Article Fiber Bragg Grating (FBG) Sensors in a High-Scattering Optical Fiber Doped with MgO Nanoparticles for Polarization-Dependent Temperature Sensing Carlo Molardi 1 , Tiago Paixão 2, Aidana Beisenova 1, Rui Min 3,4 , Paulo Antunes 2 , Carlos Marques 2 , Wilfried Blanc 5 and Daniele Tosi 1,6,* 1 School of Engineering, Nazarbayev University, 53 Kabanbay Batyr, Astana 010000, Kazakhstan 2 Physics Department & I3N, University of Aveiro, 3810-193 Aveiro, Portugal 3 Intelligent Manufacturing Faculty, Wuyi University, Jiangmen, China 4 ITEAM Research Institute, Universitat Politècnica de València, 46022 València, Spain 5 INPHYNI–CNRS UMR 7010, Université Côte d’Azur, Parc Valrose, 06108 Nice, France 6 Laboratory of Biosensors and Bioinstruments, National Laboratory Astana, 53 Kabanbay Batyr, Astana 010000, Kazakhstan * Correspondence: [email protected] Received: 3 July 2019; Accepted: 30 July 2019; Published: 1 August 2019 Featured Application: Inscription and interrogation of fiber Bragg gratings into MgO nanoparticle-doped fiber for optical fiber distributed and multiplexed sensing. Abstract: The characterization of Fiber Bragg Grating (FBG) sensors on a high-scattering fiber, having the core doped with MgO nanoparticles for polarization-dependent temperature sensing is reported. The fiber has a scattering level 37.2 dB higher than a single-mode fiber. FBGs have been inscribed by mean of a near-infrared femtosecond laser and a phase mask, with Bragg wavelength around 1552 nm. The characterization shows a thermal sensitivity of 11.45 pm/◦C. A polarization-selective thermal behavior has been obtained, with sensitivity of 11.53 pm/◦C for the perpendicular polarization (S) and 11.08 pm/◦C for the parallel polarization (P), thus having 4.0% different sensitivity between the two polarizations. -
Functionalized Etched Tilted Fiber Bragg Grating Aptasensor for Label-Free Protein Detection
Biosensors and Bioelectronics 146 (2019) 111765 Contents lists available at ScienceDirect Biosensors and Bioelectronics journal homepage: http://www.elsevier.com/locate/bios Functionalized etched tilted fiber Bragg grating aptasensor for label-free protein detection a,b,* a,1 � c Marzhan Sypabekova , Sanzhar Korganbayev , Alvaro Gonzalez-Vila� , Christophe Caucheteur c, Madina Shaimerdenova a, Takhmina Ayupova a, Aliya Bekmurzayeva a,b, Luca Vangelista d, Daniele Tosi a,b a PI National Laboratory Astana, Laboratory of Biosensors and Bioinstruments, 53 Kabanbay Batyr Avenue, 010000, Nur-Sultan, Kazakhstan b School of Engineering and Digital Sciences, Nazarbayev University, 53 Kabanbay Batyr Avenue, 010000, Nur-Sultan, Kazakhstan c Electromagnetism and Telecommunication Department, University of Mons, Boulevard Dolez 31, 7000, Mons, Belgium d School of Medicine, Nazarbayev University, 53 Kabanbay Batyr Avenue, 010000, Nur-Sultan, Kazakhstan ARTICLE INFO ABSTRACT Keywords: An aptasensor based on etched tilted fiber Bragg grating (eTFBG) is developed on a single-mode optical fiber Optical fiber targeting biomolecule detection. TFBGs were chemically etched using hydrofluoric acid (HF) to partially remove Aptasensor the fiber cladding. The sensor response was coarsely interrogated, resulting on a sensitivity increase from 1.25 Thrombin nm/RIU (refractive index unit) at the beginning of the process, up to 23.38 nm/RIU at the end of the etching, for Etching a RI range from 1.3418 to 1.4419 RIU. The proposed aptasensor showed improved RI sensitivity as compared to Detection the unetched TFBG, without requiring metal depositions on the fiber surface or polarization control during the measurements. The proposed sensor was tested for the detection of thrombin-aptamer interactions based on silane-coupling surface chemistry, with thrombin concentrations ranging from 2.5 to 40 nM. -
A Guide to Fiber Bragg Grating Sensors
Chapter 1 A Guide to Fiber Bragg Grating Sensors Marcelo M. Werneck, Regina C. S. B. Allil, Bessie A. Ribeiro and Fábio V. B. de Nazaré Additional information is available at the end of the chapter http://dx.doi.org/10.5772/54682 1. Introduction Optical fiber sensors (OFS) appeared just after the invention of the practical optical fiber by Corning Glass Works in 1970, now Corning Incorporated, that produced the first fiber with losses below 20 dB/km. At the beginning of this era, optical devices such as laser, photodetectors and the optical fibers were very expensive, afforded only by telecom companies to circumvent the old saturated copper telephone network. With the great diffusion of the optical fiber technology during the 1980’s and on, optoelectronic devices became less expensive, what favored their use in OFS. OFS can be applied in many branches of the industry but we will concentrate here the electrical power industry. In this area, the operators need to measure and monitor some important physical parameters that include: Strain (µє) Vibration of structures and machines Electric current (from A to kA) Voltage (from mV to MV) Impedance (µΩ) Leakage current of insulators (µA to mA) Temperature Pressure Gas concentration Distance between stationary and rotating or moving parts In the electrical power industry (EPI) we have two facts that can cause collapse of an electronic sensor: presence of high voltage and presence of high electromagnetic interference. Therefore, depending on where we want to measure a parameter it can be very difficult or even impossible to use a conventional sensor. -
Fabrication and Characterization of Polycarbonate Microstructured Polymer Optical Fibers for High-Temperature-Resistant Fiber Bragg Grating Strain Sensors
Fabrication and characterization of polycarbonate microstructured polymer optical fibers for high-temperature-resistant fiber Bragg grating strain sensors Andrea Fasano,1 Getinet Woyessa,2 Pavol Stajanca,3 Christos Markos,2,4 Alessio Stefani,2,5 Kristian Nielsen,2 Henrik K. Rasmussen,1 Katerina Krebber,3 and Ole Bang2,* 1 DTU Mekanik, Department of Mechanical Engineering, Technical University of Denmark, 2800 Kgs. Lyngby, Denmark 2 DTU Fotonik, Department of Photonics Engineering, Technical University of Denmark, 2800 Kgs. Lyngby, Denmark 3 Division 8.6 “Optical and Fibre Optic Methods“, BAM Federal Institute for Materials Research and Testing, 12205 Berlin, Germany 4 CREOL, The College of Optics & Photonics, University of Central Florida, 4000 Central Florida Blvd., Orlando, FL 32816, USA 5 Institute of Photonics and Optical Science (IPOS), School of Physics, The University of Sydney, NSW 2006, Australia *[email protected] Abstract: Here we present the fabrication of a solid-core microstructured polymer optical fiber (mPOF) made of polycarbonate (PC), and report the first experimental demonstration of a fiber Bragg grating (FBG) written in a PC optical fiber. The PC used in this work has a glass transition temperature of 145°C. We also characterize the mPOF optically and mechanically, and further test the sensitivity of the PC FBG to strain and temperature. We demonstrate that the PC FBG can bear temperatures as high as 125°C without malfunctioning. In contrast, polymethyl methacrylate-based FBG technology is generally limited to temperatures below 90°C. ©2016 Optical Society of America OCIS codes: (060.2370) Fiber optics sensors; (060.3735) Fiber Bragg gratings; (060.4005) Microstructured fibers; (060.2270) Fiber characterization; (160.5470) Polymers. -
Fabrication and Application of Polymer Optical Fiber Grating Devices Rui Min
Chapter Fabrication and Application of Polymer Optical Fiber Grating Devices Rui Min Abstract Grating devices in polymer optical fiber (POFs) have attracted interest due to varies potential applications in recent years. This chapter presents the state of art about the fabrication technology of grating devices in different kinds of POFs and explores potential sensing application scenarios, focus on the fabrication of chirped POF FBG devices and the potential application of such devices. Present several typical applications with uniform POF FBG. Also present several typical applica- tions based on Chirped POF FBG, which indicate POF FBG shown promising in the sensing area with show higher sensitivity and bio-compatibility than silica ones, and special grating in POF are attractive for future biomedical applications. Keywords: polymer optical fiber, fiber Bragg grating, refractive index change, long-period grating 1. Introduction Polymer Optical fiber (POF) is one kind of optical fiber made of polymer material. It has attractive characteristics such as low Young’s modulus, high strain, high flexibility, and biocompatibility performance compared with silica optical fiber. The first commercially polymer optical fiber with deuterated polymer was reported in the early 1960s [1]. From the 1950s, optical fibers are under research due to the demand of transmission high-speed data. Silica fibers were also under intense research since their first proposal as a transmission medium by Kao et al. [2]. At that time the transmission loss of silica fibers was high and the theoretical predictions allow to propose pure glass as fiber material able to transmit light over a hundred kilometers. Then, the purity of silica material was significantly improved and losses were reduced up to 0.5 dB/km at 1300 nm, and 0.2 dB/km at 1550 nm after a few years [3]. -
Fiber Bragg Grating Vibration Sensor with DFB Laser Diode
See discussions, stats, and author profiles for this publication at: https://www.researchgate.net/publication/269072826 Fiber Bragg Grating vibration sensor with DFB laser diode Conference Paper in Proceedings of SPIE - The International Society for Optical Engineering · December 2012 DOI: 10.1117/12.2010467 CITATIONS READS 6 237 8 authors, including: Jakub Cubik Stanislav Kepak VŠB-Technical University of Ostrava University of Strathclyde 45 PUBLICATIONS 204 CITATIONS 53 PUBLICATIONS 335 CITATIONS SEE PROFILE SEE PROFILE Petr Koudelka Jan Latal Czech Telecommunication Office VŠB-Technical University of Ostrava 84 PUBLICATIONS 494 CITATIONS 113 PUBLICATIONS 383 CITATIONS SEE PROFILE SEE PROFILE Some of the authors of this publication are also working on these related projects: Advances in Fetal Monitoring View project TA ČR GAMA: PRE SEED VŠB-Technical University of Ostrava fund - BroadbandLIGHT View project All content following this page was uploaded by Jan Latal on 16 April 2018. The user has requested enhancement of the downloaded file. Fiber Bragg Grating vibration sensor with DFB laser diode Petr Siska*, Martin Brozovic, Jakub Cubik, Stanislav Kepak, Jan Vitasek, Petr Koudelka, Jan Latal, Vladimir Vasinek *VSB-Technical University of Ostrava, Faculty of Electrical Engineering and Computer Science, Department of Telecommunications, 17. listopadu 15, Ostrava, 708 33, Czech Republic *[email protected]; phone +420 596991417; fax +420 597321650; http://kat440.vsb.cz/optice ABSTRACT The Fiber Bragg Grating (FBG) sensors are nowadays used in many applications. Thanks to its quite big sensitivity to a surrounding environment, they can be used for sensing of temperature, strain, vibration or pressure. A fiber Bragg grating vibration sensor, which is interrogated by a distributed feedback laser diode (DFB) is demonstrated in this article. -
The Impact of Deflection on the Sensing Response of Fiber Bragg Gratings Bonded to Graphene and PMMA Substrates
Current Optics and Photonics ISSN: 2508-7266(Print) / ISSN: 2508-7274(Online) Vol. 4, No. 2, April 2020, pp. 95-102 DOI: https://doi.org/10.3807/COPP.2020.4.2.095 The Impact of Deflection on the Sensing Response of Fiber Bragg Gratings Bonded to Graphene and PMMA Substrates Younis Mohammed Salih1, Mudhaffer Mustafa Ameen2, Fahmi F. Muhammadsharif3*, Mohammad Fadhli Ahmad1, Nor Aieni Haji Mokhtar1, Ismael Mohammed Mohammed Saeed4, Md Nurul Islam Siddique1, Ahmad Nazri Dagang1, Salisa Abdul Rahman1, Nurul Adilah Abdul Latiff1, and Abd Khamim Ismail5 1School of Ocean Engineering Technology and Informatics, Universiti Malaysia Terengganu, 21030 Kuala Nerus, Terengganu, Malaysia 2Department of Physics, Faculty of Education, Tishk International University, 44001 Erbil, IRAQ 3Department of Physics, Faculty of Science and Health, Koya University, 44023 Koya, Kurdistan Region-F.R., Iraq 4Department of Physics, College of Educational Science, University of Garmian, 46021 Kalar, Kurdistan Region-Iraq 5Department of Physics Faculty of Science, Universiti Teknologi Malaysia, Skudai, 81310 Johor, Malaysia (Received October 11, 2019 : revised January 17, 2020 : accepted February 12, 2020) The impact of graphene and poly(methyl methacrylate) (PMMA) substrates on the response of a fiber Bragg grating (FBG) due to mechanical deflection was investigated. For this purpose, four FBGs with grating lengths of 5, 15, 25, and 35.9 mm were utilized. Higher sensitivity was found for FBGs of larger grating length and for those bonded to graphene substrate. It was concluded that FBGs of smaller grating length (5 and 15 mm) were more sensitive in compression mode, while those of larger grating length (25 and 35.9 mm) were seen to be highly sensitive in tension mode. -
Fiber Optical Sensing with Fiber Bragg Gratings
Fiber Optical Sensing with Fiber Bragg Gratings Eisenmann Th. INFAP GmbH, Fürstenrieder Straße 279a, 81377 München [email protected] Summary areexplosion-proof zones, exhibit strong Anew measurement method is presented uti- magnetic fields or arenot accessible anymore lizing glass fibers with inscribed Fiber Bragg after the sensors have been installed. Gratings (FBG). Strain and temperature – Attenuation 0.1 dB/km only.Thus ameas- changes have direct effects on these gratings. urement lengthofsome 100 km can With this technology and suitable transducers, be realized. however,also parameters like pressure, dislo- cation, vibration, acceleration, humidity and 1. Introduction even chemicals can be monitored. Abroad- Initially conceived as amedium to carry light band or sweeping laser light source is used and images for medical endoscopic applica- and light with wavelengths corresponding to tions, optical fibers werelater proposed in the the FBGs is reflected back to adata acquisition mid 1960’sasanadequate information carry- unit (interrogator). Depending on variations of ing medium for telecommunication applica- the parameter to be measured, the grating is tions. At the heart of this technology is the stretched or compressed and as aresult the optical fiber itself – ahair-thin cylindrical fila- reflected (Bragg) wavelength is shifted to ment made of glass that is able to guide light longer or shorter wavelength respectively.This through itself by confining it within regions shift is proportional to the change of the para- having different optical indices of refraction. meters value. The fiber sensor or the trans- Ever since, optical fiber technology has been ducers can be fixed, welded, glued onto or the subject of considerable research and devel- even embedded in the media, which shall be opment.