Study of Laminar Flow Forced Convection Heat Transfer Behavior of a Phase Change Material Fluid
Total Page:16
File Type:pdf, Size:1020Kb
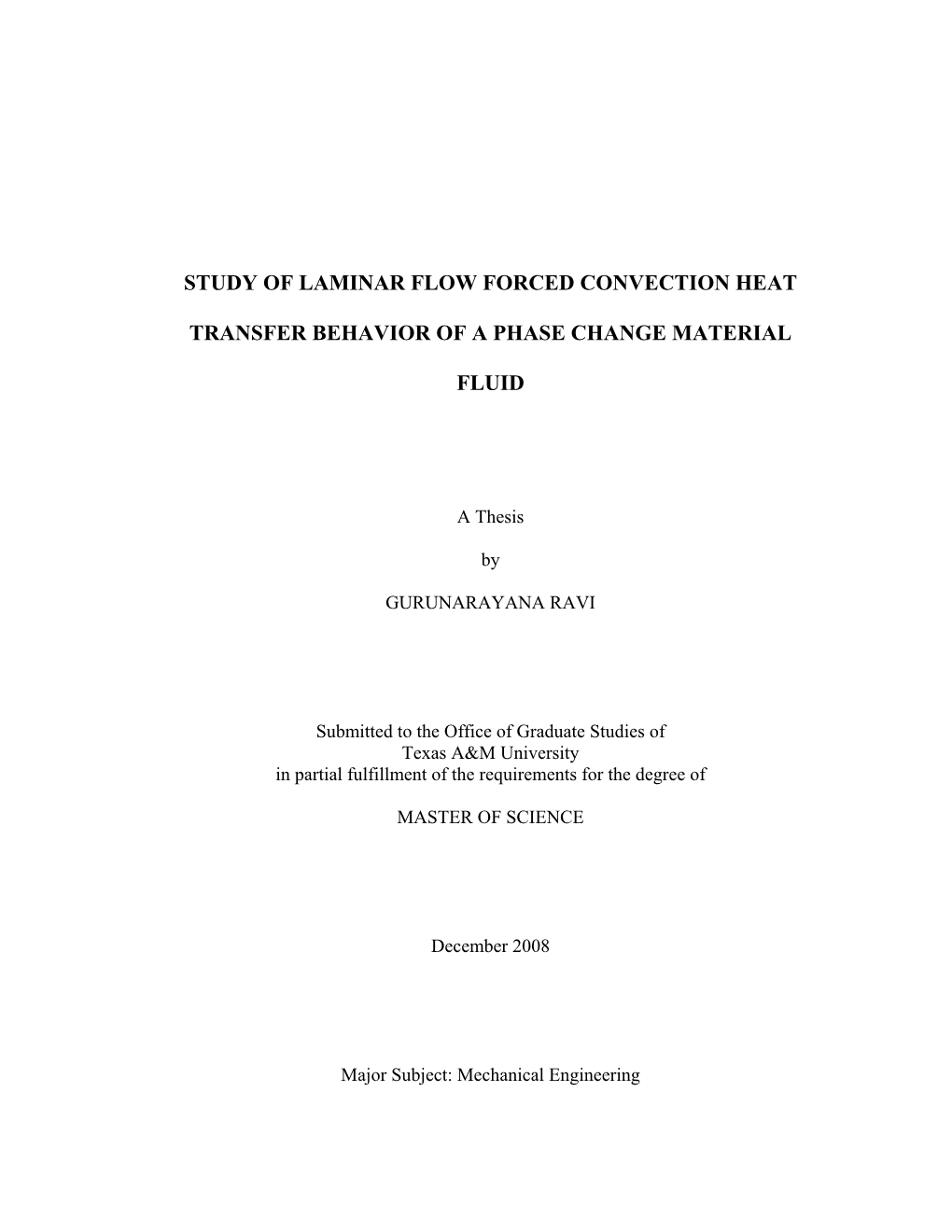
Load more
Recommended publications
-
Beyond the Classical Stefan Problem
Beyond the classical Stefan problem Francesc Font Martinez PhD thesis Supervised by: Prof. Dr. Tim Myers Submitted in full fulfillment of the requirements for the degree of Doctor of Philosophy in Applied Mathematics in the Facultat de Matem`atiques i Estad´ıstica at the Universitat Polit`ecnica de Catalunya June 2014, Barcelona, Spain ii Acknowledgments First and foremost, I wish to thank my supervisor and friend Tim Myers. This thesis would not have been possible without his inspirational guidance, wisdom and expertise. I appreciate greatly all his time, ideas and funding invested into making my PhD experience fruitful and stimulating. Tim, you have always guided and provided me with excellent support throughout this long journey. I can honestly say that my time as your PhD student has been one of the most enjoyable periods of my life. I also wish to express my gratitude to Sarah Mitchell. Her invaluable contributions and enthusiasm have enriched my research considerably. Her remarkable work ethos and dedication have had a profound effect on my research mentality. She was an excellent host during my PhD research stay in the University of Limerick and I benefited significantly from that experience. Thank you Sarah. My thanks also go to Vinnie, who, in addition to being an excellent football mate and friend, has provided me with insightful comments which have helped in the writing of my thesis. I also thank Brian Wetton for our useful discussions during his stay in the CRM, and for his acceptance to be one of my external referees. Thank you guys. Agraeixo de tot cor el suport i l’amor incondicional dels meus pares, la meva germana i la meva tieta. -
Improved Lumped Parameter Model for Phase Change in Latent Thermal Energy Storage Systems
IX Minsk International Seminar “Heat Pipes, Heat Pumps, Refrigerators, Power Sources”, Minsk, Belarus, 07-10 September, 2015 IMPROVED LUMPED PARAMETER MODEL FOR PHASE CHANGE IN LATENT THERMAL ENERGY STORAGE SYSTEMS Mina Rouhani, Majid Bahrami Laboratory for Alternative Energy Conversion (LAEC), School of Mechatronic Systems Engineering, Simon Fraser University, V3T 0A3 +1 (778) 782-8538/ [email protected] Abstract A modified lumped parameter model has been used to study transient conduction in phase change materials (PCM) in cylindrical coordinates. The two-point Hermite approximation is used to compute the average temperatures and the temperature gradient in each phase. The performance of PCM has been analyzed during the charging processin terms of energy storage and density. The effect of Stefan number on melting front dynamics is comprehensively studied. The results are verified with exact solutions as well as steady-state asymptotes and also show good agreement with existing experimental data. KEYWORDS Stefan problem; Lumped model; phase change material (PCM); Thermal energy storage; Solidification;Hermite approximation INTRODUCTION Thermal energy storage (TES) systems are a sustainable, energy efficient alternative to conventional heating and cooling methods. TES can play a pivotal role in synchronizing energy demand and supply, both on a short and long term basis.TES is divided into sensible, latent, and thermochemical mechanisms. Latent thermal storage using phase change materials(PCM) has a relatively constant melting/solidification temperature,higher energy storage density compared to sensible TES,and less complexity and lower manufacturing cost than the thermochemical TES [1]. Due to the non-linearity of phase change problems, analytical solutions to the analysis of phase change problem are limited by assumptions such as small Stefan number, specific boundary conditions, and simple geometries. -
Numerical Solution to Two-Phase Stefan Problems by the Heat Balance Integral Method J. Caldwell & C.K. Chiu Department of Ma
Transactions on Engineering Sciences vol 5, © 1994 WIT Press, www.witpress.com, ISSN 1743-3533 Numerical solution to two-phase Stefan problems by the heat balance integral method J. Caldwell & C.K. Chiu Department of Mathematics, City Polytechnic of Hong Kong, 83 Tat Chee Avenue, Kowloon, Hong Kong ABSTRACT Caldwell and Chiu [1, 2] have used a simple front-fixed method, namely, the Heat Balance Integral Method (HBIM), to solve one-phase solidification problems. In this paper the method is extended to two-phase Stefan prob- lems which arise when the effect of sub-cooling is taken into consideration. Numerical results for the two-phase cylindrical problem are obtained for a range of sub-divisions (n), sub-cooling parameters (0), Stefan number (a) and ratio of conductivities (/<i/%2). The effects of variation of parameters on the solidification process are also studied. INTRODUCTION Melting and solidification problems occur in numerous important areas of science, engineering and industry. For example, freezing and thawing of foods, production of ice, ice formation on pipe surface, solidification of steel and chemical reaction all involve either a melting or solidification process. Mathematically, melting/solidification problems are special cases of mov- ing boundary problems. Problems in which the solution of a differential equation has to satisfy certain conditions on the boundary of a prescribed domain are referred to as boundary-value problems. In the cases of melt- ing/solidification problems, however, the boundary of the domain is not known in advance, so the solution of melting/solidification problems re- quires solving the diffusion or heat-conduction equation in an unknown re- gion which has also to be determined as part of the solution. -
List of Commonly Used Variables for Sea-Ice Studies
(A) (B) Free Drift Linear Viscosity (C) (D) Ideal Plastic Viscous Plastic Collision Induced Rheology Figure 2.1: Schematic representation of the most commonly used rheologies includ- ing (A) free drift, (B) linear viscosity, (C) ideal and viscous plastic, and (D) collision induced. Modified from Washington and Parkinson (2005; Figure 3.24) 15 Figure 2.2: Schematic representation of the energy balance vertically through an ice pack. Modified from Washington and Parkinson (2005; Figure 3.21). is balanced along the air/snow, air/ice, snow/ice, and ice/ocean interfaces. The steady-state equation for the conservation of energy at the surface of ice covered water follows: 0 if T0 < Tf QH + QL + QLW + (1 α0)QSW I0 QLW + QG0 = (2.14) ↓ − ↓ − − ↑ Q if T = T M 0 f where I0 is the amount of solar radiation that penetratesthe snow/ice column, and Tf is the salinity dependent freezing point. The surface energy balance for the sea- ice zone will be equal to zero for surface temperatures below freezing (T0 < Tf ), otherwise melt will occur (Wadhams 2000, Washington and Parkinson 2005). It should be noted that for sea ice, the sensible and latent heat fluxes are positive downward ( ) (Washington and Parkinson 2005). ↓ The steady-state equation for the conservation of energy along the air/snow interface follows equation 2.14 for the snow surface and the values for emissivity, 17 albedo, and the conductive flux are specific to the snow surface ("s, αs, and QGs ). Snowmelt is dependent on surface temperature, which is that of the snow surface, and equals 0 for surface temperature below freezing. -
Lecture 1 (Pdf)
GFD 2006 Lecture 1: Introduction to Ice Grae Worster; notes by Rachel Zammett and Devin Conroy March 15, 2007 1 Introduction Our aim in this course is to understand some of the processes associated with ice in the natural environment. Figure 1 shows the location of some of Earth's ice during the north- ern winter. These ice deposits may be categorized as sea ice, ice sheets and shelves, and permafrost. Figure 1: Satellite image showing the ice cover in the northern hemisphere during northern winter, showing sea ice lying in the Arctic basin, the permanent ice sheet over Greenland and permafrost in the exposed land surface. 2 Ice sheets Firstly, figure 1 shows the ice sheet that covers approximately 80% of Greenland. This is about 105 years old and reaches depths of 2{3 kilometers. On large scales, ice can be treated as a highly viscous, non-Newtonian fluid that can flow because it is a polycrystalline solid and contains a percentage of unfrozen water (figure 2). Looking on a scale of about 100µm, 1 Figure 2: Image of the intersection of four ice grains. Between these grains lie the veins containing liquid water and dissolved impurities. The scale bar on this picture is 100 µm. we can see the ice grain junctions and the veins which lie between them. The liquid water contained in the veins between the ice crystals lubricates the flow, allowing the ice to flow more easily. This water can also transport dissolved impurities, which will therefore move relative to the ice crystals; this is important when analyzing ice cores, for example. -
A Continuum Model for Meltwater Flow Through Compacting Snow
The Cryosphere, 11, 2799–2813, 2017 https://doi.org/10.5194/tc-11-2799-2017 © Author(s) 2017. This work is distributed under the Creative Commons Attribution 4.0 License. A continuum model for meltwater flow through compacting snow Colin R. Meyer1 and Ian J. Hewitt2 1John A. Paulson School of Engineering and Applied Sciences, Harvard University, Cambridge, MA 02138, USA 2Mathematical Institute, Woodstock Road, Oxford, OX2 6GG, UK Correspondence to: Colin R. Meyer ([email protected]) Received: 2 July 2017 – Discussion started: 19 July 2017 Revised: 13 October 2017 – Accepted: 23 October 2017 – Published: 11 December 2017 Abstract. Meltwater is produced on the surface of glaciers health of glaciers and ice sheets under atmospheric warming and ice sheets when the seasonal energy forcing warms the (Harper et al., 2012; Enderlin et al., 2014; Forster et al., 2014; snow to its melting temperature. This meltwater percolates Koenig et al., 2014; Machguth et al., 2016). The balance be- into the snow and subsequently runs off laterally in streams, tween runoff, refreezing, and storage is controlled by the me- is stored as liquid water, or refreezes, thus warming the sub- chanics and thermodynamics of the porous snow. These pro- surface through the release of latent heat. We present a con- cesses also underlie the rate of compaction of firn into ice and tinuum model for the percolation process that includes heat therefore control the average temperature and accumulation conduction, meltwater percolation and refreezing, as well as rate that provide surface boundary conditions to numerical mechanical compaction. The model is forced by surface mass ice-sheet models (which typically do not include the com- and energy balances, and the percolation process is described pacting firn layer explicitly). -
Arxiv:1803.04883V1 [Physics.Flu-Dyn] 13 Mar 2018
Melting probe technology for subsurface exploration of extraterrestrial ice – Critical refreezing length and the role of gravity K. Sch¨uller, J. Kowalski∗ AICES Graduate School, RWTH Aachen University, Schinkelstr. 2, 52062 Aachen, Germany. Abstract The ’Ocean Worlds’ of our Solar System are covered with ice, hence the water is not directly accessible. Using melting probe technology is one of the promising technological approaches to reach those scientifically interesting water reservoirs. Melting probes basically consist of a heated melting head on top of an elongated body that contains the scientific payload. The traditional engineering approach to design such melting probes starts from a global energy balance around the melting head and quantifies the power necessary to sustain a specific melting velocity while preventing the probe from refreezing and stall in the channel. Though this approach is sufficient to design simple melting probes for terrestrial applications, it is too simplistic to study the probe’s performance for environmental conditions found on some of the Ocean’s Worlds, e.g. a lower value of the gravitational acceleration. This will be important, however, when designing exploration technologies for extraterrestrial purposes. We tackle the problem by explicitly modeling the physical processes in the thin melt film between the probe and the underlying ice. Our model allows to study melting regimes on bodies of different gravitational acceleration, and we explicitly compare melting regimes on Europa, Enceladus and Mars. In addition to that, our model allows to quantify the heat losses due to convective transport around the melting probe. We discuss to which extent these heat losses can be utilized to avoid the necessity of a side wall heating system to prevent stall, and introduce the notion of the ’Critical Refreezing Length’. -
Nondimensionalisation
Chapter 3 Nondimensionalisation The first and arguably the most important step in the analysis of a system of differential equations. It involves scaling each variable (dependent and independent) by a typical or reference value, leaving a nondimensional variable whose typical scale is O(1). Nondimensionalisation or problem normalisation has several important uses: 1. It identifies the dimensionless groups (ratios of dimensional parameters) which control the solution behaviour. 2. Terms in the equations are now dimensionless and so allows comparison of their sizes. This allows the identification of the important (i.e. dominant) terms in the equations and their interaction in different regimes, giving insight into the structure of solutions and the dominant physical mechanisms at work. In particular, negligible terms can be identified leading to simplification in many circumstances. 3. It allows estimates of the effects of additional features to the original model through the new dimensional group(s) associated with the additional term(s). This allows measurement of the effect of the physical feature(s) in the model. 4. Finally, it can reduce the number of parameters ocurring in the problem by forming the nondi- mensional parameters or dimensionless groups. 1 CHAPTER 3. NONDIMENSIONALISATION 2 3.1 Scaling If an equation has a variable u, say, then we nondimensionalise that variable by writing, for example, u = [u]¯u where [u] is the chosen scale (with the same dimensions as u) andu ¯ is the corresponding dimensionless variable. If a system of equations describes a real process then it is dimensionally homogeneous i.e. consistent. The process of nondimensionalisation will necessarily give a set of equations, each of whose terms is dimensionless, after division through by the dimensions of the equations. -
Heat Transfer During Melting and Solidification in Heterogeneous Materials
HEAT TRANSFER DURING MELTING AND SOLIDIFICATION IN HETEROGENEOUS MATERIALS By Sepideh Sayar Thesis submitted to the Faculty of the Virginia Polytechnic Institute and State University in partial fulfillment of the requirements for the degree of Master of Science In Mechanical Engineering Dr. Brian Vick, Chairman Dr. Elaine P. Scott Dr. Karen A. Thole Dr. James R. Thomas December, 2000 Blacksburg, Virginia Keywords: Heterogeneous Material, Phase changing, Melting, Solidification, Numerical Method, Finite Difference Method (FDM) Copyright 2000, Sepideh Sayar HEAT TRANSFER DURING MELTING AND SOLIDIFICATION IN HETEROGENEOUS MATERIALS By Sepideh Sayar Dr. Brian Vick, Chairman Department of Mechanical Engineering ABSTRACT A one-dimensional model of a heterogeneous material consisting of a matrix with embedded separated particles is considered, and the melting or solidification of the particles is investigated. The matrix is in imperfect contact with the particles, and the lumped capacity approximation applies to each individual particle. Heat is generated inside the particles or is transferred from the matrix to the particles coupled through a contact conductance. The matrix is not allowed to change phase and energy is either generated inside the matrix or transferred from the boundaries, which is initially conducted through the matrix material. The physical model of this coupled, two-step heat transfer process is solved using the energy method. The investigation is conducted in several phases using a building block approach. First, a lumped capacity system during phase transition is studied, then a one-dimensional homogeneous material during phase change is investigated, and finally the one- dimensional heterogeneous material is analyzed. A numerical solution based on the finite difference method is used to solve the model equations. -
Numerical Scheme for the One-Phase 1D Stefan Problem Using Curvilinear
Please cite this article as: Marek Błasik, Numerical scheme for the one-phase 1D Stefan problem using curvilinear coordinates, Scientific Research of the Institute of Mathematics and Computer Science, 2012, Volume 11, Issue 3, pages 9-14. The website: http://www.amcm.pcz.pl/ Scientific Research of the Institute of Mathematics and Computer Science 3(11) 2012, 9-14 NUMERICAL SCHEME FOR THE ONE-PHASE 1D STEFAN PROBLEM USING CURVILINEAR COORDINATES Marek Błasik Institute of Mathematics, Czestochowa University of Technology Czestochowa, Poland [email protected] Abstract. In this paper we present a new approach to solving a one-dimensional, one-phase Stefan problem. The proposed method is based on choosing (a) suitable curvilinear space coordinate/s for the heat-flow equation and the finite difference method. In the final part of this paper, examples of numerical calculations are shown. Introduction Moving boundary problems in which the boundary of the domain is not known occur in subjects such as heat flow, hydrology, solute transport or molecular diffu- sion. Moving boundaries are associated with time dependent problems and the position of the boundary has to be determined as a function of time. Moving boundary problems are often called Stefan problems, with reference to the work of J. Stefan, who investigated the melting of the polar ice cap [1-3]. In the literature there are many well-known methods for solving the Stefan prob- lem. One of them, proposed by Schniewind, is based on the concept that moving boundary moves “from node to node” [4, 5]. A similar approach, where the moving boundary always moves from one grid point to another, was applied by Douglas and Gallie in [6]. -
Improved Stefan Equation Correction Factors to Accommodate Sensible Heat Storage During Soil Freezing Or Thawing
Improved Stefan equation correction factors to accommodate sensible heat storage during soil freezing or thawing Barret L. Kurylyk and Masaki Hayashi Department of Geoscience, University of Calgary, Calgary, AB, Canada Note: This is a post-print of an article published in Permafrost and Periglacial Processes in 2016. For a final, type-set version of the article, please email me at [email protected] or go to: http://onlinelibrary.wiley.com/doi/10.1002/ppp.1865/abstract Abstract In permafrost regions, the thaw depth strongly controls shallow subsurface hydrologic processes that in turn dominate catchment runoff. In seasonally freezing soils, the maximum expected frost depth is an important geotechnical engineering design parameter. Thus, accurately calculating the depth of soil freezing or thawing is an important challenge in cold regions engineering and hydrology. The Stefan equation is a common approach for predicting the frost or thaw depth, but this equation assumes negligible soil heat capacity and thus exaggerates the rate of freezing or thawing. The Neumann equation, which accommodates sensible heat, is an alternative implicit equation for calculating freeze-thaw penetration. This study details the development of correction factors to improve the Stefan equation by accounting for the influence of the soil heat capacity and non-zero initial temperatures. The correction factors are first derived analytically via comparison to the Neumann solution, but the resultant equations are complex and implicit. Thus, explicit equations are obtained by fitting polynomial functions to the analytical results. These simple correction factors are shown to significantly improve the performance of the Stefan equation for several hypothetical soil freezing and thawing scenarios. -
Chapter 2 Problems with Explicit Solutions
CHAPTER 2 PROBLEMS WITH EXPLICIT SOLUTIONS The formulation of Stefan Problems as models of basic phase-change processes was presented in §1.2.Under certain restrictions on the parameters and data such problems admit explicit solutions in closed form.These simplest possible, explicitly solvable Stefan problems form the backbone of our understanding of all phase-change models and serve as the only means of validating approximate and numerical solutions of more complicated problems. Unfortunately,closed-form explicit solutions (all of which are of similarity type) may be found only under the following very restrictive conditions: 1-dimensional, semi-infinite geometry,uniform initial temperature, constant imposed temperature (at the boundary), and thermophysical properties constant in each phase. Within these confines we present a succession of models of increasingly complicated phase-change processes. We begin with the simplest possible models, the classical 1-phase Stefan problem ( §2.1), and 2-phase Stefan Problem ( §2.2), modeling the most basic aspects of a phase-change process (as discussed in §1.2). Wepresent the Neumann similarity solution and familiarize the reader with some of the information it conveys. Next ( §2.3 )werelax the assumption of constant density by allowing the densities of solid and liquid to be different (but each still a constant), thus bringing density change effects into the picture. We study the effect of volume expansion (no voids), and of shrinkage (causing formation of a void near the wall). In each case we formulate explicitly solvable thermal models (neglecting all mechanical effects) and examine the effect of density change on the Neumann solution.