Latticesc DDR/DDR2 SDRAM Memory Interface User's Guide
Total Page:16
File Type:pdf, Size:1020Kb
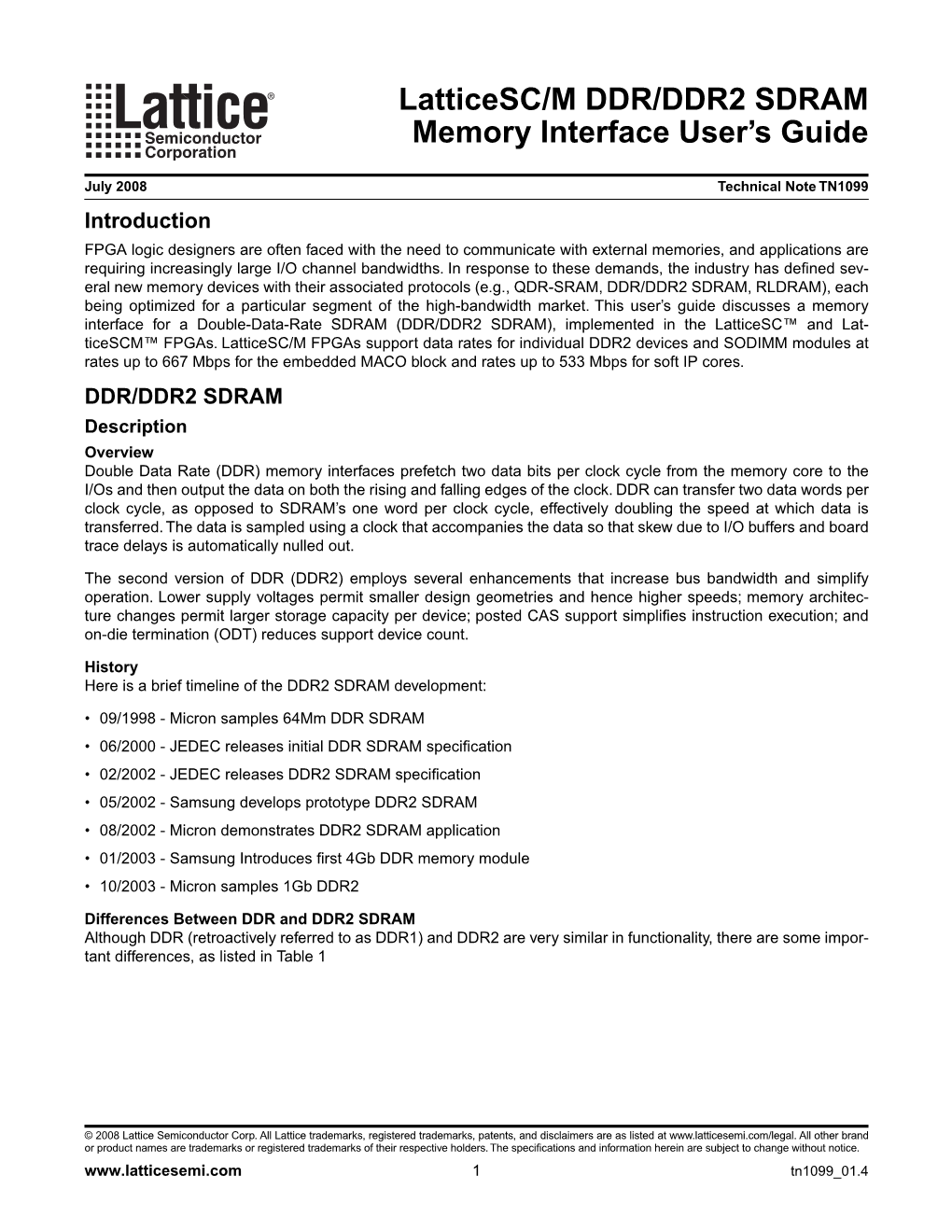
Load more
Recommended publications
-
Different Types of RAM RAM RAM Stands for Random Access Memory. It Is Place Where Computer Stores Its Operating System. Applicat
Different types of RAM RAM RAM stands for Random Access Memory. It is place where computer stores its Operating System. Application Program and current data. when you refer to computer memory they mostly it mean RAM. The two main forms of modern RAM are Static RAM (SRAM) and Dynamic RAM (DRAM). DRAM memories (Dynamic Random Access Module), which are inexpensive . They are used essentially for the computer's main memory SRAM memories(Static Random Access Module), which are fast and costly. SRAM memories are used in particular for the processer's cache memory. Early memories existed in the form of chips called DIP (Dual Inline Package). Nowaday's memories generally exist in the form of modules, which are cards that can be plugged into connectors for this purpose. They are generally three types of RAM module they are 1. DIP 2. SIMM 3. DIMM 4. SDRAM 1. DIP(Dual In Line Package) Older computer systems used DIP memory directely, either soldering it to the motherboard or placing it in sockets that had been soldered to the motherboard. Most memory chips are packaged into small plastic or ceramic packages called dual inline packages or DIPs . A DIP is a rectangular package with rows of pins running along its two longer edges. These are the small black boxes you see on SIMMs, DIMMs or other larger packaging styles. However , this arrangment caused many problems. Chips inserted into sockets suffered reliability problems as the chips would (over time) tend to work their way out of the sockets. 2. SIMM A SIMM, or single in-line memory module, is a type of memory module containing random access memory used in computers from the early 1980s to the late 1990s . -
DDR and DDR2 SDRAM Controller Compiler User Guide
DDR and DDR2 SDRAM Controller Compiler User Guide 101 Innovation Drive Software Version: 9.0 San Jose, CA 95134 Document Date: March 2009 www.altera.com Copyright © 2009 Altera Corporation. All rights reserved. Altera, The Programmable Solutions Company, the stylized Altera logo, specific device designations, and all other words and logos that are identified as trademarks and/or service marks are, unless noted otherwise, the trademarks and service marks of Altera Corporation in the U.S. and other countries. All other product or service names are the property of their respective holders. Altera products are protected under numerous U.S. and foreign patents and pending ap- plications, maskwork rights, and copyrights. Altera warrants performance of its semiconductor products to current specifications in accordance with Altera's standard warranty, but reserves the right to make changes to any products and services at any time without notice. Altera assumes no responsibility or liability arising out of the application or use of any information, product, or service described herein except as expressly agreed to in writing by Altera Corporation. Altera customers are advised to obtain the latest version of device specifications before relying on any published information and before placing orders for products or services. UG-DDRSDRAM-10.0 Contents Chapter 1. About This Compiler Release Information . 1–1 Device Family Support . 1–1 Features . 1–2 General Description . 1–2 Performance and Resource Utilization . 1–4 Installation and Licensing . 1–5 OpenCore Plus Evaluation . 1–6 Chapter 2. Getting Started Design Flow . 2–1 SOPC Builder Design Flow . 2–1 DDR & DDR2 SDRAM Controller Walkthrough . -
Dual-DIMM DDR2 and DDR3 SDRAM Board Design Guidelines, External
5. Dual-DIMM DDR2 and DDR3 SDRAM Board Design Guidelines June 2012 EMI_DG_005-4.1 EMI_DG_005-4.1 This chapter describes guidelines for implementing dual unbuffered DIMM (UDIMM) DDR2 and DDR3 SDRAM interfaces. This chapter discusses the impact on signal integrity of the data signal with the following conditions in a dual-DIMM configuration: ■ Populating just one slot versus populating both slots ■ Populating slot 1 versus slot 2 when only one DIMM is used ■ On-die termination (ODT) setting of 75 Ω versus an ODT setting of 150 Ω f For detailed information about a single-DIMM DDR2 SDRAM interface, refer to the DDR2 and DDR3 SDRAM Board Design Guidelines chapter. DDR2 SDRAM This section describes guidelines for implementing a dual slot unbuffered DDR2 SDRAM interface, operating at up to 400-MHz and 800-Mbps data rates. Figure 5–1 shows a typical DQS, DQ, and DM signal topology for a dual-DIMM interface configuration using the ODT feature of the DDR2 SDRAM components. Figure 5–1. Dual-DIMM DDR2 SDRAM Interface Configuration (1) VTT Ω RT = 54 DDR2 SDRAM DIMMs (Receiver) Board Trace FPGA Slot 1 Slot 2 (Driver) Board Trace Board Trace Note to Figure 5–1: (1) The parallel termination resistor RT = 54 Ω to VTT at the FPGA end of the line is optional for devices that support dynamic on-chip termination (OCT). © 2012 Altera Corporation. All rights reserved. ALTERA, ARRIA, CYCLONE, HARDCOPY, MAX, MEGACORE, NIOS, QUARTUS and STRATIX words and logos are trademarks of Altera Corporation and registered in the U.S. Patent and Trademark Office and in other countries. -
DDR SDRAM SO-DIMM MODULE, 2.5V 128Mbyte - 16MX64 AVK6416U35C5266K0-AP
DDR SDRAM SO-DIMM MODULE, 2.5V 128MByte - 16MX64 AVK6416U35C5266K0-AP FEATURES JEDEC Standard DDR 266MHz PC2100 Version 1.0, Lead Free, RoHS compliant Clock frequency: 133MHz with CAS latency 2.5 256 byte serial EEPROM Data input and output masking Programmable burst length: 2, 4, 8 Programmable burst type: sequential and interleave Programmable CAS latency: 2.5 Auto refresh and self refresh capability Gold card edge fingers 8K refresh per 64ms Low active and standby current consumption SSTL-2 compatible inputs and outputs Decoupling capacitors at each memory device Double-sided module 30.75mm (1.25 inch) height DESCRIPTION The AVK6416U35C5266K0-AP is an Unbuffered DDR SDRAM SODIMM memory module. This module is JEDEC- standard 200-pin, small-outline, dual in-line memory module. A 256 byte serial EEPROM on board can be used to store module information such as timing, configuration, density, etc. The AVK6416U35C5266K0-AP memory module is 128MByte and organized as a 16MX64 array using (8) 8MX16 DDR SDRAMs in lead free TSSOP II packages. All memory modules are fabricated using the latest technology design, six-layer printed circuit board substrate construction with low ESR decoupling capacitors on-board for high reliability and low noise. PHYSICAL DIMENSIONS 67.60 (2.66) 3.50 (0.14) SPD 128Mbit 128Mbit 128Mbit 128Mbit ) 5 8MbX16 8MbX16 8MbX16 8MbX16 2 . 1 ( DDR DDR DDR DDR 5 7 SDRAM SDRAM SDRAM SDRAM . 1 ) 3 7 8 7 . 0 ( 0 2 FRONT SIDE 1.00 (0.04) Pin 1 Pin 199 NOTES: 1- All dimensions are in milimeters (inches) 2- All blue ICs are on the front, and all red ICs are on the back side of the module. -
64M X 16 Bit DDRII Synchronous DRAM (SDRAM) Advance (Rev
AS4C64M16D2A-25BAN Revision History 1Gb Auto-AS4C64M16D2A - 84 ball FBGA PACKAGE Revision Details Date Rev 1.0 Preliminary datasheet Jan 2018 Alliance Memory Inc. 511 Taylor Way, San Carlos, CA 94070 TEL: (650) 610-6800 FAX: (650) 620-9211 Alliance Memory Inc. reserves the right to change products or specification without notice Confidential - 1 of 62 - Rev.1.0 Jan. 2018 AS4C64M16D2A-25BAN 64M x 16 bit DDRII Synchronous DRAM (SDRAM) Advance (Rev. 1.0, Jan. /2018) Features Overview JEDEC Standard Compliant The AS4C64M16D2A is a high-speed CMOS Double- AEC-Q100 Compliant Data-Rate-Two (DDR2), synchronous dynamic random- JEDEC standard 1.8V I/O (SSTL_18-compatible) access memory (SDRAM) containing 1024 Mbits in a 16-bit wide data I/Os. It is internally configured as a 8- Power supplies: V & V = +1.8V 0.1V DD DDQ bank DRAM, 8 banks x 8Mb addresses x 16 I/Os. The Operating temperature: TC = -40~105°C (Automotive) device is designed to comply with DDR2 DRAM key Supports JEDEC clock jitter specification features such as posted CAS# with additive latency, Fully synchronous operation Write latency = Read latency -1, Off-Chip Driver (OCD) Fast clock rate: 400 MHz impedance adjustment, and On Die Termination(ODT). Differential Clock, CK & CK# All of the control and address inputs are synchronized Bidirectional single/differential data strobe with a pair of externally supplied differential clocks. Inputs are latched at the cross point of differential clocks (CK - DQS & DQS# rising and CK# falling) All I/Os are synchronized with a 8 internal banks for concurrent operation pair of bidirectional strobes (DQS and DQS#) in a source 4-bit prefetch architecture synchronous fashion. -
DDR2 SDRAM SO-DIMM MODULE, 1.8V 512Mbyte - 64MX64 AVK6464U51E5667F0
DDR2 SDRAM SO-DIMM MODULE, 1.8V 512MByte - 64MX64 AVK6464U51E5667F0 FEATURES JEDEC Standard DDR2 PC2-5300 667MHz - Clock frequency: 333MHz with CAS latency 5 - 256 byte serial EEPROM - Data input and output masking - Programmable burst length: 2, 4, 8 - Programmable burst type: sequential and interleave - Programmable CAS latency: 5 - Auto refresh and self refresh capability - Gold card edge fingers - 8K refresh per 64ms - Low active and standby current consumption - SSTL-2 compatible inputs and outputs - Decoupling capacitors at each memory device - Double-sided module - 1.18 inch height DESCRIPTION The AVK6464U51E5667F0 family consists of Unbuffered DDR2 SDRAM SODIMM memory module. This module is JEDEC-standard 200-pin, small-outline, dual in-line memory module. A 256 byte serial EEPROM on board can be used to store module information such as timing, configuration, density, etc. The AVK6464U51E5667F0 memory module is 512MByte and organized as a 64MX64 array using (8) 32MX16 (4 internal banks) DDR2 SDRAMs in BGA packages. All memory modules are fabricated using the latest technology design, six-layer printed circuit board substrate construction with low ESR decoupling capacitors on-board for high reliability and low noise. PHYSICAL DIMENSIONS 2.661 0.040 256MBit 256MBit 256MBit 256MBit 1.18 32MX8 DDR2 32MX8 DDR2 32MX8 DDR2 32MX8 DDR2 BGA SDRAM BGA SDRAM BGA SDRAM BGA SDRAM 512MBit (8MX16X4) 512MBit (8MX16X4) S 512MBit (8MX16X4) 512MBit (8MX16X4) P 32MX16 DDR2 BGA SDRAM 32MX16 DDR2 BGA SDRAM D 32MX16 DDR2 BGA SDRAM 32MX16 DDR2 BGA SDRAM 0.787 1 199 0.140 All gray ICs are on the top, and all white ICs are on the back side of the modude The SPD EEPROM is populated on the back side of the module BGA Package Avant™ Technology LP. -
Memory Controller SC White Paper
DEVELOPING HIGH-SPEED MEMORY INTERFACES: THE LatticeSCM FPGA ADVANTAGE A Lattice Semiconductor White Paper February 2006 Lattice Semiconductor 5555 Northeast Moore Ct. Hillsboro, Oregon 97124 USA Telephone: (503) 268-8000 www.latticesemi.com Developing High-Speed Memory Interfaces A Lattice Semiconductor White Paper Introduction A common problem for today’s system designers is to reliably interface to their next generation high- speed memory devices. As system bandwidths continue to increase, memory technologies have been optimized for higher speeds and performance. As a result, these next generation memory interfaces are also increasingly challenging to design to. Implementing high-speed, high-efficiency memory interfaces in programmable logic devices such as FPGAs has always been a major challenge for designers. Lattice Semiconductor offers customers a high performance FPGA platform in the LatticeSC to design high-speed memory interface solutions. The LatticeSC family implements various features on- chip that facilitate designing high-speed memory controllers to interface to the next generation high- speed, high performance DDR SDRAM, QDR SRAM, and emerging RLDRAM memory devices. The PURESPEED I/O structures on the LatticeSC, combined with the clock management resources and a high-speed FPGA fabric help customers reduce design risk and time-to-market for high-speed memory based designs. Additionally, the LatticeSCM family implements full-featured embedded high-speed memory controllers on-chip to interface smoothly to the next generation high-speed, high performance DDR I/II SDRAM, QDR II SRAM, and RLDRAM I/II memory devices. The embedded memory controllers, coupled with the I/O structures and clock management resources, are fully verified controllers for customers to use as off-the-shelf solutions. -
2048Mb Ddr2 Dimm
Apacer Memory Product Specification 2048MB DDR2 DIMM 2GB DDR2 DIMM based on 128MX8 ,8Banks, 1.8V DDR2 DIMM with SPD Features ‧Performance range ( Bandwidth: 5.3 GB/sec ) Part Number Max Freq. (Clock) Speed Grade 78.A1G9O.404 333MHz(3ns@CL5) 667Mbps ‧JEDECstandard 1.8V ± 0.1V Power Supply ‧VDDQ = 1.8V± 0.1V ‧Internal Bank: 8 Bank ‧Posted CAS ‧Programmable CAS Latency: 4, 5, 6 ‧Programmable Additive Latency: 0, 1 , 2 , 3 and 4 ‧Write Latency(WL) = Read Latency(RL) -1 ‧Burst Length: 4 , 8(Interleave/nibble sequential) ‧Programmable Sequential / Interleave Burst Mode ‧Bi-directional Differential Data-Strobe (Single-ended data-strobe is an optional feature) ‧Off-Chip Driver(OCD) Impedance Adjustment ‧On Die Termination ‧Refresh and Self Refresh Average Refesh Period 7.8us ‧Serial presence detect with EEPROM ‧Compliance with RoHS ‧Compliance with CE ‧Operating Temperature Rang: ‧Commercial 0°C ≦ TC ≦ 85°C ‧Refresh: auto-refresh, self-refresh ‧─Average refresh period 7.8us at 0°C ≦ TC ≦ 85°C 3.9us at 85°C ≦ TC ≦ 95°C Pin Description Pin Name Description Pin Name Description A0-A13 DDR2 SDRAM address bus CK0, CK1, CK2 DDR2 SDRAM clocks (positive line of differential pair) BA0-BA2 DDR2 SDRAM bank select CK0, CK1, CK2 DDR2 SDRAM clocks (negative line of differential pair) RAS DDR2 SDRAM row address strobe SCL I2C serial bus clock for EEPROM CAS DDR2 SDRAM column address strobe SDA I2C serial bus data line for EEPROM WE DDR2 SDRAM wirte enable SA0-SA2 I2C serial address select for EEPROM S0, S1 DIMM Rank Select Lines VDD* DDR2 SDRAM core power supply -
Swissbit SMT Memory Product Guide Rev1.9.Pub
SWISSMEMORY™ Industrial Product Line DRAM Memory Products Solutions for Industrial and Embedded Applications Surface Mount Technology (SMT) DDR3 DDR2 DDR SDRAM DRAM Visit us at www.swissbit.com Version 1.9 - 01/2009 DDR3 SDRAM TECHNOLOGY SDRAM DDR3 modules are Swissbit’s most recent Double Data Rate products to market. DDR3 is the memory choice for performance driven systems with clock frequencies of 400 to 800MHz and data rates of 800 to 1600 Mb per second. In addition to DDR3’s improved performance in dual- and multi-core systems, it also provides increased efficiency with lower power consumption. DDR3 power consumption is approximately 20% or more lower than its predecessor at 1.35V to 1.5V as compared to the 1.8V of DDR2. Swissbit offers DDR3’s unmatched combination of high bandwidth and density with lower power consumption in the variety of module packages. Density Swissbit PN Data Rate (MT/s) - CL Height # IC’s IC Org Rank DDR3 SDRAM UDIMM (240 pin) 512MB (64Mx64) SGU06464C1CB1xx-ssR 800-CL5 / 1066-CL7 / 1333-CL9 1.18" (29.97mm) 4 64Mx16 1 1GB (128Mx64) SGU12864D1BB1xx-ssR 800-CL5 / 1066-CL7 / 1333-CL9 1.18" (29.97mm) 8 128Mx8 1 2GB (256Mx64) SGU25664E1BB2xx-ssR 800-CL5 / 1066-CL7 / 1333-CL9 1.18" (29.97mm) 16 128Mx8 2 DDR3 SDRAM UDIMM w/ ECC (240 pin) 512MB (64Mx72) SGU06472H1CB1xx-ssR 800-CL5 / 1066-CL7 / 1333-CL9 1.18" (29.97mm) 5 64Mx16 1 1GB (128Mx72) SGU12872F1BB1xx-ssR 800-CL5 / 1066-CL7 / 1333-CL9 1.18" (29.97mm) 9 128Mx8 1 2GB (256Mx72) SGU25672G1BB2xx-ssR 800-CL5 / 1066-CL7 / 1333-CL9 1.18" (29.97mm) 18 128Mx8 2 DDR3 SDRAM -
Dynamic Random Access Memory Topics
Dynamic Random Access Memory Topics Simple DRAM Fast Page Mode (FPM) DRAM Extended Data Out (EDO) DRAM Burst EDO (BEDO) DRAM Synchronous DRAM (SDRAM) Rambus DRAM (RDRAM) Double Data Rate (DDR) SDRAM One capacitor and transistor of power, the discharge y Leaks a smallcapacitor amount slowly Simplicit refresh Requires top sk de in ed Us le ti la o v General DRAM Formats • DRAM is produced as integrated circuits (ICs) bonded and mounted into plastic packages with metal pins for connection to control signals and buses • In early use individual DRAM ICs were usually either installed directly to the motherboard or on ISA expansion cards • later they were assembled into multi-chip plug-in modules (DIMMs, SIMMs, etc.) General DRAM formats • Some Standard Module Type: • DRAM chips (Integrated Circuit or IC) • Dual in-line Package (DIP) • DRAM (memory) modules • Single in-line in Package(SIPP) • Single In-line Memory Module (SIMM) • Dual In-line Memory Module (DIMM) • Rambus In-line Memory Module (RIMM) • Small outline DIMM (SO-DIMM) Dual in-line Package (DIP) • is an electronic component package with a rectangular housing and two parallel rows of electrical connecting pins • 14 pins Single in-line in Package (SIPP) • It consisted of a small printed circuit board upon which were mounted a number of memory chips. • It had 30 pins along one edge which mated with matching holes in the motherboard of the computer. Single In-line Memory Module (SIMM) SIMM can be a 30 pin memory module or a 72 pin Dual In-line Memory Module (DIMM) Two types of DIMMs: a 168-pin SDRAM module and a 184-pin DDR SDRAM module. -
SDRAM Memory Systems: Architecture Overview and Design Verification SDRAM Memory Systems: Architecture Overview and Design Verification Primer
Primer SDRAM Memory Systems: Architecture Overview and Design Verification SDRAM Memory Systems: Architecture Overview and Design Verification Primer Table of Contents Introduction . 3 - 4 DRAM Trends . .3 DRAM . 4 - 6 SDRAM . 6 - 9 DDR SDRAM . .6 DDR2 SDRAM . .7 DDR3 SDRAM . .8 DDR4 SDRAM . .9 GDDR and LPDDR . .9 DIMMs . 9 - 13 DIMM Physical Size . 9 DIMM Data Width . 9 DIMM Rank . .10 DIMM Memory Size & Speed . .10 DIMM Architecture . .10 Serial Presence Detect . .12 Memory System Design . .13 - 15 Design Simulation . .13 Design Verification . .13 Verification Strategy . .13 SDRAM Verification . .14 Glossary . .16 - 19 2 www.tektronix.com/memory SDRAM Memory Systems: Architecture Overview and Design Verification Primer Introduction Memory needs to be compatible with a wide variety of memory controller hubs used by the computer DRAM (Dynamic Random Access Memory) is attractive to manufacturers. designers because it provides a broad range of performance Memory needs to work when a mixture of different and is used in a wide variety of memory system designs for manufacturer’s memories is used in the same memory computers and embedded systems. This DRAM memory system of the computer. primer provides an overview of DRAM concepts, presents potential future DRAM developments and offers an overview Open memory standards are useful in helping to ensure for memory design improvement through verification. memory compatibility. DRAM Trends On the other hand, embedded systems typically use a fixed There is a continual demand for computer memories to be memory configuration, meaning the user does not modify larger, faster, lower powered and physically smaller. These the memory system after purchasing the product. -
Datakommunikasjon Og Maskinvare
Institutt for økonomi og IT Datakommunikasjon og maskinvare Kompendium til emnet 6105N Windows Server og datanett Jon Kvisli Universitetet i Sørøst-Norge, Januar 2020 © Jon Kvisli, 2020 Windows® og Windows Server® er varemerker registrert av Microsoft Corporation. Det må ikke kopieres fra dette heftet ut over det som er tillatt etter bestemmelser i «Lov om opphavsrett til åndsverk», og avtaler om kopiering inngått med Kopinor. Forsidebilde: Colourbox Sats: Jon Kvisli 2 Innhold 1. GRUNNPRINSIPPER I DATAKOMMUNIKASJON .......................................................................... 4 1.1. Punkt-til-punkt kommunikasjon ................................................................................................................ 4 1.2. Kommunikasjonsbusser ............................................................................................................................. 8 1.3. Signalering ................................................................................................................................................ 10 1.4. Dempning, støy og forvrengning.............................................................................................................. 14 1.5. Digitale og analoge signaler ..................................................................................................................... 16 1.6. Noen kommunikasjonsstandarder ........................................................................................................... 17 1.7. Sammendrag ...........................................................................................................................................